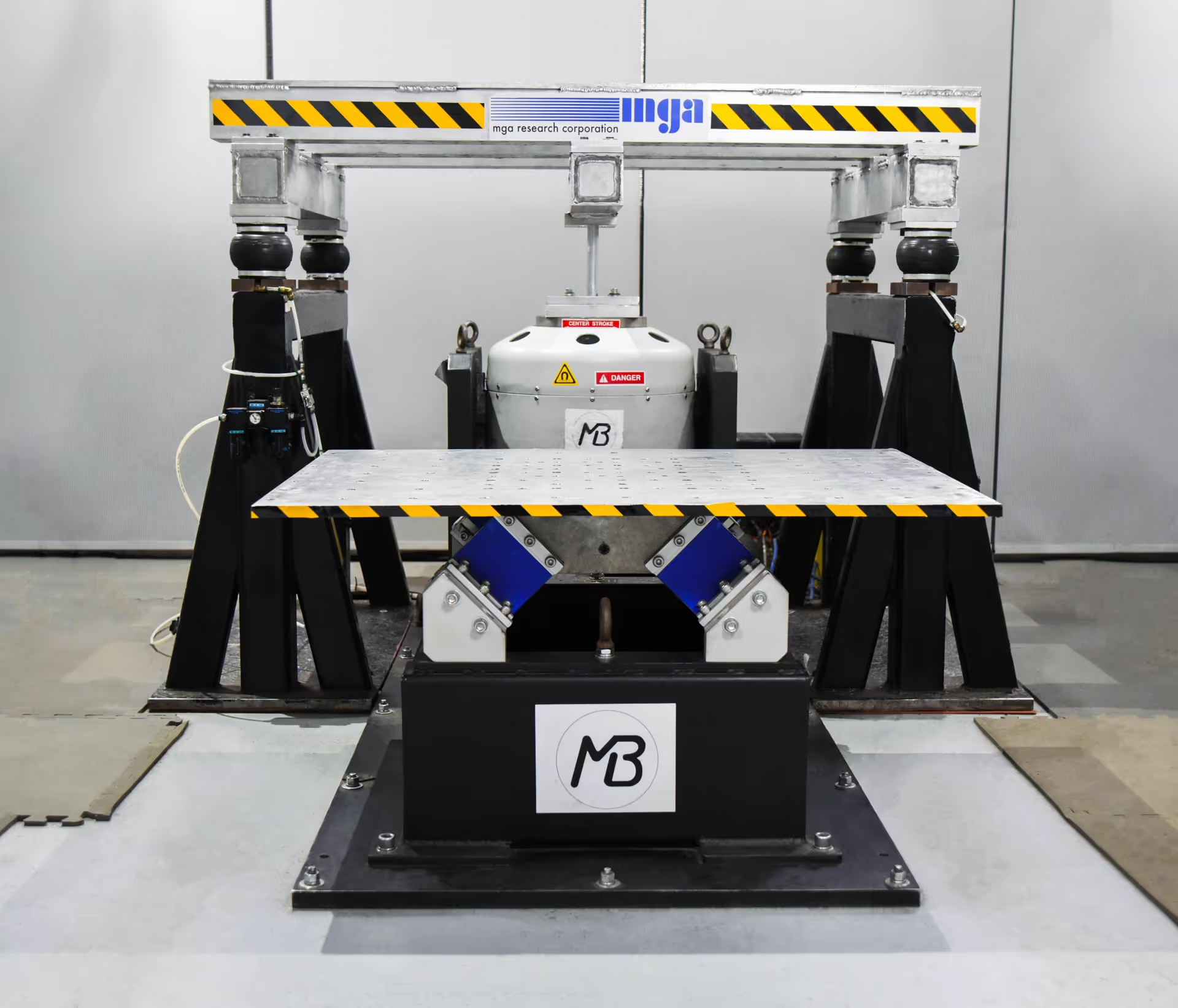
Vibration Testing
MGA offers comprehensive vibration testing services across seven laboratories, utilizing state-of-the-art equipment to simulate real-world conditions and ensure product reliability for automotive, aerospace, electronics, and defense industries.
Quick Overview
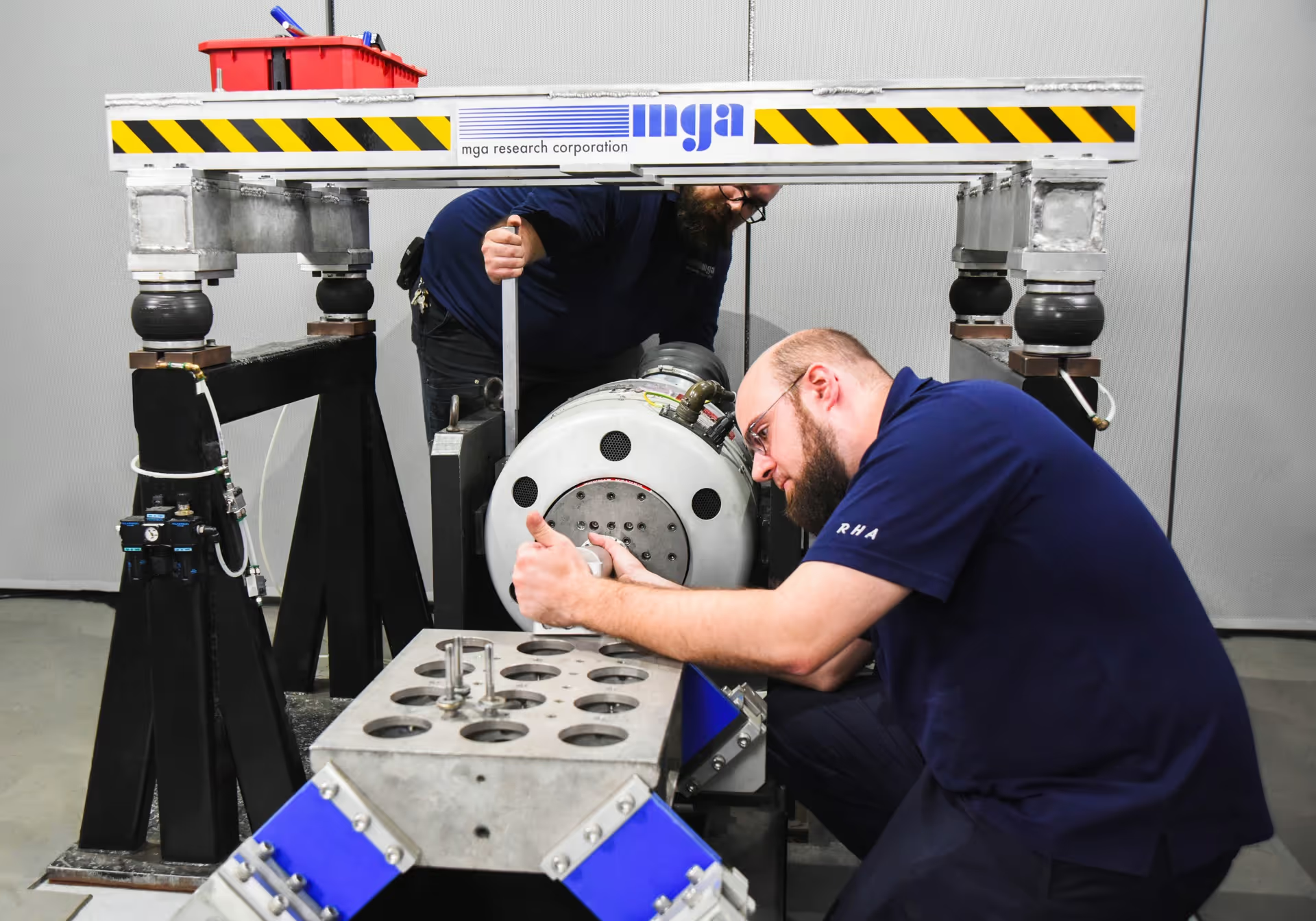
Comprehensive Vibration Testing Services
We offer extensive vibration testing capabilities across seven laboratories, serving automotive, aerospace, electronics, and defense industries.
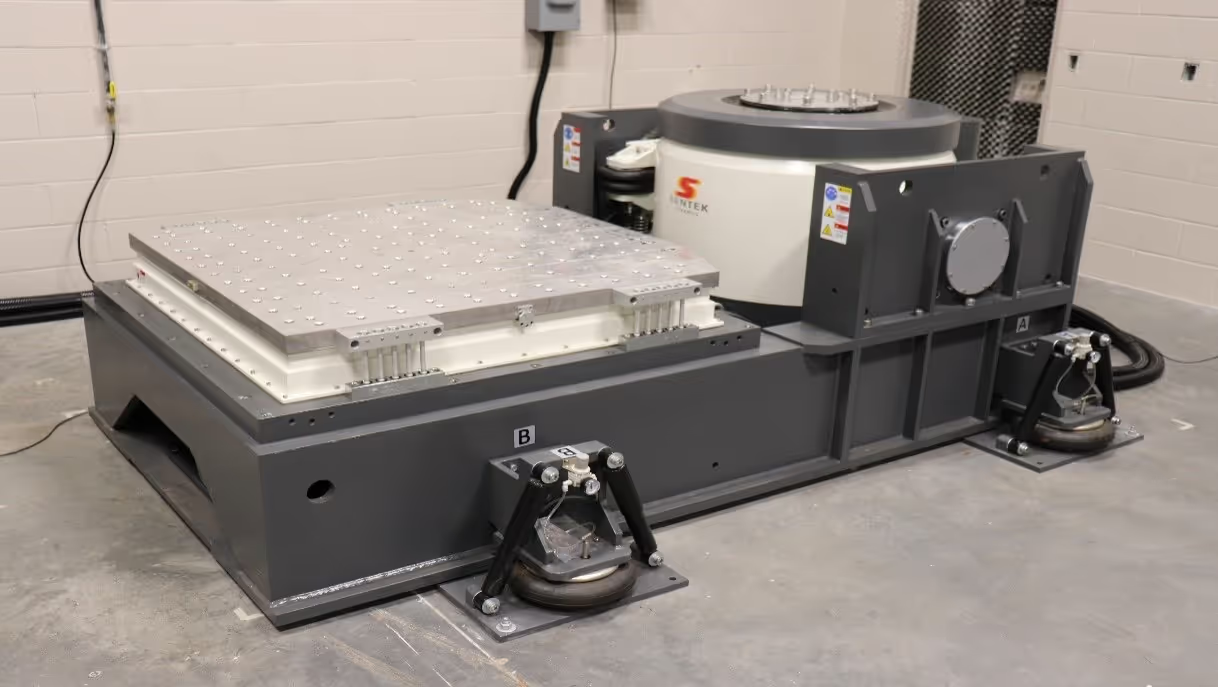
Advanced Testing Equipment
We utilize over 40 electrodynamic shakers and 15+ multi-axis tables to conduct a wide range of vibration tests, including sine, random, and shock testing.
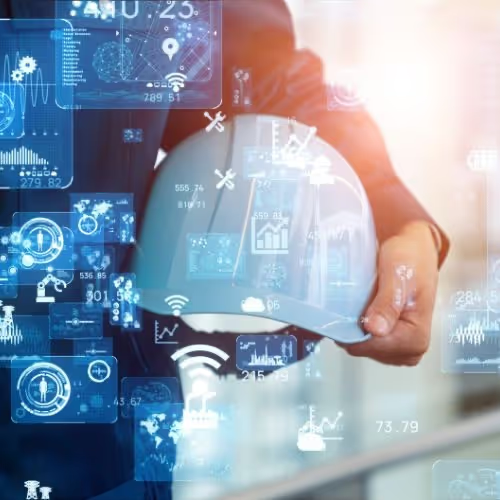
Multi-Industry Expertise
We provide tailored vibration testing solutions for various sectors, including automotive components, batteries, aerospace parts, and military equipment.
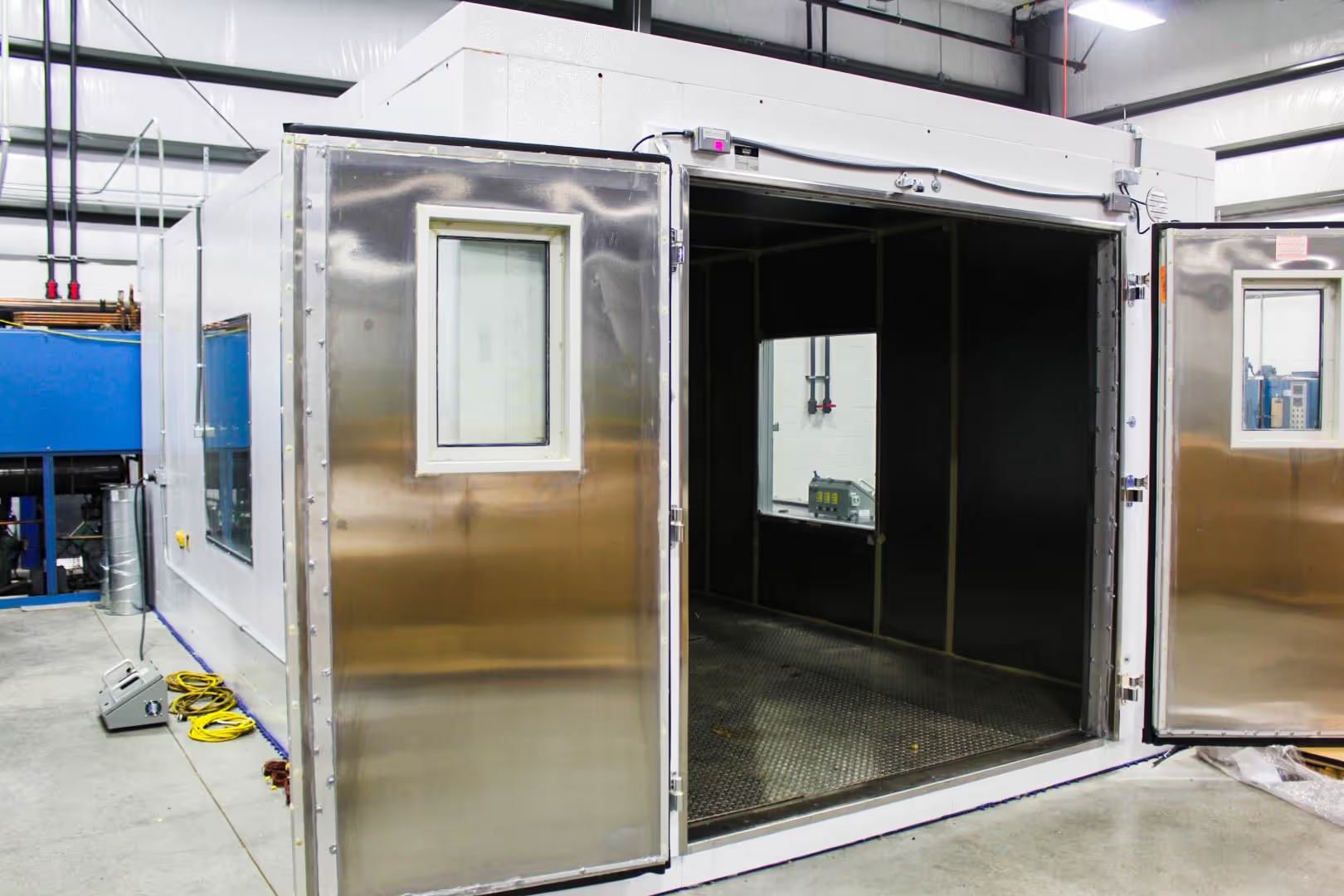
Environmental Simulation Capabilities
We combine vibration testing with temperature and humidity control to assess product performance under complex environmental conditions.
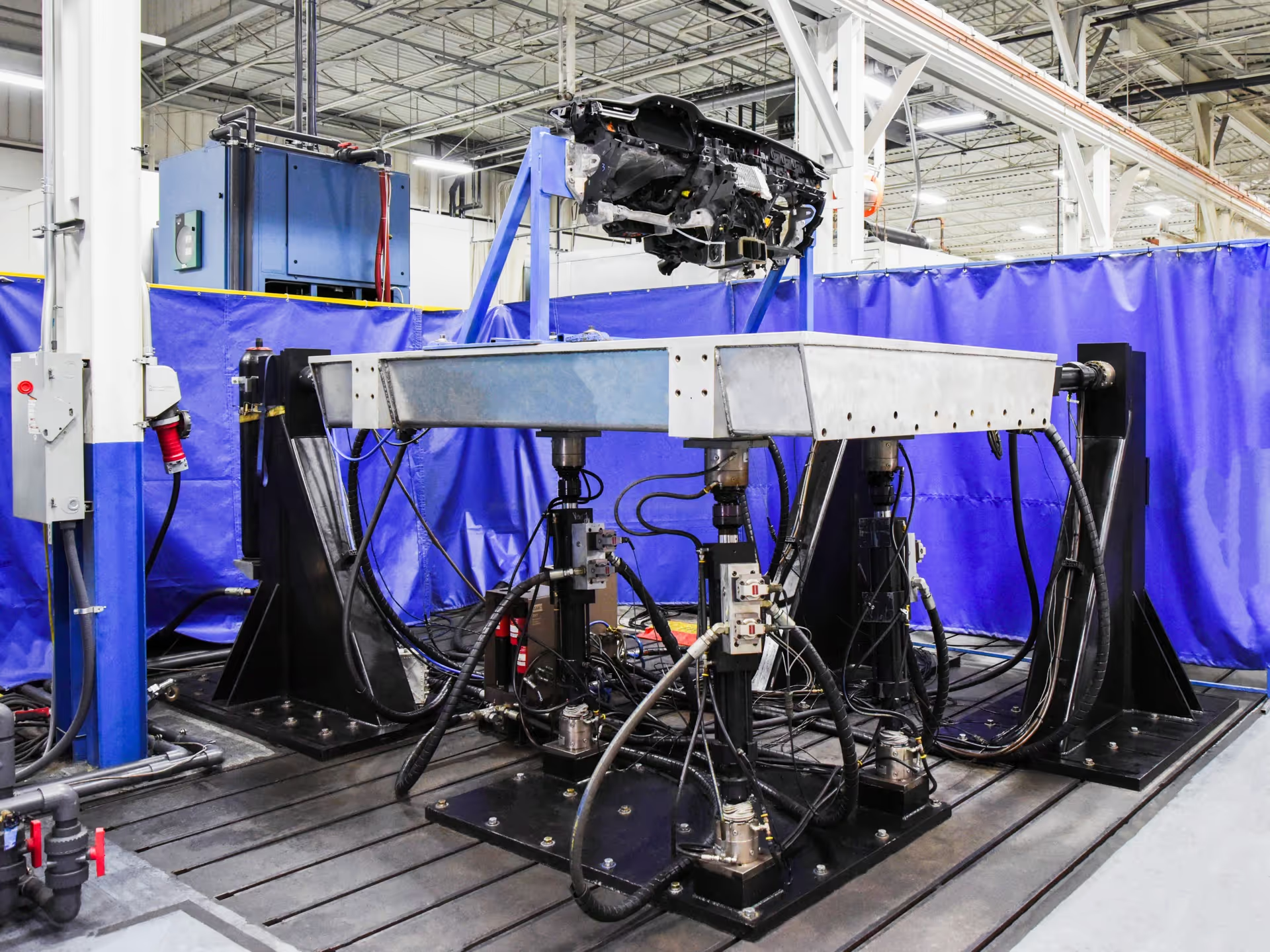
Road Simulation Technology
We use advanced multi-axis simulation tables and four-post rigs to replicate real-world driving conditions for both full vehicles and sub-systems.
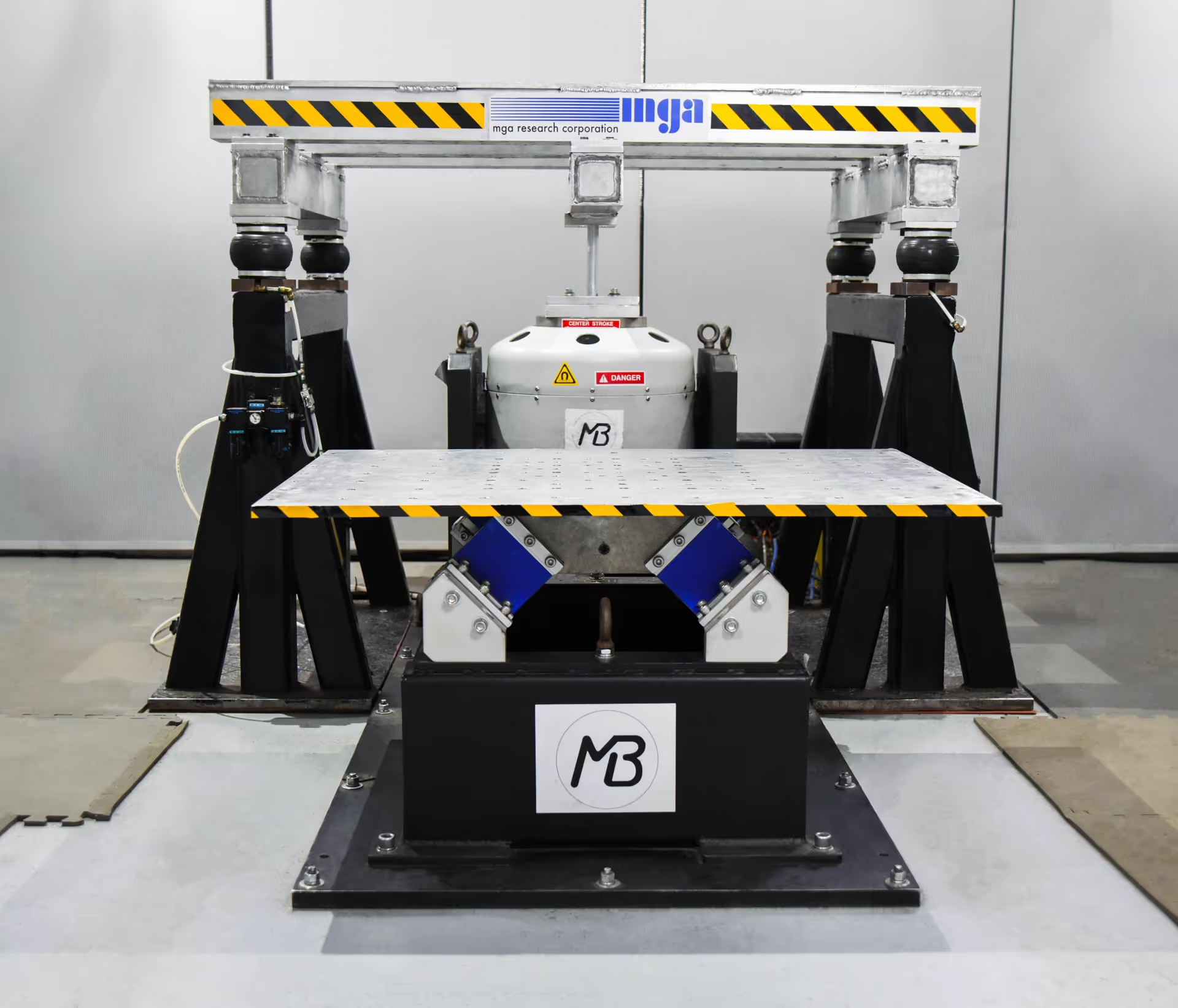
Specialized Acoustic Testing
We offer anechoic chambers with MB Dynamics shakers for noise, vibration, and harshness (NVH) testing, including buzz-squeak-rattle (BSR) evaluations.
Automotive design is an ongoing transformative evolution, driven by technological advancements, sustainability imperatives, and changing consumer expectations. These trends are not merely cosmetic but reflect profound shifts in how vehicles are conceived, constructed, and perceived in the modern era. These new systems and technologies, some of which are critical to safety and quality, are susceptible to issues due to road produced vibration, and as such require extensive testing to ensure long term reliability.
Vibration testing is a critical piece in the testing process in many industries used to assess the durability, reliability, and performance of mechanical and electronic systems when subjected to simulated real-world conditions. By subjecting a product or component to controlled vibrations, engineers can identify potential weaknesses, structural flaws, or design issues that might lead to malfunction or failure during operation.
Of MGA’s network of nine laboratories across North America, seven have capability for vibration testing. Vibration testing is primarily conducted utilizing two styles of equipment. Single axis testing with high frequency potential is conducted with electro-dynamic (ED) shaker systems, while multi-axis testing is conducted using multi-axis simulation tables (MAST).
Applications
These shaker systems are integral to the development and validation of products and components in industries such as:
- Automotive: Testing vehicle components and systems for durability and reliability under road conditions.
- Battery: The drive to furthering electrification of vehicles has increased the need for vibration on energy storage systems (high voltage batteries).
- Aerospace: Simulating the vibrations experienced during flight to ensure the structural integrity and performance of aerospace components. Vibration is a critical part of FAA Flight Qualification requirements
- Electronics: Assessing the resilience of electronic devices to vibrations that may occur during transportation or operational use.
- Military and Defense: Validating the ruggedness of equipment used in harsh environments or under extreme conditions, such as rockets and missiles
MGA Advantage
- Unmatched capacity with over forty (40+) electrodynamic shakers and 15+ multi-axis tables
- Vibration testing integrated with Full DVP&R support
- Anechoic chambers featuring MB Dynamics shakers for NVH / Buzz-Squeak-Rattle (“BSR”) Testing
- Full environmental add-on capability featuring both temperature and humidity control
- Full capability including sine, random, sine-on-random, shock, multi-axis control, and modal analysis
Vibration Test Methods
ED Shaker Testing
Components or full assemblies are mounted on an electrodynamic shaker table that vibrates at various frequencies and amplitudes to simulate real-world conditions.
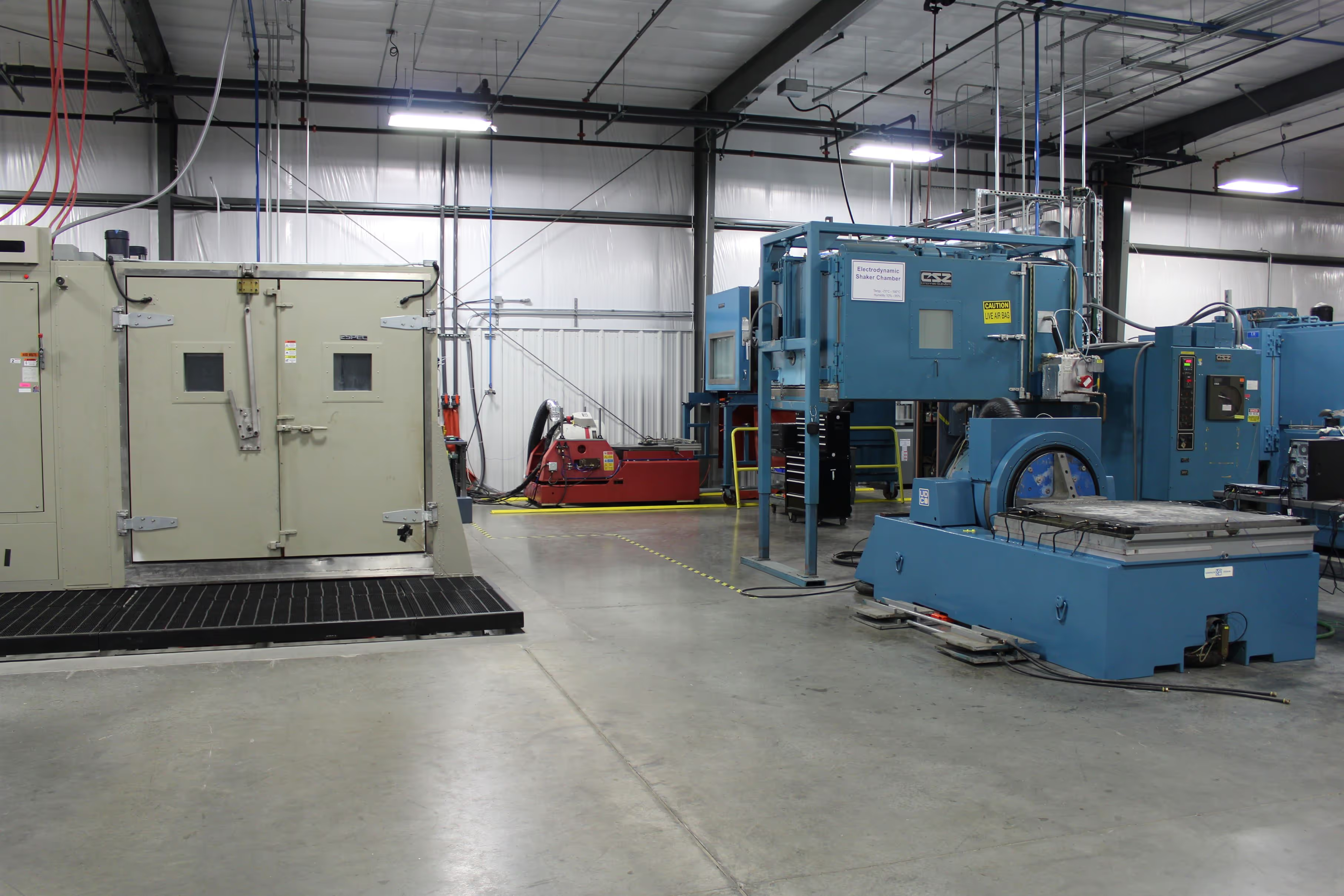
Electrodynamic shakers are designed with various specifications to accommodate different testing requirements, such as frequency range, maximum force capacity (measured in pounds-force or newtons), and displacement capabilities. They can generate vibrations across a wide frequency spectrum, typically from a few hertz (low-frequency vibrations) up to several kilohertz (high-frequency vibrations), depending on the model and application.
MGA supports all common vibration tests that utilize ED Shakers including sinusoidal (sine), Random, Sine-on-Random, Resonance sweeps and dwell, and Shock.
- Sinusoidal (Sine) Vibration / Resonance Sweep and Dwell – typically used to evaluate how a component or system responds to vibrations at specific frequencies. Frequently used for identifying resonant frequencies, which can lead to noise issues or damage. Ideally, the resonant frequency range is outside of the ranges the component would see in regular use. Unfortunately, this is rarely the case. Often, after identifying, components are subjected to these resonant frequencies continuously to accelerate stress and failure potential. Resonance searches can also provide feedback to the engineers, allowing the design to be modified which can help move the resonant frequencies outside of normal use ranges.
- Random Vibration – Commonly used in many industries including Aerospace and Automotive. Used to simulate real-world, unpredictable vibration environments that components will encounter during operation. Vibration is applied across a broad frequency spectrum, with varying amplitudes to mimic the random nature of road conditions and vehicle dynamics.
- Shock - Used to evaluate a component’s ability to withstand sudden changes in acceleration, or shock. A critical testing element for both the automotive industry, but also flight qualification testing the Space and Defense industries.
Road Simulation / Multi-Axis Simulation
The entire vehicle may be placed on a four-post rig, where each wheel rests on a platform that moves to replicate driving on different surfaces. Or, at a sub-system level, components can be placed on a Multi-Axis Simulation Table (“MAST”) to simulate vibration conditions with up to six degrees of freedom. MGA uses the latest MTS® controls with FlexTest controllers and RPC® Pro software.
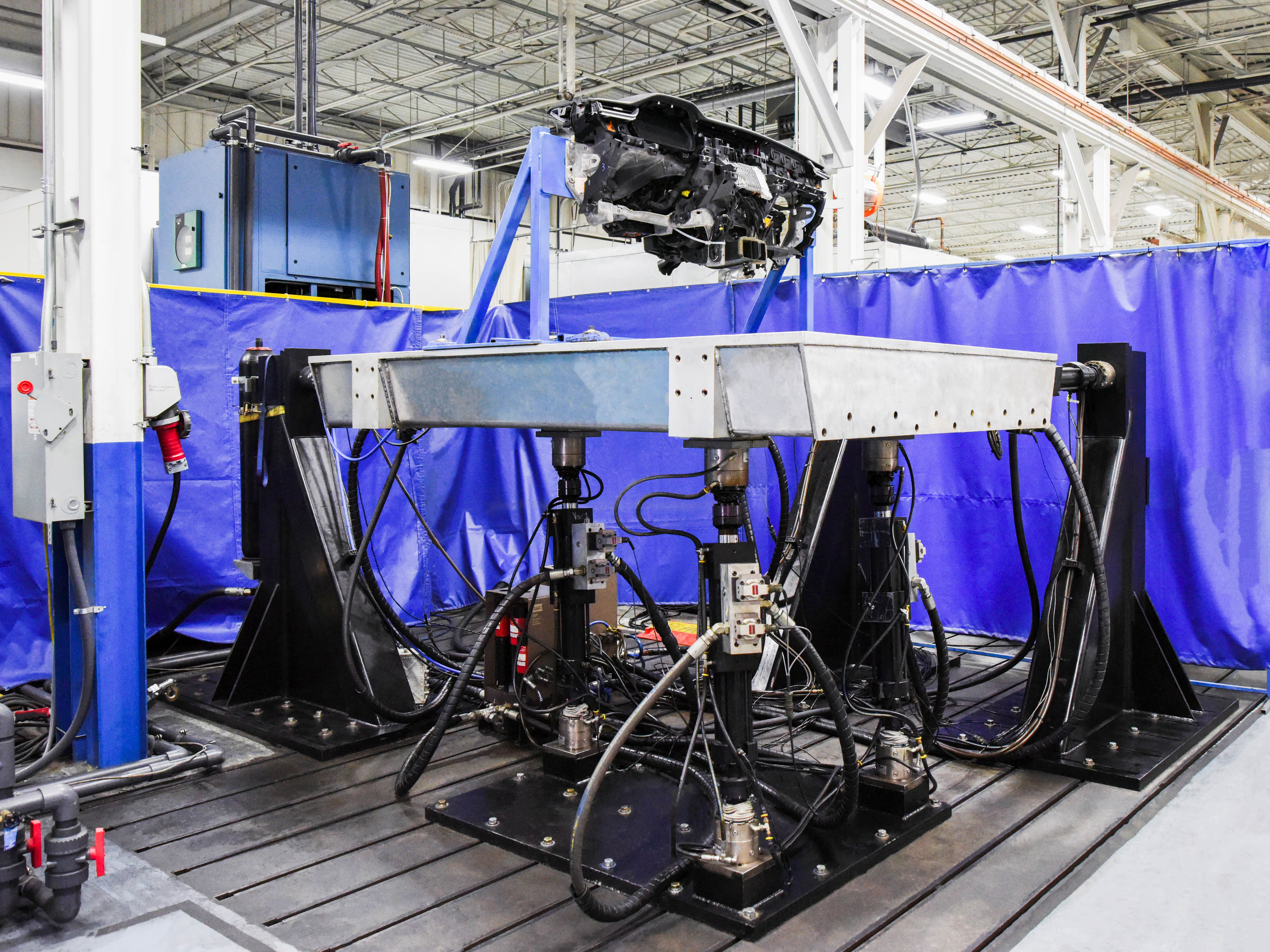
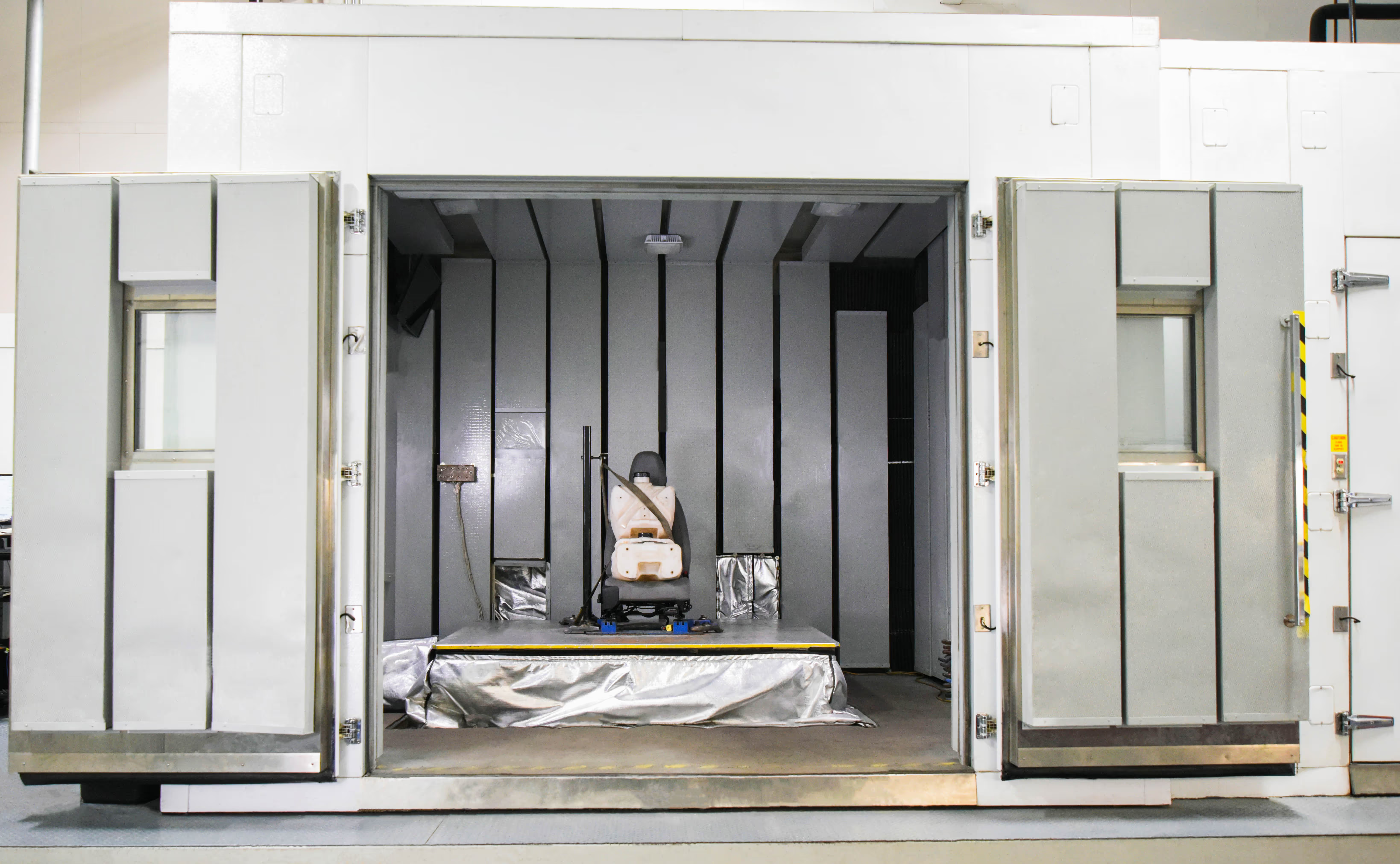
Environmental Testing Add-On
Combining vibration testing with other environmental conditions like temperature and humidity to assess how components perform under combined stresses. MGA has full environmental capability for all vibration types
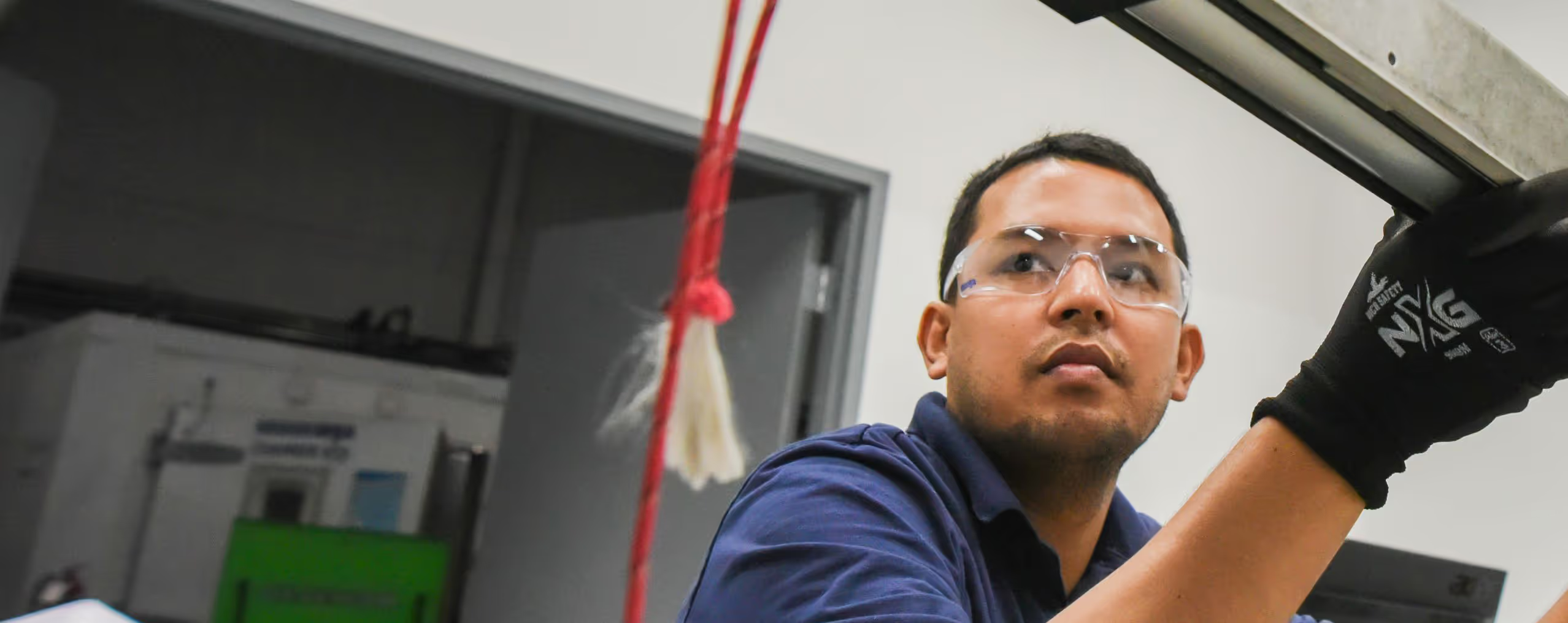
Ready to Get Started?
Let's discuss your testing needs and how MGA can help. Our team is ready to provide the expertise and solutions you're looking for.