Pioneering Safety Through Testing & Technology
For over 45 years, MGA has been at the forefront of independent testing and equipment solutions. Our comprehensive services and cutting-edge equipment empower automotive, aerospace, and defense industries to meet the highest safety and durability standards.
Comprehensive Testing Capabilities
MGA provides specialized testing services and equipment for critical sectors.
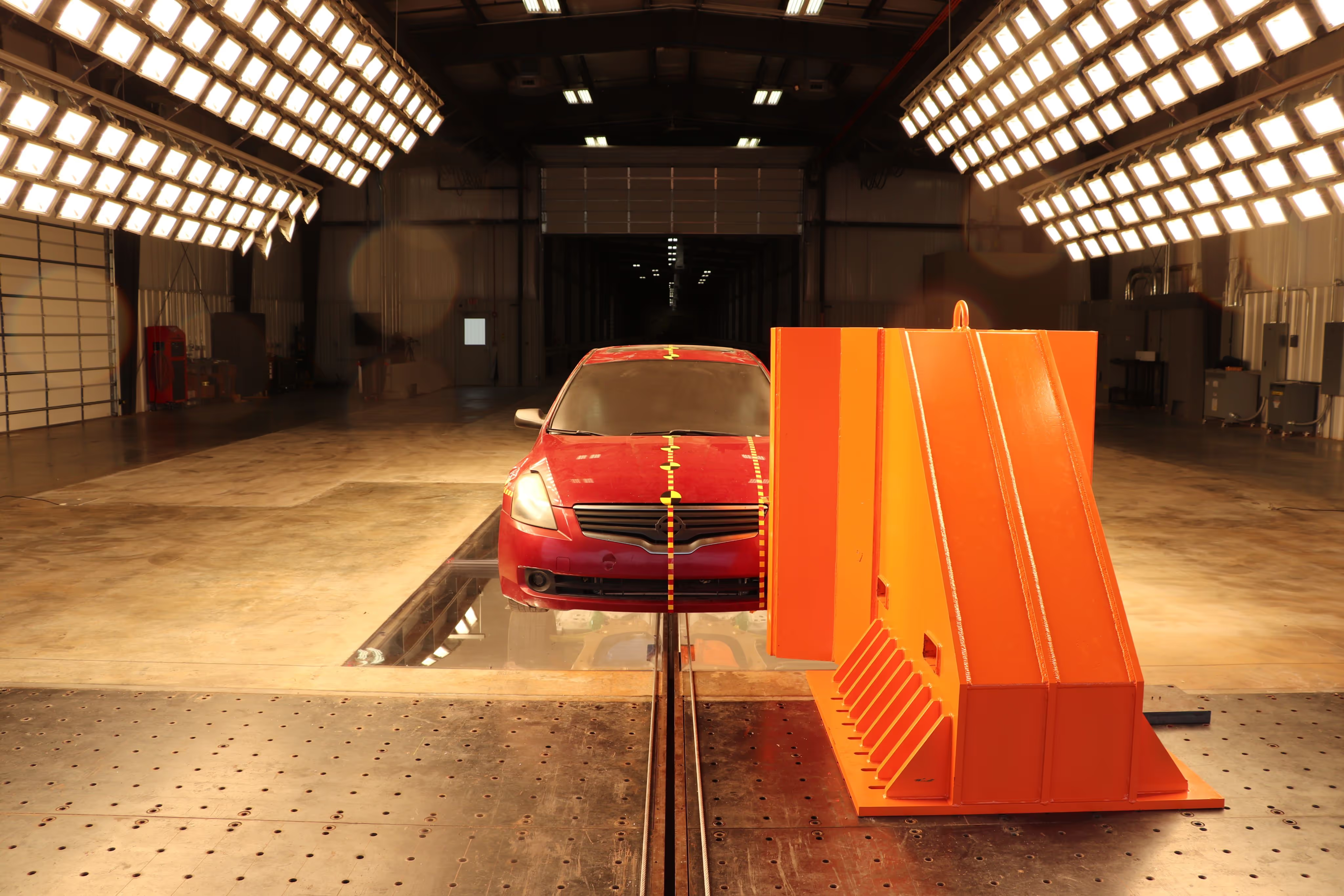
Automotive
From crash testing to durability evaluations, we ensure vehicle safety and performance.
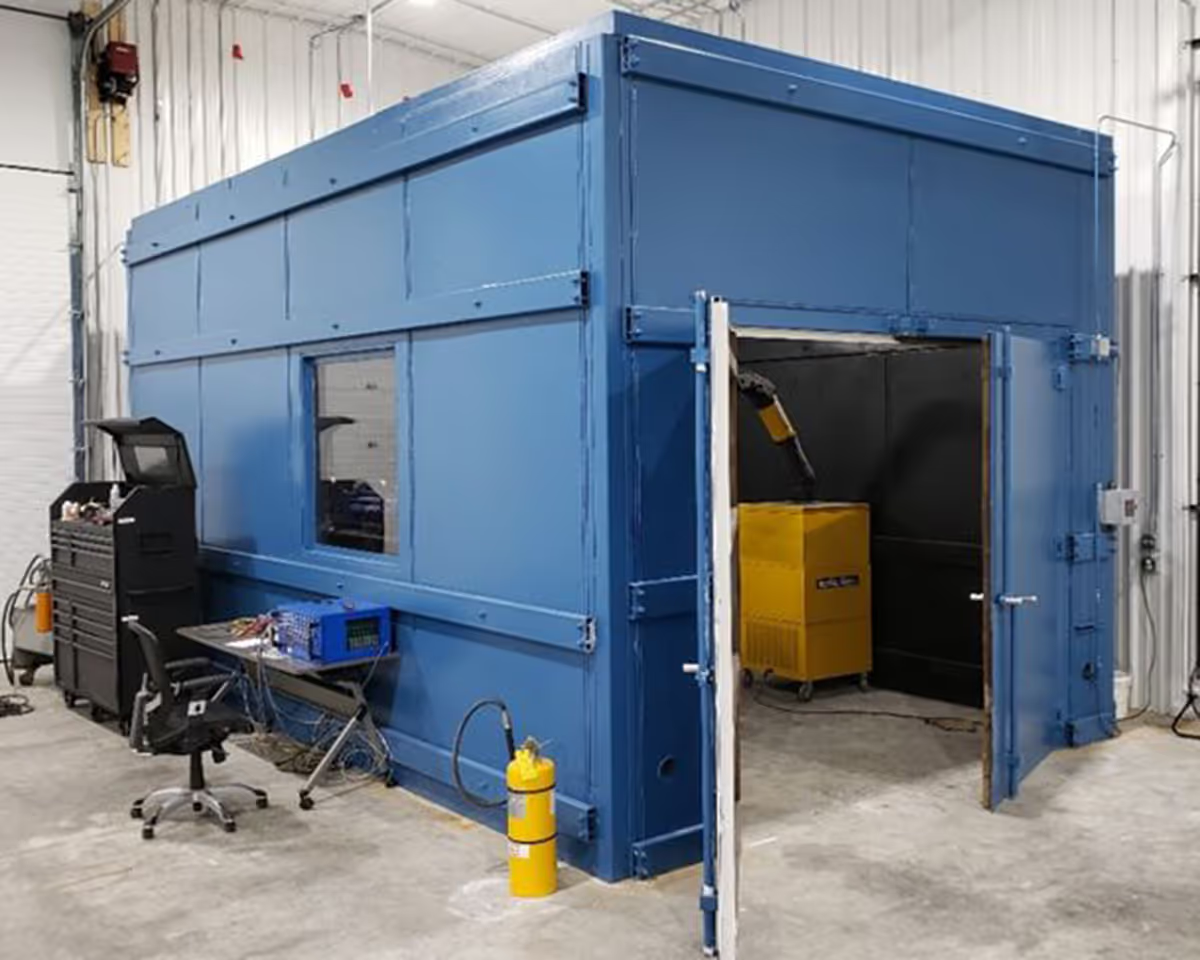
Battery
We offer cell-to-pack testing for electric vehicle batteries and energy storage systems.
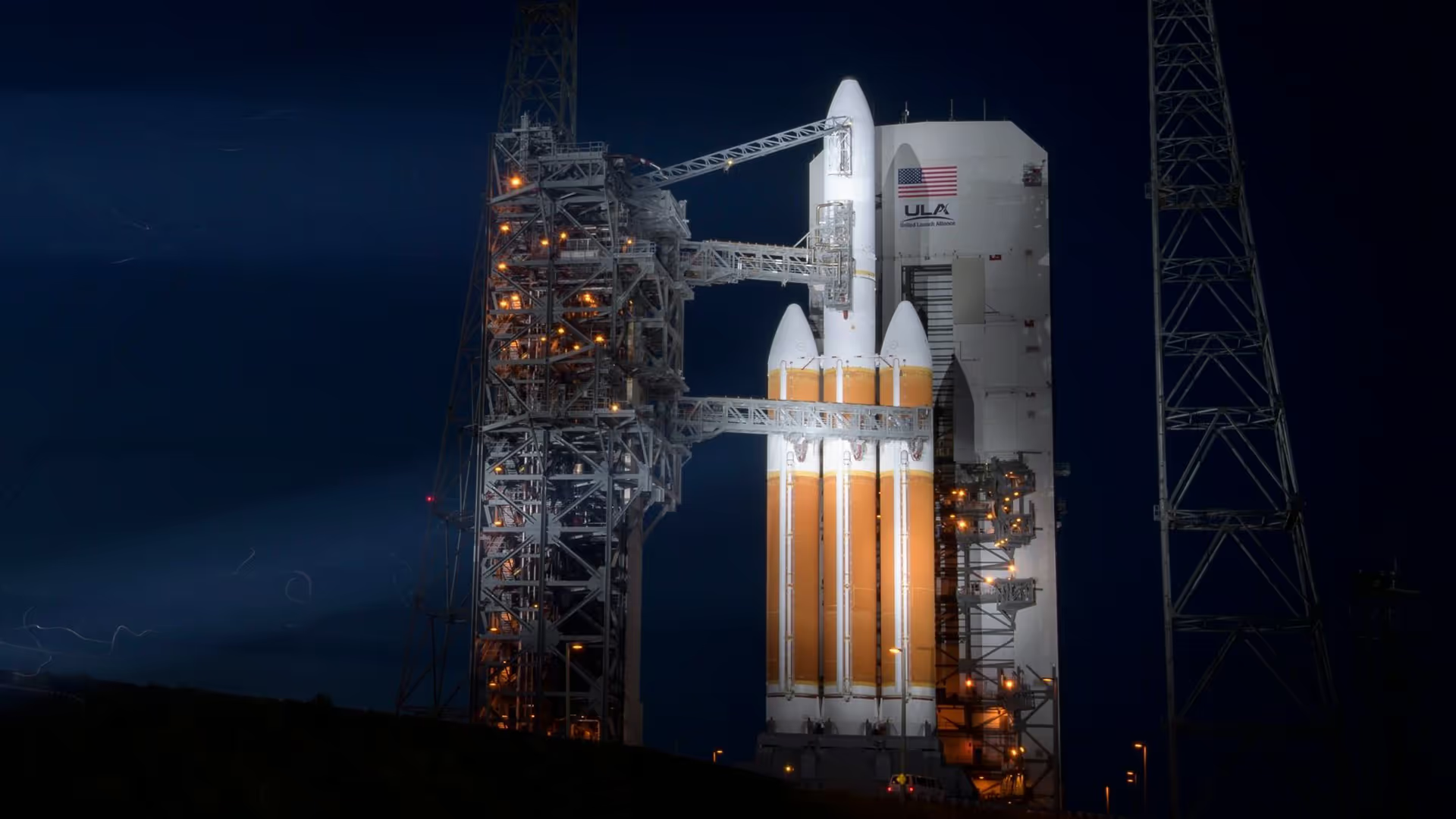
Aerospace/Defense
Our facilities support aircraft safety testing and flight qualification testing for the Space and Defense sectors.
Industry-Leading Test Equipment
At MGA, we provide industry-leading testing equipment used by manufacturers and regulatory bodies worldwide. Our comprehensive portfolio includes safety equipment ranging from impactors to full crash facilities, battery abuse testing systems, and durability test controllers, all designed to meet the highest standards of accuracy and performance.
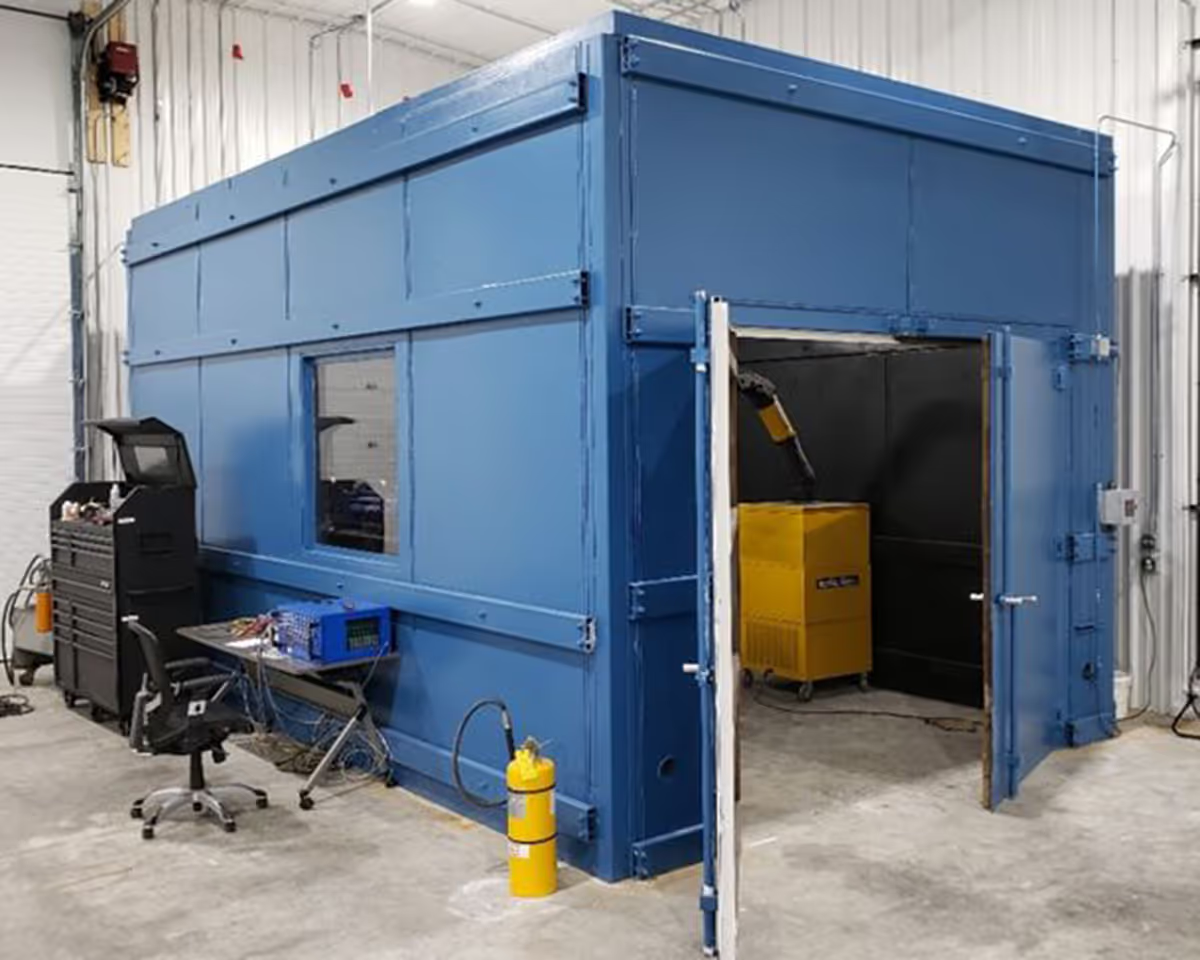
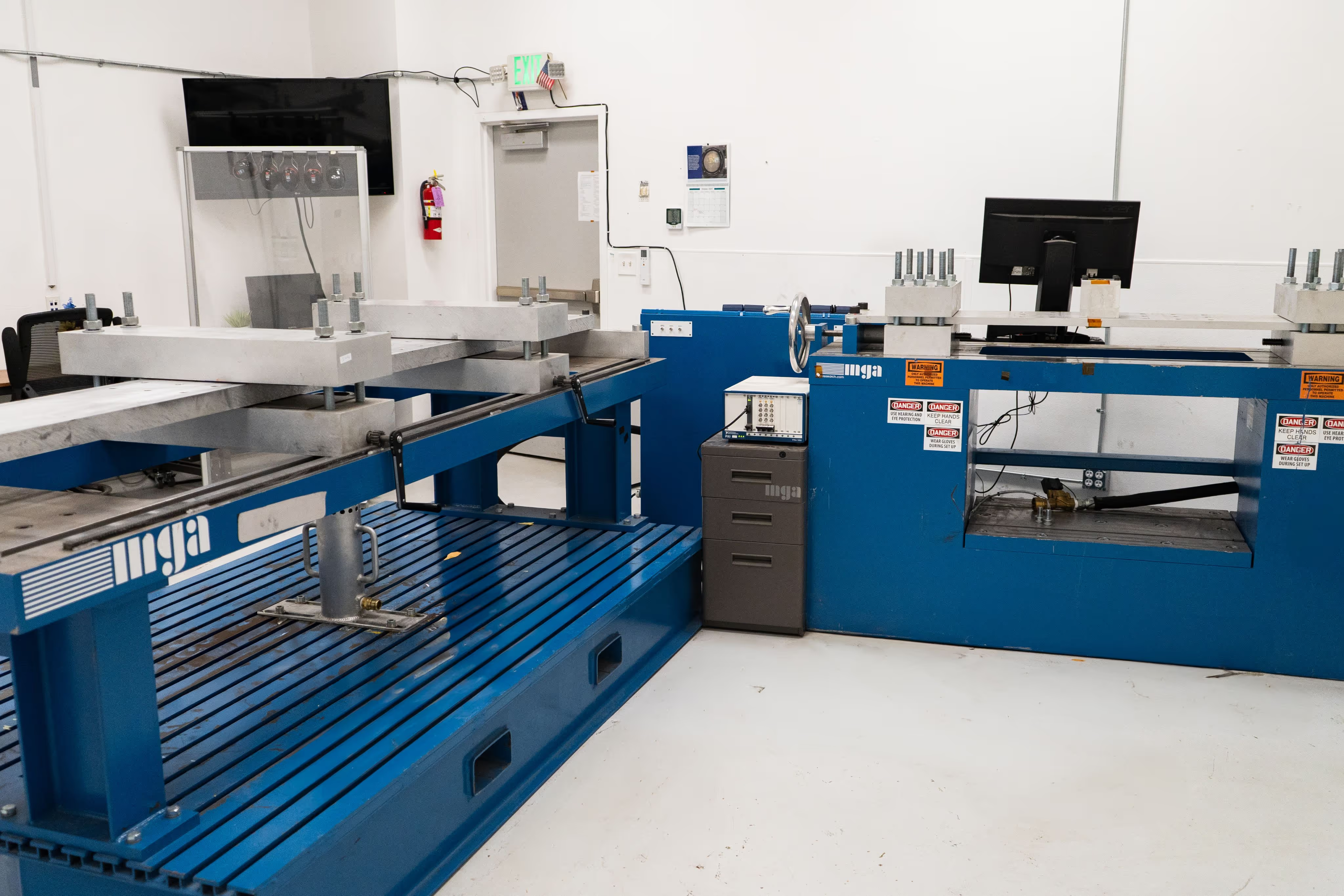

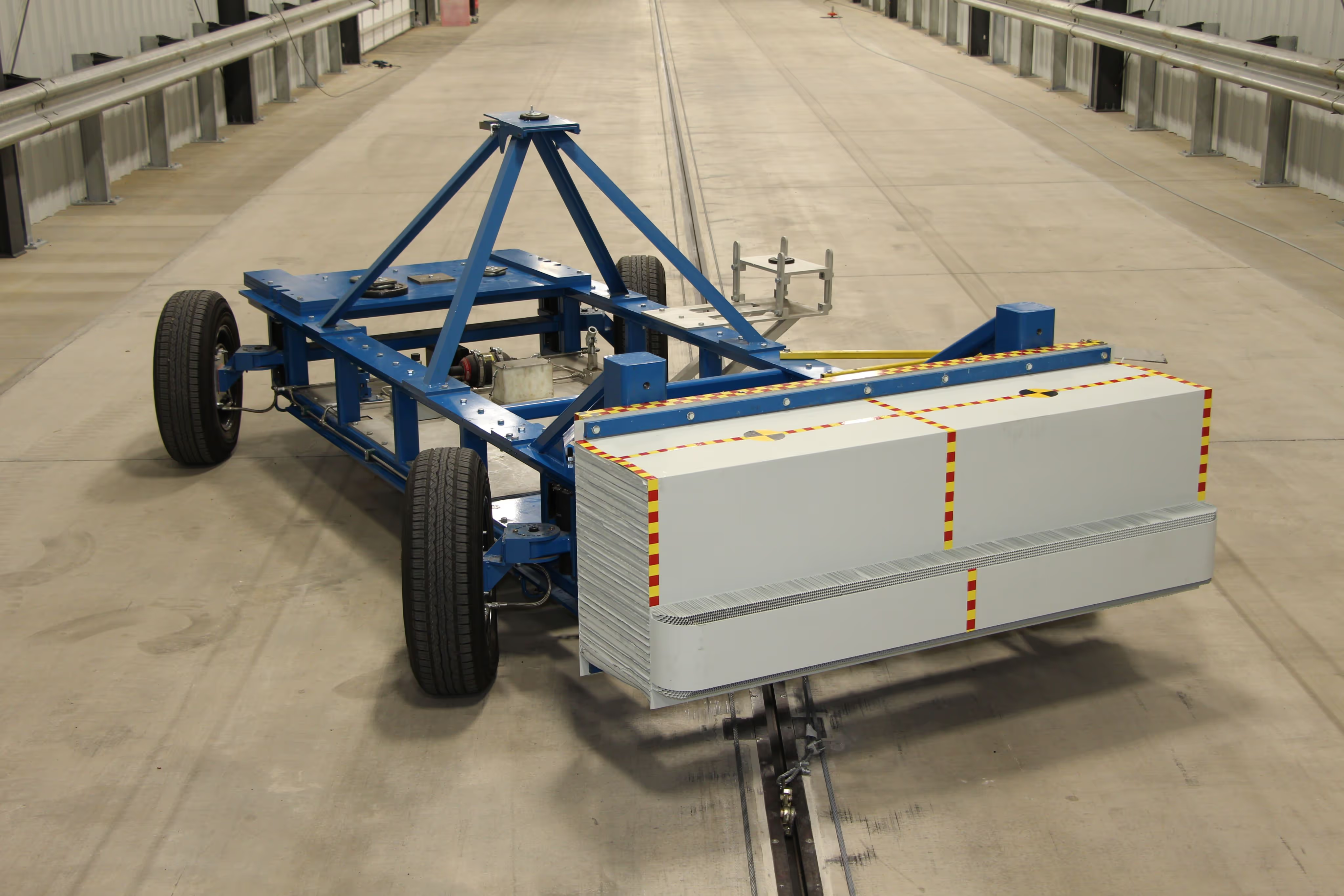
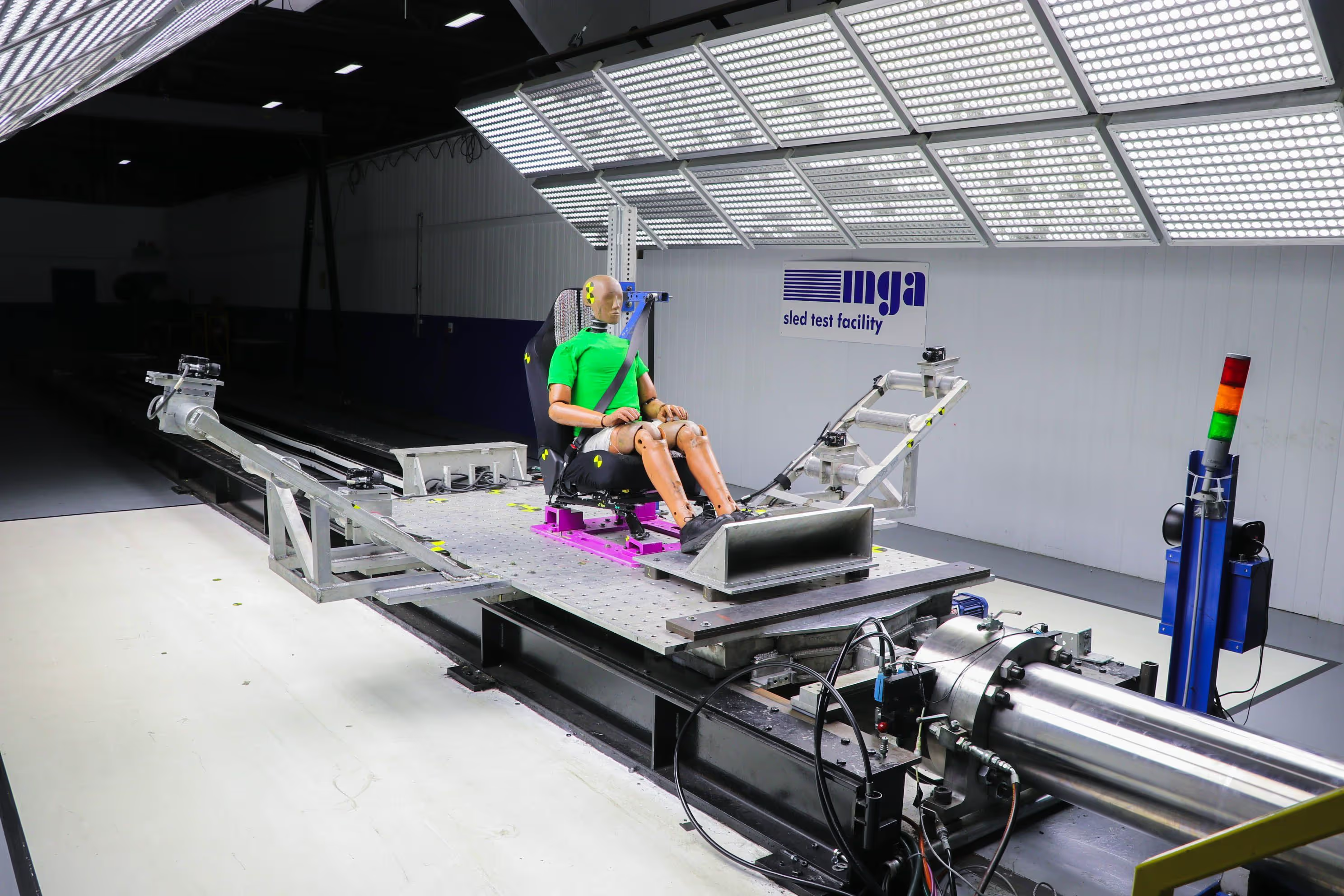
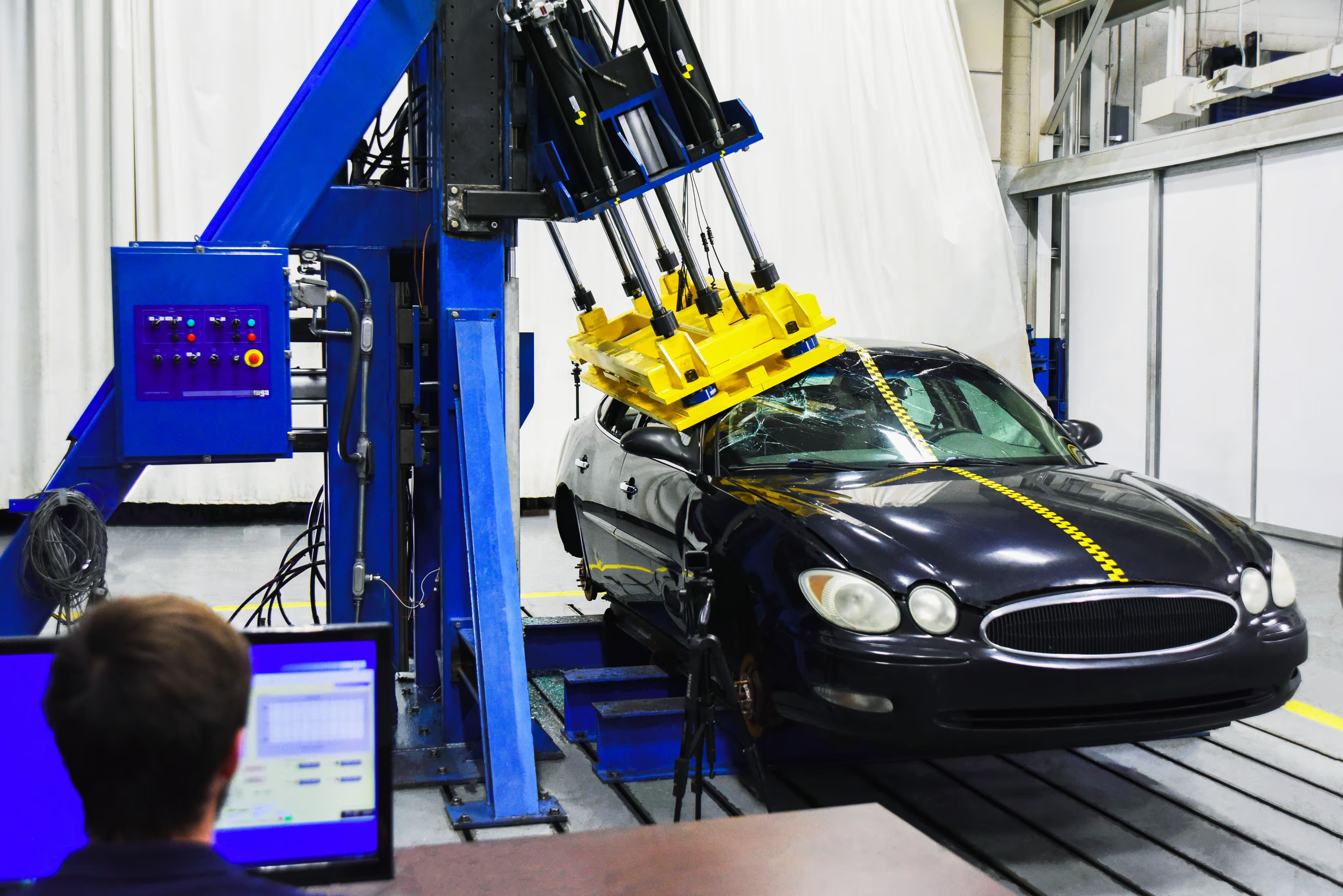
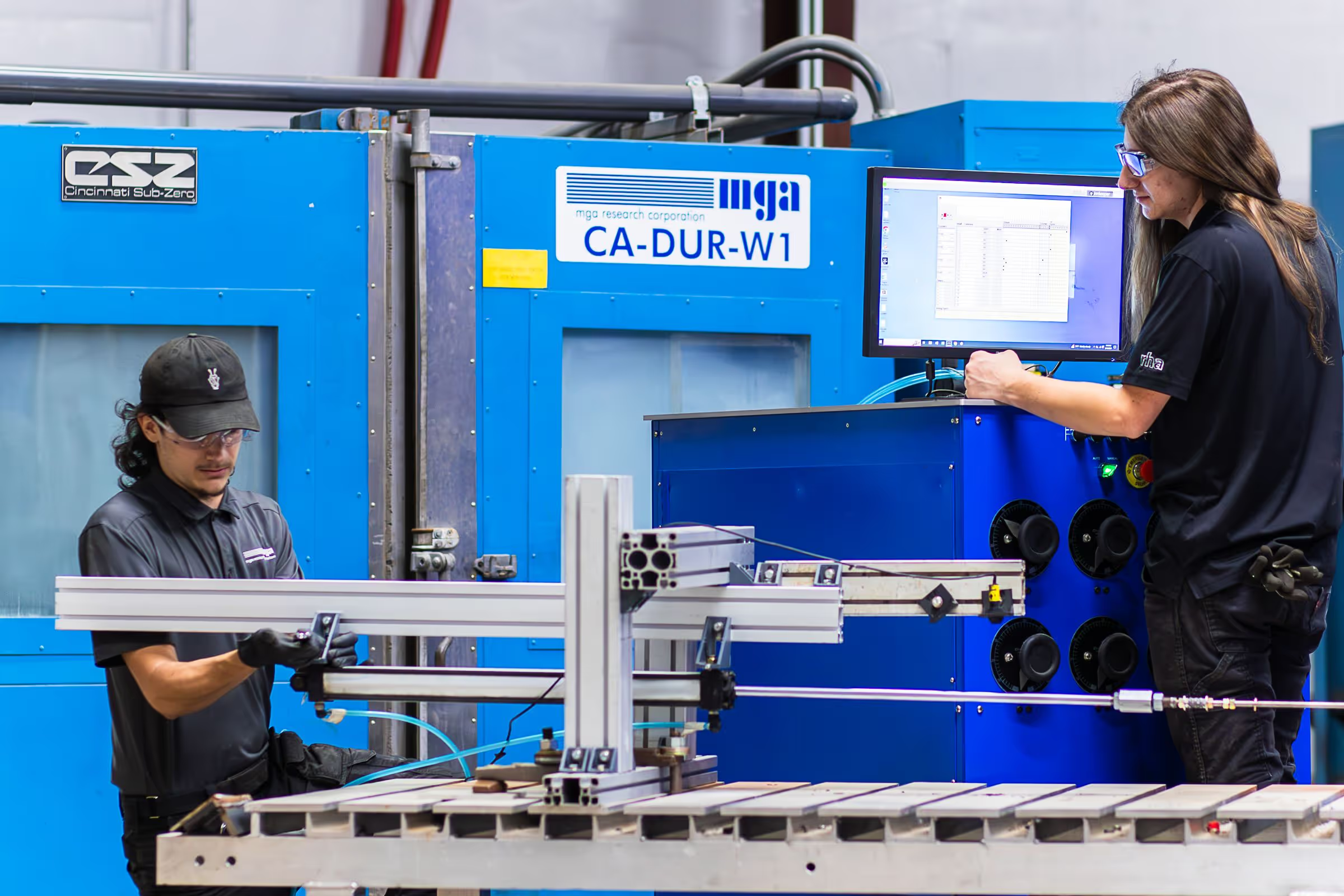
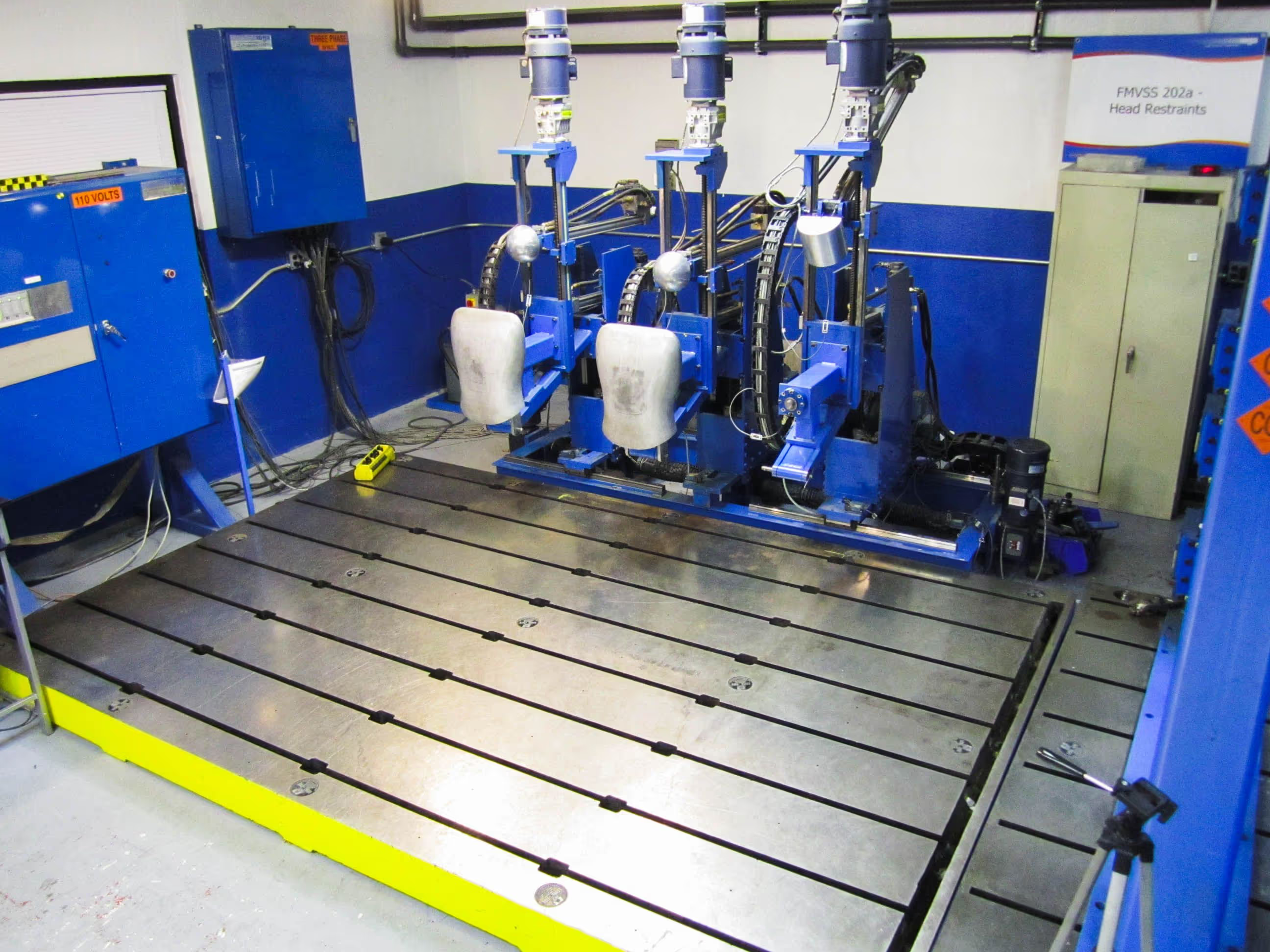
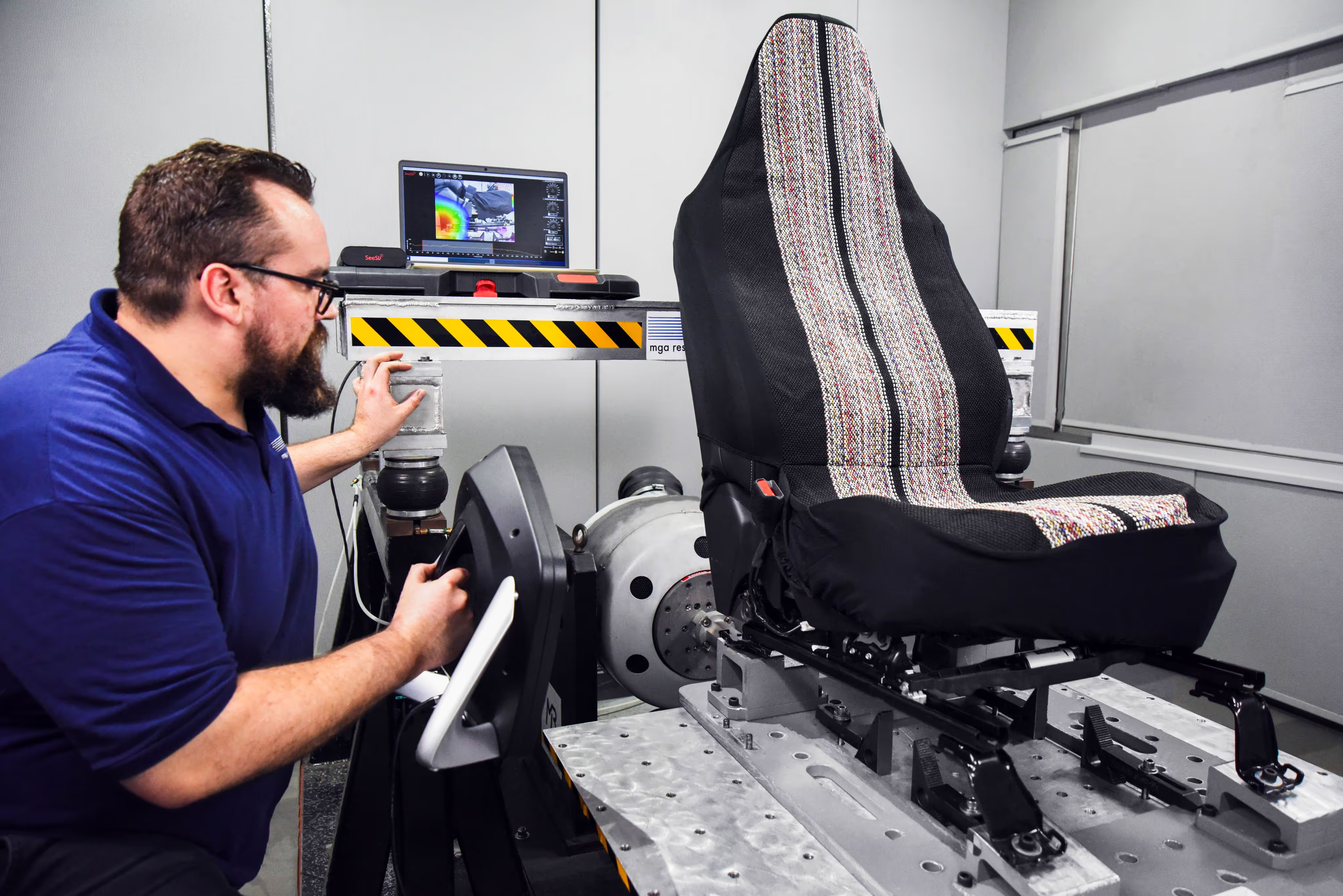
The MGA Advantage
We're not just another testing company. As a privately-owned business with 47 years of experience, we offer unmatched flexibility and expertise. Our cross-functional team can tackle complex projects with agility, delivering the results you need when you need them.
Latest from MGA
Stay up-to-date with our latest developments, industry insights, and testing innovations.
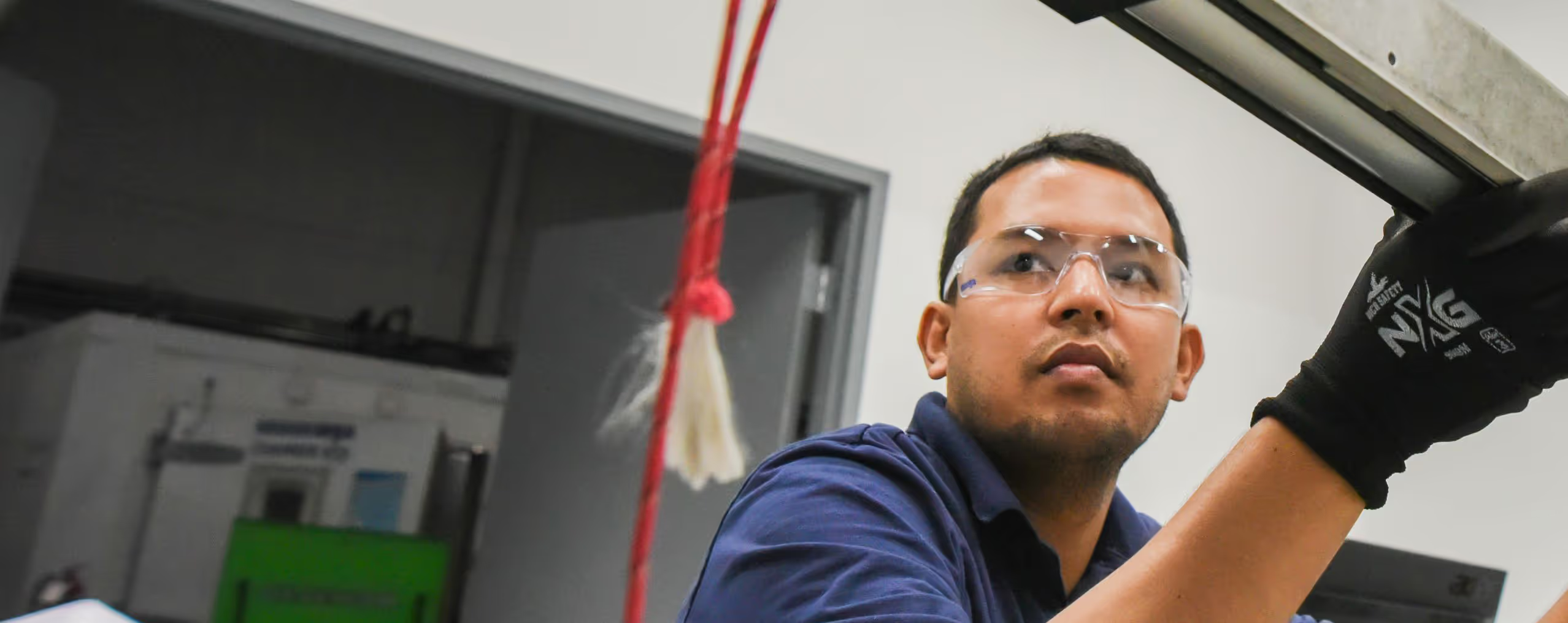
Ready to Get Started?
Let's discuss your testing needs and how MGA can help. Our team is ready to provide the expertise and solutions you're looking for.