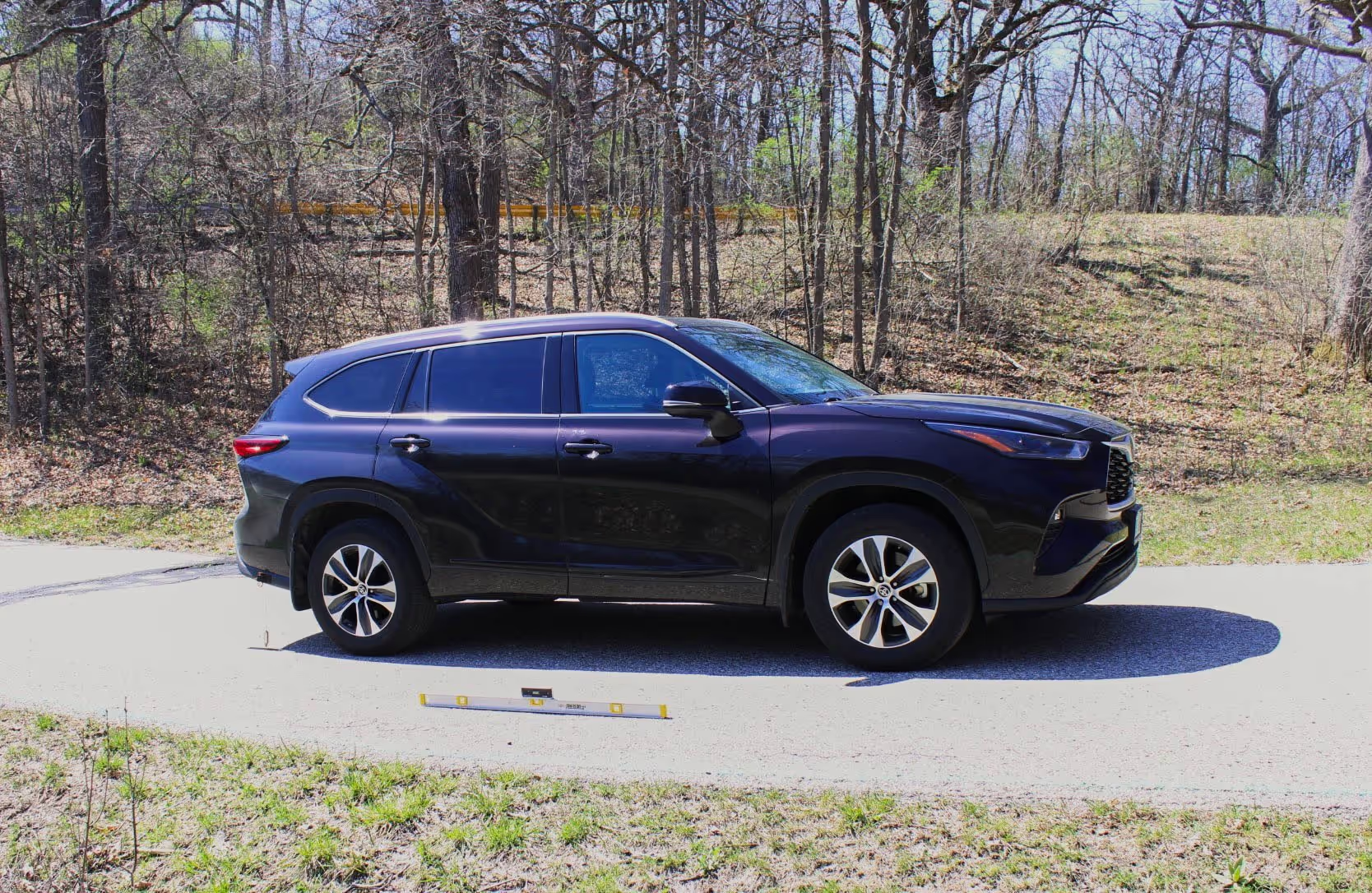
Exteriors & Closures
MGA Research Corporation offers comprehensive testing services for automotive exteriors, ensuring components meet the highest standards of aesthetics, functionality, and durability under various environmental conditions and usage scenarios.
Quick Overview
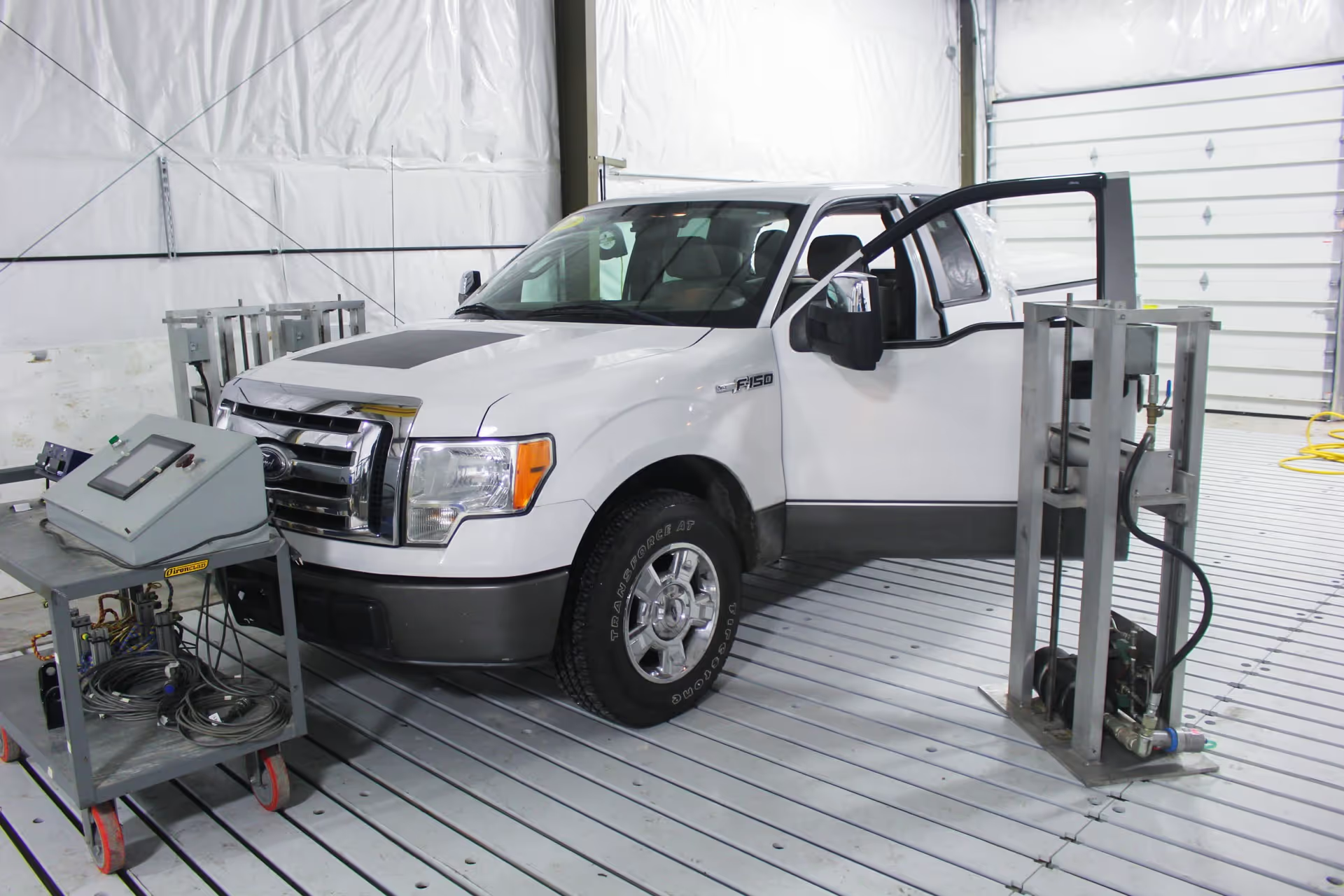
Comprehensive Exterior Testing Solutions
We offer extensive testing services for automotive exterior components, ensuring they meet the highest standards of aesthetics, functionality, and durability.
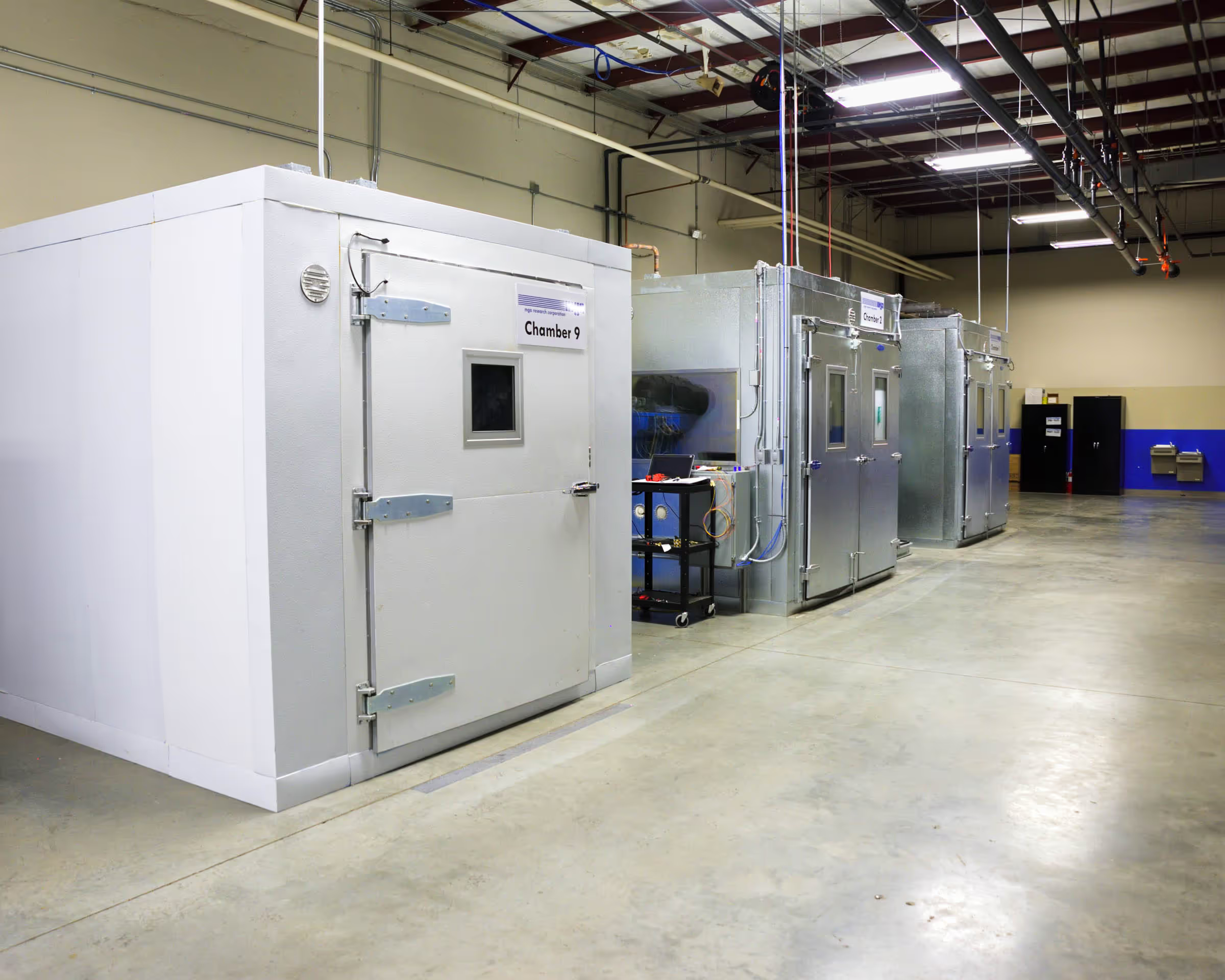
Advanced Environmental Simulation
We utilize over 100 environmental chambers nationwide, including mega drive-ins, to simulate extreme conditions and evaluate component performance.
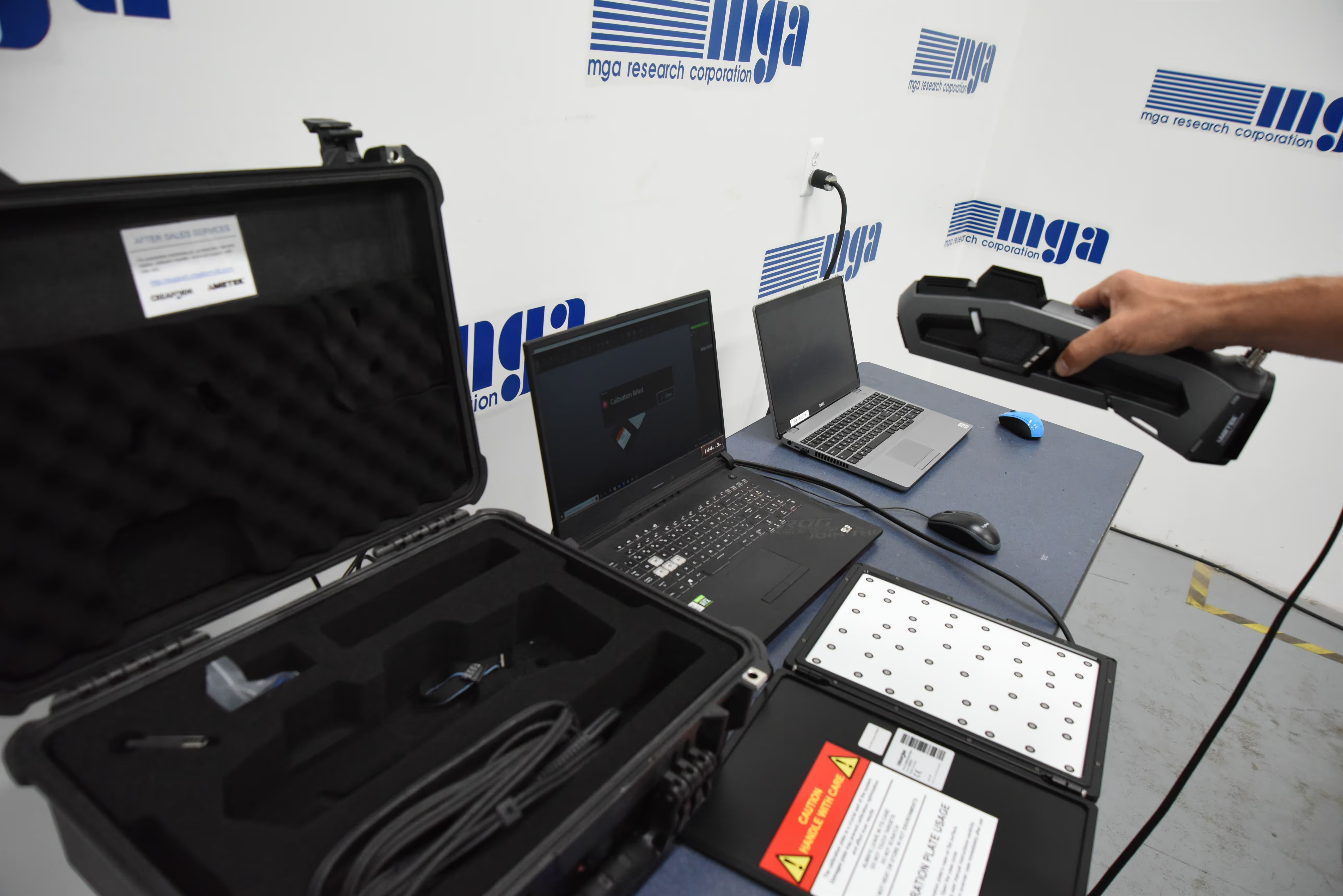
Diverse Testing Capabilities
We conduct a wide range of tests, including dimensional stability, cold impact, vibration, firm feel, and solar load simulations for various exterior components.
.avif)
Closures and Window Durability Expertise
We specialize in lifecycle testing for doors, trunk lids, liftgates, and windows, simulating real-world usage under various environmental conditions.
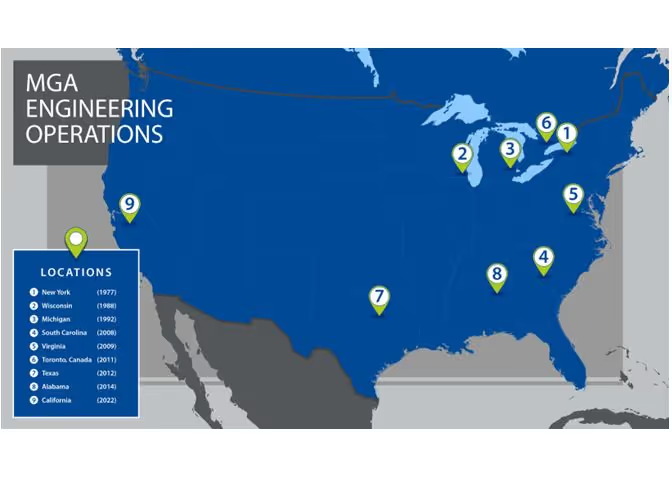
Multi-Location Testing Network
We offer testing services across nine North American laboratories, providing flexibility and rapid response to OEMs and suppliers in key industry regions.
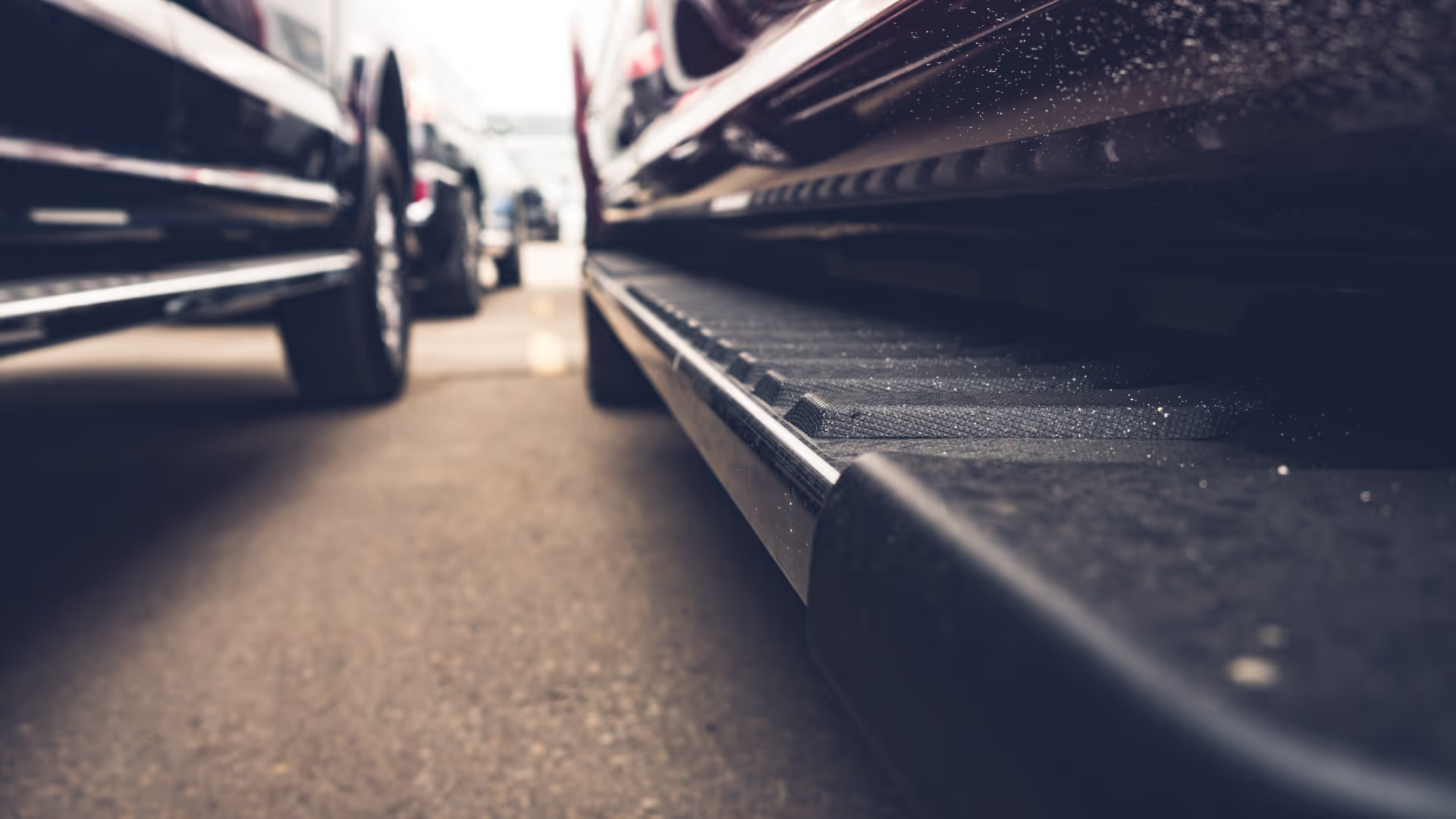
Customized Testing Solutions
We develop tailored testing methodologies and offer root cause analysis capabilities to address unique challenges in exterior component development.
It is said that first impressions last. With up to 60% of buyers relying on aesthetics and functionality in their vehicle selection, exterior designs have given a competitive edge to OEMs. New body geometry and lighting solutions have yielded the exploration of novel materials as well as manufacturing technologies. With cost in mind, finding a balance between an attractive design and reliable functionality of exterior component has proven to be a feat.
Developmental and production level testing for exterior components can be demanding. Whether it be months long of accelerated weathering exposures, or functionality use and abuse via life-cycle testing, MGA combines decades of experience and extended project support to provide a high level of urgency and care each program deserves.
MGA Advantage
With a network of 9 laboratories and an experience covering coupon level to full vehicle testing, MGA provides the following advantages to its customers:
- Over 100 environmental chambers nationwide.
- Extensive experience with major OEM specifications including GM, BMW, VW, Stellantis, Volvo, and Mercedes-Benz
- Large inventory of controllers including pneumatic, electric, sun-load, and servo electric.
- Large inventory of robotic arms capable of extreme temperature exposure.
- Large inventory of instrumentation (force, displacement, velocity, acceleration, temperature, and humidity)
- Ability to maintain aggressive schedules through our network of laboratories.
- Ability to develop customized testing methodologies.
- Experienced personnel supporting component level and full vehicle testing.
- Unmatched root cause analysis capabilities.
Temperature and Humidity capabilities
MGA currently has over 100 chambers nationwide, with over 10% of them being considered mega drive-ins as they can accommodate commercial vehicles up to 27’ feet long with up to 15’ ceilings. Our large network of chambers helps to provide the best possible timing and large quantity of throughput.
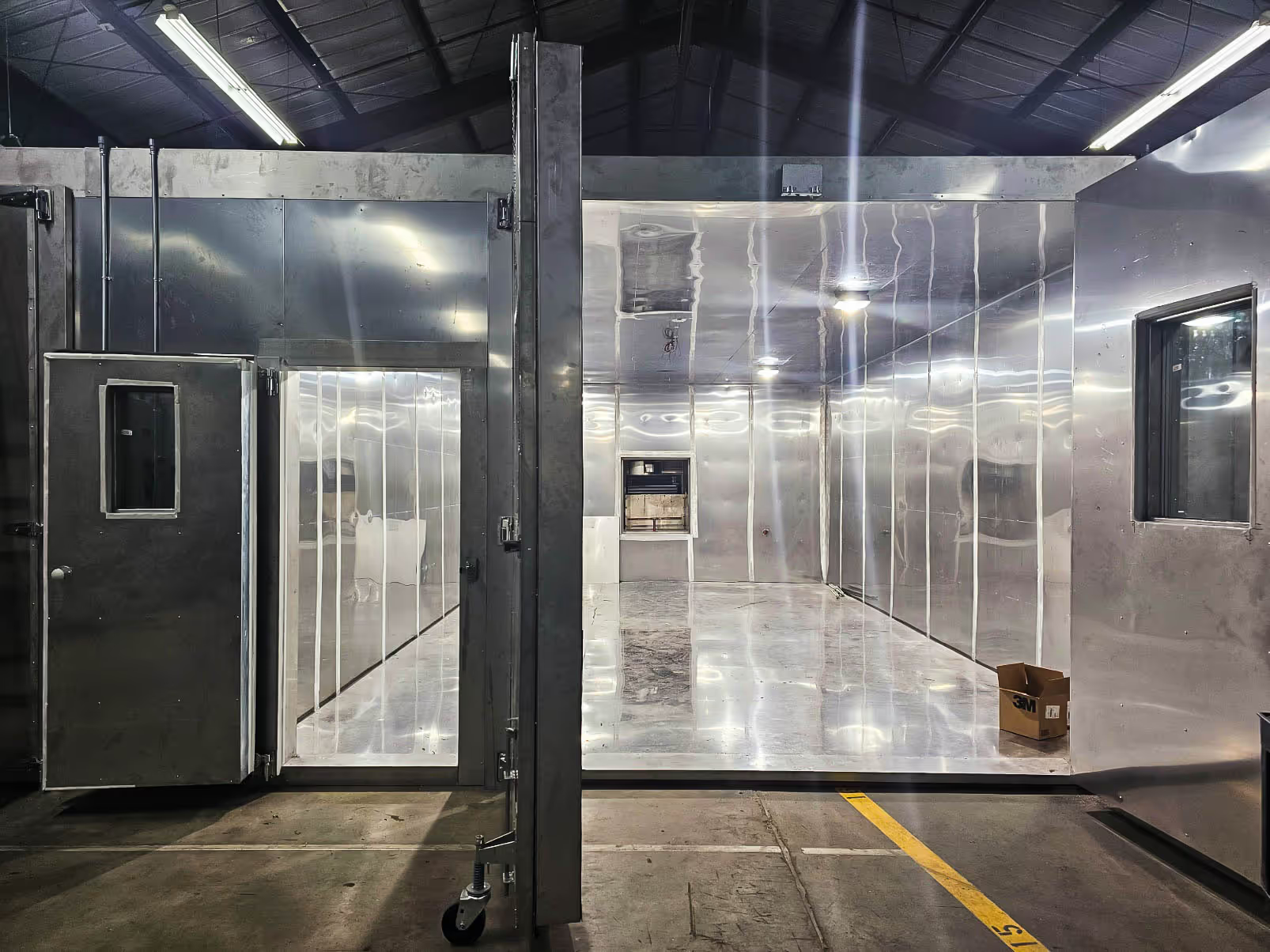
With achievable temperature ranges from -50°C to 150°C, our Drive-In chambers have the capability to handle the most extreme environmental conditioning profiles required per OEM specifications.
Maintenance on MGA’s environmental chambers is performed regularly and can be handled internally. Experienced personnel in this area allow for shortened down time if a chamber needs repair, and consistent maintenance of equipment allows for troubleshooting prior to an issue arising.
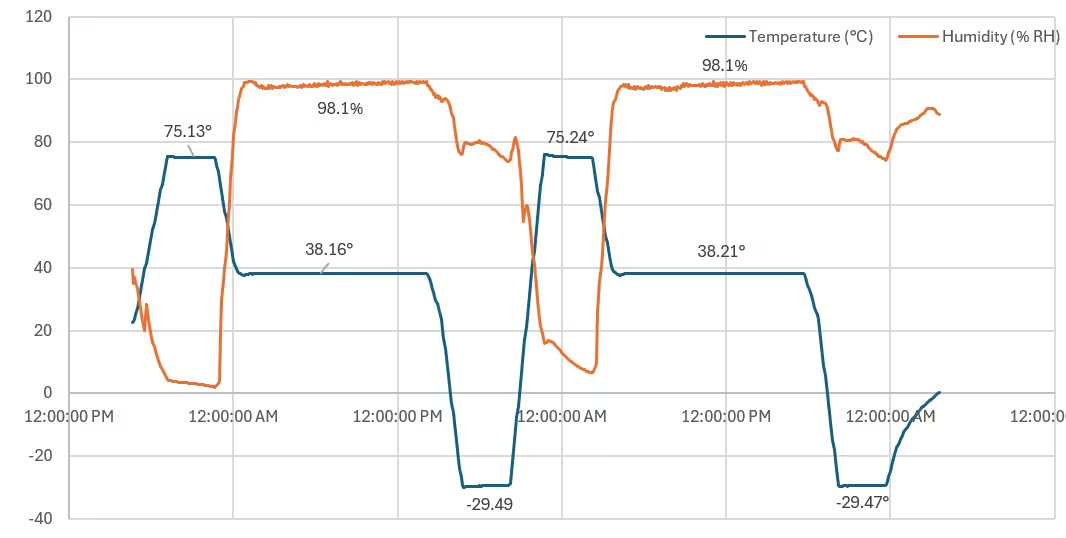
Services currently supported
Aesthetics
Resistance to harsh environment conditions is an unspoken expectation vehicle owners and operators have of the OEM. Covered in snow or parked under a scorching sun, exterior components are expected to not have any physical degradation. In such extreme conditions, the ability to live up to such expectations might not be as simple as one might think. In early development phases, each component is tested to extreme environmental conditions, replicating high heat, high humidity, extreme cold, UV exposure, and corrosion. Aside from environmental conditioning, exterior components also need to be able to withstand high impact at cold temperature, such as the ones seen from hail exposure. With requirements ranging from structural degradation (dents) to physical degradation (warpage, corrosion, etc…), OEMs have defined overall performance expectations that need to be met prior to releasing the product to the market.
Dimensional stability
The process of analyzing the effects of environmental conditioning. Typically, a 3-Dimensional scan is taken prior to conditioning, which is used as the standard (or reference) scan. Depending on the specification being followed, environmental conditioning consists of a cold, hot and humid temperature profile. An example profile could consist of 80°C, -30°C and 45°C with 85% Relative Humidity. After environmental conditioning is completed, a second 3-Dimensional scan is performed. These two scans are then compared to one another, and permanent deformation is measured.
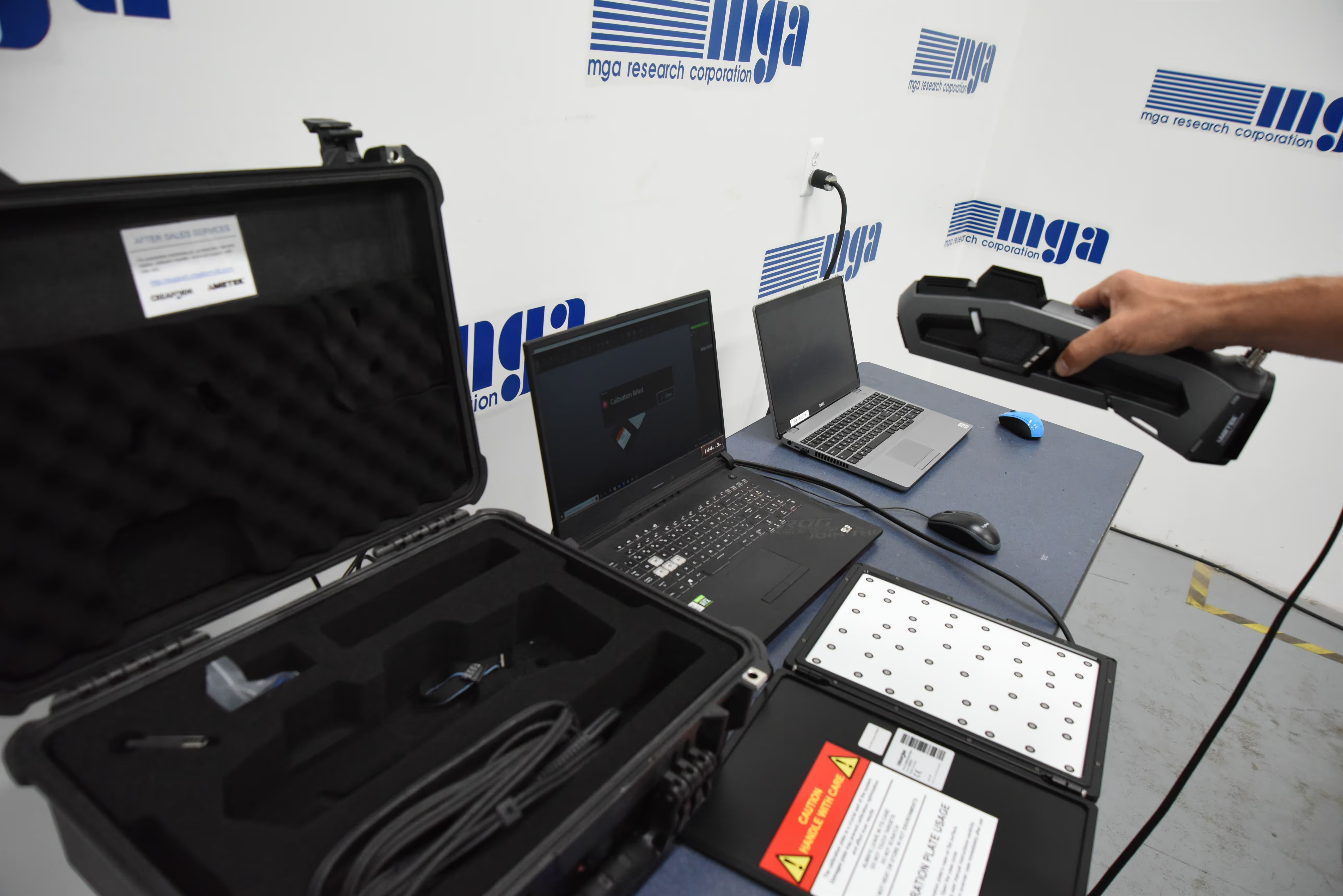
Additional types of analysis that can be performed, include, but are not limited to:
- Tenting evaluation of soft trim
- 2-Dimensional section cuts. For this process, two scans are cut in half at the area of interest. This allows engineering development from a particular axis at any location of a vehicle or component.
- Point map locations using a CMM (coordinate measuring machine).
- Color evaluation
- Gloss evaluation
- CAD comparison. Using computer software for analyzing CAD, MGA can compare scans of vehicle components with CAD that is provided by the customer. In this event, MGA is then able to deliver scan files that adopt the vehicle orientation.
Cold Impact
The purpose of cold impact testing is to determine if exterior trim components will suffer damage when impacted by small objects. These objects may include road salt, gravel, stones, or rocks. This testing can be applied to all exterior components at extreme cold temperatures to ensure the components become more brittle and susceptible to damage. This test can be performed at a component or vehicle level. In most cases, the UUT (unit under test) will be subjected to a cold temperature (typically -30°C) for 4 hours. The part is then removed from the environmental chamber and impacted in ambient conditions within a few minutes. The size and mass of the impact form, as well as methodology of impact is dependent on the vehicle location and OEM requirements. In fact, OEM requirements would often mandate a free fall ball drop, or a pendulum swing using a ball of specific size and mass. Once the methodology is identified, the energy requirements would determine the height of free fall or free swing. Meeting the cold impact requirement would depend on the OEM’s overall visual evaluation requirements.
Vibration
Vibration testing simulates the real-world vibrations that a vehicle and its components would experience during regular operation to ensure that components can withstand the vibrations over the vehicle's expected lifetime, and their intended performance under vibration conditions is maintained.
MGA offers a wide range of vibration capability with over fifty electrodynamic shakers plus multi-axis simulation tables to support vehicle interior development and validation.
Firm Feel and Materials Testing
Firm feel testing is a methodology developed to determine the stiffness of exterior components at different environmental conditions. A flat (often cylindrical) load applicator (usually 15mm – 50mm in diameter) is pushed into exterior components at a constant rate until a specified load is reached; deflection measurements are recorded throughout the loading and unloading steps with a final load vs deflection graph plot provided for performance evaluation. Suppliers will typically perform this test prior placing parts into production to ensure parts will not dent and B-surface welds will not fail while being loaded. This test is usually performed at an ambient (23°C) temperature, though extreme environmental conditioning prior to testing is possible.
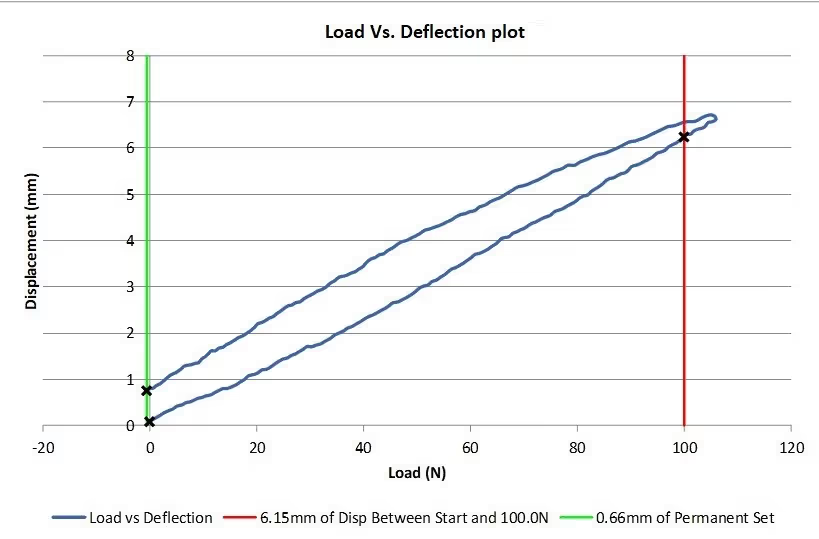
At the core of firm feel testing is the raw material. MGA operates five materials test labs across North America ensuring that the materials used in exterior components meet the required specifications for safety, durability, and performance.
Solar load (sun-load)
Solar loading is an evaluation of a component’s ability to survive exposure to excessive heat and UV rays. Examples of parts that receive this testing include exterior plastic components (fascia/cladding), and door trim components. When a UUT (unit under test) warps, melts, bubbles, or shrinks; this usually means that a supplier needs to perform a material change.
A sample temperature profile for solar load is an environmental temperature of 90°C with a surface temperature of 105°C. The surface temperature is achieved using a high-powered lamp that is activated via surface control thermocouple to ensure the surface temperature is maintained throughout the duration of the test. Depending on the specification being followed, this type of test could last for 1 to 7 days depending on the component’s location on the vehicle and the OEM’s requirements.
Solar simulation is also available in the form of “SOSI” testing. Typically done on component or full assembly, this testing determines the effects of a simulated solar spectrum on the sample, and evaluations include cracking, crazing, yellowing, and functionality. Metal Halide bulbs combined with a window filter are used to produce a spectrum very close to that of actual sunlight. Tests typically range from 10-30 days.
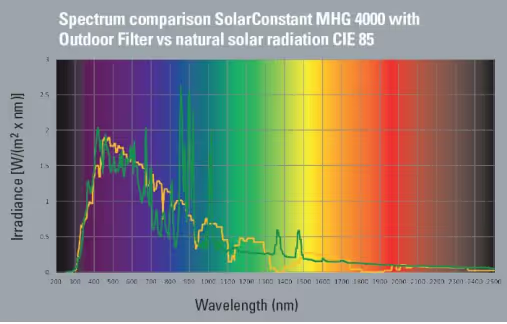
Thermal Shock
Thermal shock environmental testing is performed to identify the effects of exposing vehicle components to opposite extreme temperatures, usually from extreme heat to extreme cold, in a very short time. This could be 90°C to -30°C to 90°C with 5 minutes allowance between each temperature variation. When subjected to radical temperature changes with marginal downtime, the UUT (unit under test) can be evaluated for a wide array of physical characteristics, including deformation, warping, discoloration.
Functionality
This is where brain meets brawn. For a successful product launch, intelligent designs paired with resilience are a must! With new technologies introduced in the closures’ world, electrical components are becoming more and more dominant. Whether it be the deployment of a door handle, or the automatic closure of a trunk lid, wear and tear of such components are considered in the design process. With redundancies, and mechanical bypasses, testing such components for longevity must account for all scenarios. MGA boasts an extensive level of experience with mechanical, electrical, and CAN/LIN systems. Such advantage has allowed us to develop methodologies customized to specific applications, and a seamless automation of human-like motions.
Closures
Doors, trunk lids, liftgates, tailgates, and frunk lids have one thing in common: they get slammed daily. The design and longevity of these components as well as subcomponents is often taken from granted. With months long testing needed to ensure their proper functionality with stringent acceptance criterion, OEM and their suppliers go the extra mile to ensure the end user has a pleasant experience throughout the expected lifetime of these components. Closures testing, which is the industry term used to accelerate the use and abuse of these components at various extreme conditions, has been supported by MGA for quite some time now.
MGA has an array of Lifecycle Controllers that could be used to cycle doors with consistent opening and closing velocities. With the possibility of add-on DAQ and Signal Conditioner, we can record data from Gyroscopes, accelerometers, and displacement transducers available in inventory at a moment’s notice. This allows closing velocity recording in real time for doors, liftgates and frunks, ensuring the closing velocity stays within the required range over the course of the lifecycle test. Tests are automatically paused in the event a velocity falls below a programmed tolerance. Dedicated technicians are then able to troubleshoot any issues and correct them before resuming the test. With a dependable and highly repeatable system, we can ensure that every cycle will be executed per customer’s specifications.
Our root cause analysis procedures include hourly inspections, velocity checks, and documentation of findings by our dedicated closures team. Additional solutions such as the use of accelerometers to record data from localized stress/failure areas are also available for further root cause analysis.
Window durability
Similar to doors and lids, windows are considered to be yet another critical component in vehicles that are expected to be durable and detect any obstructions that could cause damage. Through the process of window durability testing, each component of the window is tested and monitored for any temporary and permanent degradation. Done at extreme temperature variations (high heat, high humidity, and extreme cold), the window is cycled at different positions via a signal sent to the motor, or a physical push/pull on the window switch. Furthermore, testing for obstruction detection and window responses to obstruction is also conducted. These tests are often done with live monitoring for current and voltage in the wiring, as well as resistance of any cabling utilized to send a signal in.
Our experienced staff paired with state-of-the-art controllers allow for seamless and repeatable processes while minimizing the needs for additional peripheral data collection tools. Tests can be automatically stopped if any failure mode (mechanical or electrical), or when the desired number of cycles has been reached. We also have an extensive working knowledge of CAN/LIN systems, including not just the physical set up and testing of the system but also writing custom programs to inject required commands into the system for desired motions.
Adding sound measurement capabilities for pre, mid, and post tests performance evaluations, and 3D printing capabilities for rapid manufacturing of obstruction forms, our expansive capabilities give MGA the advantage of being a single source of services for all durability testing needed.
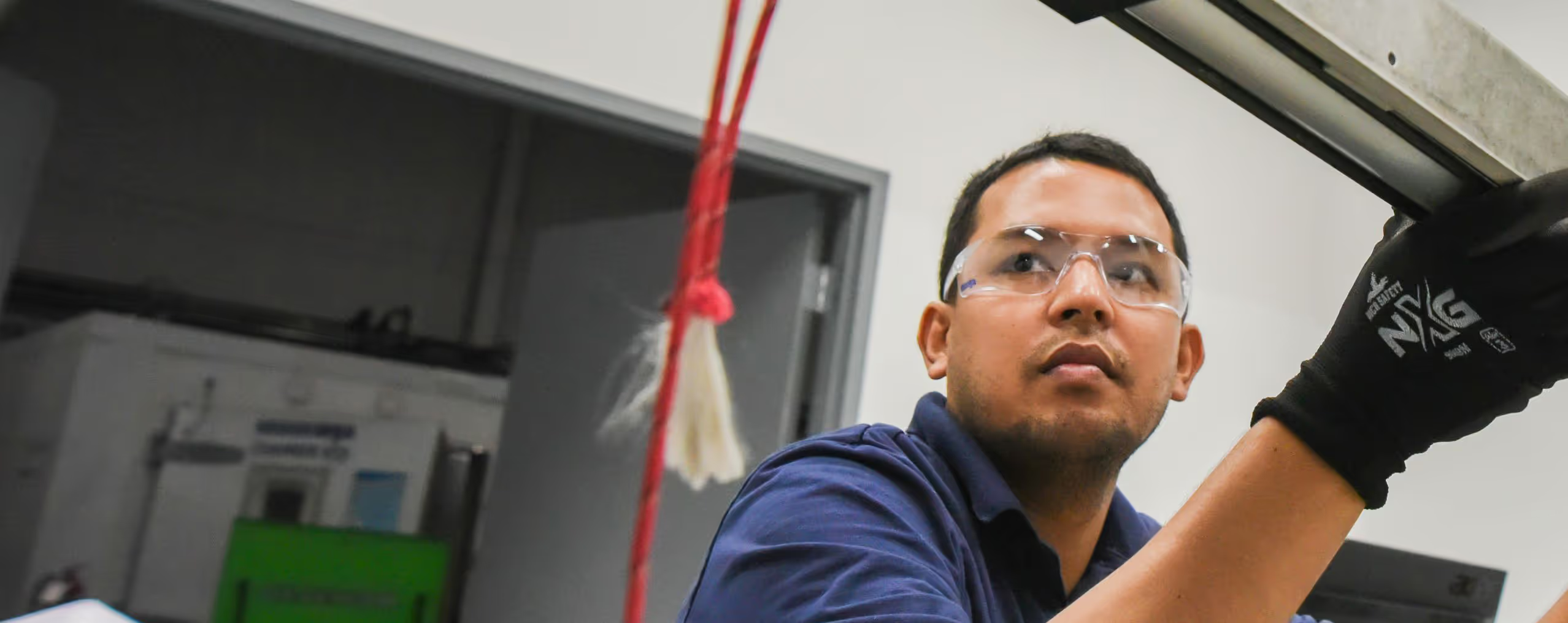
Ready to Get Started?
Let's discuss your testing needs and how MGA can help. Our team is ready to provide the expertise and solutions you're looking for.