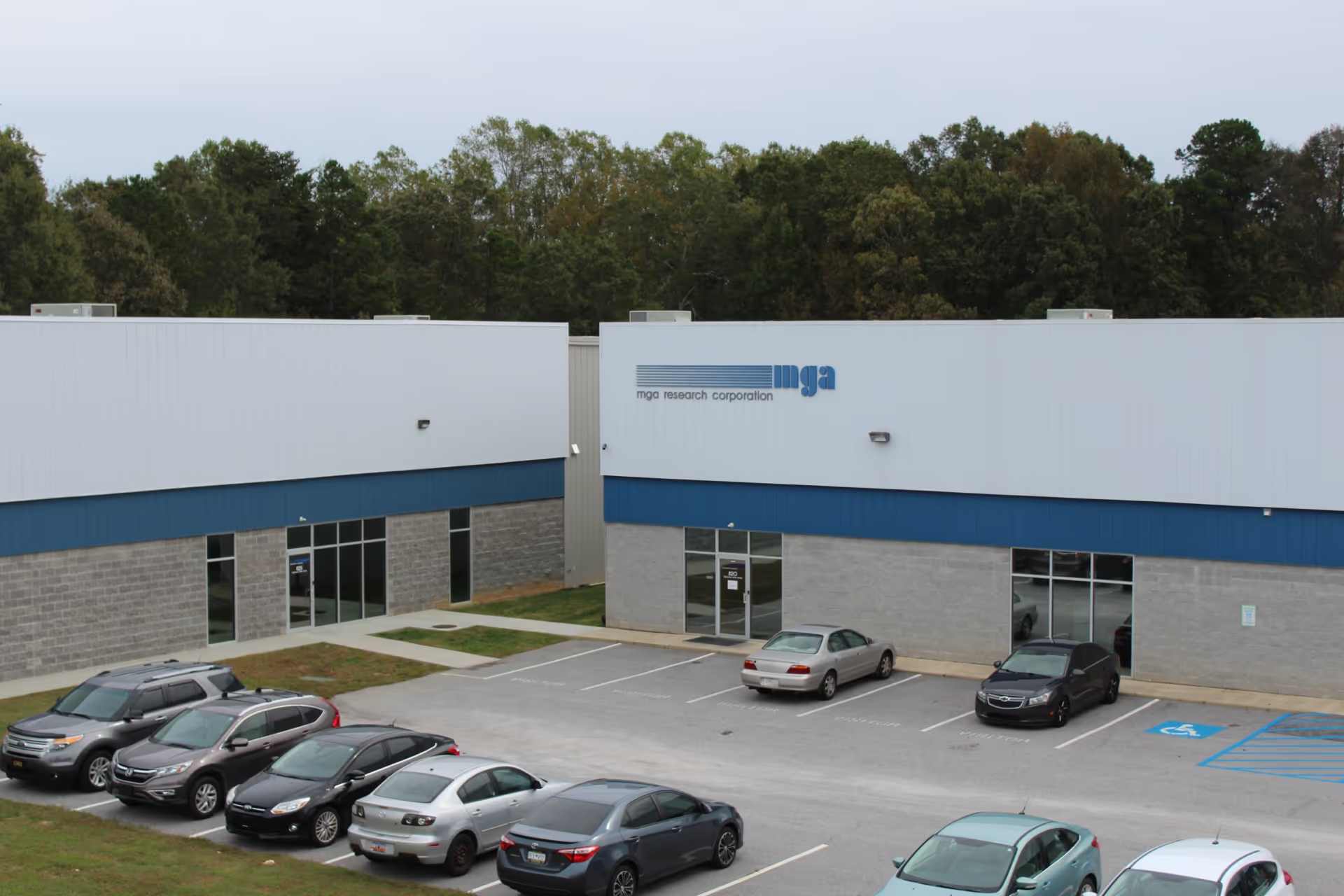
Materials Testing
MGA Research Corporation provides comprehensive material testing services for the automotive industry, evaluating both physical and aesthetic properties of interior and exterior materials to ensure quality, durability, and compliance with industry standards.
Quick Overview
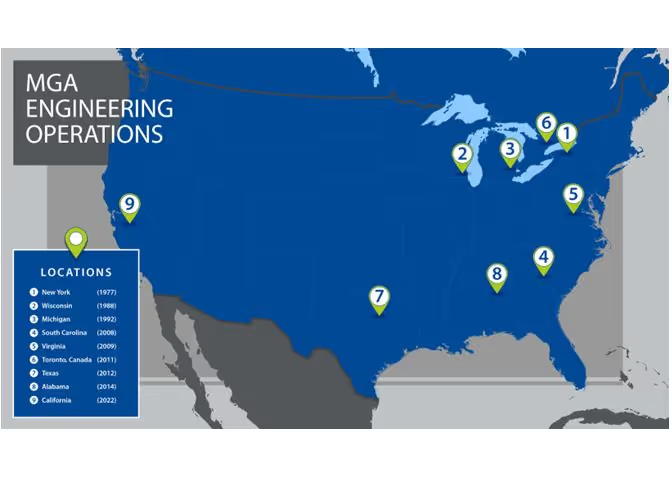
Multi-Facility Network
Our ISO 17025 accredited laboratories are located throughout North America offering localization opportunities and rapid response times
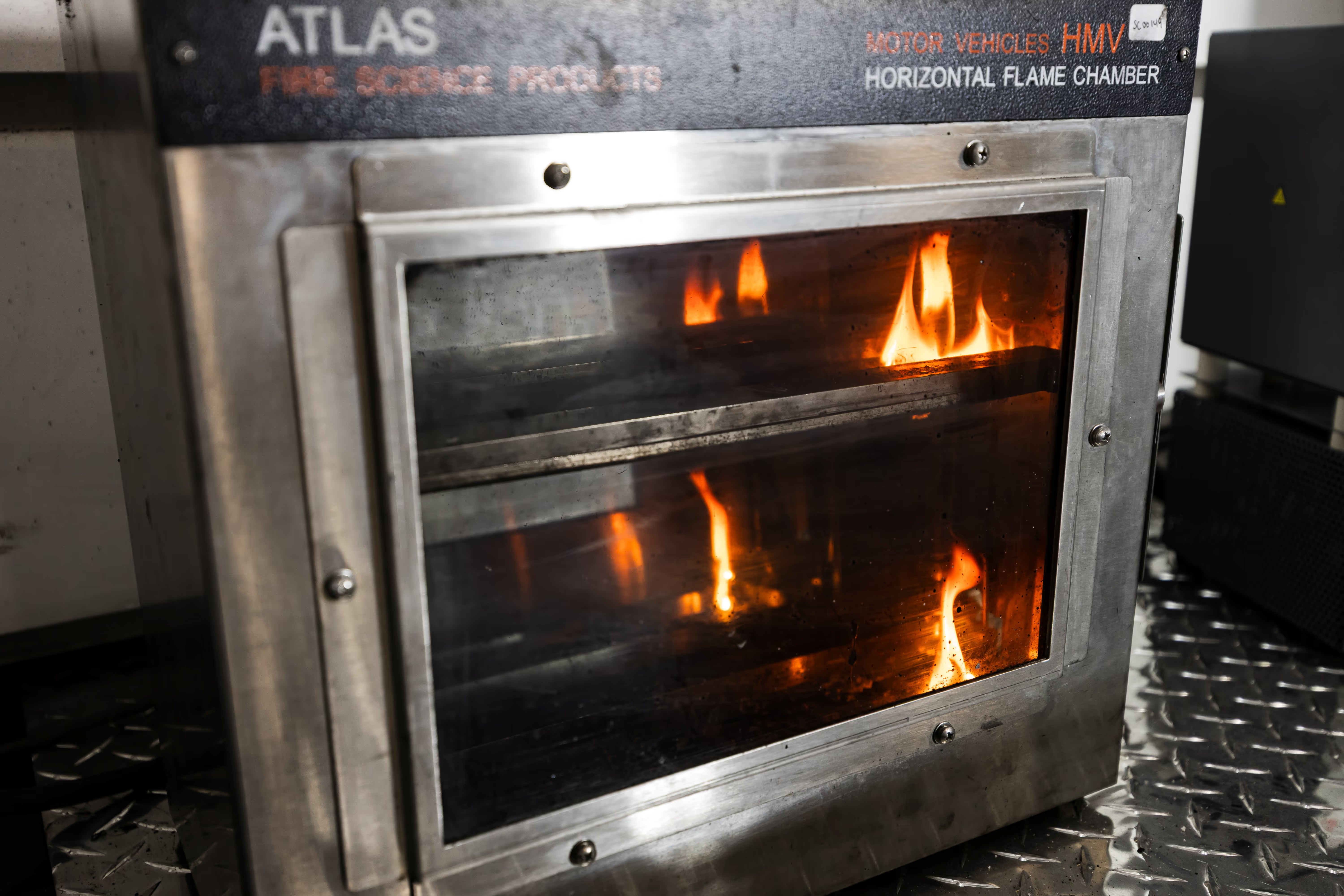
Flammability
Determine a material’s resistance to burning to FMVSS 302 and OEM standards
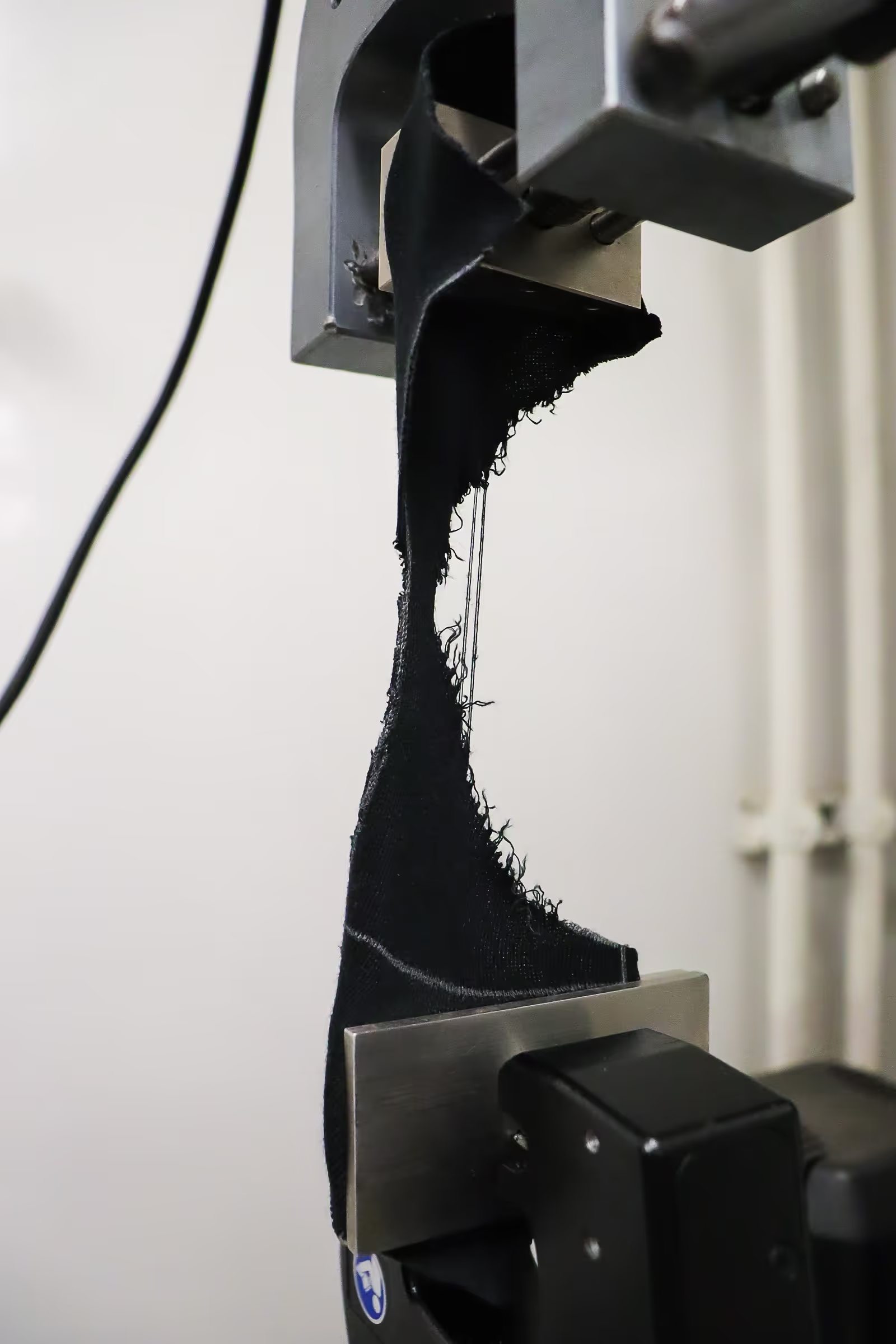
UTM / Physical Property Testing
Determine a variety of properties relating to tensile, adhesive, flexural, and compressive strength
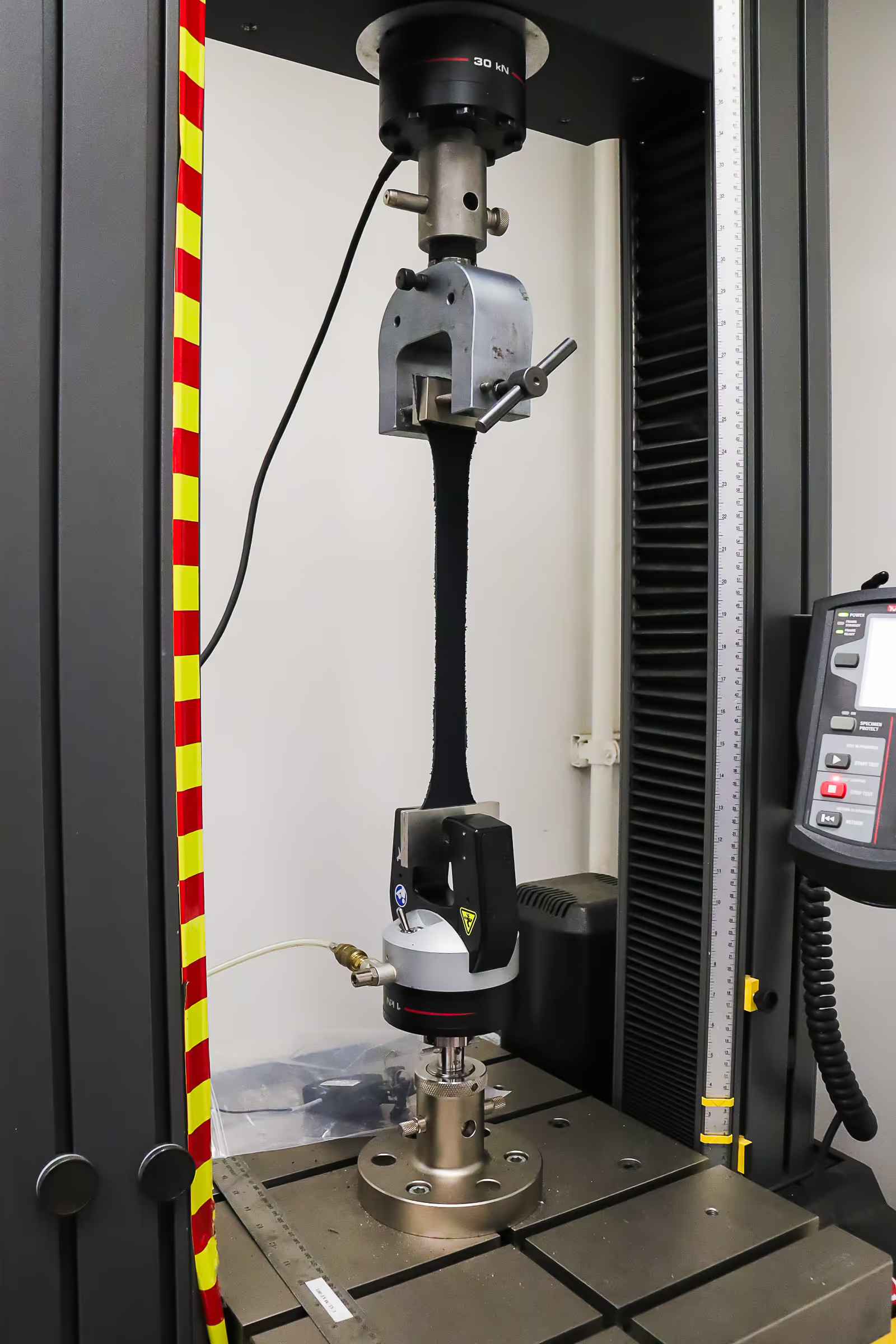
Material Property
Determine properties specific to a material through tests such as FTIR, melt flow, and density
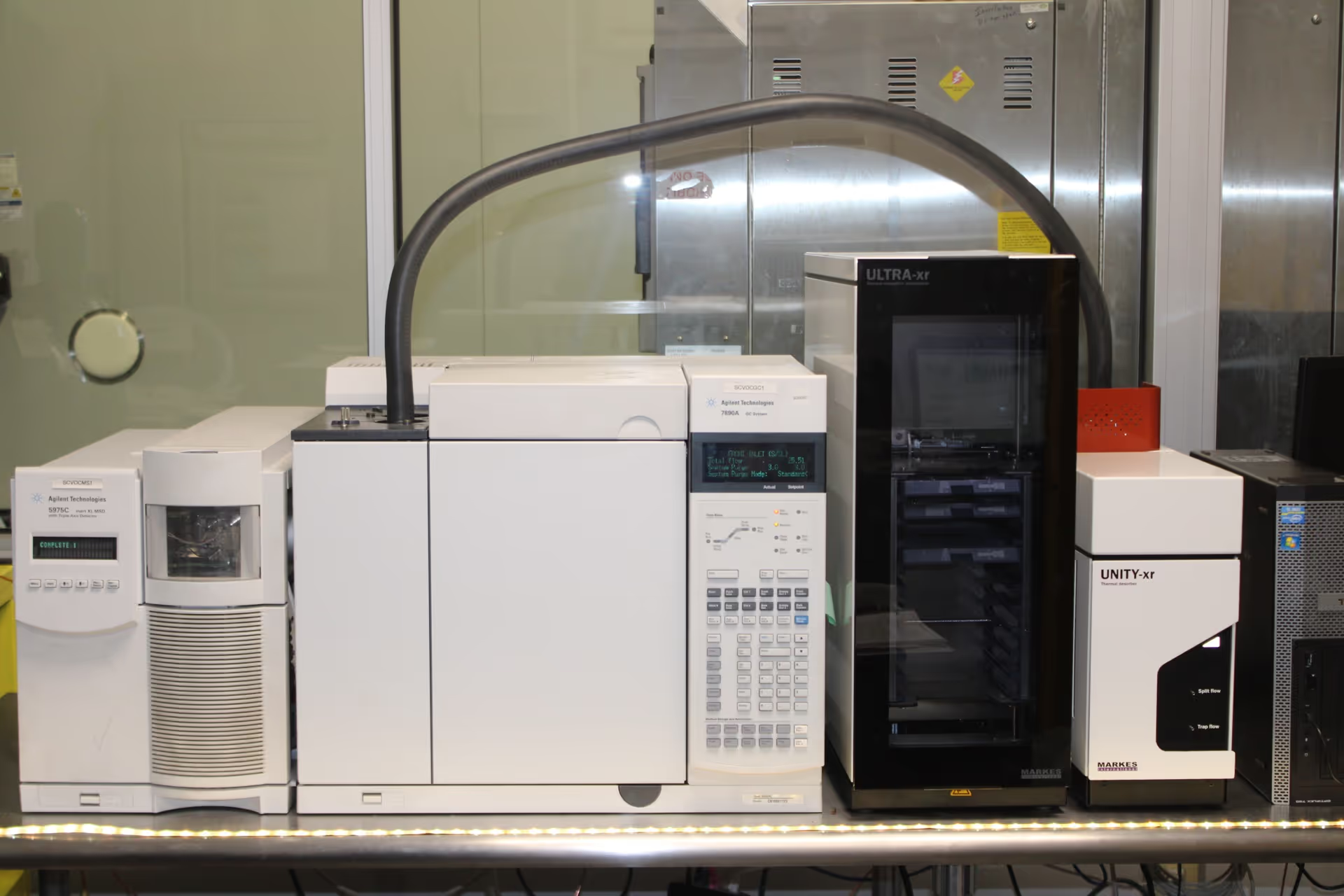
Emissions - VOC/Fogging/Odor
Quantitatively and subjectively determine off gassed chemicals from materials
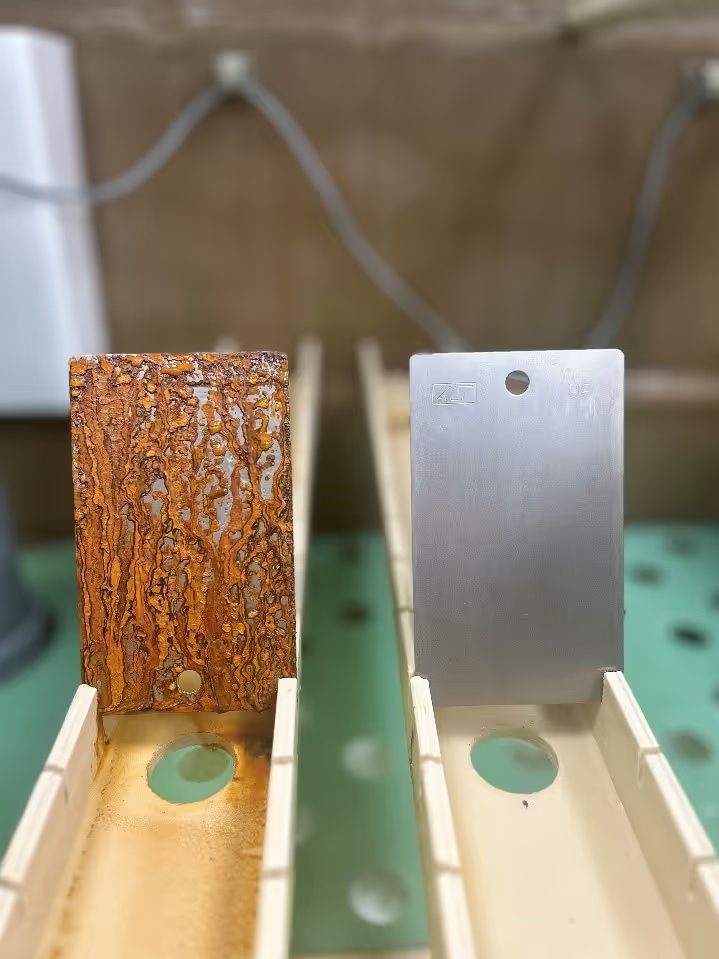
Corrosion
Evaluate components’ rust resistance when exposed to salt solution
.avif)
Solar Simulation
Evaluate a material's reaction to artificial solar exposure using either xenon or carbon arc irradiation
.avif)
Aesthetic Property
Determine the effect of simulated wear, abrasion, scratch, and mar on a material
A core part of the services provided by MGA involve the testing of interior and exterior automotive materials to determine both their physical and aesthetic properties. MGA has had a devoted materials team since 2004 and our testing capabilities are constantly growing. The requirements for automotive materials can be simply broken down into two categories: physical and aesthetic.
The physical properties are those that describe the integrity of the material itself. This testing is required from the raw material supplier, but as this raw material is processed, the chance that these properties might change means that the testing responsibility additionally falls on component suppliers. The other side of materials testing involves the aesthetic properties, for example: how much will the leather from an armrest fade while exposed to abrasion, solar exposure, controlled humidity, etc. These tests are meant to mimic real world exposures and motions, and the tests will often differ based on the region/OEM.
MGA Advantage
Boasting five laboratories and expertise across a multitude of unique specifications, MGA offers significant benefits to its clients.
- Comprehensive testing capabilities with a wide range of testing services across multiple material specifications
- State-of-the-art facilities featuring advanced laboratories equipped with cutting-edge technology
- Expertise and Experience backed by years of industry experience knowledge
- Customized testing solutions offering flexible testing programs to meet specific project requirements
- Accredited and certified labs maintain various industry accreditations and certifications ensuring accuracy and quality of testing
- Fast turnaround times with efficient processes and multiple labs helping customers meet tight deadlines.
- Proven Track Record for delivering reliable and consistent testing results, making it a trusted partner for materials testing needs.
Physical Property Testing
.avif)
MGA offers testing capabilities up to 150kN for physical testing (non-hydraulic). Specimen preparation is often done at MGA using the provided raw material or component. Testing can be performed at ambient or after environmental exposures between -40°C and 300°C, as well as up to 100% relative humidity. Some of the most common physical tests are listed below.
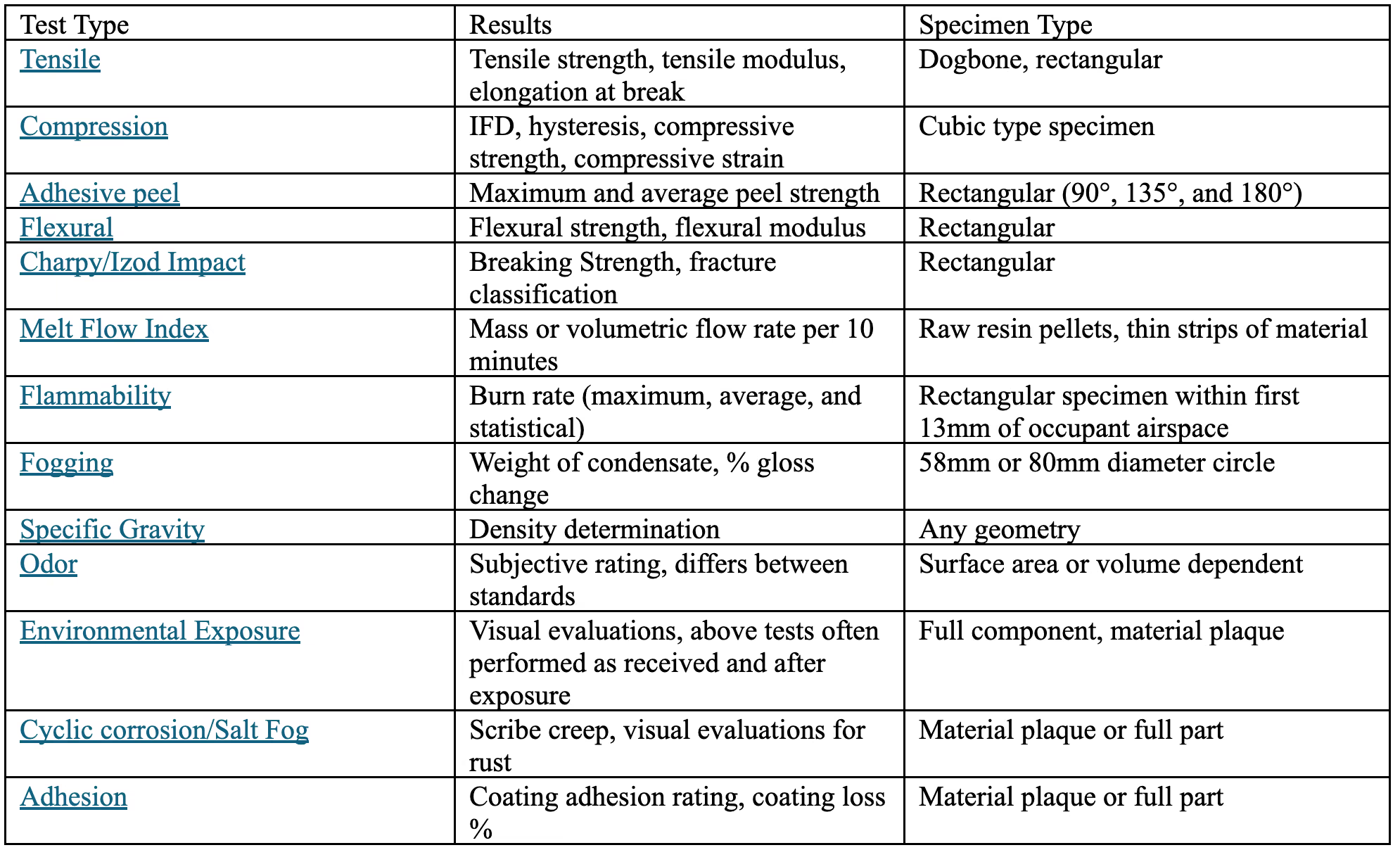
Aesthetic Property Testing
MGA offers a wide range of solutions to test how well a material will hold up visually to specified conditions. Testing is typically performed on the component level as factors such as graining will likely affect the outcome of the test.
Abrasion and Wear Resistance
Abrasion and wear resistance testing are essential methods in automotive materials testing that assess a material's ability to resist surface damage, such as scratching, scuffing, and erosion, caused by mechanical friction or contact. These tests are crucial for materials used in various vehicle components, including interior surfaces (like seats, dashboards, and carpets), exterior parts (like body panels and coatings), and mechanical elements (such as gears, bearings, and tires). By simulating real-world conditions, such as repeated rubbing, scraping, or mechanical load cycling, abrasion and wear resistance tests, like the Taber Abrasion and Pin-on-Disk tests, provide valuable data on how materials will perform over time.
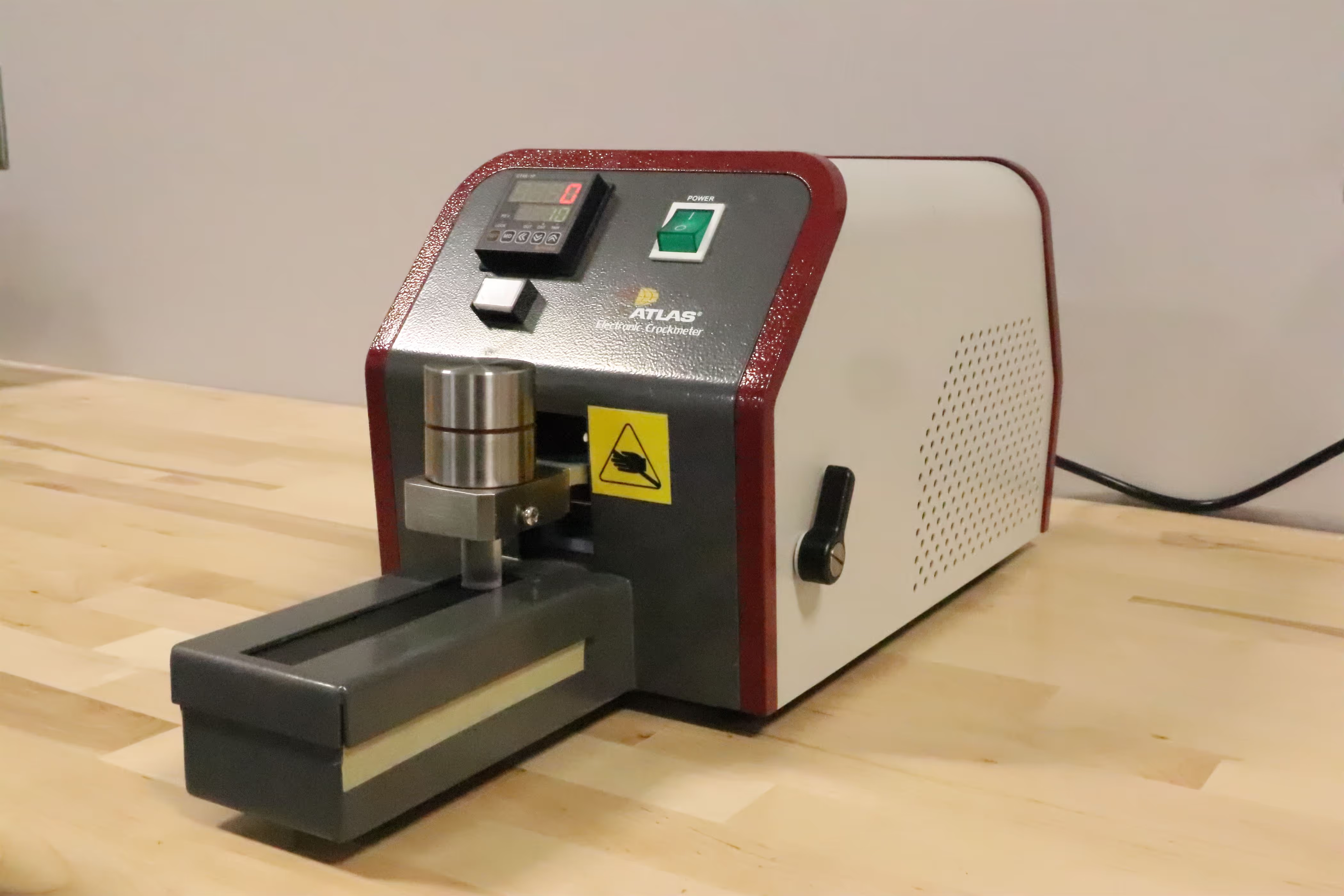
MGA offers multiple types of abrasion resistance and can produce custom setups if desired. The most common variables for these tests are number of cycles, load applied to sample, presence of water/chemicals, and test speed. Evaluations are typically visual ratings, but other specific evaluations such as mass loss of sample can be performed.
- Linear abrasion
- Rotary abrasion
- Wyzenbeek abrasion
- Washability
- Crocking
- Martindale
- Bally flex
- Pinch Fold
- Cold Cracking
Scratch and Mar Resistance
Similar to abrasion testing, scratch and mar resistance testing evaluates a material's ability to resist damage from scratches and surface marring, which can affect the aesthetic appearance and durability of vehicle components. This type of testing is particularly important for materials used in high-visibility and frequently touched areas, such as dashboards, door panels, paint finishes, and trim pieces. Scratch resistance tests, such as pencil hardness tests and nano-scratch tests, simulate the effects of sharp or abrasive objects, while mar resistance tests assess how materials withstand softer, more superficial damage that can result from contact with everyday items like keys, fingernails, or cleaning tools.
- Grid scratch/mar resistance
- Five finger scratch/mar resistance
- Scratch/mar pen
- Counter-arm scratch resistance for paints and coatings
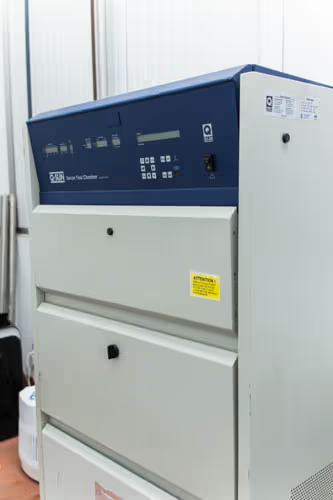
Solar Simulation
MGA offers multiple variations of simulated solar exposure, mainly xenon arc exposure and carbon arc exposure. The conditions often reflect an equivalent time of natural sun exposure, but at an accelerated rate. Irradiation spectra is controlled using various optical filters to simulate the natural spectra of sunlight while also controlling environmental conditions such as temperature, humidity, and rain simulation. Changes in color, gloss, and some mechanical properties of the material are evaluated after exposure.
Color and gloss evaluations – Measurements to determine color shift (a, b, c, L, E, etc) and gloss are often used to determine if a sample has shown significant color difference or an increase/decrease in glossiness. These objective methods take out human error and are typically performed before and after solar exposure or environmental exposure.
Tensile and Compression Testing
Tensile testing is a critical process in evaluating the mechanical properties of automotive materials, such as metals, alloys, composites, and plastics. It involves applying a controlled tensile (pulling) or compression force to a specimen until it fractures/deforms, measuring properties like tensile strength, compressive strength, yield strength, elongation, and Young's modulus. In the automotive industry, these evaluations help ensure materials can withstand the stresses and strains encountered during vehicle operation, such as those from collisions, acceleration, and braking. This testing is essential for material selection and quality control, ensuring components are strong, durable, and lightweight to enhance vehicle safety and performance. MGA also offers extensive capabilities for foam testing such as indentation force deflection and hysteresis loss per ASTM D3754.
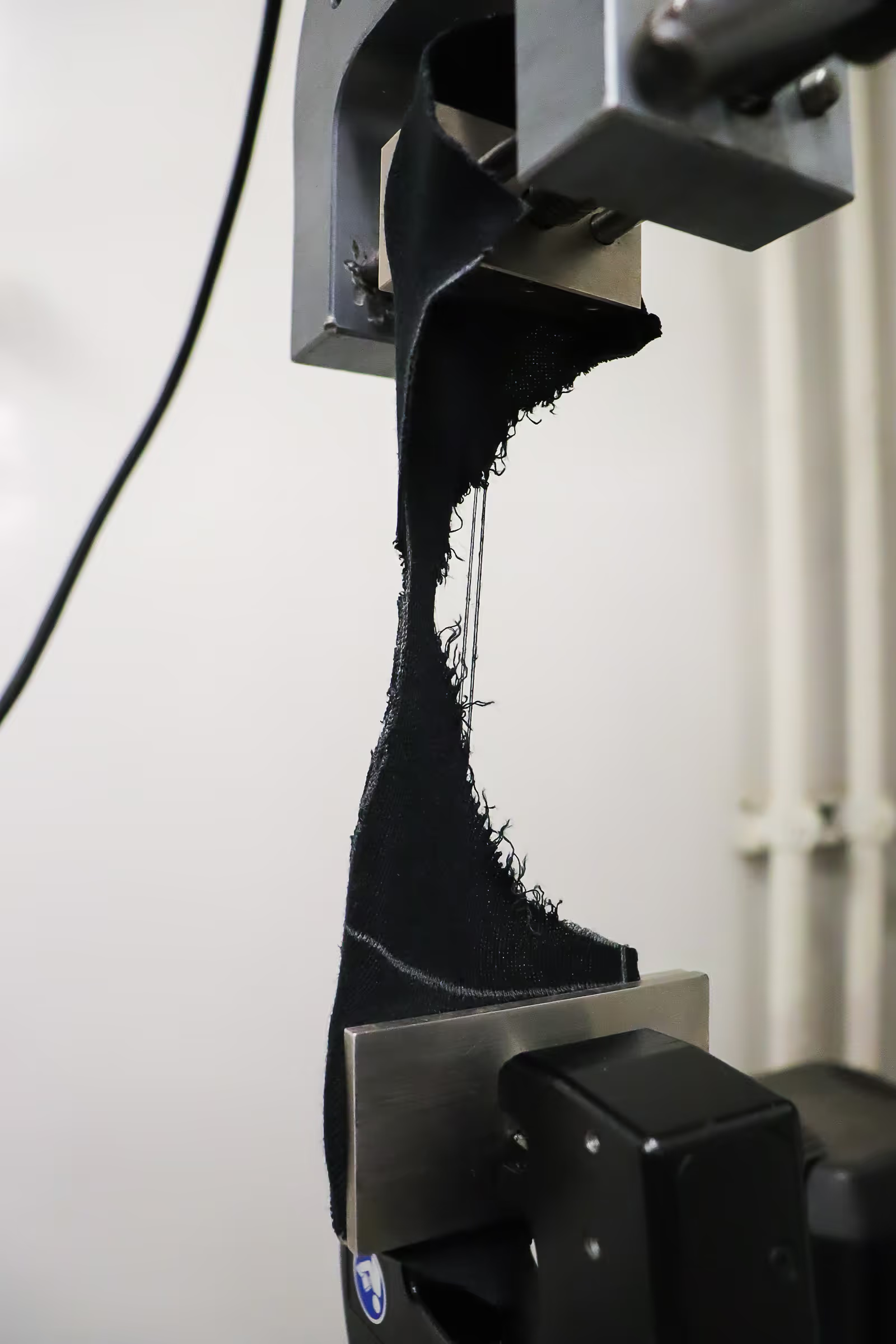
Adhesive Strength and Adhesion Testing
Adhesive strength testing is essential for evaluating the bonding performance of adhesives used in automotive materials, which are increasingly employed to join various components made from metals, plastics, and composites. This testing measures the force required to separate bonded surfaces, providing data on properties like peel strength, shear strength, and tensile strength of the adhesive joints. In the automotive industry, the results help engineers optimize adhesive formulations and application methods, ensuring safe, durable, and high-performance assemblies leading to strong and reliable adhesive bonds that are crucial for maintaining structural integrity, reducing vehicle weight, and improving crash energy management.
Similarly, adhesion testing evaluates the strength and durability of bonds between coatings, paints, adhesives, and their respective substrates, such as metals, plastics, and composites. This testing determines the ability of a coating or adhesive layer to remain attached to the underlying material under various conditions, including mechanical stress, thermal cycling, moisture, and environmental exposure.
Flexural Testing
Flexural testing, or bend testing, is a vital method for assessing the flexural strength and stiffness of automotive materials, including metals, composites, and plastics. This test involves applying a load to the center of a material specimen supported at both ends until it bends or breaks, measuring the material's resistance to deformation under bending stress.
Charpy/Izod Impact
Charpy and Izod impact testing are critical methods for assessing the impact resistance and toughness of automotive materials, such as metals, plastics, and composites. These tests involve striking a notched specimen with a pendulum hammer and measuring the energy absorbed by the material during fracture. The Charpy test places the specimen horizontally, while the Izod test positions it vertically, with the notch facing the striking direction. Testing can be performed using both notched and unnotched variations.
Melt Flow Index (MFI)
Melt Flow Index (MFI) testing is a crucial method for evaluating the flow characteristics of thermoplastic polymers used in automotive materials. This test measures the rate at which a molten polymer flows through a specified die under a defined load and temperature, providing an indication of the material's viscosity and processability. In the automotive industry, MFI testing is essential for ensuring that thermoplastic materials, such as those used in interior trims, dashboards, and under-the-hood components, can be easily molded and extruded into complex shapes with consistent quality. The results help engineers and manufacturers select the right polymer grades for specific application
Flammability
Flammability testing is a critical process in evaluating the fire resistance and safety of automotive materials, such as fabrics, plastics, foams, and composites used in vehicle interiors and components. This testing assesses how materials react to exposure to flames or heat, including ignition resistance, burn rate, flame spread, and smoke generation. In the automotive industry, flammability testing is essential to ensure that materials meet safety standards and regulations, including FMVSS 302, minimizing the risk of fire hazards in the event of accidents, electrical faults, or other ignition sources.
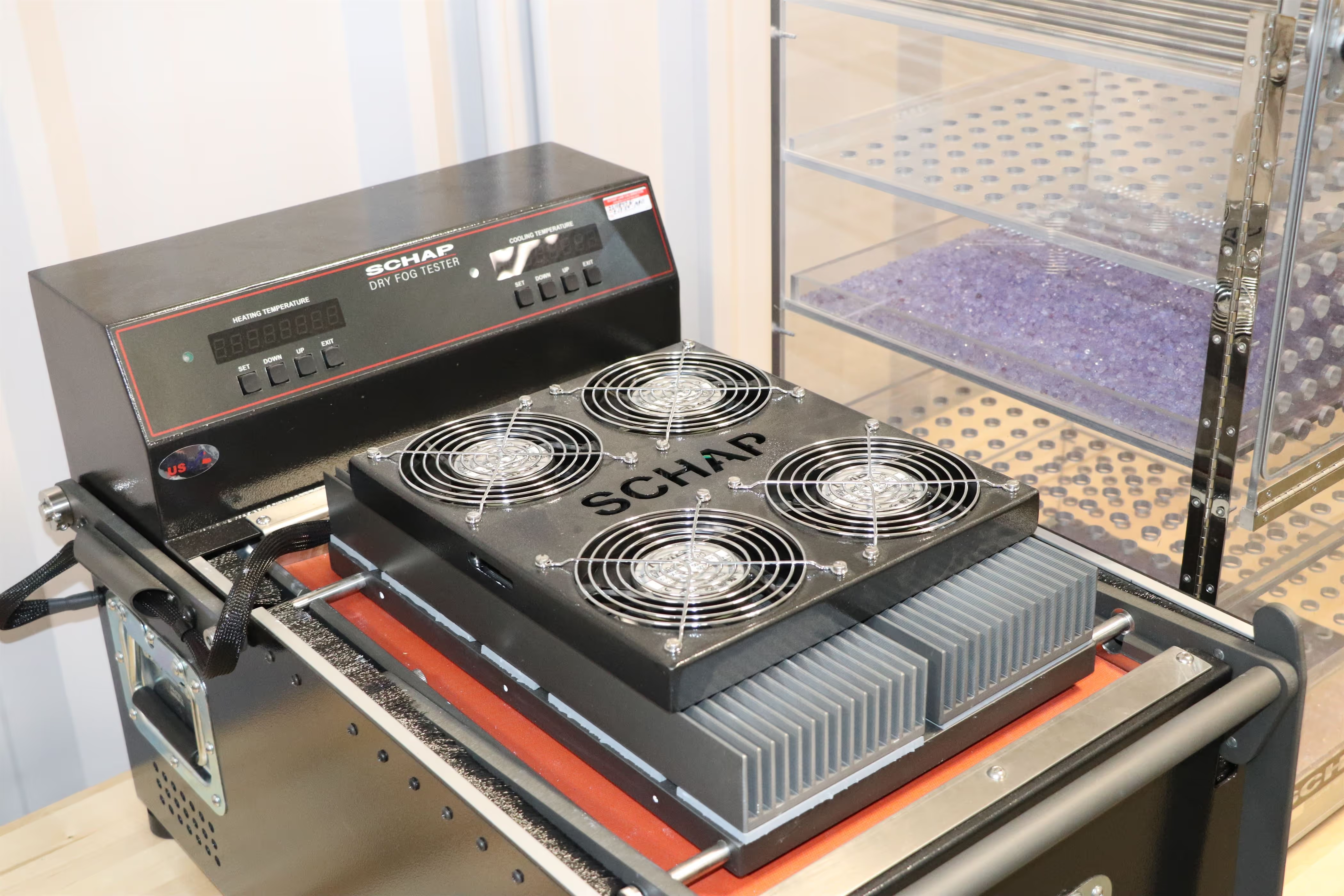
Fogging (VOC and FOG)
Fogging testing is an important process in evaluating the tendency of automotive materials to release volatile substances that condense on surfaces, particularly the interior glass, such as windshields and windows. This test measures the amount of volatile organic compounds (VOCs) that evaporate from materials like plastics, adhesives, foams, and textiles under elevated temperatures and condense on cooler surfaces. In the automotive industry, fogging and VOC testing is crucial for ensuring clear visibility for drivers and maintaining a clean and safe vehicle interior environment. High levels of fogging can obscure vision, pose safety risks, and reduce the aesthetic appeal of the vehicle interior.
Specific Gravity
Specific gravity testing is a method used to determine the density of automotive materials relative to the density of water, providing insight into the material's weight and suitability for specific applications in vehicle design.
Odor
Odor testing evaluates the “smell” emitted by various materials used in a vehicle's interior, such as plastics, textiles, foams, and adhesives, under different conditions. This involves exposing material samples to elevated temperatures or other environmental conditions and having a trained panel assess the intensity and character of any emitted odors. The results help manufacturers select materials that are low in volatile organic compounds (VOCs) and other odor-causing substances.
Cyclic Corrosion/Salt Fog
Cyclic corrosion and salt fog testing are essential methods for assessing the durability and corrosion resistance of automotive materials, particularly metals, coatings, and surface treatments exposed to harsh environmental conditions. These tests simulate real-world exposure to elements such as salt, humidity, temperature fluctuations, and other corrosive agents that vehicles encounter, especially in coastal regions or areas with heavy road salt use. Salt fog testing involves exposing materials to a mist of saltwater in a controlled environment to accelerate corrosion processes, while cyclic corrosion testing alternates between different conditions, such as wet, dry, and humid cycles, to more closely replicate natural weathering. Common standards for corrosion resistance are ASTM B117 and ISO 9227.
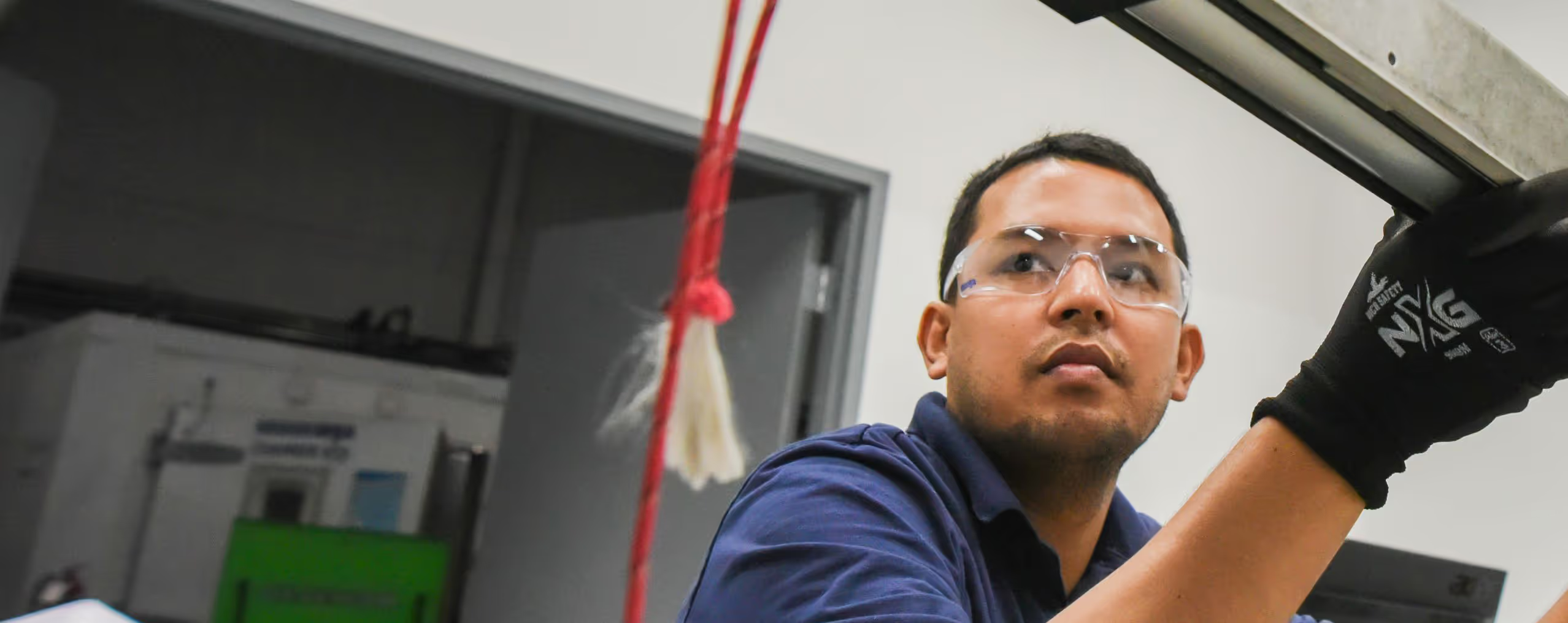
Ready to Get Started?
Let's discuss your testing needs and how MGA can help. Our team is ready to provide the expertise and solutions you're looking for.