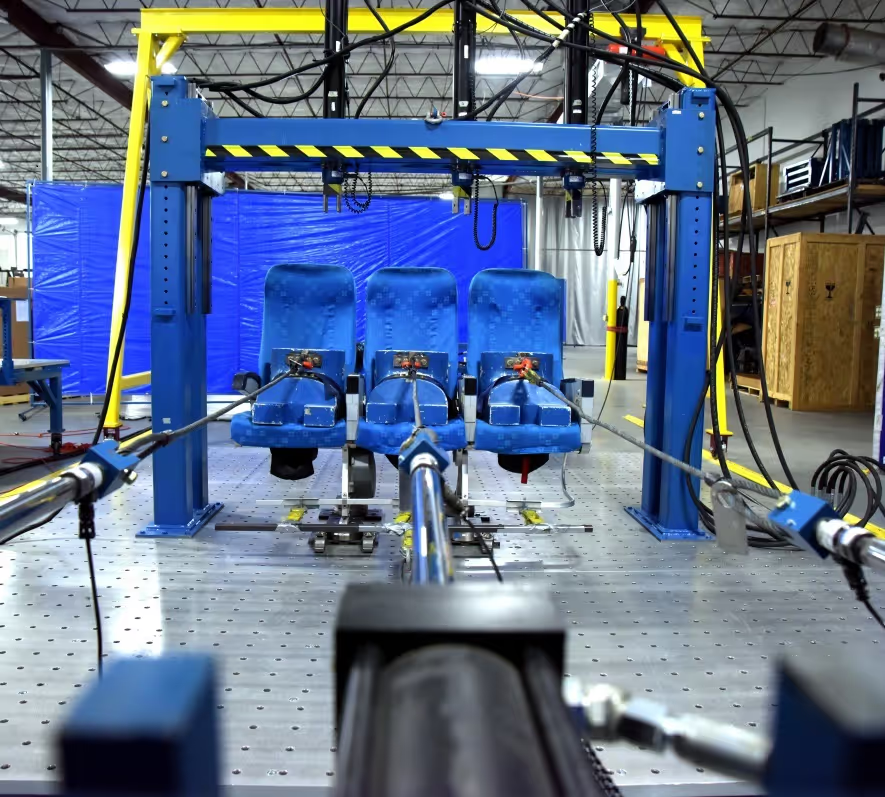
Aircraft Testing
MGA Research provides cutting-edge testing services for the aerospace industry, leveraging decades of experience and state-of-the-art facilities to support safety, durability, and performance evaluations for aircraft components and systems.
Quick Overview
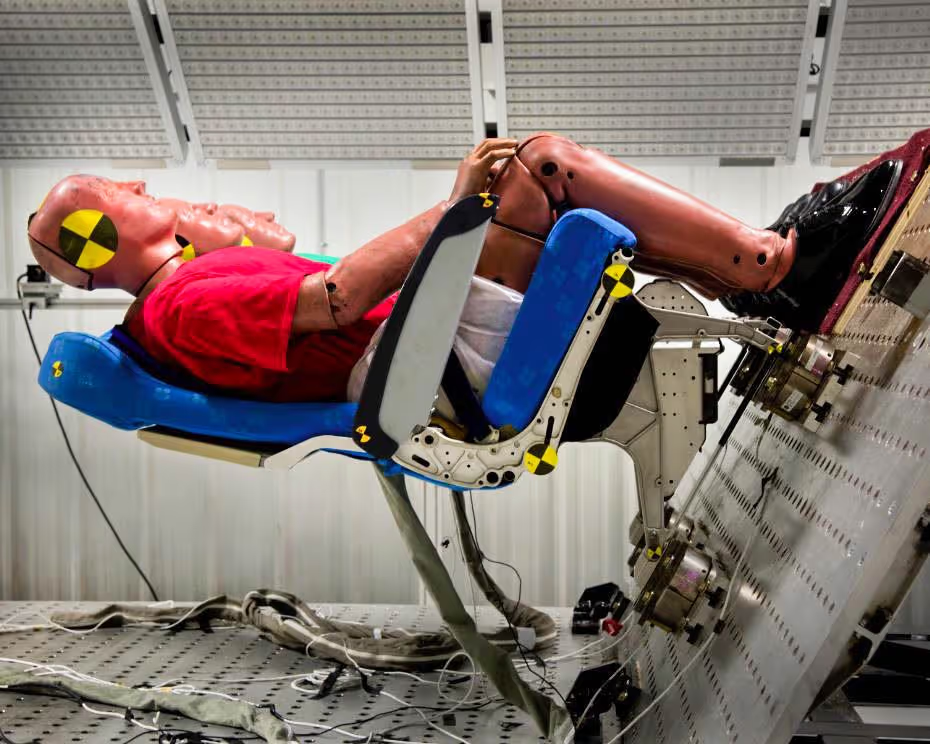
Comprehensive Aerospace Testing Services
We offer extensive testing capabilities for aircraft components and systems across nine specialized laboratories, supporting safety, durability, and performance evaluations.
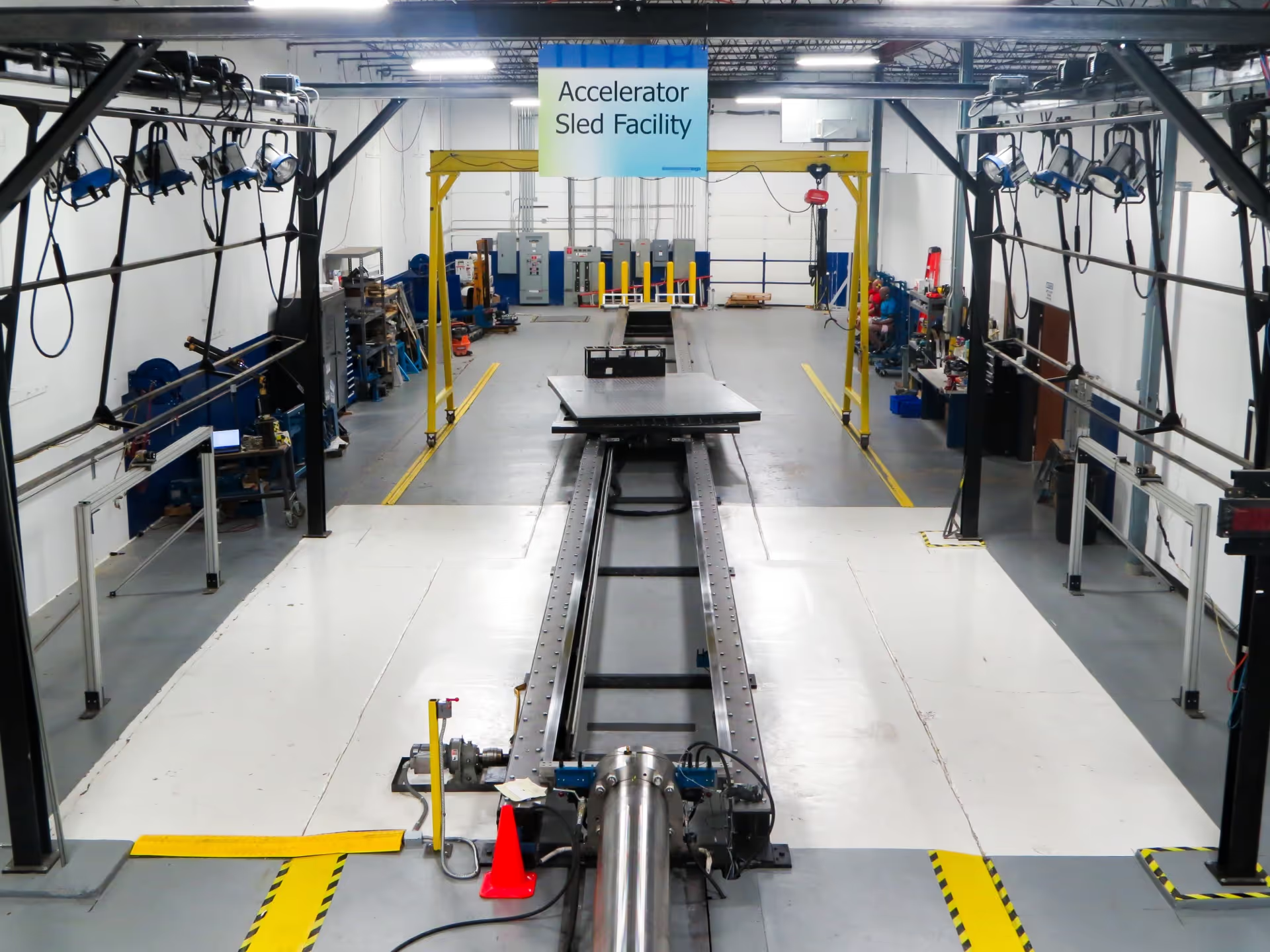
Advanced Dynamic Sled Testing
We provide FAA-compliant dynamic sled testing for Parts 23, 25, 27, and 29, utilizing over 12 accelerator sled facilities and 100+ Anthropomorphic Test Devices (ATDs).
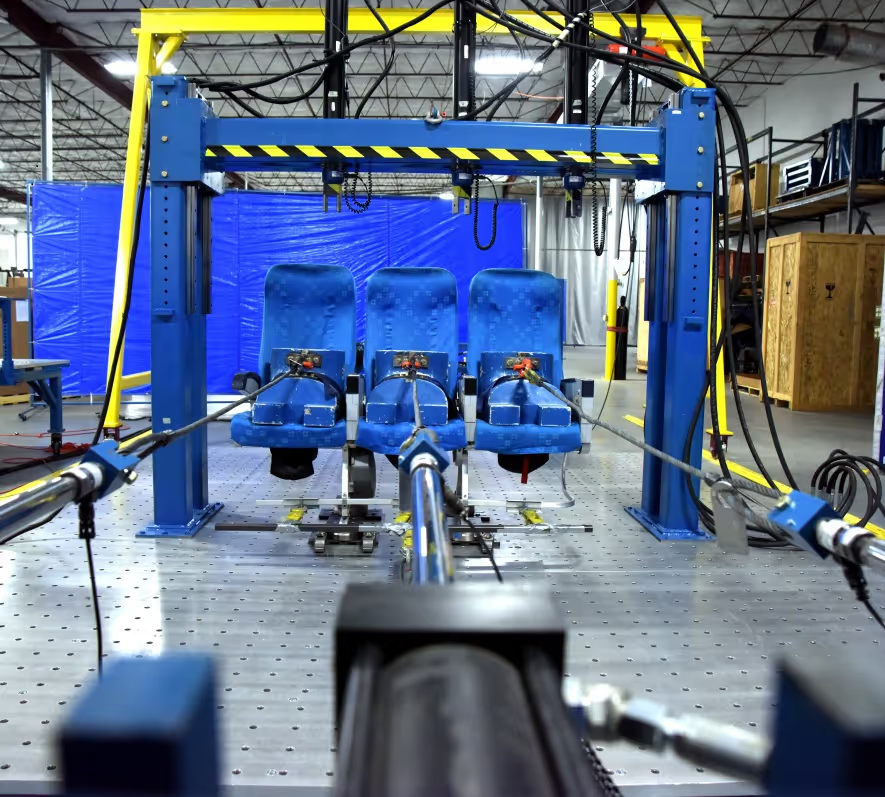
Specialized Static and Quasi-Static Testing
We conduct static and quasi-static testing for aircraft seats and furniture, including rapid decompression testing, using our large-scale adjustable test frames.
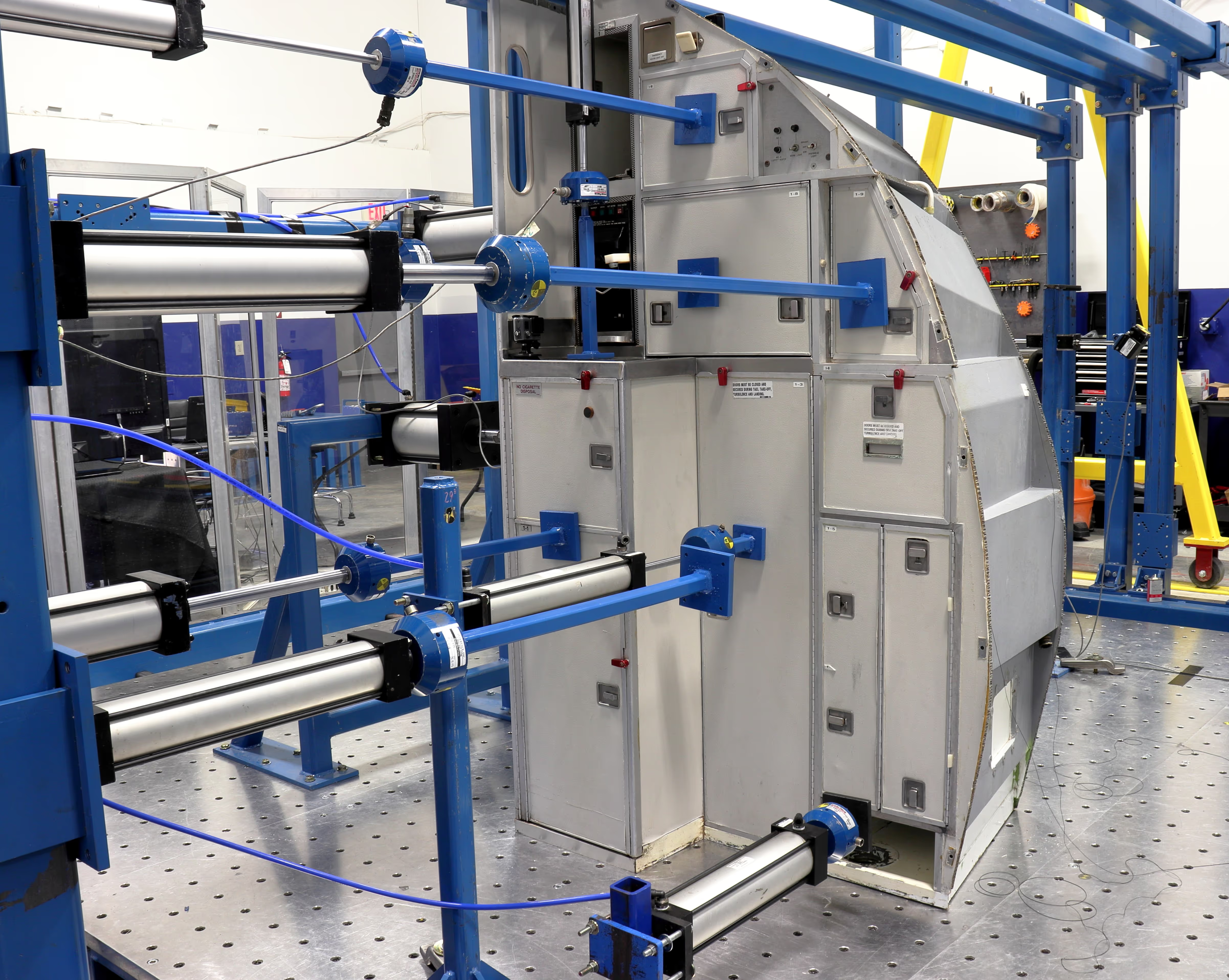
Durability and Life-Cycle Evaluation
We perform comprehensive durability testing, including life-cycle testing for seat components, furniture closures, and specialized tests like Squirmin Herman and ingress/egress simulations.
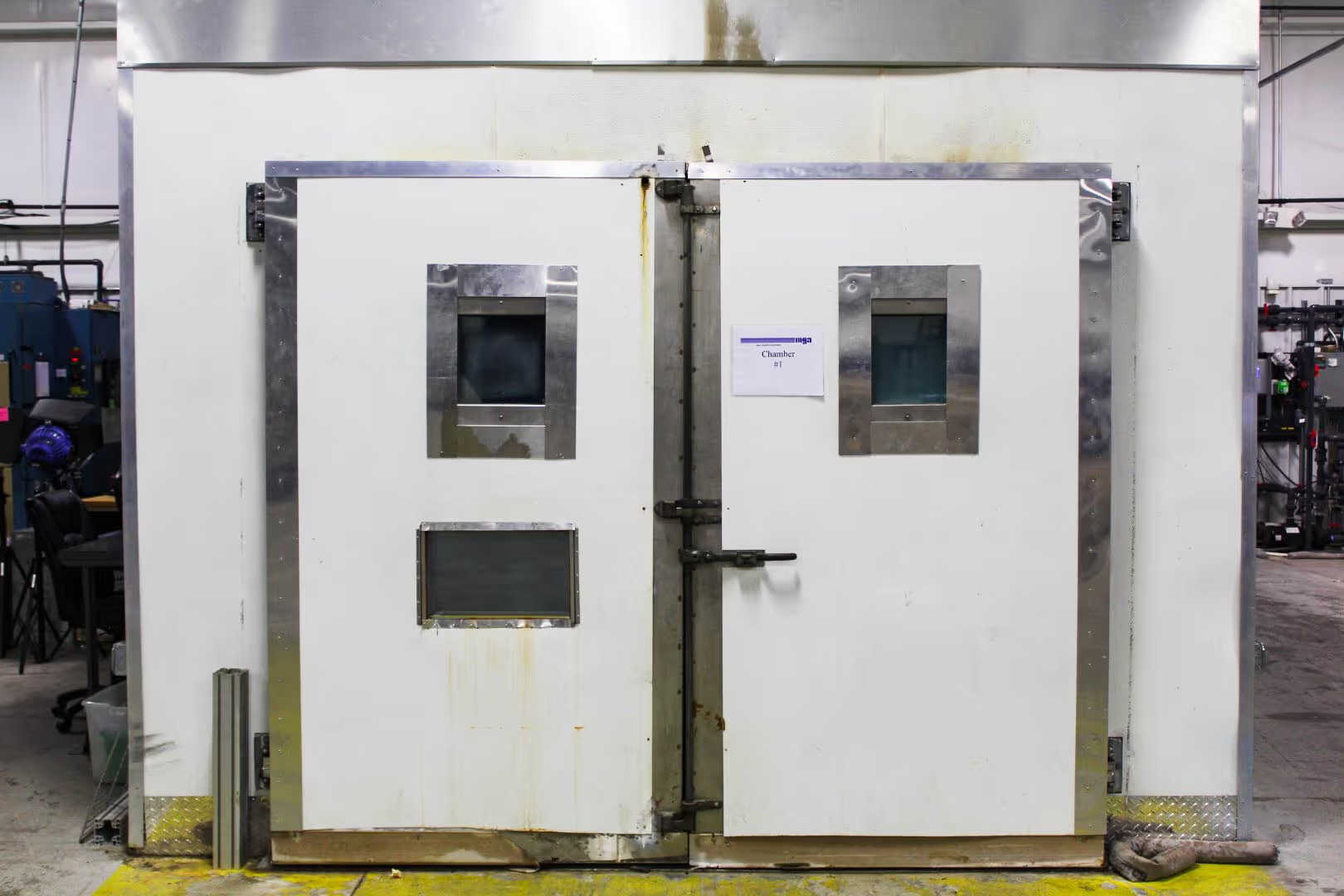
Environmental and Vibration Testing
We offer DO-160 compliant environmental and vibration testing, covering a wide range of conditions and procedures for airborne equipment.
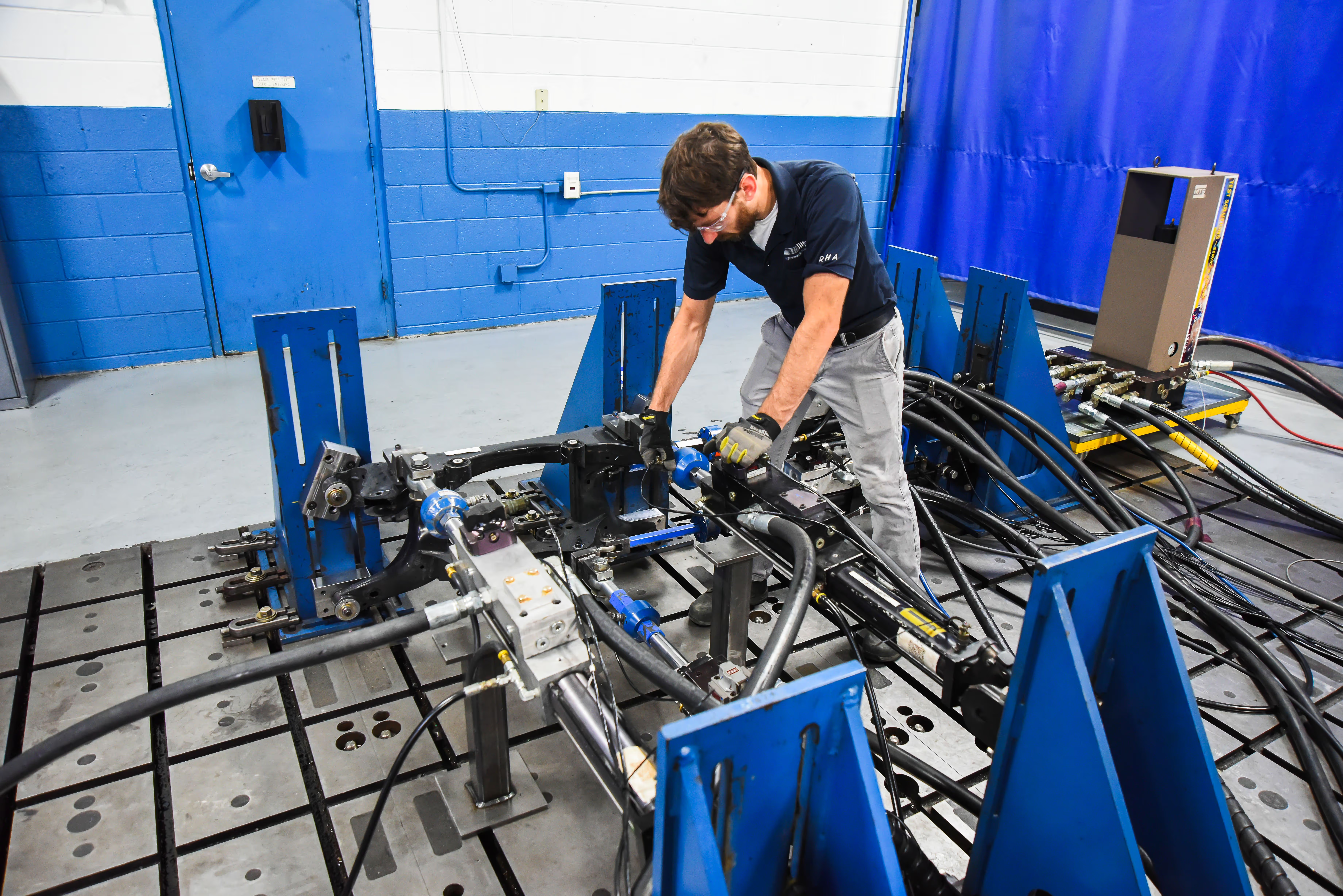
Hydraulic Durability Expertise
We provide advanced hydraulic durability testing, including AeroPro capabilities, for various aircraft structures such as landing gears, nacelles, and rotorcraft engines.
Aerospace design has always been on the forefront of the cutting edge. Amid this constantly evolving environment, where engineers are combining aircrafts and rotorcrafts to develop what is now known as electric Vertical Take-Off and Landing aircrafts (eVTOL), MGA has been a constant asset for those looking to receive the highest quality of testing services. We combine an experienced staff of experts with first class facilities to meet the needs of a diverse set of Aerospace companies.
Engaging at the forefront of new regulatory changes as well as their implementation, we have a long history of engaging with the industry to better understand the new challenges that come with innovations. This approach has allowed us to provide simple solutions to complex problems. Whether it be the development of new testing methodologies or tackling data collections for hundreds of sensors, our experienced teams and extensive resources provide our customers with an unparalleled advantage.
MGA Advantage
With a network of 9 laboratories and an experience covering coupon level to partial fuselage samples, MGA provides the following advantages to its customers:
- Over 12 accelerator sled facilities nationwide, including a proving ground
- Over 100 ATDs nationwide including FAA Hybrid III 50TH, ES2-re, and THOR-M
- Large inventory of auxiliary data collection (load, displacement, strain, and acceleration)
- Ability to maintain aggressive schedules through our network of laboratories
- Ability to develop customized testing methodologies
- Laboratories capabilities ranging from component level testing to proving grounds
- Over 100 chambers available company wide
- Experienced personnel supporting safety, environmental, durability, and materials testing
- Unmatched root cause analysis capabilities.
Safety
Towards the end of the 20th century, governmental organizations started to take a serious look at the survivability rates of aircraft crashes and how to improve those odds. After extensive crash scene investigations, and with the assistance of the industry, new standards were introduced to provide guidelines on design, manufacturing, and installation of aircraft components. In the testing world, these standards outlined the maximum forces experienced by aircraft and its component during a crash, thus paving the way to new minimum performance requirements.
FAA Dynamic Sled Testing facilities – Part 23, 25, 27, and 29 Dynamic Testing Capable
Since the introduction of aircraft dynamic testing utilizing high speed reel cameras, MGA has supported the advancement of occupant safety in aircraft with a wide range of testing capabilities. Depending on the vehicle (aircraft or rotorcraft), components that need dynamic qualification must meet three (3) different criterias.
A vertical structural & lumbar evaluation test (60 degrees from horizontal, or 30 degrees from vertical), for emergency landing conditions with velocity, rise time, and acceleration parameters varying depending on the type of aircrafts. A Lumbar load evaluation is required to determine the safety of the occupants and their ability to walk out of the aircraft.
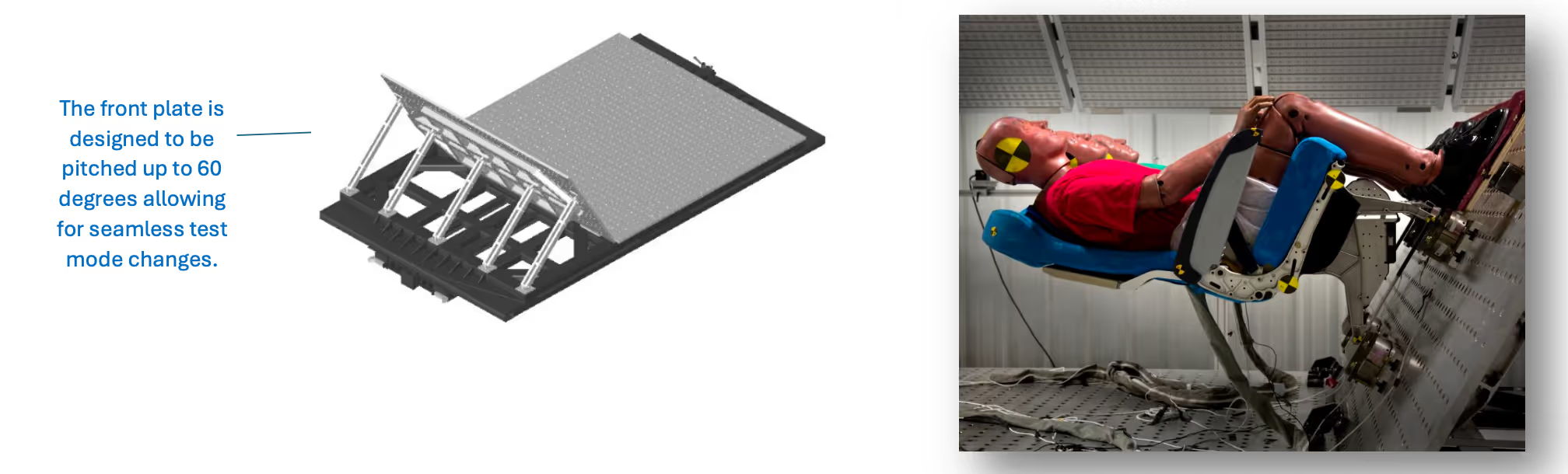
A horizontal structural test for emergency landing conditions to ensure the integrety of all load bearing components of the seats, as well as a horizontal injury criteria to determine Head Injury Criteria (HIC), Neck Injury criteria (NIJ) and any obstructions to the egress path. Though velocity, rise time, and acceleration parameters are similar for these injury evaluations, there is still some variance depending on the type of aircrafts (see table 1). The injury criteria determine any chances of blunt force trauma, or neck injury that could prevent the occupants from exiting the aircraft.
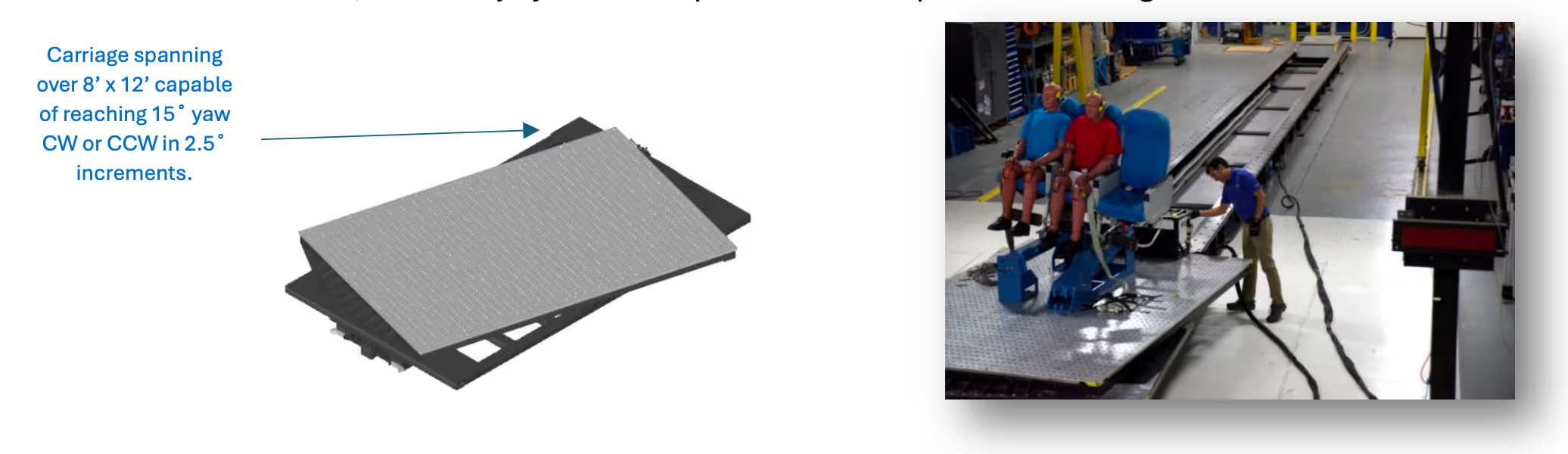
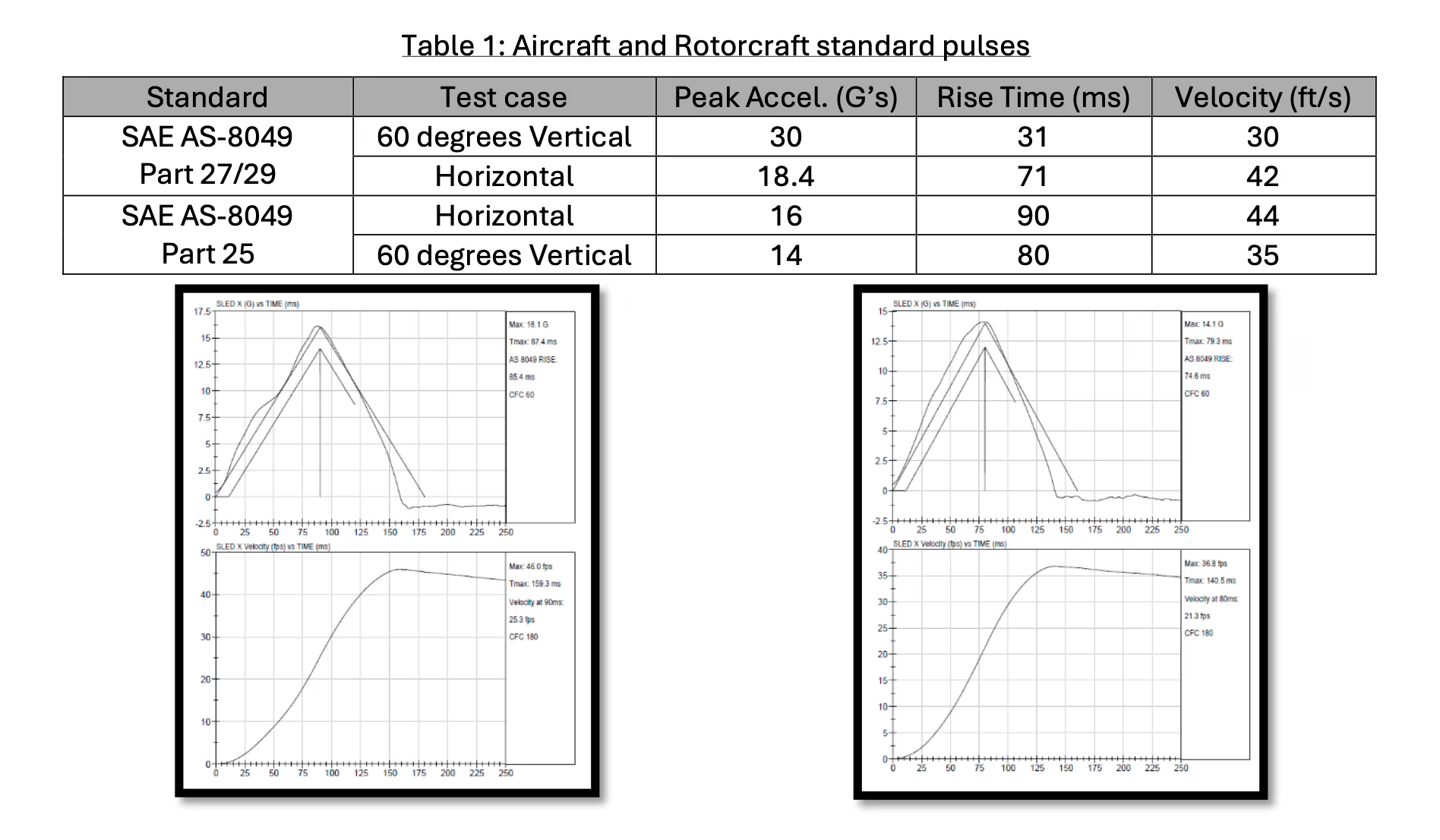
With over three decades of dynamic testing experience in the aircraft industry, we’ve developed a strong technical knowledge allowing us to support commodities such as seats, bulkheads, furniture installations, as well as fuselage sections (limited to eVTOL and acrobatic planes) with a 2000 fps videographic documentation, and state of the art photometric analysis.
Our auxiliary channel capabilities include over 100 channels of data collections for 3 axis interface floor loads, 6 axis interface floor loads and moments, high acceleration rated string potentiometers, sample mounted accelerometers, and strain gages.
Delethalization – Free Motion Head-form, Inverted pendulum, and linear impactor capable)
Delethalization testing has many benefits as it allows for component level testing to improve HIC scores observed in dynamic sled testing, egress path evaluations through sharp edge evaluations & obstructions caused by seat back components (I.e., tray tables). With the ability to conduct comparison studies between different design iterations, seat and monitor suppliers have the potential to improve energy absorption properties and component retention prior to further dynamic trials on full assemblies.
Recent efforts from the industry to push for monitor replacement qualifications (as seen in retrofits), could lead to a path for component level qualifications being established with dynamic sled HIC testing only required for new assembly certification. Our three-axis test frame and dynamic impactors offer a high level of efficiency with set-up changes at the push of a button. With a seamless integration of three different impactors, for Part 25.785 (b) & (d) certification testing, each one can attain speeds of up to 45 fps. Through our collaboration with industry, we have contributed to the development of multiple innovative testing methodologies such as the inverted pendulum impactor. Commodities supported include monitors, seat backs, and foam for energy absorption tests, among other aircraft components. MGA also offers 3- and 4-point bend testing on monitors for stiffness evaluations.
Quasi-Static on both seats and furniture – static rapid decompression capable
Prior to the introduction of dynamic qualifications, static testing was the standard of performance evaluation for aircraft cabin components. With a longer testing duration (in comparison to an average of 300ms dynamic sled test), static testing allows for real time observations of how loads propagate through seat component and transfer to the fittings. Static test modes, as defined in A.S. 8049, are done in five (5) different directions (up, down, forward, aft, and side). Though there are some instances of combined loading (2 or more directions required for a resultant force application), these tests tend to be rare.
Seat static testing
Our large frame design allows us to properly secure components with machined aluminum plates spanning over a 12’ x 15’ Footprint and an ability to conduct four test modes with only one set-up (Up, Down, Forward, and Aft loading). MGA’s aircraft seat static frame is also equipped with Ten (10) hydraulic cylinders with capability of up to 10,000 lbf of load application per cylinder, and a servo hydraulic control system allowing precise load profiles and holds. Our auxiliary channel capabilities include 3 axis interface floor loads, 6 axis interface floor loads and moments, string-potentiometers, displacement laser sensors, and strain gages.
Furniture static testing
It is important to note that not all interior components need to be qualified through dynamic testing. In the case of aircraft furniture, the decisive factor for airworthiness still depends on static qualifications. Commodities falling in that category include suites, galleys (all sorts), lavatories, ottomans, bulkheads, and custom furniture requiring airworthiness (i.e., medical beds, conference tables, etc.). With similar test-modes to seats (up, down, forward, aft, and side), furniture testing can prove to be more complex due to the size and nature of the test samples. Performance evaluations go beyond structural integrity. In a galley, for example, it is critical to ensure that moveable components such as trolleys, coffee pots, or toaster ovens are secured in place to avoid further injuries to cabin occupants.
In furniture static testing, combined loading tends to be more frequent and would usually involve Z & X axis, or Z & Y axis. Some less frequent combined load applications are static Rapid Decompression (RD) testing which is often done via simulations using validated models. A Rapid decompression event is defined as a rapid change of cabin pressure which is often the result of a structural failure or breach in the fuselage. During these events, Interior components (such as galleys), connected to that section of the fuselage are expected to contain this immense pressure differential for passenger safety. Replicating this event in a static environment consists of load application in the normal plane of each panel. These loads are derived from the pressure difference between each side of the panels. RD tests require an extensive level of fixturing & set-up, and could be considered the ultimate combined load testing.
MGA’s test rig comprises of two separate frames each having a footprint of 15’ X 12’ X 12’. This fully adjustable system allows for vertical and horizontal beams adjustments for custom set-ups. With the ability to combine both frames into one 30’ X 12’ X 12’, our team can support static tests on multiple suites in-line for load-sharing, as well as custom AFT galley rapid decompression. Load applications are done via the use of pneumatic actuators, hydraulic actuators, dead mass, or any combination necessary. The large frame and bed plates are placed upon a strong floor yielding to a total bedplate stiffness greater than 100,000 Psi (Boeing and Airbus compliant).
Durability
Net zero emission goals have been a driving factor to develop interiors and seats structures that are rated to a higher level of use and abuse, thus extending the lifetime of the structure. By doing so, airlines can minimize the need for cabin upgrades due to wear and tear. Combined with modular designs, durability testing can contribute to the use of less natural resources and manufacturing, which yields to a decrease in each aircraft’s environmental footprint.
Life-cycle testing – seat components, and furniture closure capable
Utilizing our fully adjustable aircraft furniture structural test system, MGA is capable of actuating different seat components such as recline, seat swivel, front row tray tables, front entertainment systems, headrest adjustments, galley doors, trolleys’ stowing, and many more. With robots, pneumatic actuators, and power controllers, our staff can reproduce any motion with a high level of repeatability and speed control.
Seat durability – Ingress Egress & Squirmin Herman capable
Traditionally required in the automotive industry, seat durability testing has caught the attention of the aircraft industry in recent years. Like the automotive industry, it all starts with a pressure mapping study which leads to path creation on a robot. This path will replicate the most aggressive profile collected and run for the expected life of the seat. Pre/Post test photos (subjective), as well as 3D scans overlays (objective) are provided to show any wear and tear observed.
Another approach to testing the durability of the seat is the famous Squirmin Herman test methodology developed by the Boeing Company (BSS-7302). This methodology is also supported by our team with possibilities of adjusting all parameters (weight, yaw angle, roll angle, and cycle rate).
DO160 – Environmental and vibration
The aerospace industry is constantly evolving as innovative technologies and mission plans are developed for governments, and the private sector. As the momentum for these projects increases, it is vital for these organizations to intensify the testing of these technologies for a better understanding of the data and behavior of their products. The Radio Technical Commission for Aeronautics (RTCA) has published DO-160, which covers environmental conditions and test procedures for airborne equipment. MGA, in the pursuit of servicing the testing needs of the automotive and aerospace industries, can provide support to the following sections:
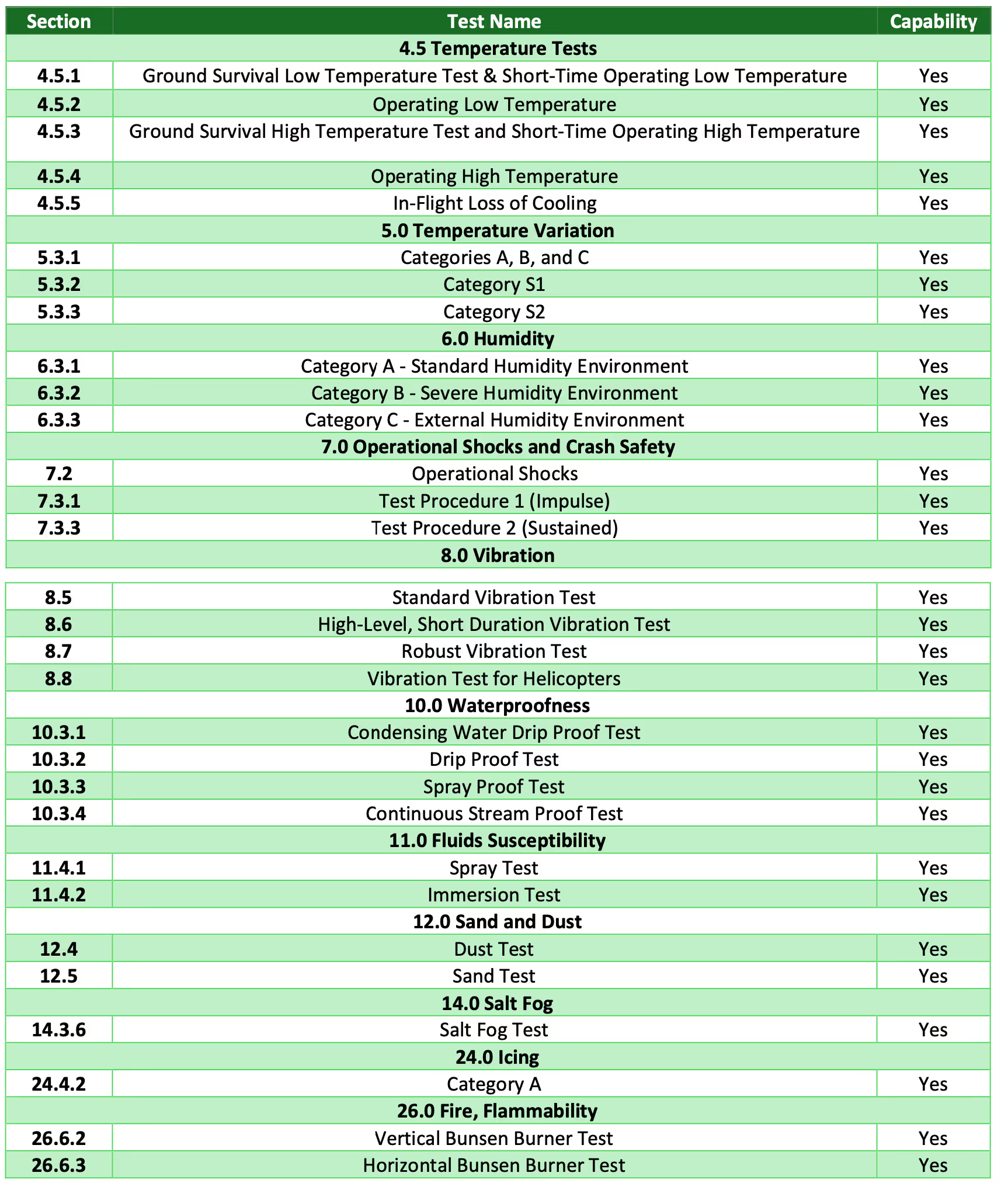
Hydraulic Durability – AeroPro capable
As one of our core competencies, Hydraulic Durability (HD) testing involves applying a certain load of displacement to components, subassemblies, or full assemblies, at a higher frequency than usual. At an average frequency of 3 Hz (±2Hz), hydraulic actuators are programmed to accurately follow a profile in tension and compression at specific location of key components for the predicted lifetime of the vehicle. Through this testing campaign, OEMs and suppliers can ensure the structural integrity as well as reliability of their components thus verifying proper operational capacities. Through our efforts to support the aircraft industry, HD testing has been conducted for a decade on landing gears. In recent years, we have developed further capabilities to offer such services to different structures such as nacelles, cargo doors & hinges, latches, as well as rotorcraft engines (eVTOL supported) as of 2024. Recent addition allows our teams to simulate in-plane forces, moments, and thrust on rotorcraft structural components to ensure structural integrity throughout its operational life. MGA operates a multitude of controllers and software provided by MTS (including Aero-pro).
Hydraulic durability support can be done with multiple actuators operating in parallel, at ambient or extreme temperatures, with the ability to collect auxiliary channels (i.e., strain gages, interface loads, surface temperature, and displacement).
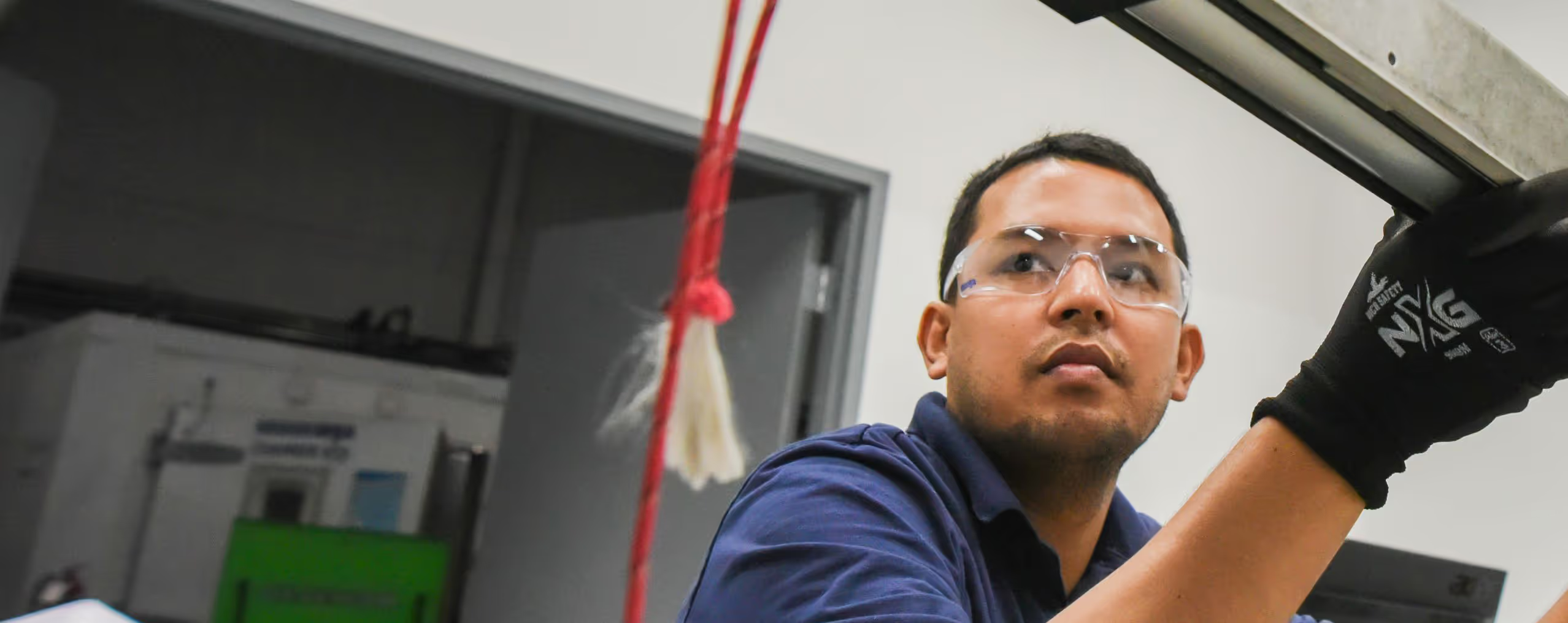
Ready to Get Started?
Let's discuss your testing needs and how MGA can help. Our team is ready to provide the expertise and solutions you're looking for.