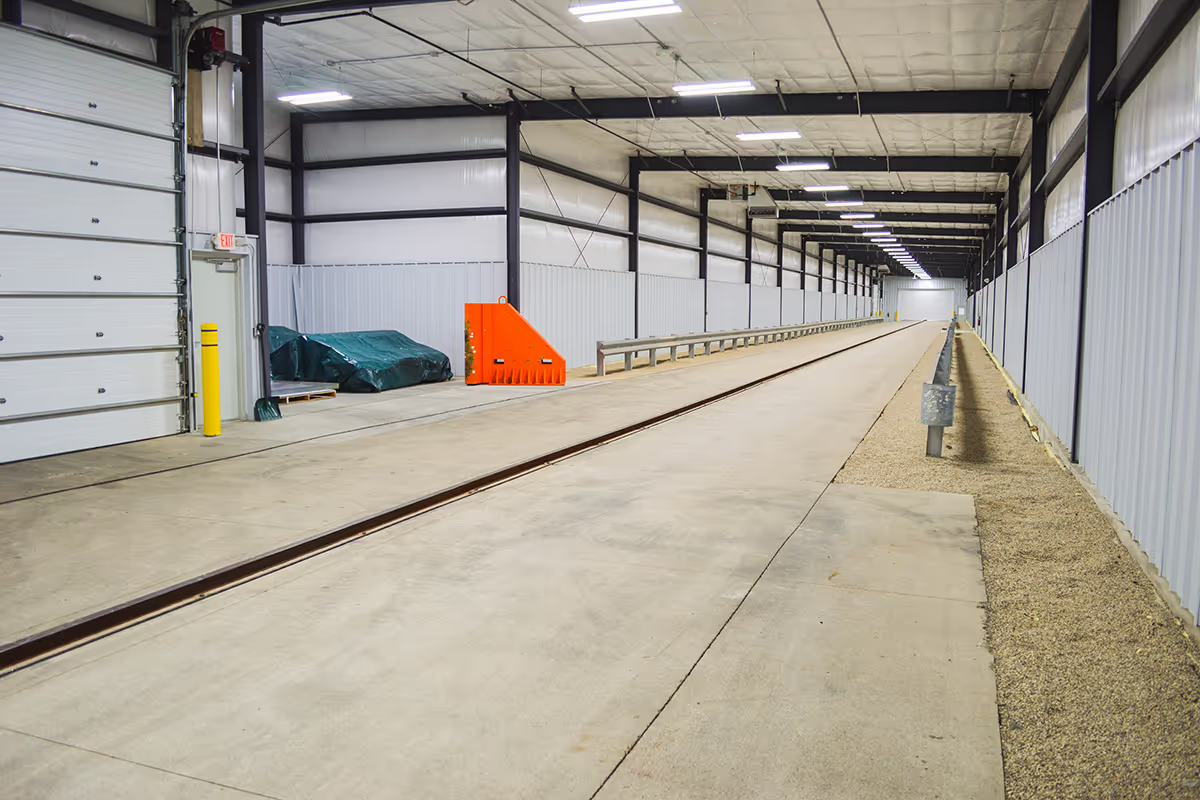
Vehicle Crash Testing
MGA Research Corporation offers comprehensive vehicle crash testing services, leveraging over 35 years of experience to support automotive safety development engineers from early prototypes through final regulatory compliance and consumer ratings.
Quick Overview
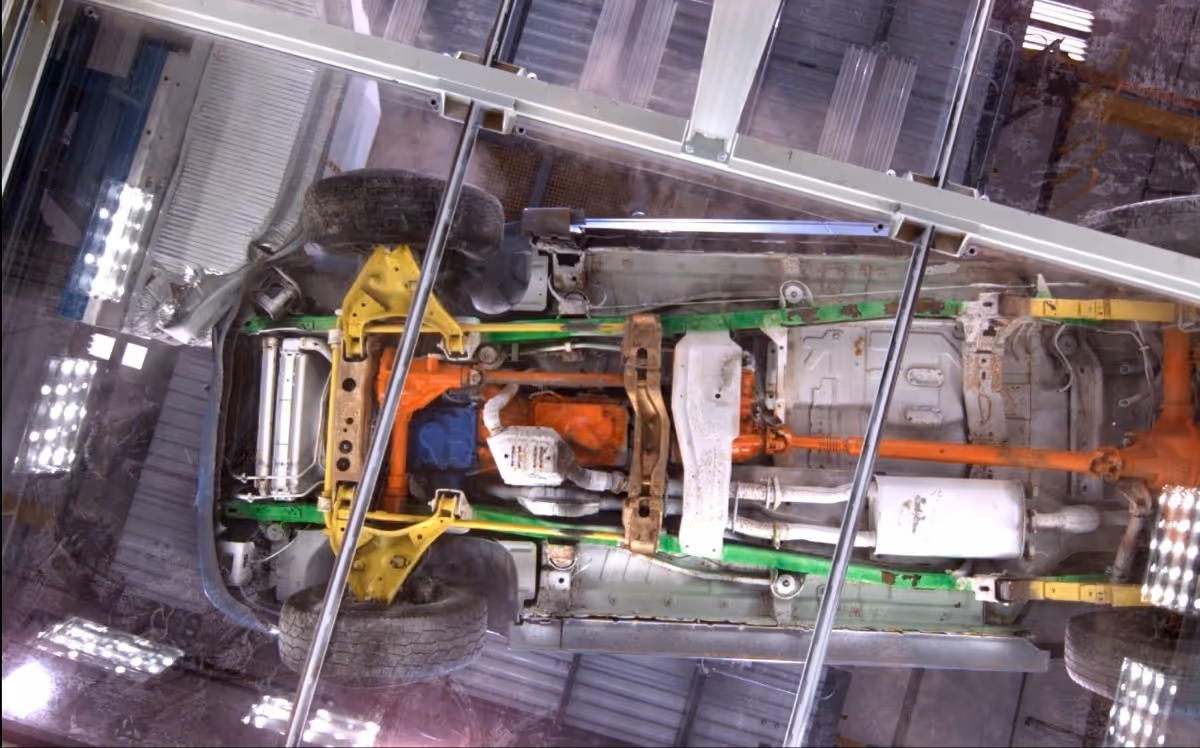
Comprehensive Development Test Support
MGA offers a complete range of vehicle crash tests to support vehicle development from early phase structural validations through consumer ratings.
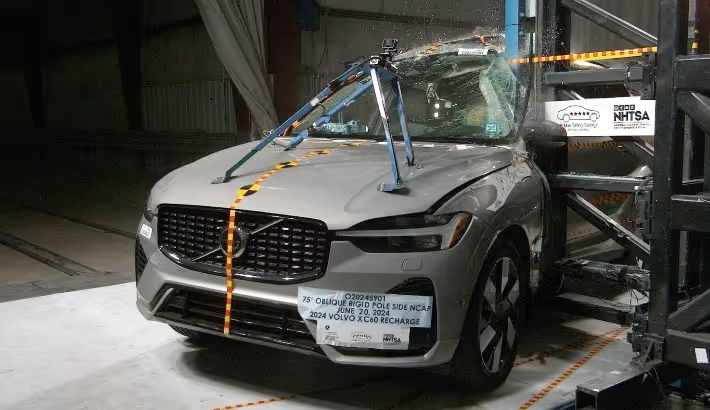
FMVSS Testing
We conduct all FMVSS crash test modes for U.S. safety compliance.
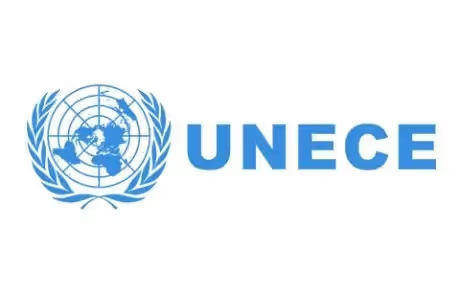
UN / ECE Type Approval
Experienced in meeting EU export requirements with multiple witness agencies

Consumer Testing: NCAP & IIHS
MGA is experienced in Global NCAP and IIHS test protocols, including the latest frontal and side impacts.
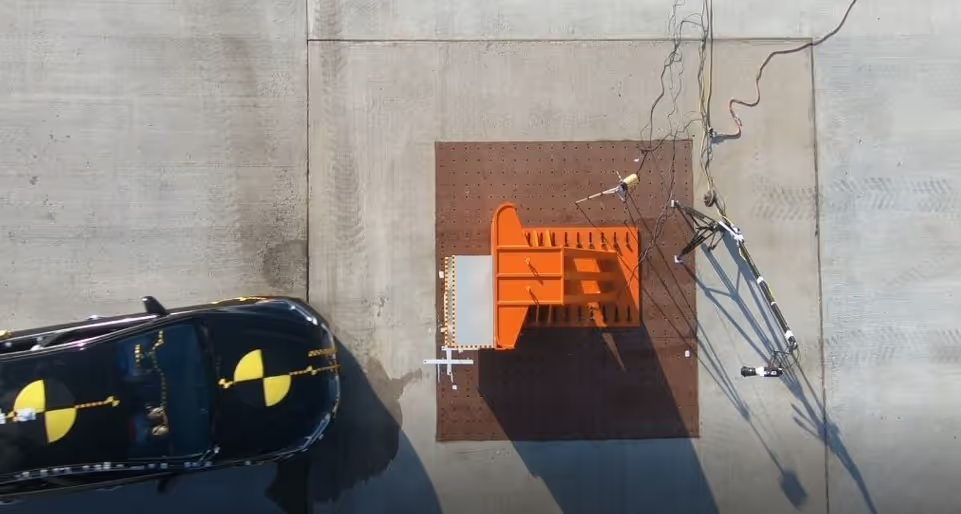
Custom Test Modes & Crash Research
We leverage our in-house equipment and fabrication experience to create unique crash test setups for specialized research projects, including car-to-car and other real-world crash scenarios.
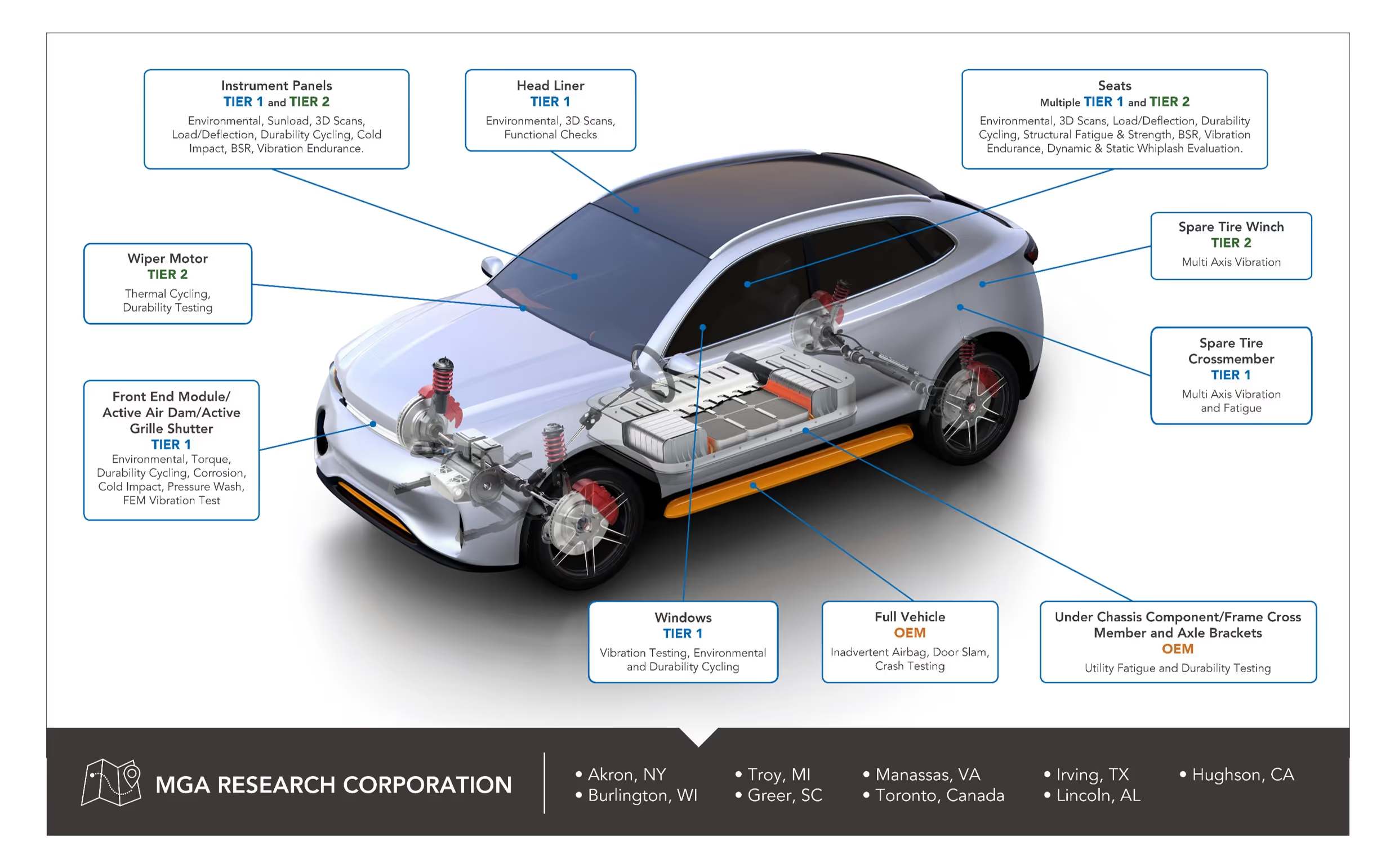
Electric & Alternative Fuel Vehicles
We have extensive experience testing electric (EV), Hybrid (HEV), and fuel cell vehicles, adapting to the ever-evolving automotive market.

Multiple Test Facilities
MGA operates two distinct crash test facilities in the USA with six total crash lanes, offering our customers unmatched test capacity and flexibility.
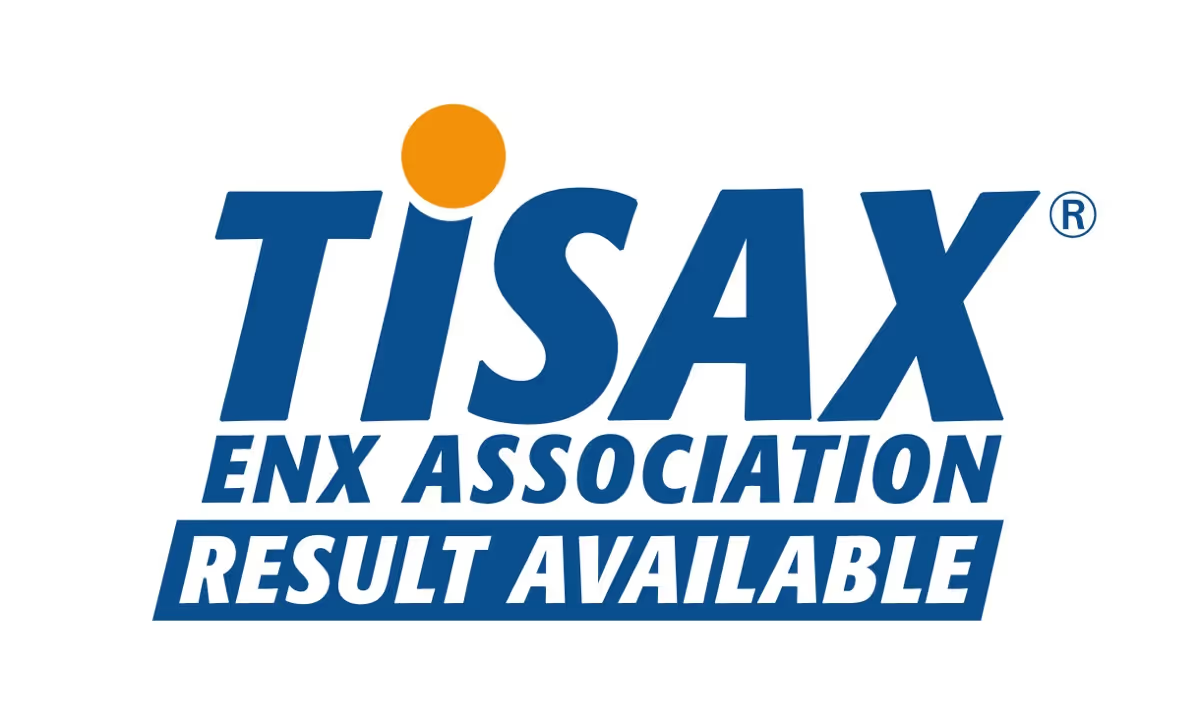
Quality and Security
Our test facilities are ISO 17025 accredited, and MGA Research Corporation is a TISAX participant
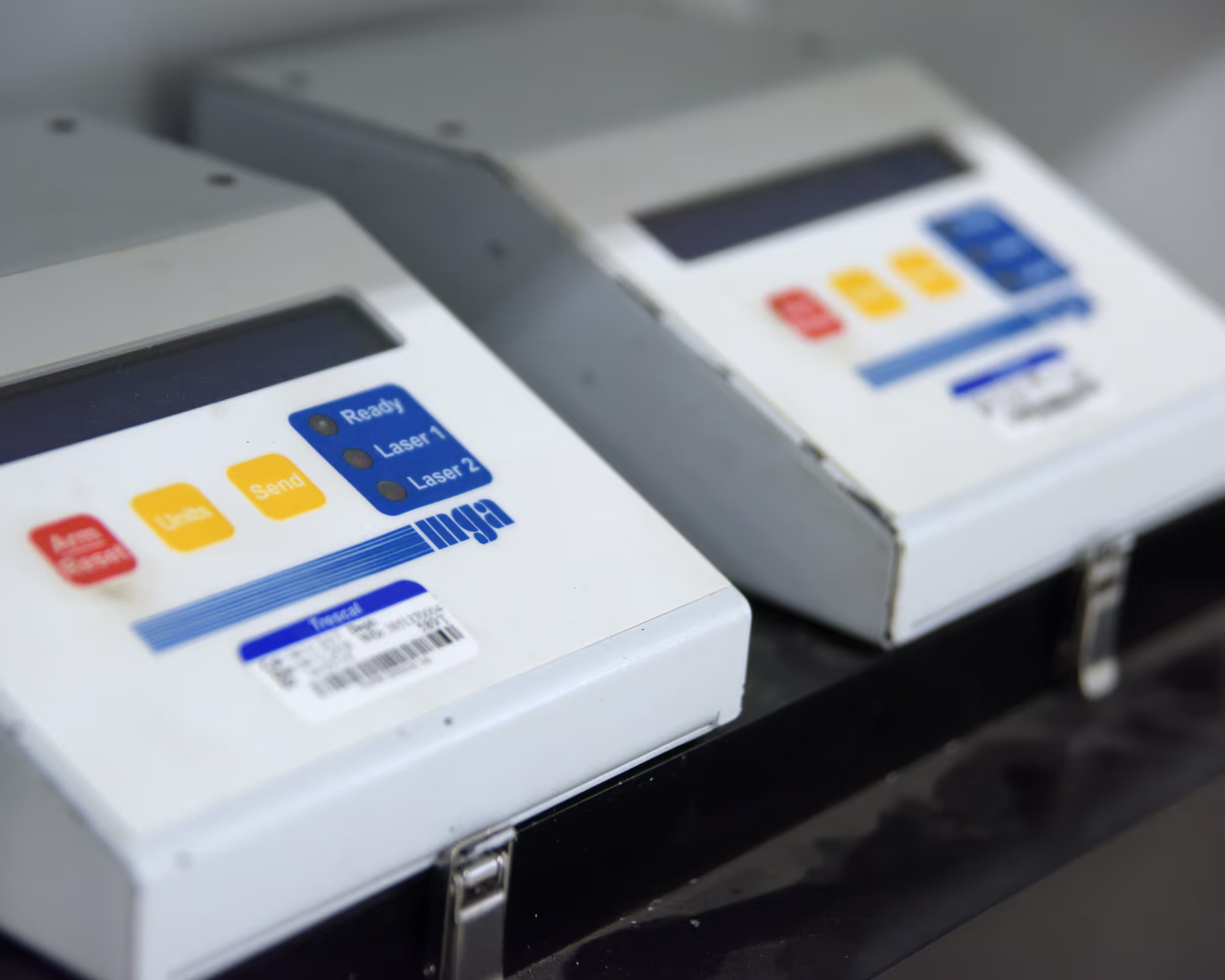
End-to-End Project Support
We work alongside our clients throughout the development process, from early prototypes to final release testing. We even support our international customers through the vehicle import process.
Full vehicle crash testing is the culmination of the automotive industry’s safety development efforts to improve passive safety on roadways around the world. MGA has over 35 years of experience working with customers during all phases of crash development from early CAE physical validations to final homologation, consumer ratings, and everything in between.
MGA has extensive experience working with most of the OEMs from around the World. Our independent and privately-owned crashworthiness operations consist of two physical locations in Wisconsin and Alabama providing unmatched capacity and flexibility. These facilities cover all Regulatory tests (FMVSS), Ratings tests (NCAP, IIHS), and most global protocols. MGA provides full vehicle safety capabilities for vehicle development with companywide ability to conduct FMVSS 100 and 200 level testing. MGA takes pride in working with our customers to develop unique cutting-edge crash modes for research and development purposes.
MGA Advantage:
- 6 total crash lanes between WI and AL (5 Fully enclosed, 1 outdoor for multicar and high-risk impacts)
- 3 frontal barrier sites
- MGA is the only independent test provider in the USA providing complete testing services for Crash, FMVSS 200 Series, FMVSS 100 Series, and Rollover
- FMVSS, IIHS, Most Global Protocols, Development, Benchmarking, Research, and Real-World Scenarios
- Extensive alternative fuel crash experience (electric, hybrid, fuel cell, etc.)
- Secure, confidential test sites with key card access and private conference rooms.
Common Standardized Test Modes Supported
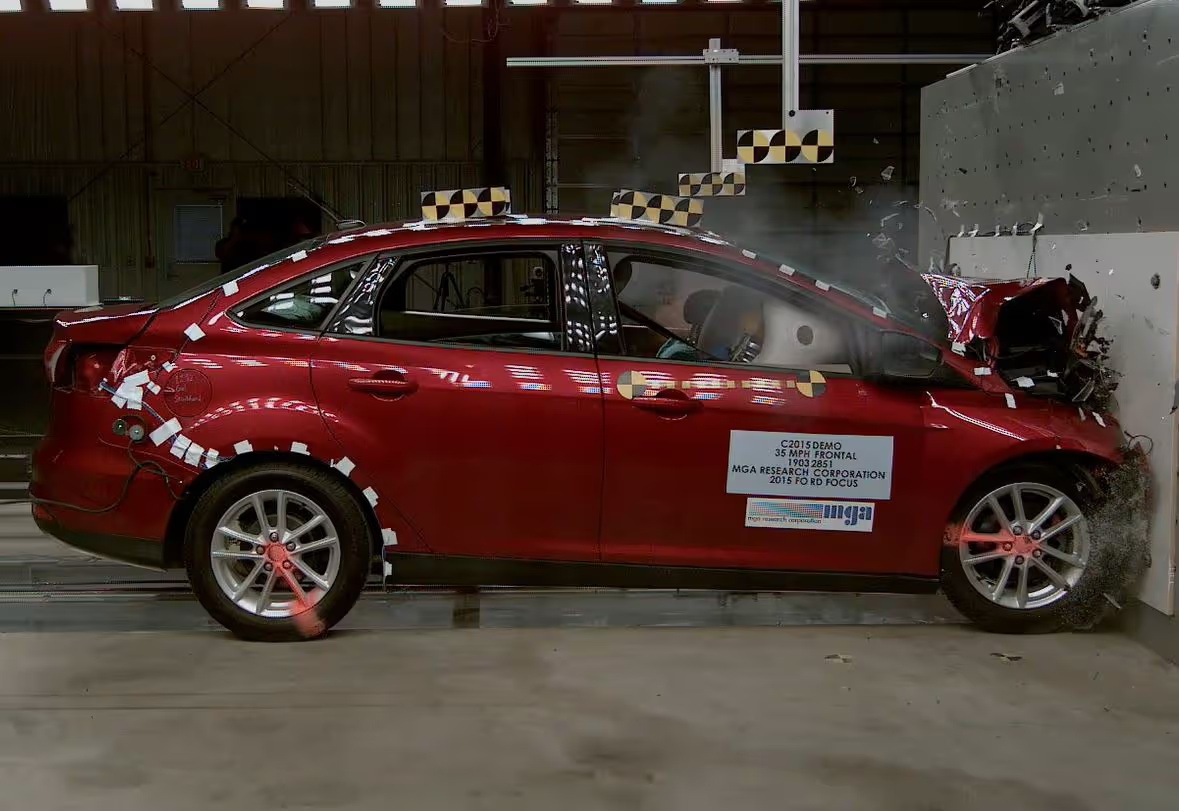
Front Crash
- FMVSS 208, 25mph ODB 40%
- FMVSS 208, 20/25 mph wall 0°
- FMVSS 208, 20/25 mph wall 30° left and right
- FMVSS 208/301, 35 mph wall 0°
- FMVSS 301, 30 mph wall 30° left and right
- US-NCAP, 35 mph wall 0°
- IIHS, 40 mph Small Overlap 25% left and right
- IIHS, 40 mph 40% ODB 2.0 left
- Latin NCAP, 64 km/h 40% ODB
- 27 km/h wall 0° (sensor system)
- 30 km/h underride Type 1 (sensor system)
- 32 km/h 30° left and right (sensor system)
- 35 km/h pole center (sensor system)
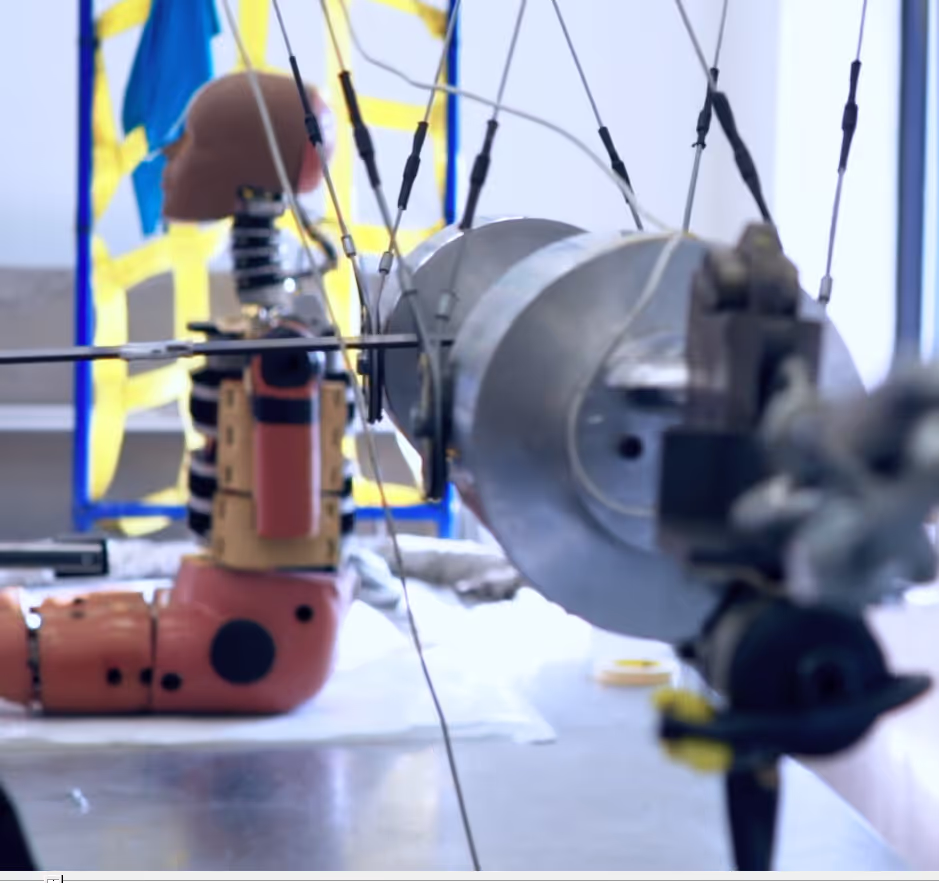
Side Crash
- FMVSS214, 54 km/h MDB
- FMVSS214, 32 km/h pole front
- US-NCAP, 62 km/h MDB
- US-NCAP, 32 km/h pole front
- IIHS 50 km/h MDB (2016)
- IIHS 60 km/h MDB (2022)
- Latin NCAP, 50 km/h MDB
- Latin NCAP, 29 km/h pole
- UN-R95, 50 km/h MDB
- UN-R135, 32 km/h pole
- UN-R95, 30 km/h MDB (sensor system)
Rear impact
- FMVSS 301/305, 50 mph ODB 70% rear end, left and right 1361 kg
- UN-R 34, 53 km/h 100% 1100 kg
Rollover (sensor system)
- Corkscrew ramp
- Curb trip
Front RCAR
- Structure: 15 km/h +1 km/h (10° barrier)
- Bumper: 10 km/h ±0.5 km/h (height 455 mm)
Rear end
- Structure: 15 km/h +1 km/h (trolley against rear end)
- Bumper: 10 km/h ±0.5 km/h (height 405 mm)
Bumper system on trolley
- Front + Rear end: 10-15 km/h (trolley against wall)
MGA builds the majority of our own crash equipment, so we have an unmatched understanding of equipment limits and capabilities. Our experienced team members along with our design and fabrication teams in NY allow us to build just about any situation that can be dreamed up.
Some examples of highly customized testing includes:
- Steering Robot maneuvers (steering, braking, and throttle) before impact
- Multi-Car impacts
- Custom Barrier impacts
- Multi-Impact crash tests (Secondary hit)
- High Speed Pole tests
- Custom Cart Impacts
- Custom Rollover scenarios
- High-Risk Impacts
MGA understands that the development of vehicles, especially in the early phases, is challenging and things don’t always go as planned. We pride ourselves in working with our customers to truly understand each of their unique needs and tailor our services to provide a seamless experience.
This includes:
- Deliverable format options ranging from industry standard ISO/MME to highly customized formats to match your internal data management systems
- Unmatched capacity by leveraging our multiple Vehicle Safety facilities
- Flexible scheduling
- Technical review by a project management team with many years of combined experience.
- Your project engineer will follow your testing from initial request to final deliverable review
Full vehicle safety capabilities, beyond just crash.
Facilities
The Wisconsin operations, established in 1988, is a 400-acre proving grounds with a Vehicle Safety Center consisting of three indoor crash lanes (two frontal barrier sites), two accelerator sleds, as well as a 4th outdoor crash lane for multi-car and high-risk impacts.
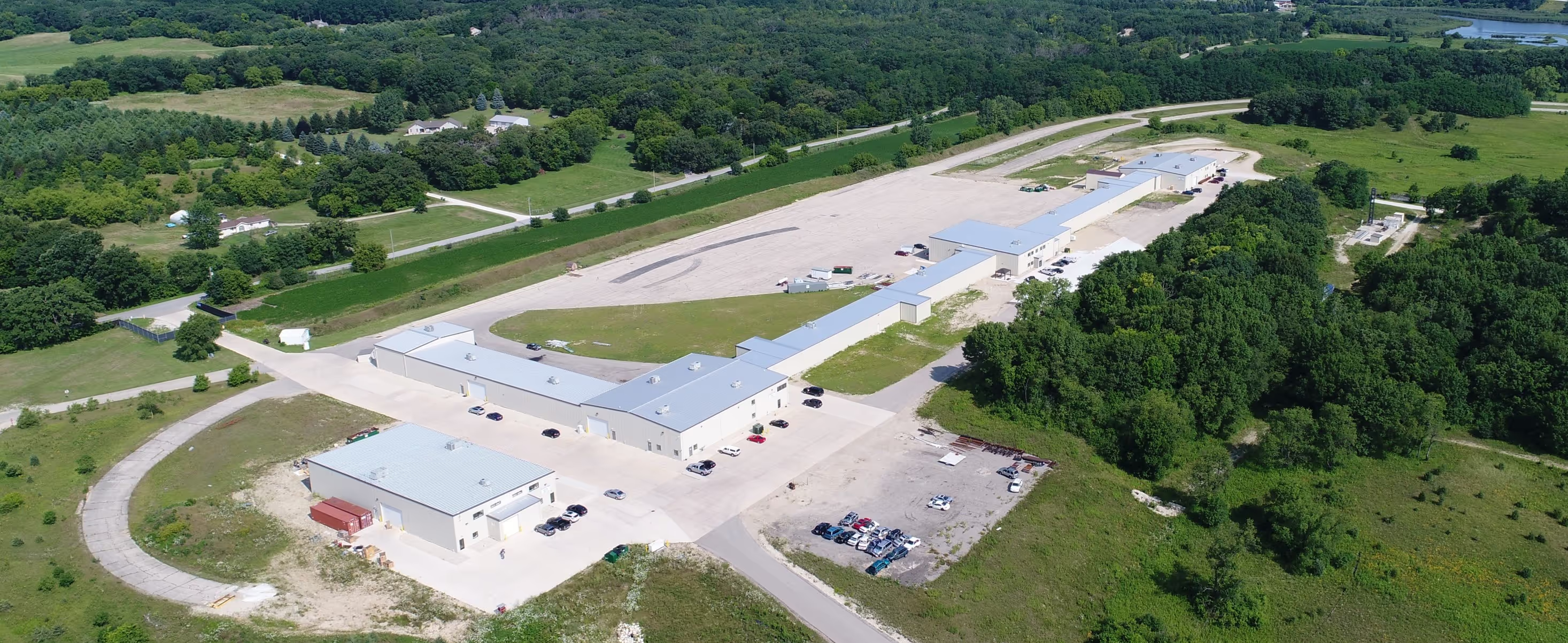
The Alabama test facility was established more recently in 2014, with two separate crash halls connected by a single track. This facility has over 75,000 square feet of testing area and room to expand in order to support our global customer base in the area and is strategically located in the middle of automotive manufacturing activities in the Southeastern United States. The facility has a modular design, allowing the crash facility to be completely isolated from the component safety and durability lab. It is the first facility of its kind in the southeast to combine component level durability, safety, and full vehicle crash testing in one location.
.avif)
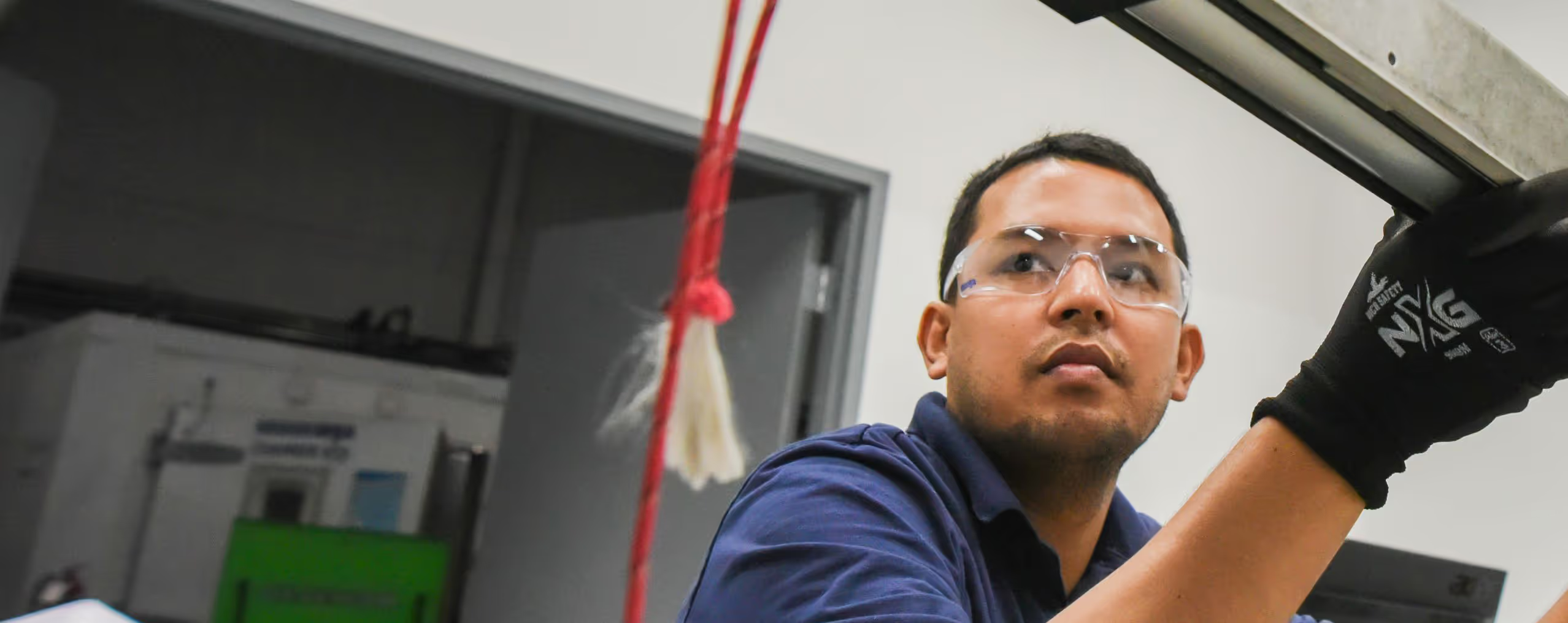
Ready to Get Started?
Let's discuss your testing needs and how MGA can help. Our team is ready to provide the expertise and solutions you're looking for.