
Sled Testing
MGA Research Corporation offers comprehensive sled testing services, leveraging over 30 years of experience to support multiple industries in evaluating the safety and performance of components and systems under simulated crash conditions.
Quick Overview
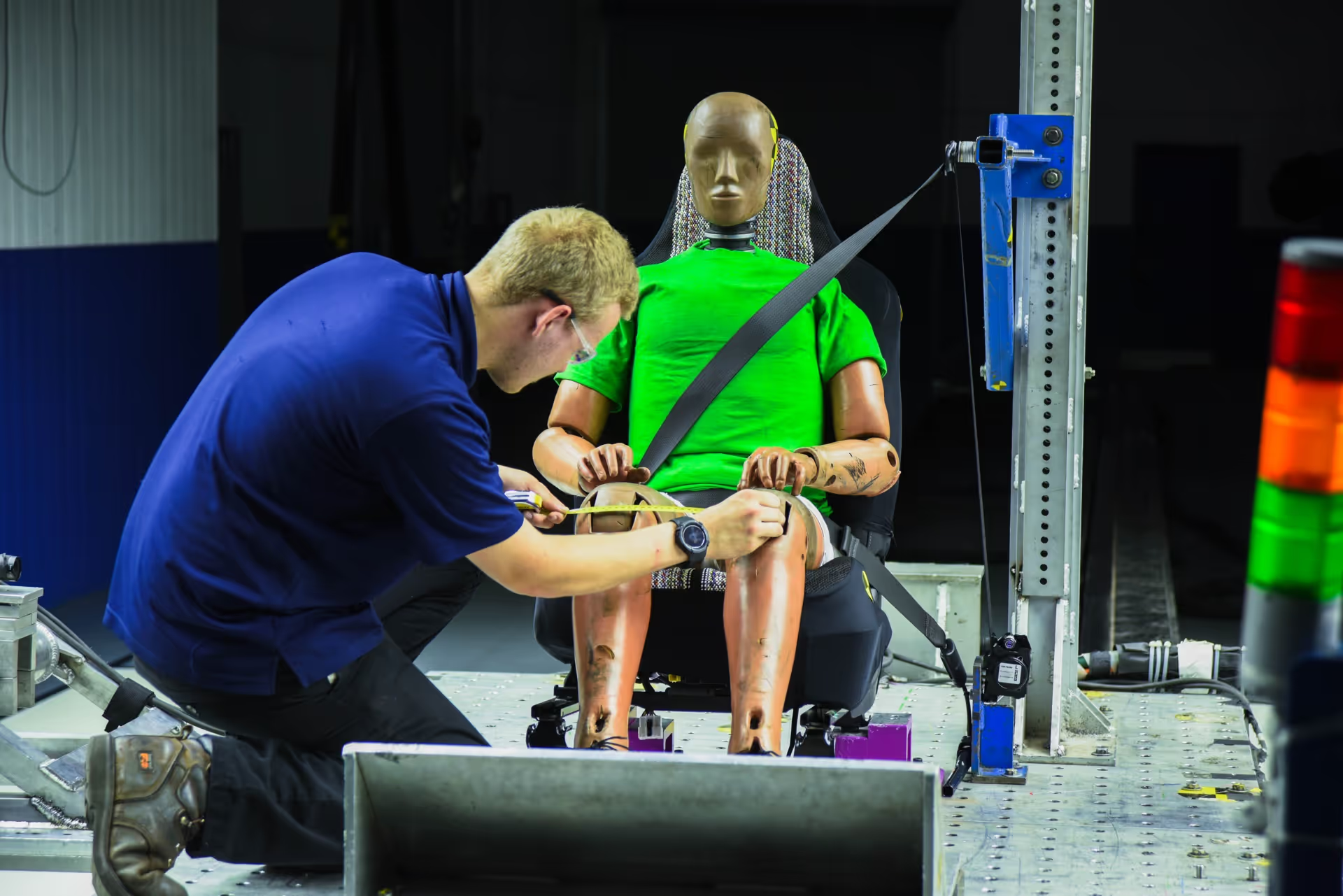
Comprehensive Sled Testing Services
From project conception to completion, our engineering and technical staff are able to provide support during every stage of the testing process, including test plan development, fixture and buck fabrication, and post-test analysis
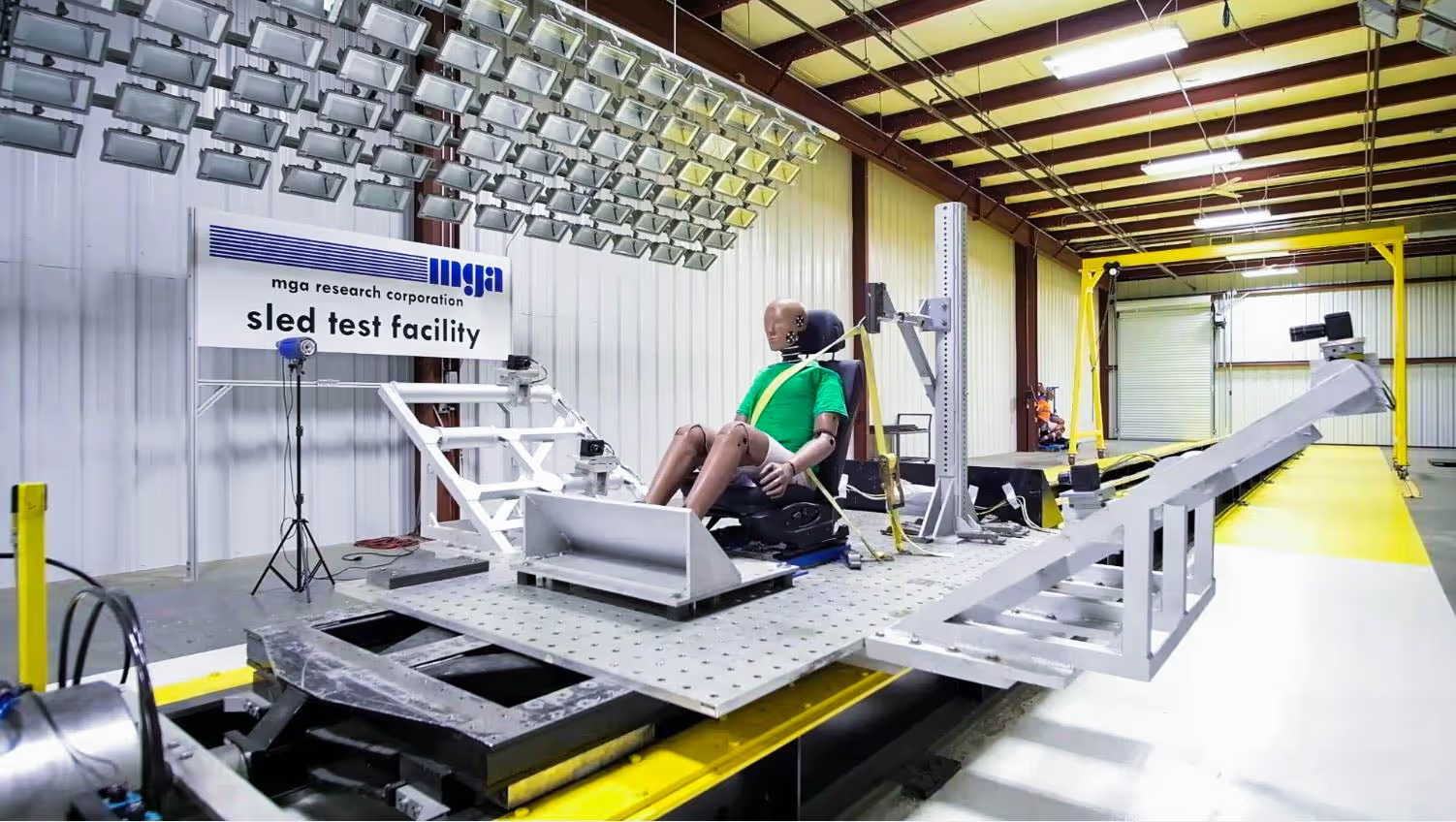
Advanced Equipment and Facilities
Our facilities feature state-of-the-art sled systems, manufactured by MGA, and data collection tools, supported by over 30 years of experience in delivering accurate and repeatable results. Our largest accelerator is 4.5 MN capacity.
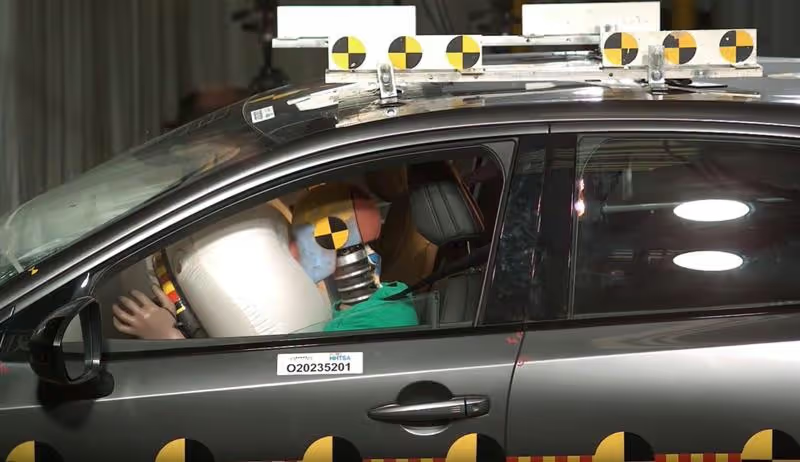
Automotive Development
Utilize MGA’s extensive crash and safety experience to support automotive restraint, seating, and interior safety development.
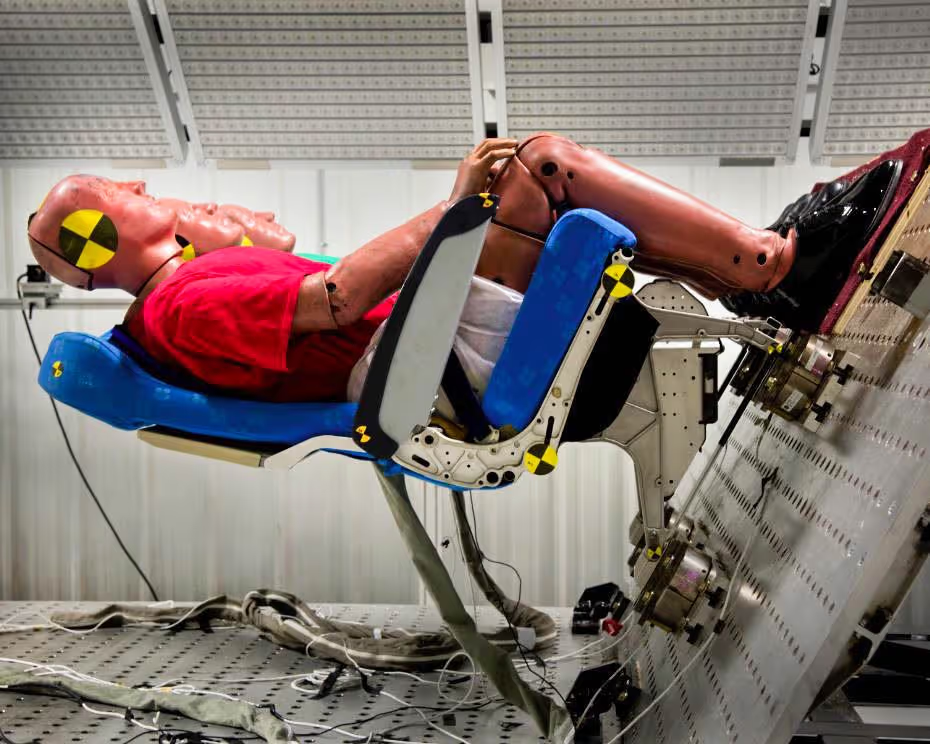
Aircraft Sled Testing
Perform dynamic sled testing per FAA Airworthiness Standards utilizing MGA’s custom sled carriages in Texas.

Child Restraint Systems
Over 20 years of experience in dynamic testing per Federal requirements, including the latest updates to FMVSS 213a.
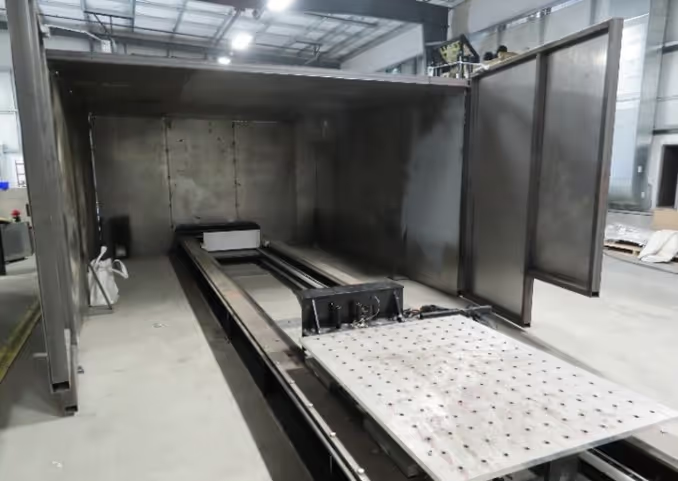
Dynamic Battery Testing
MGA has the capacity to dynamically test even the largest of modern EV battery packs. MGA’s Holly, Michigan lab offers integrated safety features to prevent and contain possible dangers.
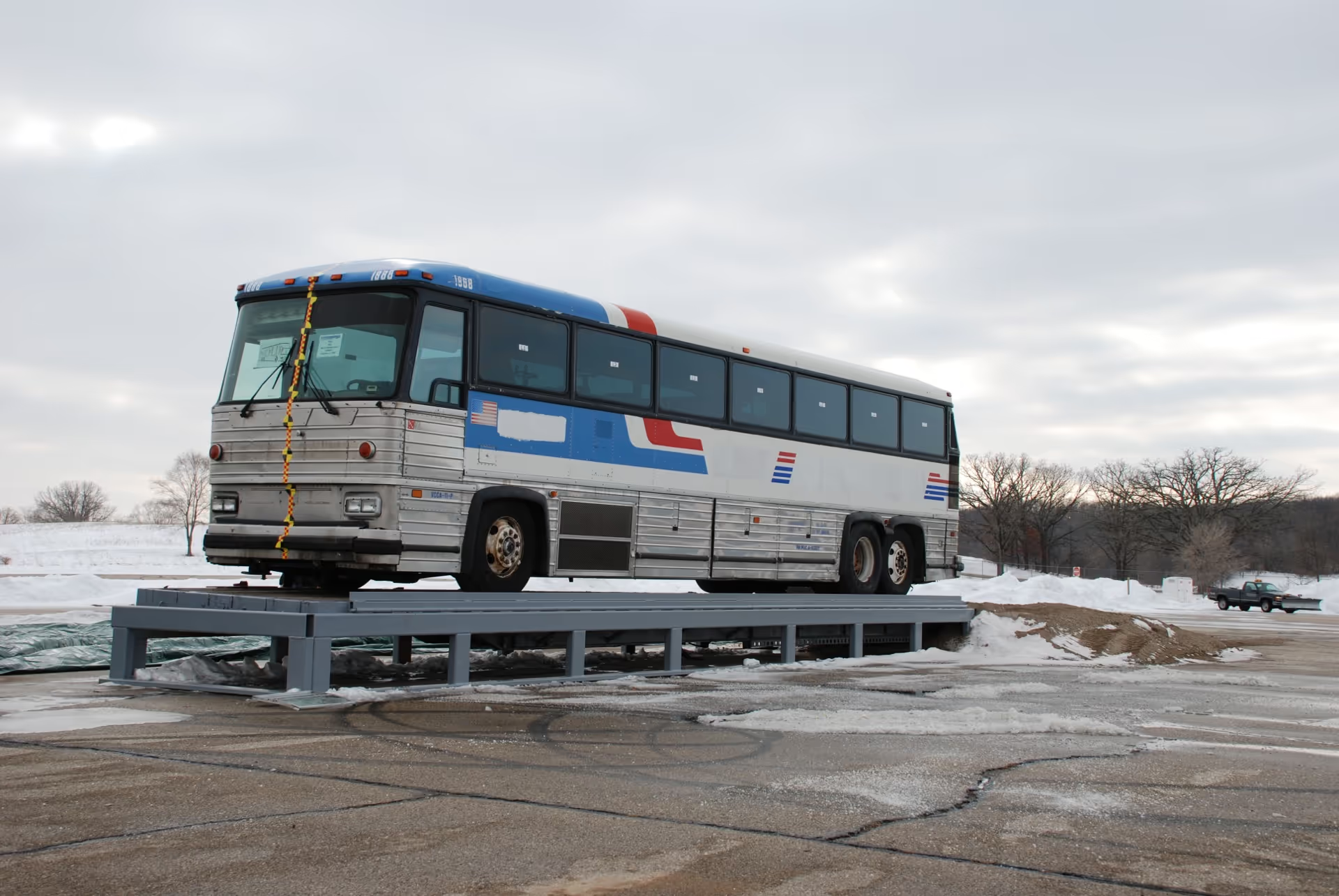
Mass Transit and Railway
We work closely with industry leaders to provide testing services according to the American Public Transportation Services (APTA) standards.
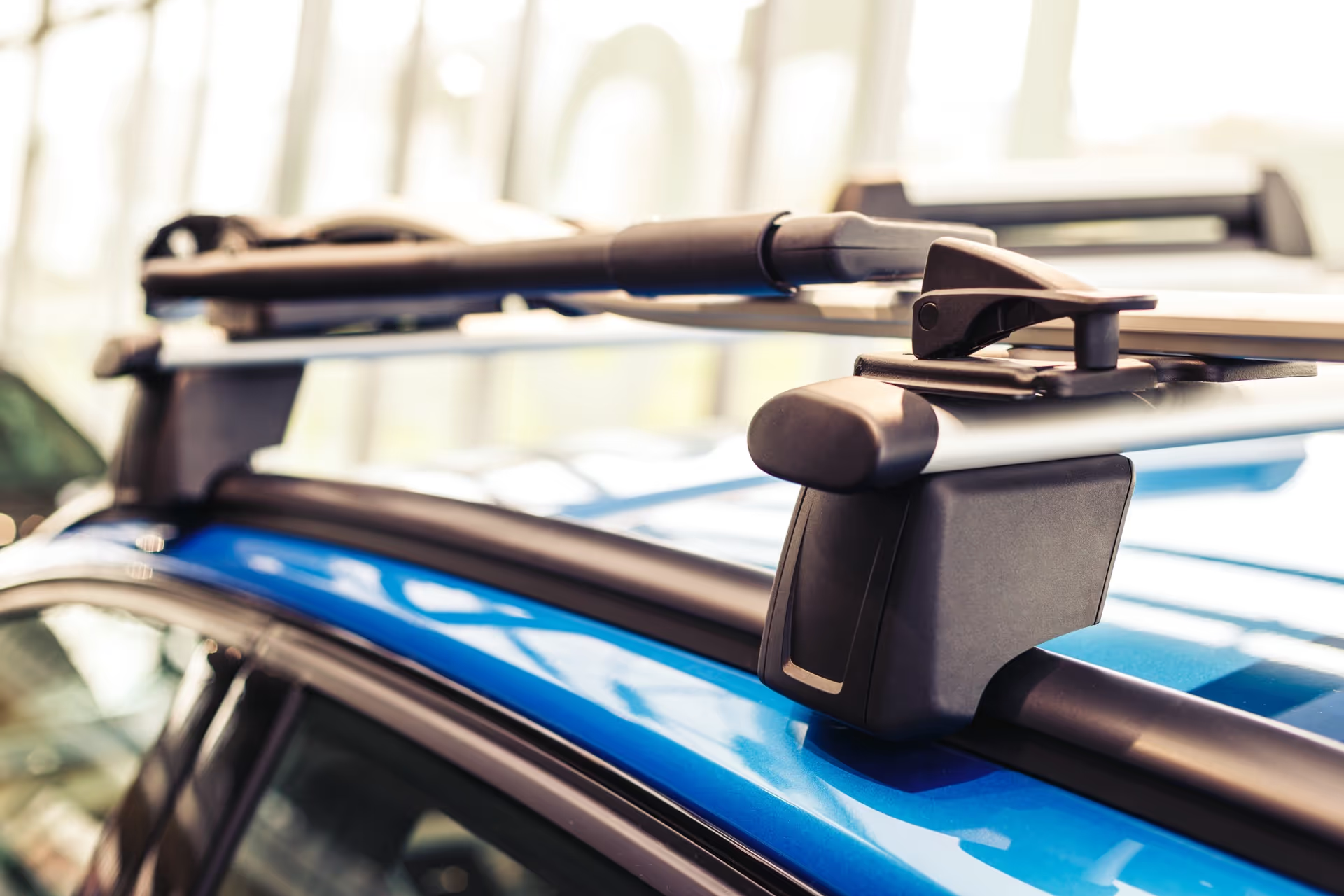
Vehicle Accessories
We support OEM accessory groups and the aftermarket with dynamic testing of fuel tanks, roof and bike racks, pet restraints, and more.
Sled testing has been one of MGA’s fundamental capabilities, supporting a variety of industries around the world for more than 30 years. With over a dozen of our sled systems in use across the company, our world-class team provides our clients with accurate, efficient, and repeatable results to help them achieve their most ambitious testing needs.
In addition to providing testing support through our comprehensive knowledge of sled testing in multiple industries, MGA also has the resources to collect any type of information our clients may request. On the data side, we have numerous types of sensors available such as accelerometers, angular rate sensors (ARS), potentiometers (string, linear, etc.), load cells (including seat belt and floor specific), and many more. During the tests we can focus on critical areas, providing our clients with an in-depth look as to what is happening dynamically by collecting high-speed video coverage at 1000+ frames per second.
We have an extensive inventory of ATD’s across all our locations including Hybrid III, THOR, side impact (WorldSID, SID-IIs, ES-2, etc.), rear impact (BioRID-II), and child ATD’s. MGA has made sled testing easier for our clients by providing on-site ATD qualifications and buck / fixture fabrication services to ensure seamless integration into our sled systems.
Not only do we perform tests daily at our own facilities, our internally designed and fabricated accelerator sleds have been installed across the world. With systems located in facilities ranging from automotive OEMs to child restraint manufacturers, our accelerator sleds have been proven to be the best choice for achieving our clients’ product development goals.
Sled testing is just another example of how MGA is an industry leader keeping our community safe!
Industries Supported:
- Automotive
- Aircraft
- Child Restraint Systems (CRS)
- Battery
- Transit/Rail
- And more!
What is Sled Testing?
When many people hear the terms ‘safety testing’, they will most likely think of a typical crash test involving a vehicle with test dummies (ATDs) crashing at high speed into a rigid barrier. Although this is a very valuable tool used in the automotive industry, it is not the only testing service provided by MGA. Sled testing is similar in many ways to an actual crash test as it creates a simulated acceleration shock, known as a ‘crash pulse’ within the automotive industry, to replicate the forces seen in a crash test.
There are a few main advantages to performing a sled test over a standard crash test. First, sled tests are generally considered non-destructive, meaning that an entire vehicle, aircraft, etc. does not need to be tested and destroyed to evaluate their internal parts. Instead, specific sub-systems or components can be evaluated independently, such as restraints, seats, HV battery packs, and many more. This also has the added benefit of reducing our client’s costs by limiting the number of samples they need to produce and test. Finally, due to the lower complexity of sled testing when compared with standard crash tests, we are able to perform tests more frequently and efficiently, optimizing the timeline of our client’s development cycle and delivering the results they depend on.
Acceleration Sled Testing
There are two main versions of sled systems used across the industry: acceleration and deceleration. MGA utilizes the former, meaning that our sled carriage and the test articles start at rest and are accelerated up to a desired maximum velocity. Essentially, this can be considered as a “Crash in Reverse”. In a standard crash test, a vehicle will travel down the track at a fixed speed before striking a rigid barrier, at which point the occupants’ momentum will carry them forward into the seatbelts and airbags. Instead, our sled tests work in the opposite manner, accelerating the vehicle and its components into the occupants, still replicating the kinematics of a crash test.
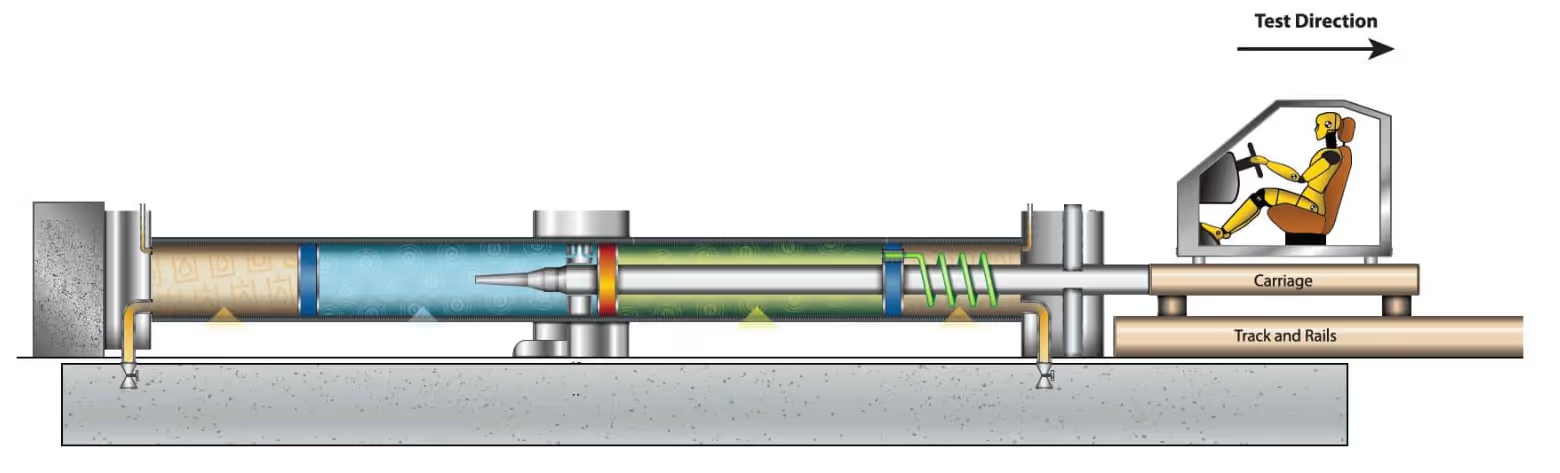
MGA’s sled systems incorporate a few fundamental components. Primarily, a thrust column is pressurized and used to deliver the amount of force required to propel a sled carriage longitudinally along a set of fixed rails. This column has a piston located within that is in contact with the carriage externally, while a metering pin is attached internally at the other end. Using principles of fluid mechanics, the metering pin is the ‘heart’ of sled testing as it varies the flow of air around its geometry, thus creating a sled pulse specific for each test.
We know that adaptability is key in providing the best support possible for our clients. Therefore, our sled carriages are designed to be used in a wide range of applications with multiple sizes and specializations available, including the ability to pitch and yaw test articles. Whether the product is as small as a phone or as large as a full vehicle, MGA is able to accommodate any sort of test.
Impact Carriage Testing
As an alternative to the standard acceleration sled testing MGA typically provides, we also offer impact carriage testing. This unique approach involves having two carriages placed on the rails, rather than just a singular carriage. To perform this testing the ‘launch’ carriage is positioned against the thrust column and accelerated into a stationary ‘target’ carriage positioned further down the track, upon which the test article is located. Impact attenuating material is placed at the contact point between the two carriages to achieve the desired acceleration characteristics.
Impact carriage testing provides a great solution for situations where a high G short duration type test is needed, especially with test articles that have a large mass/size. Many of these products are unable to be tested using standard shock/vibration equipment, thus making MGA’s impact carriages the perfect answer to perform the necessary mechanical shock tests. We have conducted this testing for our clients in a wide variety of applications, including full HV battery packs and other large vehicle components.
Custom Pulse Matching
MGA’s sleds are highly versatile when it comes to providing the exact pulse characteristics required for any given test. Using our cutting-edge in-house developed software, AutoPin, we can design and fabricate a metering pin that is able to meet any type of acceleration profile our clients may request. From real-world crash test acceleration data to CAE predictions, MGA has the tools available to match the severest of pulse profiles.
Sled Testing Services
Automotive Sled Testing
Occupant protection and the overall safety of vehicles on the road today is rapidly evolving. MGA collaborates with automotive OEMs, suppliers, and aftermarket clients to perform sled tests as advancements continue to be made throughout the industry. Our services are the perfect tool for validating CAE results and evaluating new components without the need to crash a full vehicle.
The scope of MGA’s automotive sled testing is diverse, ranging from seat jig tests all the way up to full buck-level tests. Using MGA’s vast array of ATD’s available, seat jig tests help our clients to assess the effect a new restraint or airbag has on the occupant’s potential injury risk, as well as to understand the structural durability of the seat itself after being subjected to a representative crash pulse. Given the efficient nature of sled testing, combined with MGA’s unrivaled ability to produce consistently equivalent sled pulses, our clients are able to make valuable comparisons between part revisions, new model year updates, and even competitor benchmarks.
Automotive manufacturers are highly focused on not only meeting but exceeding federal and international safety standards. NHTSA’s New Car Assessment Program (NCAP) and the Insurance Institute for Highway Safety (IIHS) are two significant resources consumers use to influence their decision when purchasing a new vehicle. As such, manufacturers make it a goal to ensure they receive the highest ratings possible awarded during these tests. MGA supports these efforts by providing full buck level sled testing for automotive OEMs. Multiple test modes such as an FMVSS 208 or NCAP Frontal test can be replicated using the exact ATD’s and acceleration pulse found during the actual crash test. In doing so, the occupant’s kinematics can be observed, and the theoretical injury values are recorded to give an understanding of how the vehicle performs. MGA gives our clients a major advantage as sled testing can be performed faster, more often, and at a fraction of the cost of a typical crash test.
In addition to providing exceptional sled testing services, we also work with our clients to design and fabricate any fixture or test buck needed for their application. MGA’s sled systems are capable of supporting large payloads, allowing us to fabricate a wide range of bucks including both ‘soft’/non-reinforced bucks and ‘heavy’/reinforced bucks, while also incorporating unique design features like multiple seating rows, built in high-speed camera mounts, and the ability to yaw and/or pitch the entire vehicle. This process can be done with any type of vehicle, from body-in-white (BIW), up to a complete running vehicle.
Supported Standards:
- FMVSS 208 Frontal
- NCAP Frontal
- IIHS ODB 2.0 (with XSensor vest)
- EuroNCAP Knee Mapping
- EuroNCAP Far Side
- FMVSS 202a
- And more!
Aircraft Sled Testing
As the aircraft industry strives to make their seats and interiors lighter and safer, our FAA accepted sled testing facilities have been a dependable asset for those looking to receive high quality testing. MGA’s sled testing services are able to support crash/emergency landing testing efforts within the aerospace industry, as well as provide due-care testing for any stresses these products may see.
Our sled carriages’ exceptional size allows us to run single occupant seats, row-to-row quads, as well as installation tests. The carriage can be pitched to varying angles (up to 60°), allowing the seats to be mounted horizontally, vertically, and every angle in between. These fixtures can also be yawed 30° in either direction for additional flexibility.
Supported Standards:
- 14 CFR 23.562 (part 23): Normal Category Airplanes
- 14 CFR 25.562 (part 25): Transport Category Airplanes
- 14 CFR 27.562 (part 27): Normal Category Rotorcraft
- 14 CFR 29.562 (part 29): Transport Category Rotorcraft
- SAE AS-8049 Parts 23, 25, 27 and 29
- And more!
Child Restraint Systems Sled Testing
MGA has been a leader in child restraint system (CRS) testing for global manufacturers over the last two decades. With extensive experience performing dynamic tests that adhere to Federal standards governing child restraint safety, our clients work with MGA because of the breadth of knowledge we have to perform these tests effectively. Holding the compliance contract for FMVSS 213 allows us to remain close to both the industry and its regulators, staying up to date with the newest requirements and standards. Our flexibility allows us to accommodate our clients’ needs during their product development process and remain current with the latest technologies in the CRS industry.
MGA personnel also stay in touch with the consumers’ use of child seat products. Many of our personnel have been certified as Child Passenger Safety technicians. They stay active in their communities helping real families understand and install their child restraint systems. Our familiarity with both the regulations and the real-world applications of child safety products gives us a unique insight into the industry. We apply this knowledge to our clients’ testing needs and endeavor to be a resource in the industry.
Primarily, sled testing is performed on a CRS to measure the safety of the child in the event a vehicle experiences a frontal or side collision. MGA equips test fixtures with high-speed cameras and sensors to record detailed data. This allows our engineers to evaluate structural integrity and determine if the restraint meets the injury criteria limits defined within various federal and international regulations. For instance, the federalized standard within the United States (FMVSS 213) requires that the child’s head acceleration, chest acceleration, bodily excursion for forward facing child restraints, and maximum rotation angle for rear facing child restraints all fall within a specific window for the CRS to be available for purchase in the US and be deemed as safe.
New to MGA’s CRS sled testing portfolio is the introduction of a universal side impact fixture, designed to meet the requirements of the recently released FMVSS 213a standard. This testing features a sliding test bench that contacts an impact attenuating material to deliver an impulse to the CRS representative of what it may see during a side impact crash. Our team has worked directly with representatives from NHTSA to help develop this standard, once again demonstrating our ability to be at the forefront of CRS safety testing.
Additional CRS Testing:
MGA is known for dynamic testing of child restraint systems using our acceleration systems, but we also provide our clients with detailed child seat inspections, and inversion testing services. Each child seat and its associated user manual must contain specific information that defines appropriate methods for use and ensures that the end user installs the CRS correctly. Our team works with clients to help them understand their product’s adherence to federal regulations regarding the content of the CRS’s labels and user manuals.
Supported Standards:
- FMVSS 213
- FMVSS 213a (Side Impact)
- FMVSS 213b (NPRM)
- CMVSS 213
- Consumer Reports
- And more!
Battery and EV Components Sled Testing
As the electric vehicle (EV) market continues to grow within the automotive industry, so does the demand for high level structural and safety testing on these systems. MGA has a long history of performing sled testing on battery components and providing our clients with industry-leading knowledge to meet and exceed their expectations. We have performed testing on batteries as small as those found within a watch, all the way up to full vehicle level battery packs.
Safety is always at the forefront for MGA, and battery sled testing is no exception. MGA’s sled systems and facilities have integrated safety features designed to prevent and contain any possible danger that may arise during or after a test is completed. Our expert teams have the knowledge to monitor HV packs for isolation as per FMVSS 305 and work with our clients to identify and diagnose potential faults when communicating with the device through CAN systems. If a situation arises where the test article is no longer safe to interact with, we can utilize our innovative sled carriage controls to remotely move the battery into a containment chamber.
Sled testing can involve testing with batteries and their related components in many shapes and sizes. MGA has experience performing EV battery tests at all levels: cell, module, and complete HV packs. We have the option to perform tests purely intended for structural purposes, as well as tests with live packs for a full system diagnosis. Our sled teams frequently work alongside our battery specific test teams to perform pre/post-test charge/discharge analysis, capacitance checks, as well as any other evaluations our clients may be looking for. The EV industry is continuously evolving, and MGA is always ready to provide world-class testing services supported by our sled testing groups.
Supported Standards:
- ECE R100
- FMVSS 305
- UN 38.3
- And more!
Mass Transit / Rail Sled Testing
Over the past few decades, the mass transit industry has grown to be a popular form of transportation for the daily commuter and leisure traveler alike. Mass transit infrastructure provides the public with a cost effect, eco-friendly and safe alternative to privatized transportation. With its growth in popularity, the American Public Transportation Association (APTA), has created several standards to improve upon the safety of these vehicles. MGA works closely with industry leaders and our clients to provide sled testing on multiple components such as seats and tables commonly used in mass transit applications.
Supported Standards:
- APTA PR-CS-S-011-99, Rev. 2
- APTA PR-CS-S-016-99, Rev. 3
- APTA PR-CS-S-018-13, Rev. 2
- And more!
Vehicle Accessories and Component Sled Testing
MGA is well known in the automotive industry for full vehicle safety testing, but we also lead the industry in evaluating vehicle components and accessories for OEMs, their suppliers and aftermarket manufactures. Sled testing is a great application for these types of products as real-world accelerations and forces can be replicated without the need for a full vehicle.
Common accessories we test can include trailer hitches, side steps, cargo and pet dividers, car seat mirrors as well as roof racks and their related attachments. Roof Racks and their attachments should be evaluated to ensure that the rack system and the load they are carrying stay safely mounted to the vehicle in the event of a crash. MGA follows the guidelines from ISO 11154 to perform the ‘City Crash Test’ which involves subjecting the test articles to a simulated acceleration profile they may experience during a crash event. MGA can perform tests to evaluate roof rack attachments such as cross bars, bike mounts, kayak mounts, ladders, ski/snowboard carriers, wind deflectors, and many more.
Fuel tanks and their associated parts are another critical vehicle component that must be designed to withstand the everyday forces a vehicle may experience – including a crash. Through sled testing, MGA can help our clients ensure that their fuel tank products remain structurally intact, but also eliminate any possible fluid leaks during and after the test. By collaborating with our crash facilities, we can subject test articles to the exact acceleration pulse recorded in a full vehicle crash, replicate the event with particular vehicle components during a sled test, and subsequently perform a post-test rotisserie rollover equivalent to the procedure defined in FMVSS 301.
Supported Standards:
- ISO 11154: City Crash Test
- FMVSS 301: Fuel System Integrity
- EU 2017/79 eCall Systems
- FMVSS 206
- ECE R16
- ECE R17
- SAE J2418
- SAE J1455
- And more!
Sled Equipment and Facilities Support
MGA has a long history of commissioning accelerator sled facilities internally for our various lab locations as well as for our external clients. Remaining loyal to our fundamental philosophy, all MGA sled systems delivered to our clients have undergone actual usage, refinement, and proficiency tests within the internal MGA laboratories prior to being offered for sale. We will work with our clients to develop a facility that is flexible, well thought-out, and meets the technical requirements they demand to operate efficiently. After a facility or piece of equipment is installed, in-depth training will be conducted by MGA engineers having comprehensive experience with sled testing to give our clients the best knowledge base possible. As we continue to support our customers, we strive to provide turn-key solutions for testing and equipment needs to a global customer base.
MGA’s Sled Types
MGA utilizes multiple sizes of sled systems throughout the company to provide world-class testing services. While all our systems operate under the same principles and deliver accurate and repeatable results for our customers, they each have their own advantages.
In general, MGA distinguishes our sled systems based on the diameter of the internal thrust column. The table below lists approximate capabilities for two of our most common sleds:
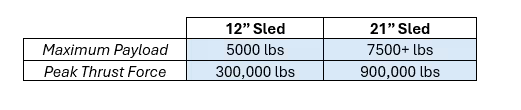
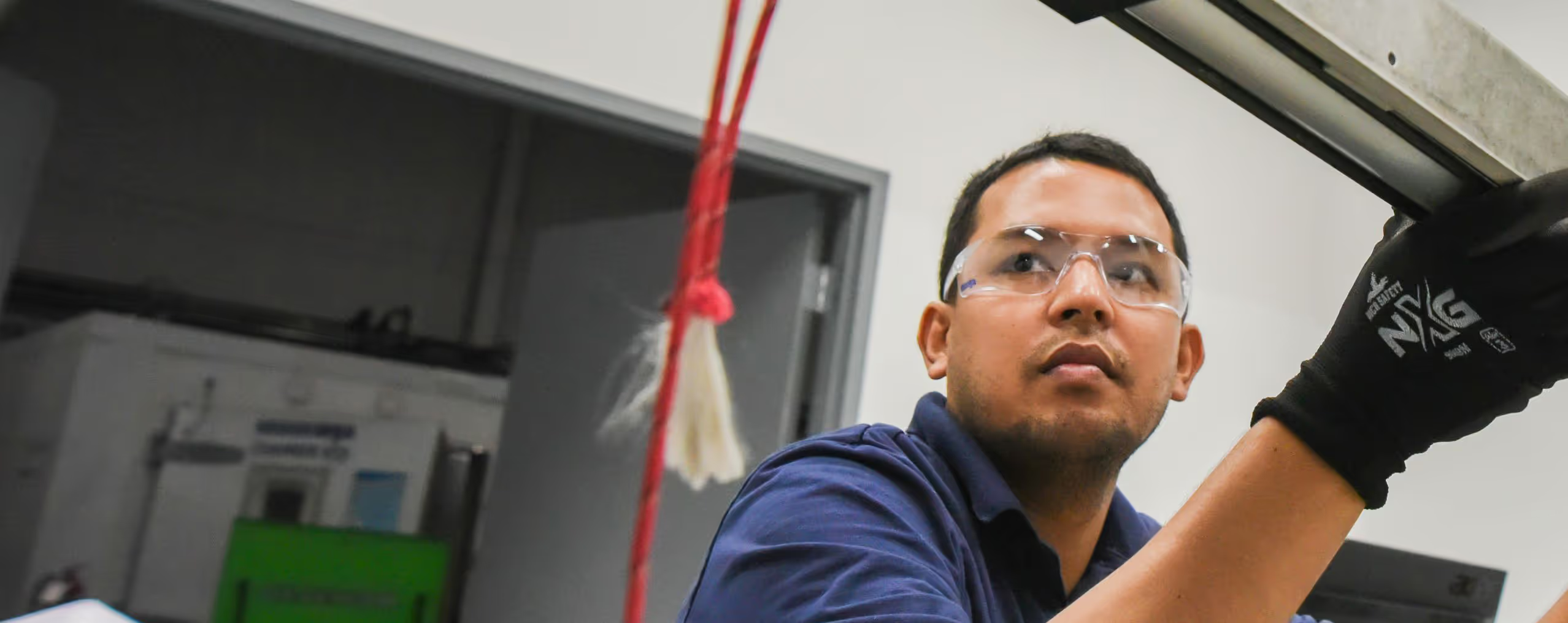
Ready to Get Started?
Let's discuss your testing needs and how MGA can help. Our team is ready to provide the expertise and solutions you're looking for.