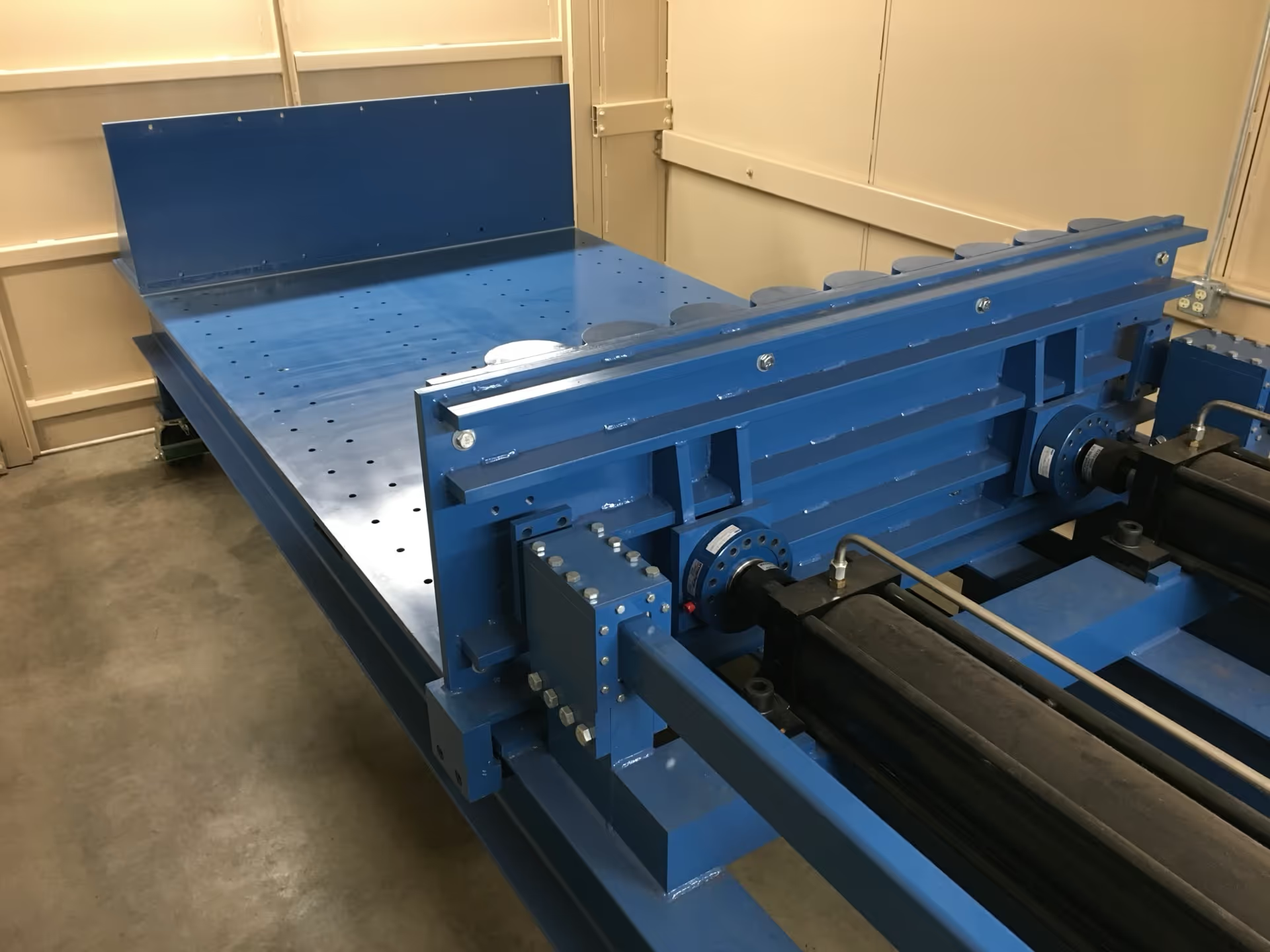
Battery Testing: Module, Pack, and Full Vehicle
MGA Research offers comprehensive battery testing services for modules, packs, and full vehicles across three specialized facilities, leveraging over 20 years of experience and advanced equipment to ensure safety, performance, and regulatory compliance for automotive, aerospace, and energy storage applications.
Quick Overview
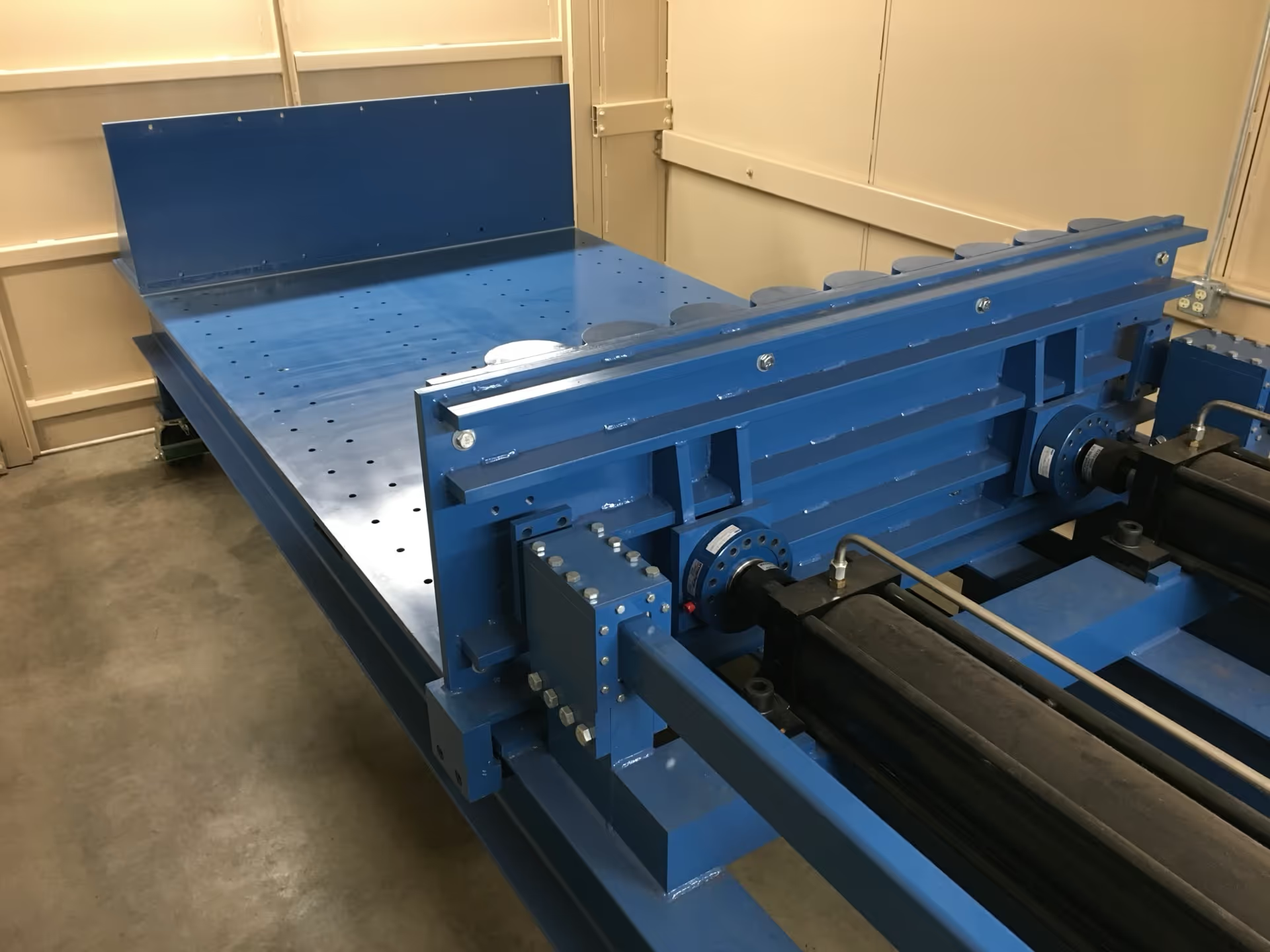
Comprehensive Battery Testing Services
We offer extensive testing for battery modules, packs, and full vehicles across three specialized facilities, serving automotive, aerospace, and energy storage applications.
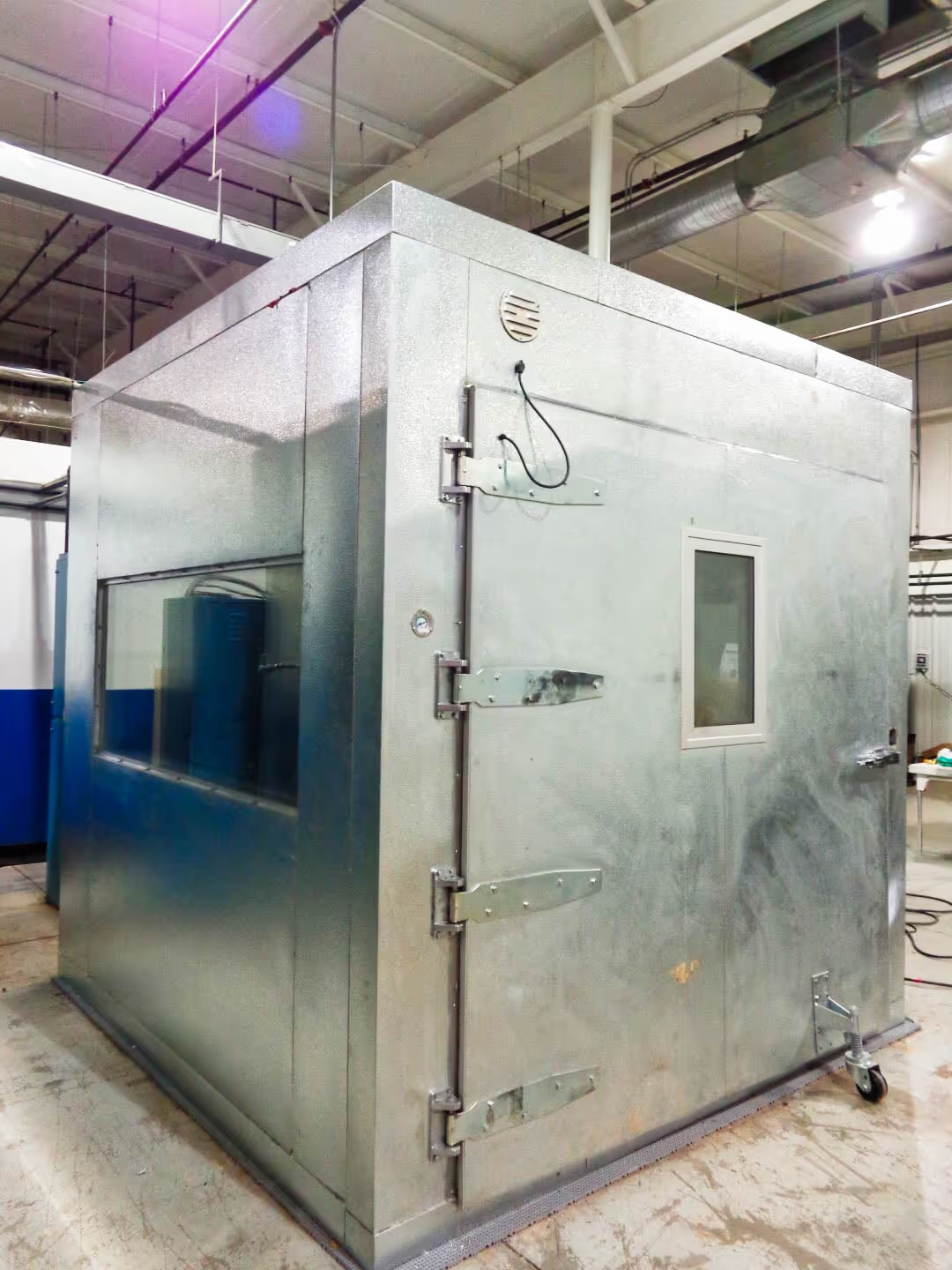
Advanced Testing Capabilities
We conduct a wide range of tests, including cycling, durability, vibration, environmental exposure, and other abuse testing for batteries of all sizes.
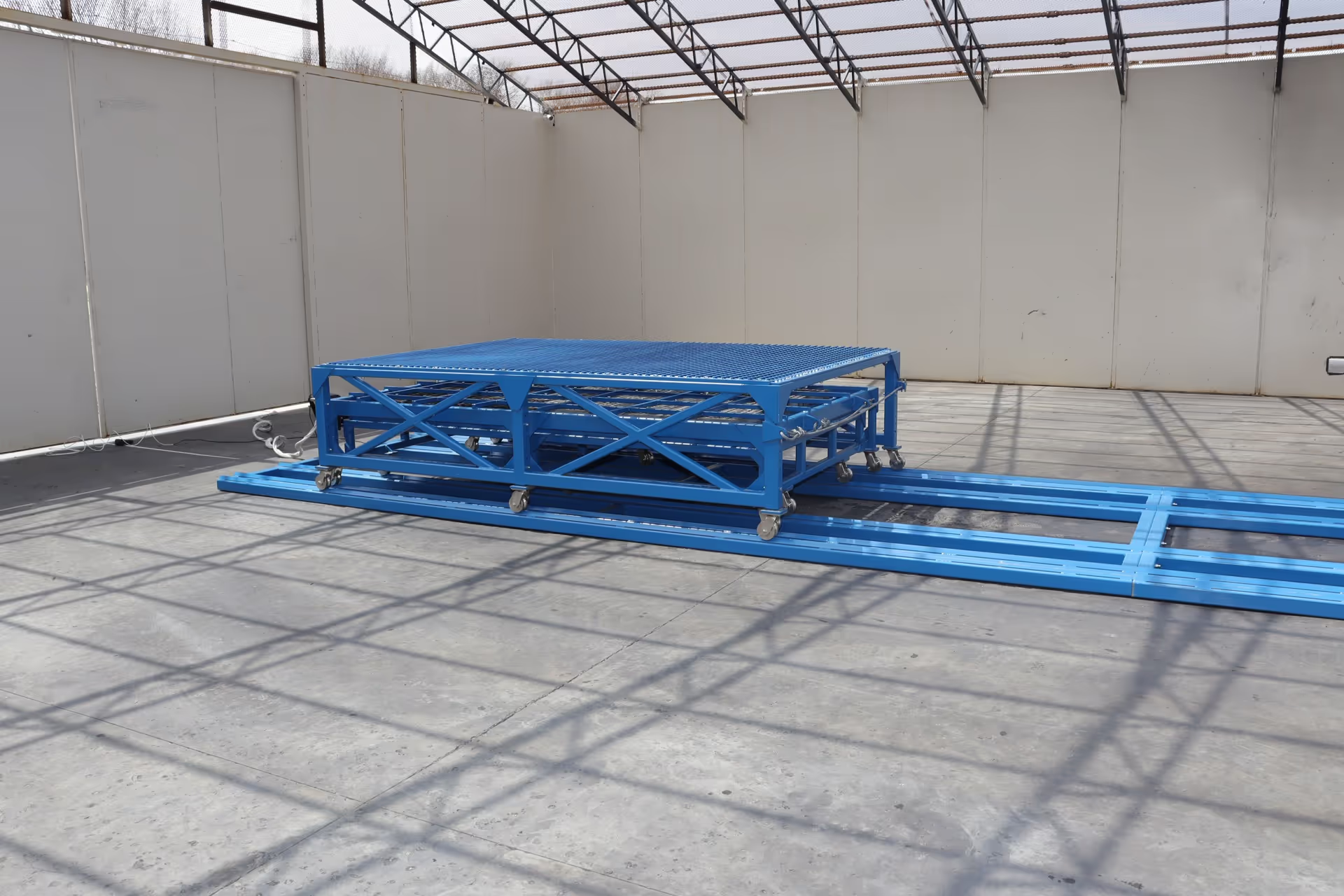
Industry-Leading Fire and Thermal Testing
We provide unique full pack and vehicle thermal propagation testing in our specially designed large-volume test chamber.
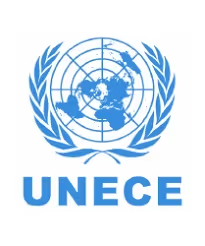
Regulatory Compliance Expertise
We ensure batteries meet various industry standards, including UN38.3, ECE R100, ECE R136, DO-311, FMVSS 305a NPRM, and SAE J2464/J2969.
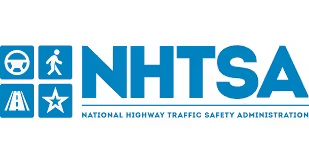
Research Partnership with NHTSA
We collaborate with NHTSA on EV battery safety topics, contributing to the research surrounding Global Technical Regulation (GTR) 20 and more.
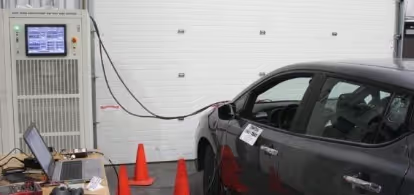
Extensive Industry Experience
We leverage over 20 years of battery and electric vehicle testing experience, dating back to the earliest NHTSA EV testing programs.
MGA Research is a leader in performance, safety, and environmental battery testing, recognized by our commitment to precision, innovation, and safety in evaluating battery performance across various industries. At the core of MGA’s capabilities, our three battery testing facilities are equipped with advanced equipment and operated by highly skilled engineers and technicians. These facilities are designed to conduct a wide range of tests that meet specific industry standards and regulatory requirements, each with their own specialty.
When MGA began testing battery cells for electric vehicles, the initial focus from our customers was on the safe shipping of these batteries following the United Nations shipping regulation “UN Transportation Testing of Lithium-Ion Batteries” (UN 38.3). From there, the additional needs from the industry have led MGA to greatly expand upon the regulatory tests into unique and customized approaches. Our Wisconsin site is uniquely suited to meet industry needs due to our isolated location, 400 acres of space, and the expertise of our staff with automotive testing. Our Wisconsin battery abuse facility, plus the additional capability established in Holly, Michigan puts MGA in a prime position to support mechanical, electrical, and environmental testing on batteries of all sizes.
MGA Advantage
MGA utilizes a network of three battery test facilities, each with unique expertise, to provide the following advantages to our customer base:
- Dedicated test facilities for each stage of the battery: cell, module, and full pack/vehicle.
- Wide range of capability including cycling, durability, vibration, environmental exposure, and abuse on cells and packs ranging in size from a few watts to 100+ kW packs.
- World class battery abuse testing facilities and equipment, much of which is MGA designed and manufactured.
- Unmatched battery abuse capabilities ranging from cell level nail penetration to full vehicle thermal propagation testing including key compliance test regulations including UN38.3, ECE R100, ECE R136, SAE J2464, SAE J2969, ISO 20653, DO-311, and more.
- MGA is a research partner to the NHTSA for EV battery safety topics. See our work related to Global Technical Regulation (GTR) 20 here.
- Over 20 years of battery and electric vehicle experience, dating back to the earliest NHTSA EV testing.
MGA is equipped for complete testing services associated with the development and safety validation of modern vehicle batteries. A generic battery development test matrix can be seen below. Utilizing our network of battery test labs, we are capable of testing and validation of batteries of all sizes from single cells/small modules to 100+kW packs found in modern EV’s.
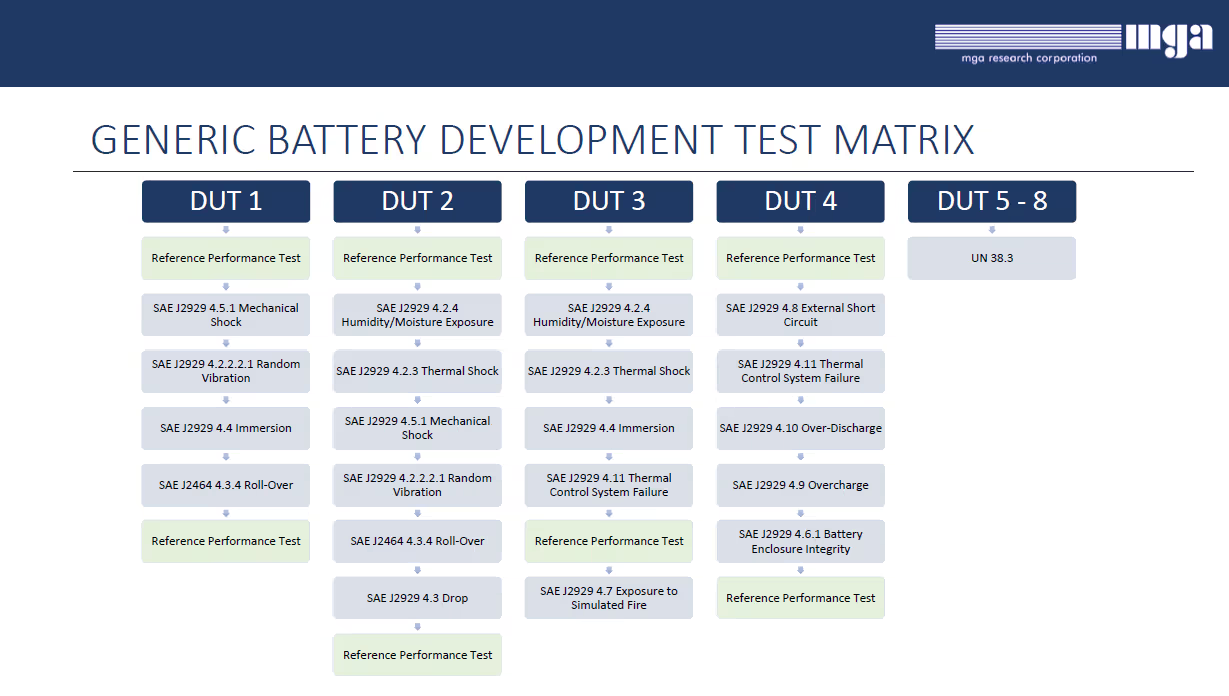
The testing process generally begins with initial characterization, where batteries undergo comprehensive evaluations to assess their electrical and thermal properties. This phase includes measuring capacity, voltage profiles, internal resistance, and impedance to establish baseline performance metrics. These tests provide essential data for understanding how the battery behaves under different operating conditions and help engineers optimize its design.
Safety testing involves subjecting batteries to extreme conditions such as high temperatures, mechanical stress, and overcharging to simulate worst-case scenarios. This ensures that batteries can withstand abuse without compromising safety or performance. Thermal runaway tests, where batteries are intentionally forced into overheating conditions, are critical to evaluate the effectiveness of thermal management systems and cell design features.
Performance testing focuses on evaluating how batteries perform under normal operating conditions over their lifecycle. Cycling tests, which involve charging and discharging batteries repeatedly, simulate real-world usage patterns to assess capacity retention and cycle life. These tests help predict how long batteries will last and how they will perform over time.
Environmental testing examines how batteries respond to environmental factors such as humidity and exposure to various temperature ranges. These tests ensure that batteries can operate reliably under diverse outdoor elements.
Overall, battery electrification testing is a comprehensive and rigorous process that ensures the safety, reliability, and performance of batteries in electric vehicles and energy storage systems. By adhering to these testing protocols, manufacturers can confidently deliver batteries that meet the demands of modern transportation and energy infrastructure, paving the way for a sustainable and electrified future.
Unique Fire and Thermal Capability
Full Pack / Vehicle Thermal Propagation
MGA has built a large volume test chamber specifically designed for full vehicle thermal propagation and fire resistance testing in mind. Thermal propagation testing refers to a scenario where a specific cell or cells within a battery are intentionally put into the thermal runaway to evaluate potential “propagation” of the thermal event to other cells or modules. Batteries are designed with this possibility in mind, so engineers often focus on complete containment and design for gas ventilation to avoid heat buildup.
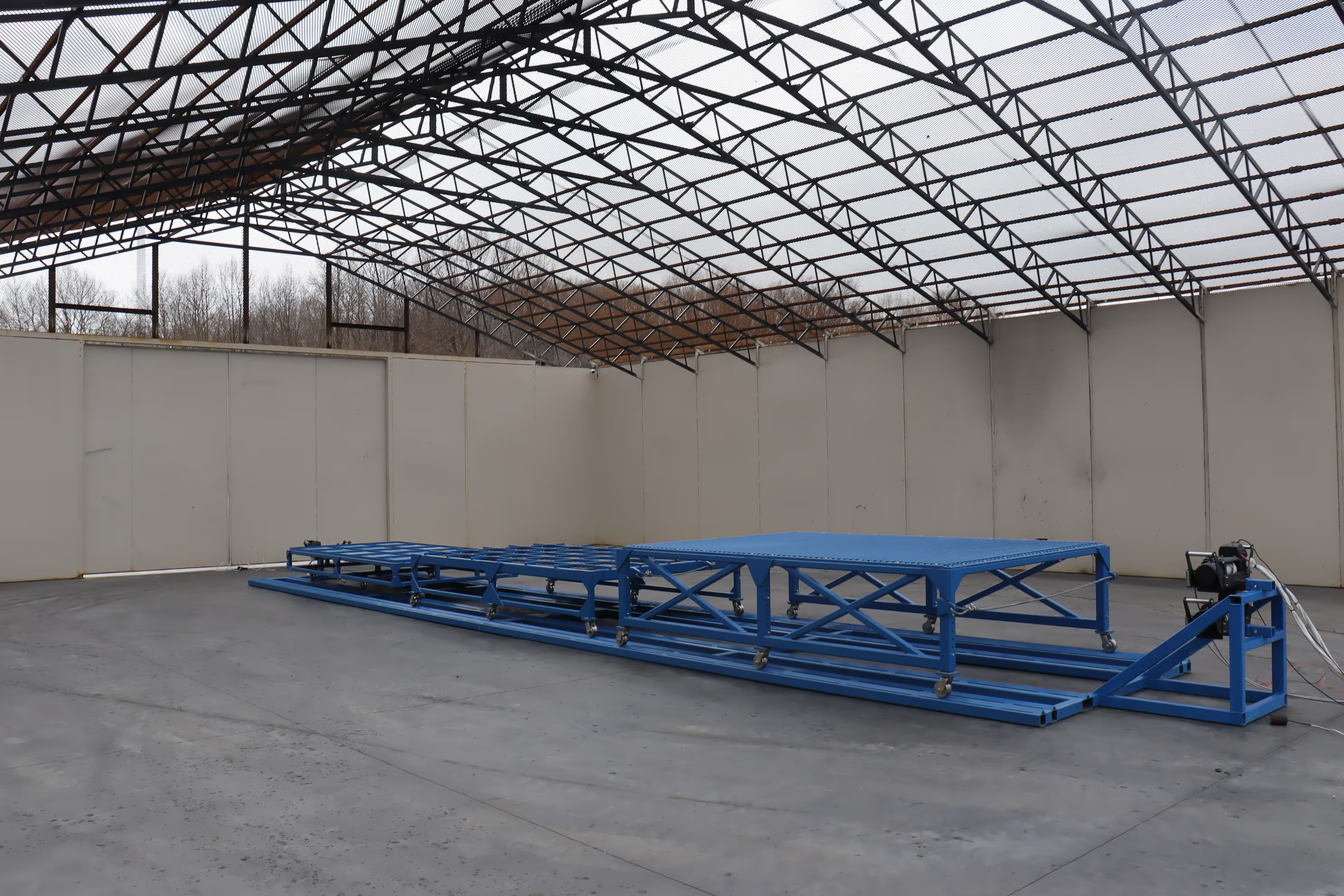
Industry Standards
Common Battery Test Standards that MGA performs are described below. A common theme across most standards include ensuring the electrical and thermal safety as it relates to the battery system when exposed to various conditions.
UN38.3
UN38.3 battery testing refers to a series of rigorous safety tests required by the United Nations for lithium batteries to ensure they can be safely transported, particularly by air. The tests are outlined in the UN Manual of Tests and Criteria, Section 38.3, and are designed to simulate the conditions that batteries might encounter during shipping. MGA’s test facilities are ISO 17025 accredited for UN38.3 testing. These tests include:
- T1: Altitude Simulation - Exposes the battery to low pressure (simulating high altitude) to ensure it doesn't leak, vent, or rupture.
- T2: Thermal Test - Subjects the battery to rapid temperature cycling between extreme hot and cold to assess its stability under thermal stress.
- T3: Vibration Test - Simulates the vibrations a battery might experience during transportation to ensure it remains intact and functional.
- T4: Shock Test - Applies sudden mechanical shock to the battery to test its resilience against impacts.
- T5: External Short Circuit - Simulates an external short circuit to verify the battery’s ability to withstand it without causing fire or explosion.
- T6: Impact/Crush - For small batteries, an impact test simulates a crush scenario to ensure safety under mechanical stress.
- T7: Overcharge - Overcharges the battery to see if it can handle excessive charging without failure.
- T8: Forced Discharge - Forces a discharge on the battery to check its safety under this abnormal condition.
ECE R100
ECE R100 is a UN regulation that specifies safety requirements and testing protocols for rechargeable energy storage systems (REESS), particularly lithium-ion batteries used in electric vehicles (EVs) and hybrid vehicles. The regulation includes a range of tests to ensure the safety, reliability, and performance of battery packs under various conditions. MGA is well suited to perform all key battery tests under ECE R100 including:
- Vibration: Simulates the vibrations a battery may experience during vehicle operation
- Thermal Shock and Cycling Test: Exposes the battery to extreme temperature changes to evaluate its ability to withstand thermal stress without degradation or failure.
- Mechanical Shock Test: Subjects the battery to mechanical shocks to simulate impacts, ensuring it remains safe and functional after severe jolts.
- External Short Circuit Test: Tests the battery's safety by intentionally short-circuiting
- Overcharge Protection Test: Assesses the battery’s ability to handle overcharging conditions without resulting in hazardous events like thermal runaway.
- Over-discharge Protection Test: Evaluates the battery's performance and safety when over-discharged, preventing cell damage or unsafe conditions.
- Fire Resistance Test: Exposes the battery to direct flames to assess its ability to resist external fire propagation.
ECE R136
ECE R136 ensures that the batteries used in electric motorcycles and LEVs meet stringent safety standards, providing a high level of protection to users and minimizing risks associated with battery use in these vehicles. Key aspects of ECE R136 include:
- Mechanical Integrity: Ensures that batteries can withstand mechanical impacts, vibrations, and other stresses
- Thermal Management: Evaluates the battery's ability to manage thermal stress and prevent thermal runaway
- Electrical Safety: Includes tests for overcharge, over-discharge, and short-circuit conditions
- Environmental Exposure: Tests for resistance to environmental factors such as water, dust, and humidity
- Fire Resistance: Assesses the battery's ability to resist ignition and prevent the spread of fire
DO 311
DO-311, published by RTCA (Radio Technical Commission for Aeronautics), specifies the minimum operational performance standards for rechargeable lithium batteries and battery systems used in aviation. It outlines testing requirements to ensure the safety, reliability, and performance of lithium batteries in aircraft applications. Key aspects of DO-311 include:
- Thermal Runaway Containment: Ensures that battery designs prevent thermal runaway or safely contain it if it occurs.
- Mechanical Shock and Vibration: Evaluates the battery's ability to withstand mechanical shocks and vibrations typical of aviation environments.
- Electrical Safety: Includes tests for overcharge, over-discharge, and short-circuit conditions.
- Environmental Tests: Assesses battery performance under extreme temperatures, humidity, altitude, and other environmental conditions found in aircraft operations.
- Fire and Overheating: Evaluates the battery's behavior under fire exposure and overheating scenarios to ensure it does not contribute to onboard fire hazards.
SAE J2464 and SAE J2969
SAE J2464 and J2969 are standards developed by the Society of Automotive Engineers (SAE) that specify recommended practices for testing the abuse tolerance of lithium-ion and other rechargeable battery systems and enclosures used in electric and hybrid vehicles. Similar to other standards, evaluations revolve around the key tests below:
- Mechanical Abuse
- Thermal and Environmental Abuse
- Electrical Abuse, including overcharge, over discharge, and short circuit.
- Fire exposure and Thermal Runaway Containment
- Vibration and Mechanical Shock
ISO 20653 and Enclosure Ingress
ISO 20653 is an international standard that specifies the degrees of protection provided by enclosures (IP code) for electrical equipment against environmental factors, such as dust, water, and foreign objects, particularly in road vehicles. The standard is primarily focused on ensuring that electrical and electronic components, including battery enclosures and connectors, are adequately protected against ingress of solid particles (like dust) and liquids (like water) to ensure their reliability and safety under various operating conditions.
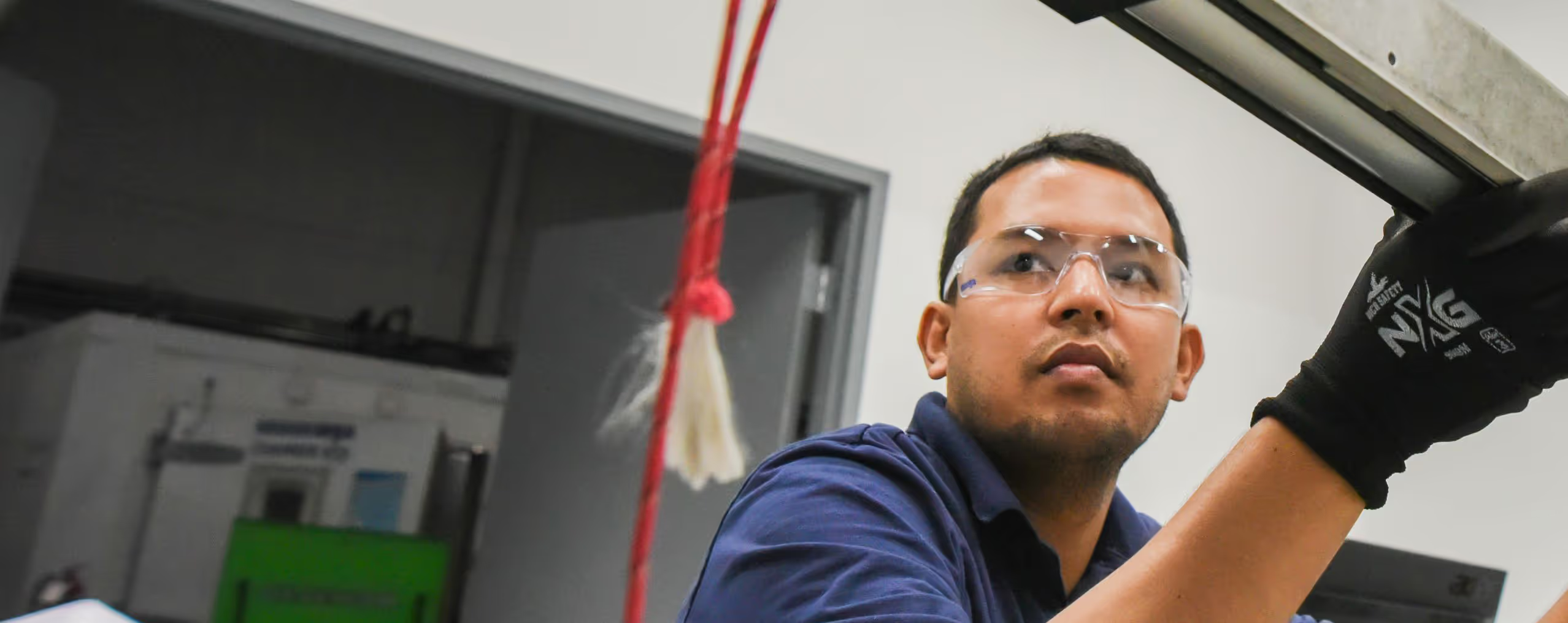
Ready to Get Started?
Let's discuss your testing needs and how MGA can help. Our team is ready to provide the expertise and solutions you're looking for.