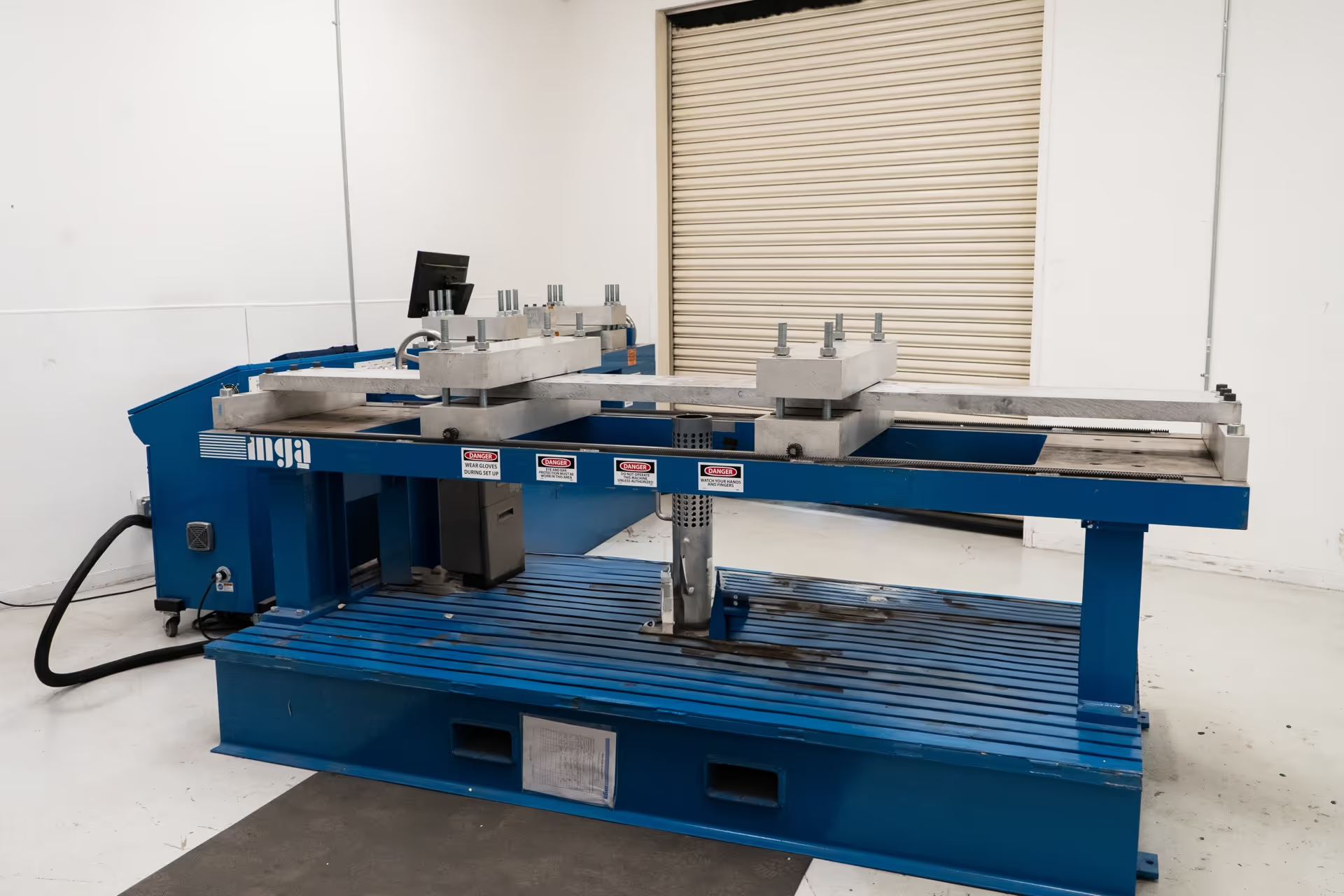
Space & Defense Testing
MGA offers comprehensive testing services for the space and defense industries, leveraging proprietary equipment and extensive expertise to simulate extreme conditions like pyroshock, vibration, thermal stress, and mine blasts, ensuring component reliability and occupant safety across various applications.
Quick Overview
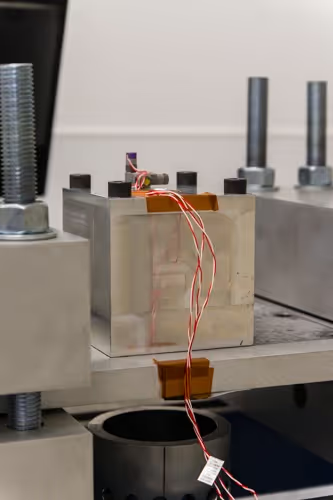
Comprehensive Space and Defense Testing
We offer extensive testing services for space and defense industries, simulating extreme conditions to ensure component reliability and occupant safety.
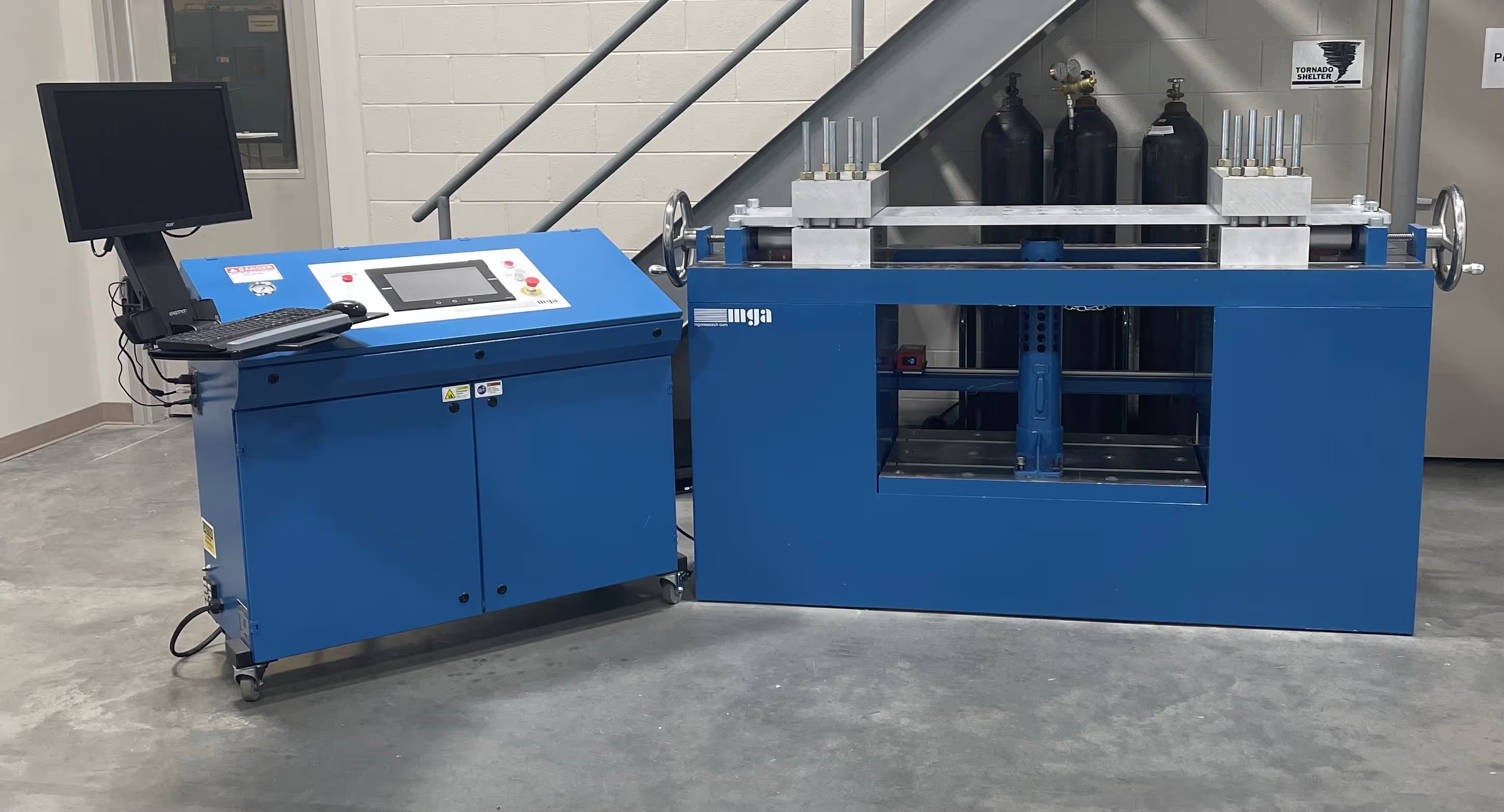
Advanced Pyroshock Simulation
We provide industry-leading pyroshock testing using our proprietary equipment, offering a safe and efficient alternative to explosive events.
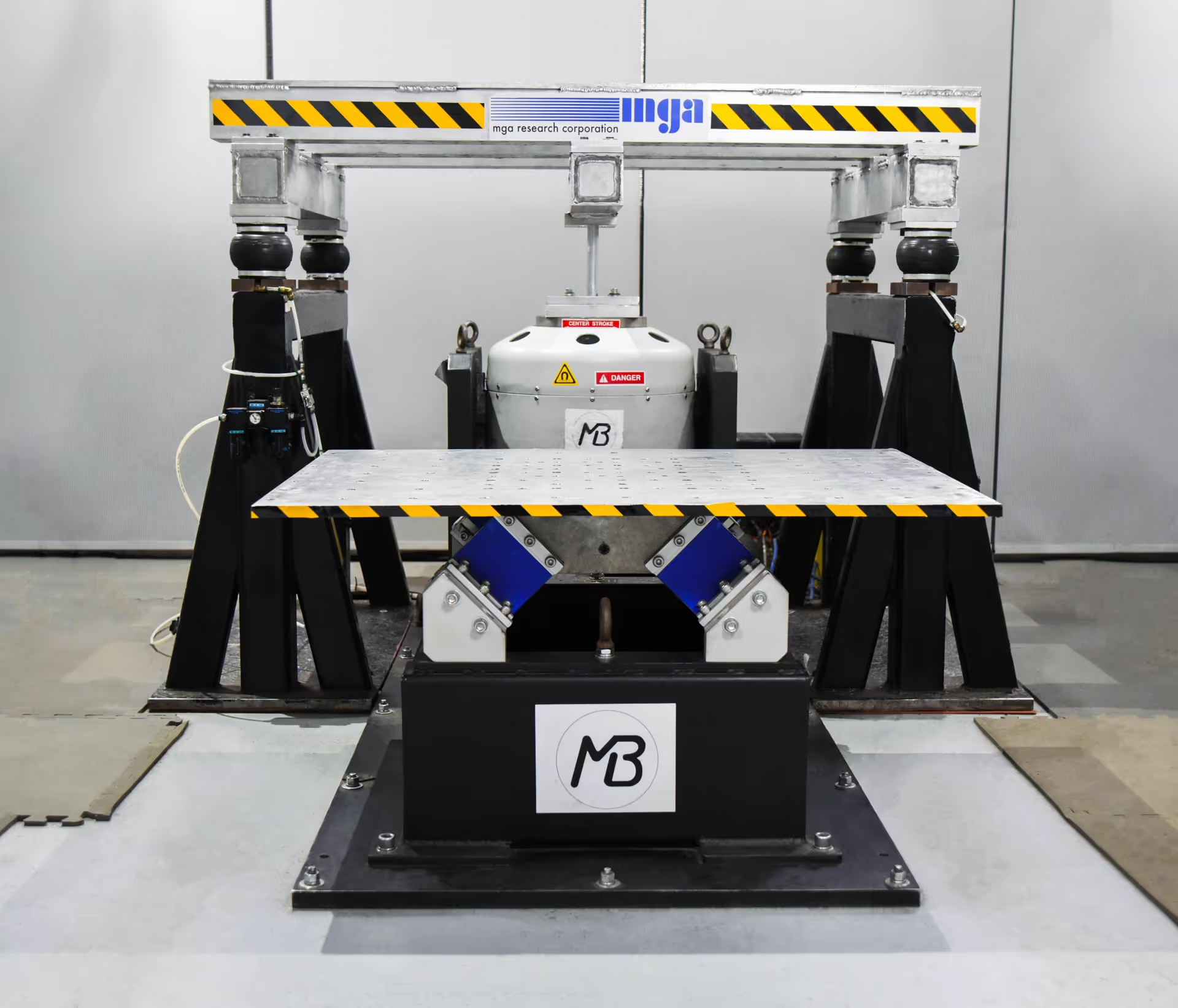
Extensive Vibration and Thermal Testing
We utilize over 40 electrodynamic shakers and 100+ environmental chambers to conduct a wide range of vibration and thermal stress tests.
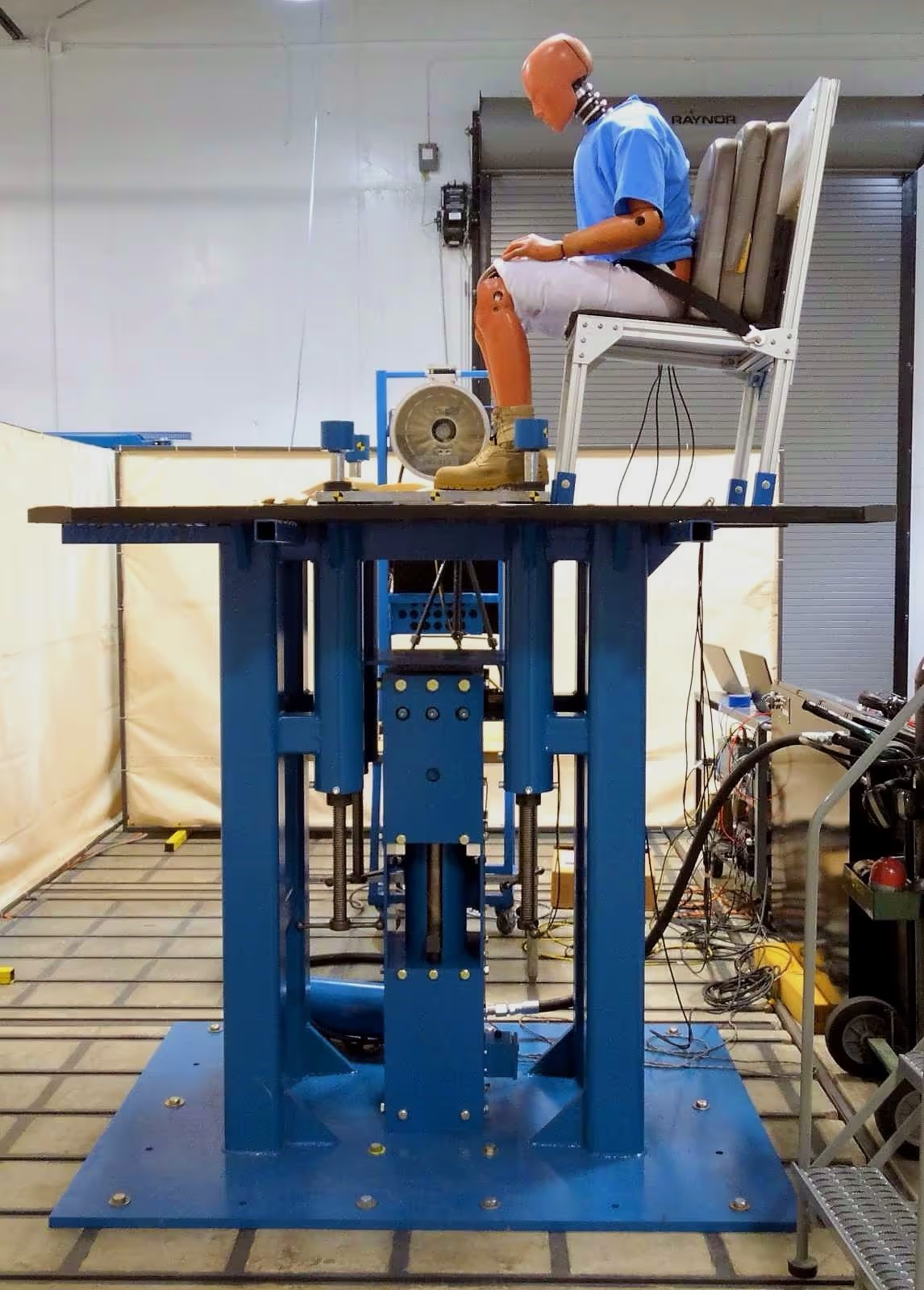
Specialized Mine Blast Simulation
We offer unique mine blast simulation capabilities, including sled tests, drop towers, and leg impactors, to evaluate occupant protection in military vehicles.
.avif)
Accredited Testing Expertise
We are ISO 17025:2017 accredited for key military testing procedures, including LAV protection evaluation and MIL-STD-810 standards.
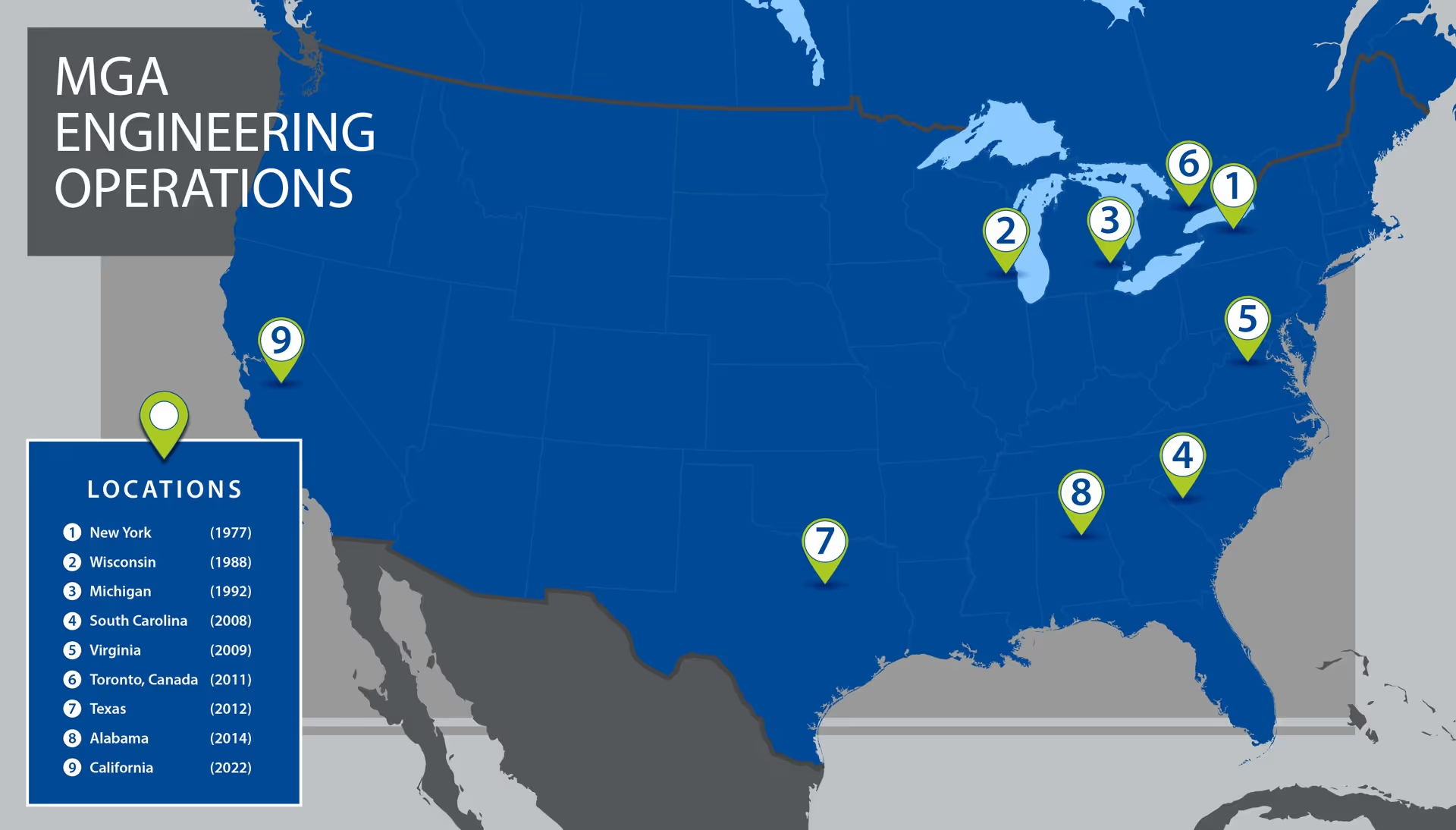
Multi-Location Testing Network
We provide testing services across multiple U.S. locations, offering proximity and flexibility to key space and defense industry sectors.
MGA has been working with the space and defense industry since the early 2000’s. MGA’s role focuses on providing customers data that can be used to qualify and improve component design and performance. Our position is to provide the highest quality services, expertise, and equipment to help our customers achieve their goals.
Due to the explosive events and high vibrations that are present during the launch and stage separation of space vehicles and other defense applications, we’ve created a solution to simulate these events without using explosives so our customers can ensure their components will survive. We have leveraged our experience manufacturing test equipment for the automotive and aircraft industries to develop and sell a turnkey pyroshock system that we also use to provide testing services. We have developed, and are continuing to develop, new test systems and methods to better serve the industries that require this testing.
The vibration levels that are present during a launch or in flight can adversely affect the intricate systems designed for space vehicles. Whether the components are large or small, we have many electrodynamic shakers in our facilities to accommodate this testing. MGA also has a large amount of thermal chambers of varying sizes to service multiple industry’s space and defense needs.
Another need in the defense industry that MGA caters to is mine blast simulation. The goal of our mine blast simulations is to promote occupant survivability. This follows MGA’s commitment to providing quality passenger safety testing services in all its industries. Like our turnkey pyroshock equipment, MGA designs, manufactures, and sells drop towers, sled systems, and leg impactors.
MGA Advantage:
- ISO 17025:2017 Accredited for 1) Procedures for Evaluating Protection Level of LAV – Department of Army, Occupant Crash Protection Handbook for Tactical Ground Vehicles, and 2) MIL-STD-810
- MGA has designed, developed, and manufactured our own industry leading test equipment specifically tailored for our space and defense customers, used by NASA and other industry leaders.
- Physical presence across the US to support key space and defense industry sectors, allowing quick test response and scheduling flexibility
Pyroshock / Shock testing
Pyroshock Table
- A safe and timely alternative to performing an explosive event
- Recordable variables are utilized for quick tuning and repeatability
- Tuning can be performed in hours as opposed to days/weeks
- Two different systems designed to accommodate items of varying mass, upwards of 500+ pounds (profile dependent)
- Tuning from 100 - 10,000 Hz
- Capability up to 100,000 G in higher frequencies
- Sample rate up to 200,000 Hz on up to 32 channels
- Unique profiles can be achieved through the pulse tuning process utilizing mass models to best simulate test conditions
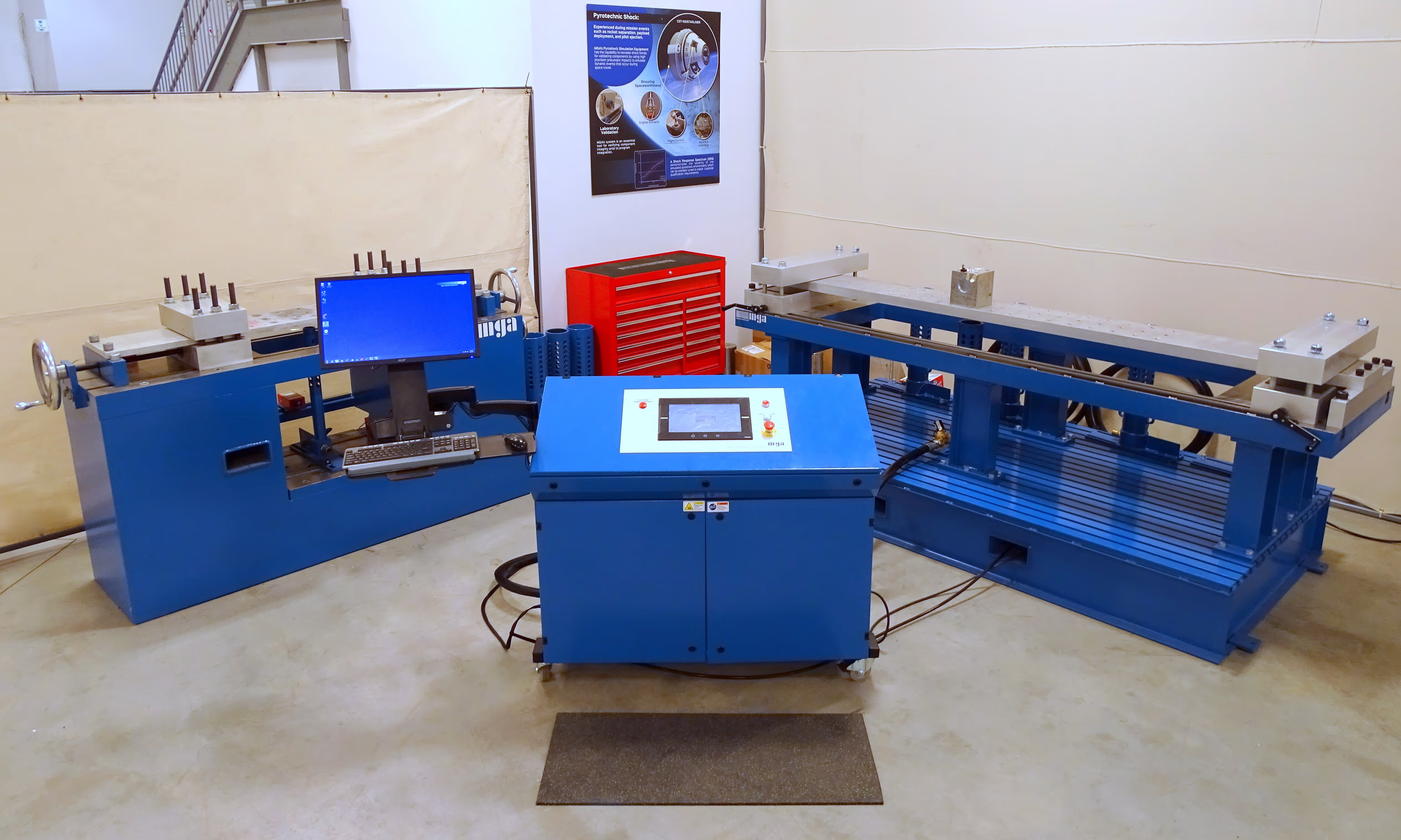
Electrodynamic Shaker
- Some shock profiles can be performed using MGA’s electrodynamic shakers
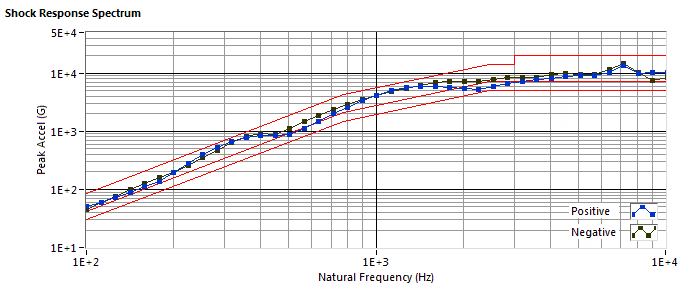

Vibration
Electrodynamic Shakers
- 40+ ED shakers throughout MGA’s network of labs
- Random Vibration
- Sine Sweeps
- Sine-on-Random
- Shock
Thermal
Thermal Chambers
- 100+ environmental chambers throughout MGA
3 Chamber Sizes:
- Reach-in: ~4’x4’x4’
- Walk-in: ~10’x10’x10’
- Drive-in: ~30’x15’10’
Mine Blast Simulation
Our testing services can be broken into two categories
Global Events
- Sled
- Drop Tower
Localized Events
- Leg Impactor
Sled
Because of the profile, duration, and maximum input of sled pulses, it is commonly used for less severe event simulations.
- Helicopter seating
- Smaller naval vessels
- APC’s (armored personnel carries)
- Depending upon the end use environment, military vehicles and their components may be subject to many of the same FMVSS standards we are accustomed to testing to
Drop Tower
- 18’ Drop Height
- 3’ x 4’ universal carriage mounting platforms: Carriage design effectively translates impact forces throughout
- Capable of ΔV of 11m/s
- Easily and quickly tunable to achieve multiple velocities and pulse durations
- Can accommodate a variety of vehicle seating systems and mounting styles - Floor, wall, or ceiling suspended seats
There are generally two pulses each seat system is subjected to
Global
- Higher impulse and shorter duration to simulate initial vehicle liftoff
- Slamdowns
- Lower impulse with a longer duration simulating the vehicle chassis returning to earth
- No longer forcefully being accelerated via ordinance
- Vehicle hull, tires, suspension system will mitigate and extend event duration
- ATD injury response is collected with data from head, chest, and pelvis accelerometers as well as upper & lower tibia, lumbar, and neck load cells
Leg Impactor
- The impact system utilizes MGA’s mobile propulsion unit that is propelled via nitrogen with pressures up to 1800psi
- Capable of 28 m/s
- Impactor mass of 70lbs
- Stroke distance and impact velocities are adjustable to replicate various blast environments
- The leg impact frame is specifically for testing floor dampening systems and components
- Additional attachment area immediately surrounding the impact zone allows for sections of vehicle hull to be fastened to the frame and impacted
- This method further simulates proper vehicle hull and EA material interactions and response data collected by the ATD
- Military After Action Reports (AAR) showed that soldiers who were involved in under-body blast (UBB) events would immediately exit the vehicle to fight and were collapsing due to extreme lower leg injuries/ missing limbs.
- Injury Response
- Blast simulation response data is collected with a sample rate of 50,000hz
- High speed videos are collected in 2000 fps
- Response data is collected from femur load cells, 5 axis upper & lower tibia load cells, and tibia accelerometers
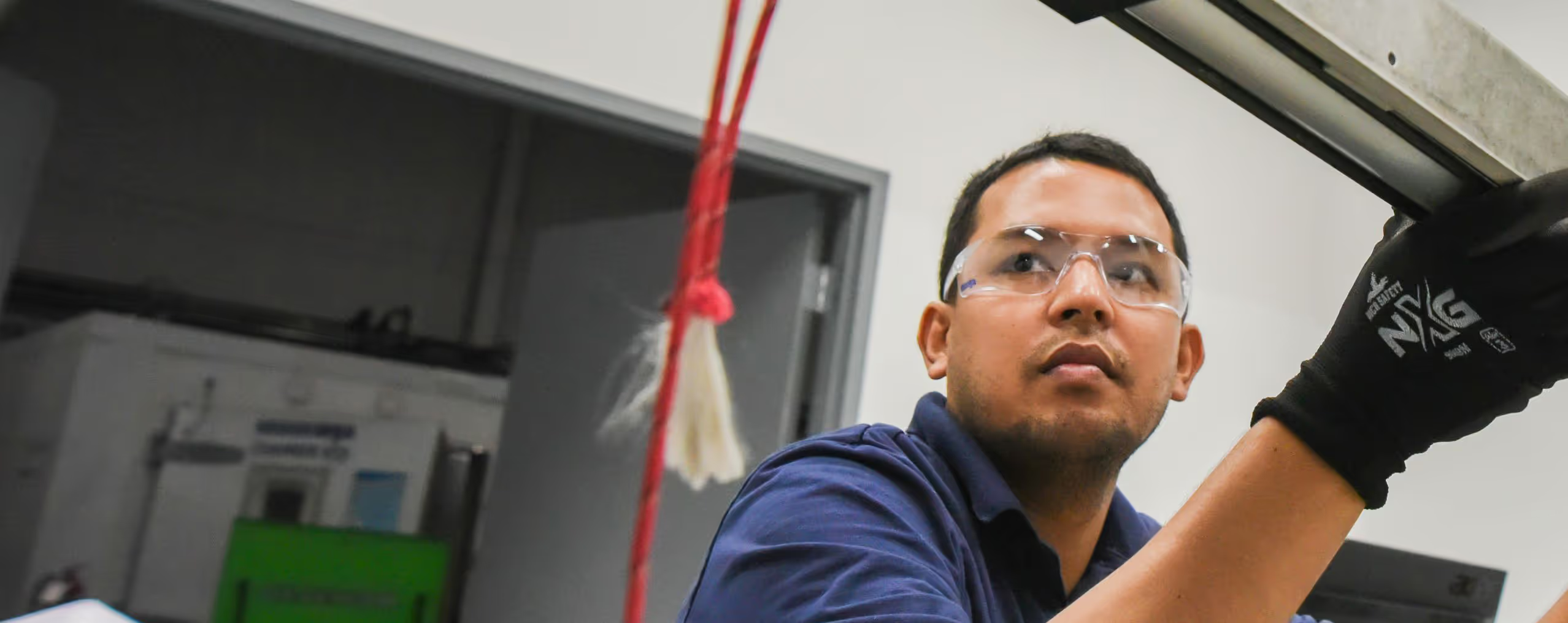
Ready to Get Started?
Let's discuss your testing needs and how MGA can help. Our team is ready to provide the expertise and solutions you're looking for.