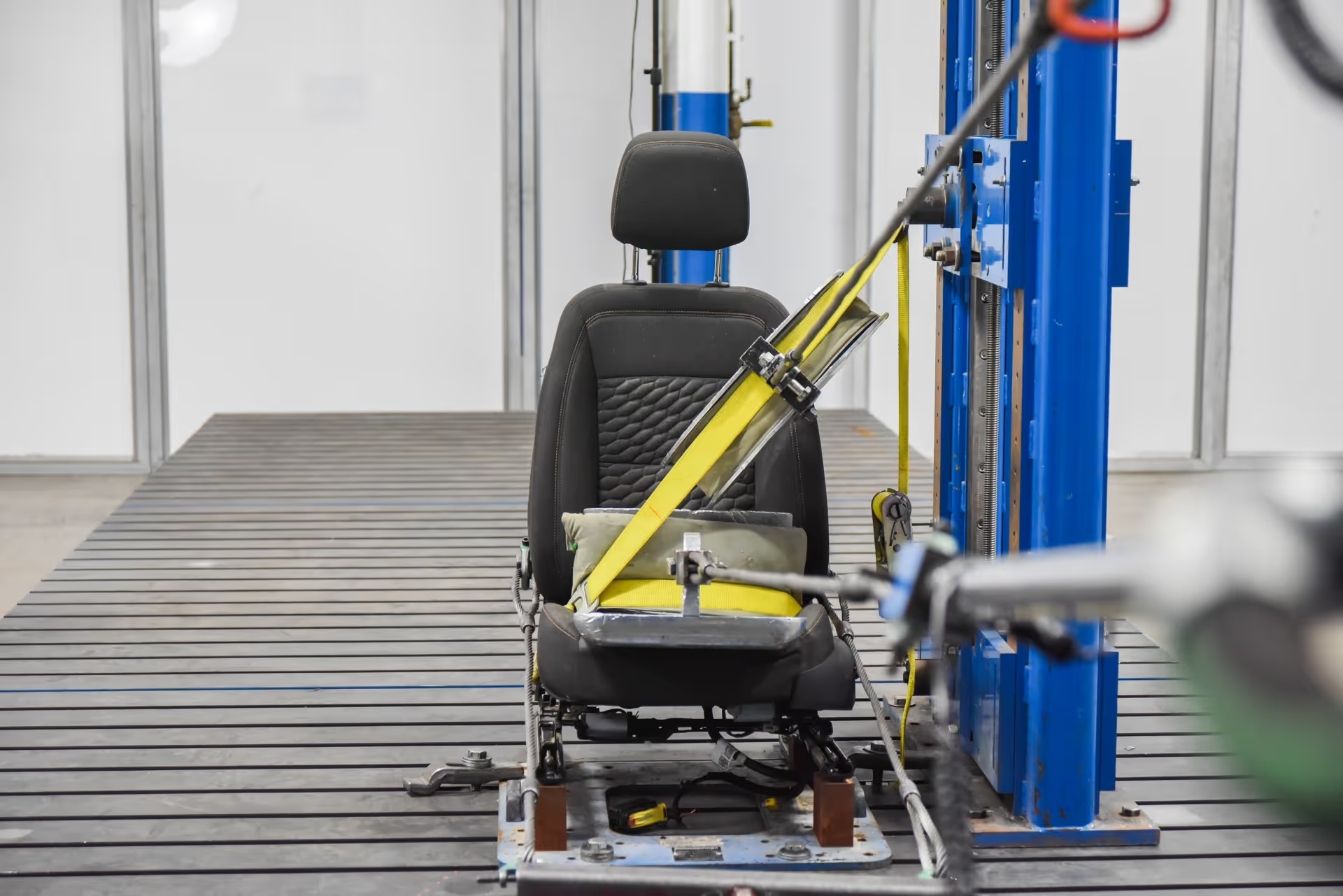
Automotive Seating Testing
MGA Research Corporation offers comprehensive automotive seating testing services, leveraging decades of experience and cutting-edge technology to ensure the quality, durability, and safety of automotive seating systems.
Quick Overview
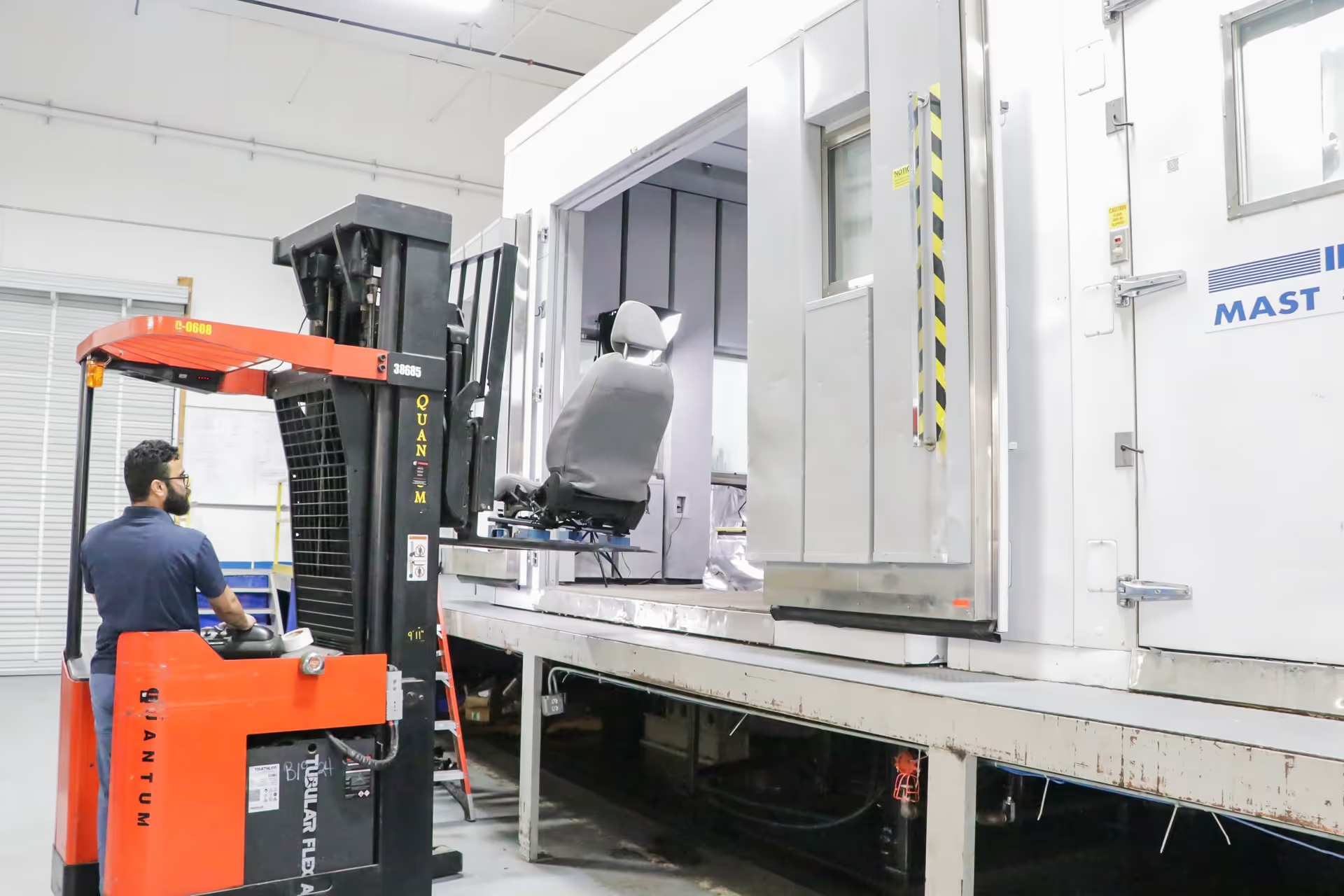
Comprehensive Seating Test Expertise
We offer a full suite of automotive seating system test services, covering all aspects of function validation, durability, quality, and safety.
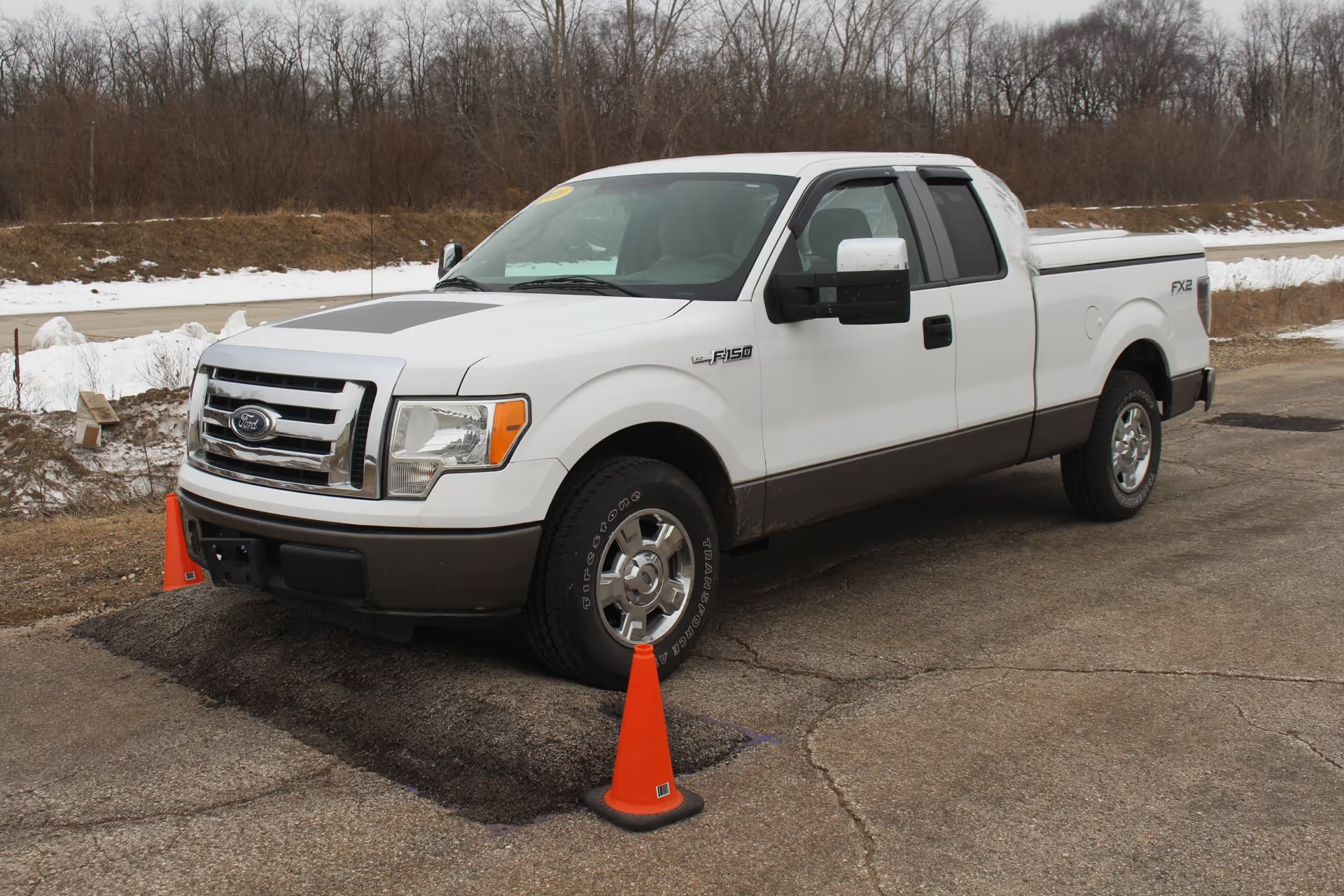
Extensive OEM Experience
MGA is experienced with test standards from all OEMs including Ford, GM, Stellantis, VW, Mercedes, BMW, Volvo, and more.
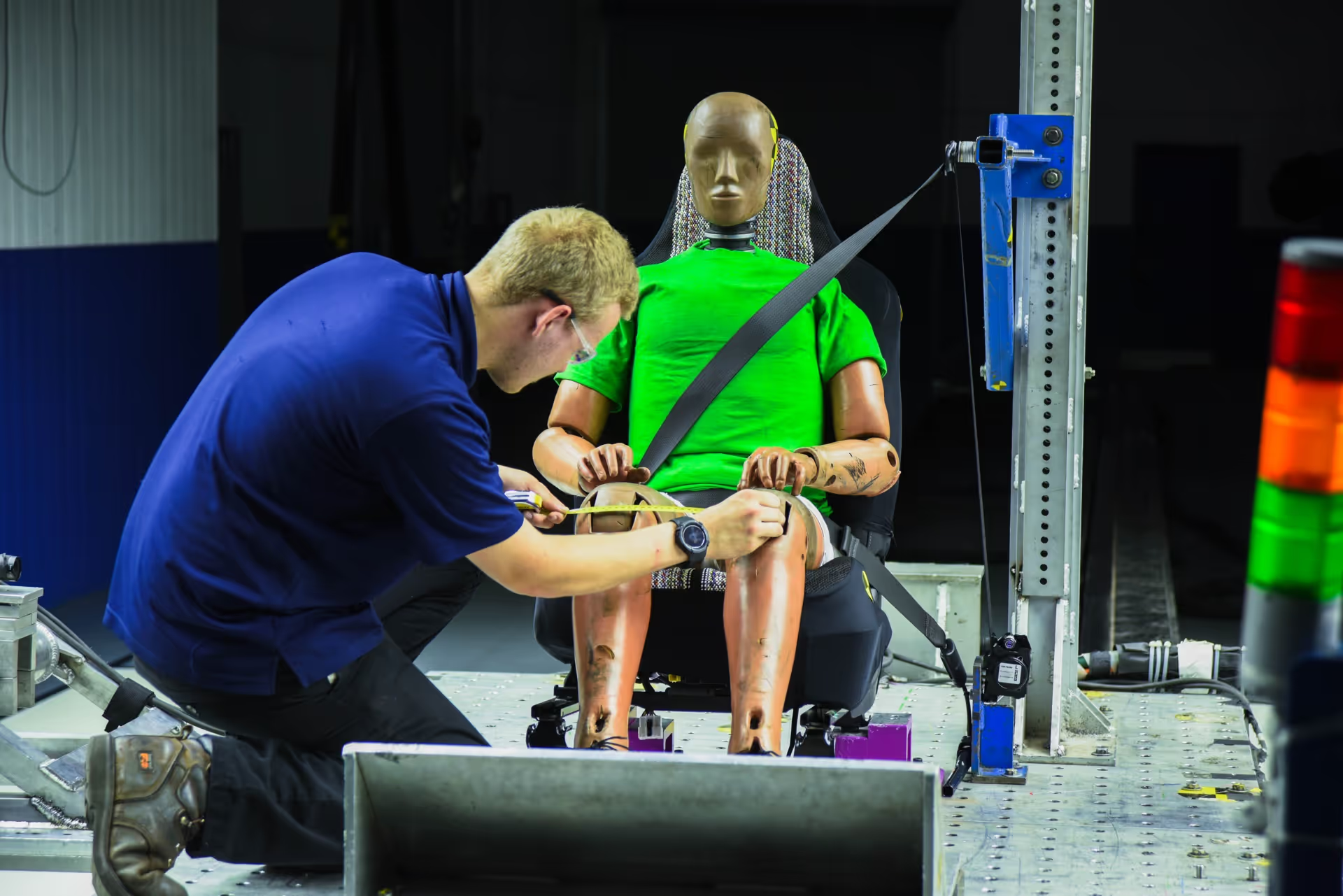
Complete Safety Testing
We perform a wide array of safety tests to both consumer and regulatory requirements, including dynamic sled testing, airbag deployment, and quasi-static testing.
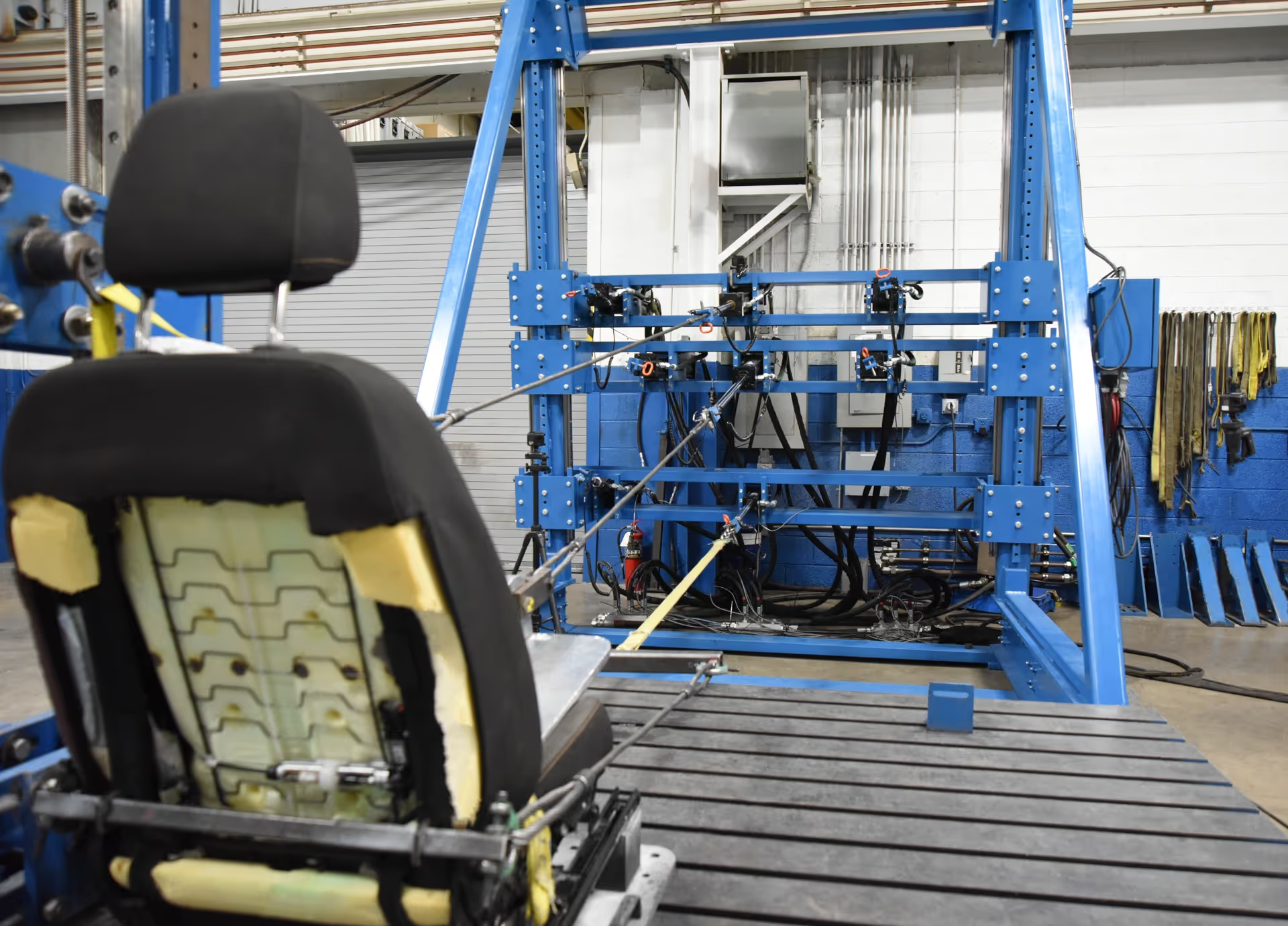
Advanced Technology and Equipment
We utilize cutting-edge technology and equipment, much of which has been developed by MGA, to deliver efficient, accurate, and consistent results across various OEM specifications and regulations.
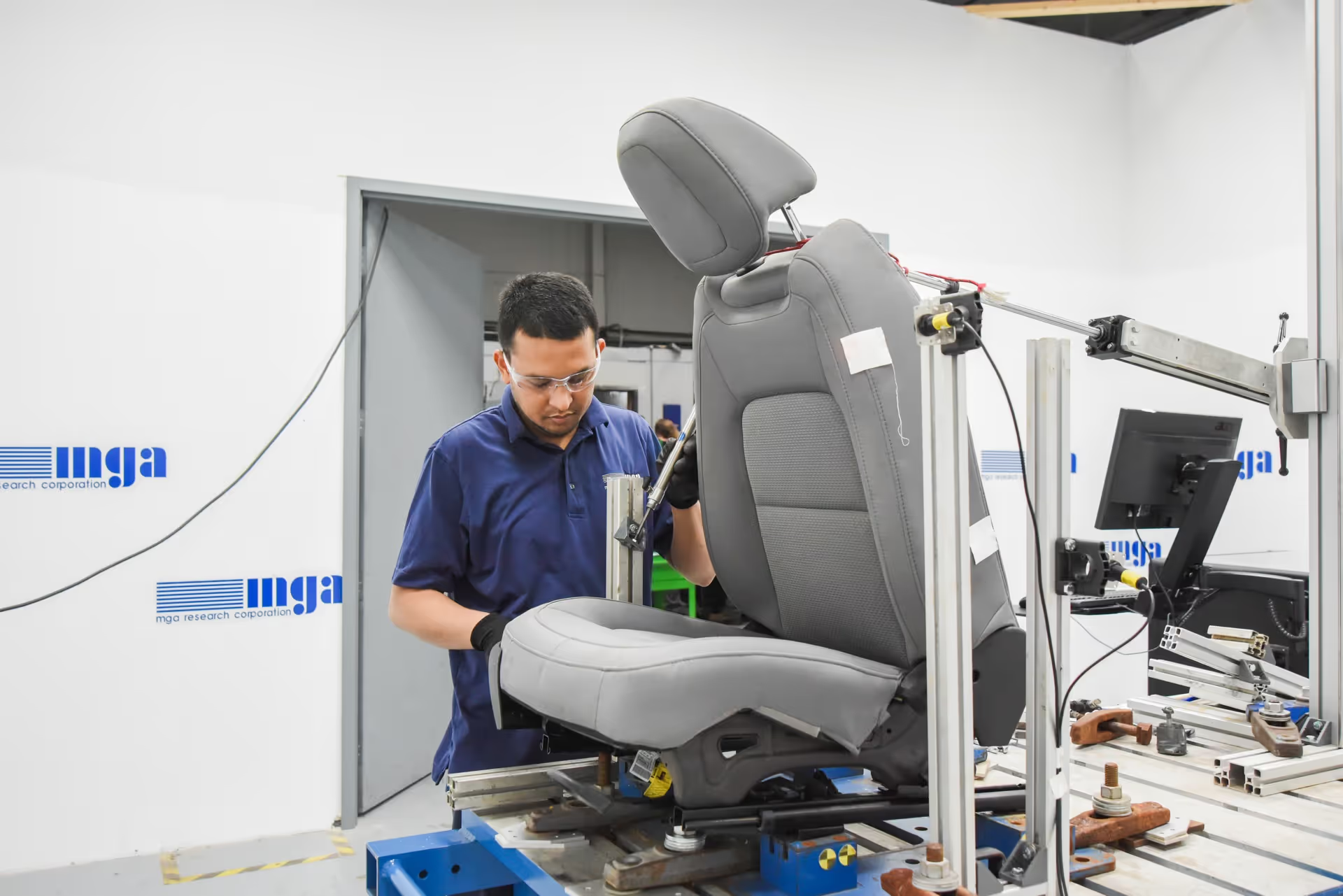
Customized Durability Testing
We provide tailored durability testing solutions using pneumatic, power, servo electric, CAN, and robotic systems to simulate real-world usage conditions.
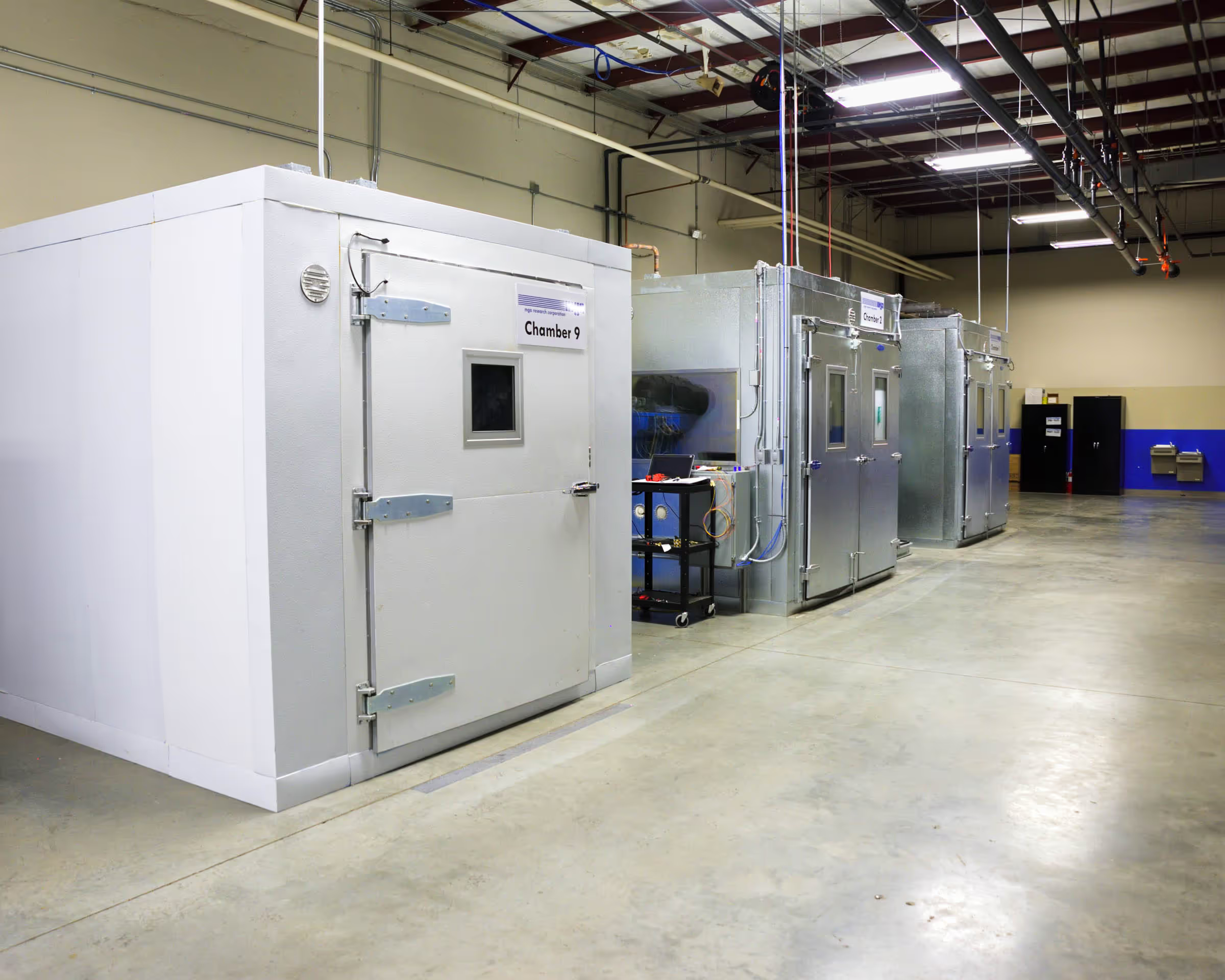
Environmental Simulation Capabilities
We offer a range of environmental chambers to replicate diverse climate conditions, ensuring seats perform optimally in any environment.
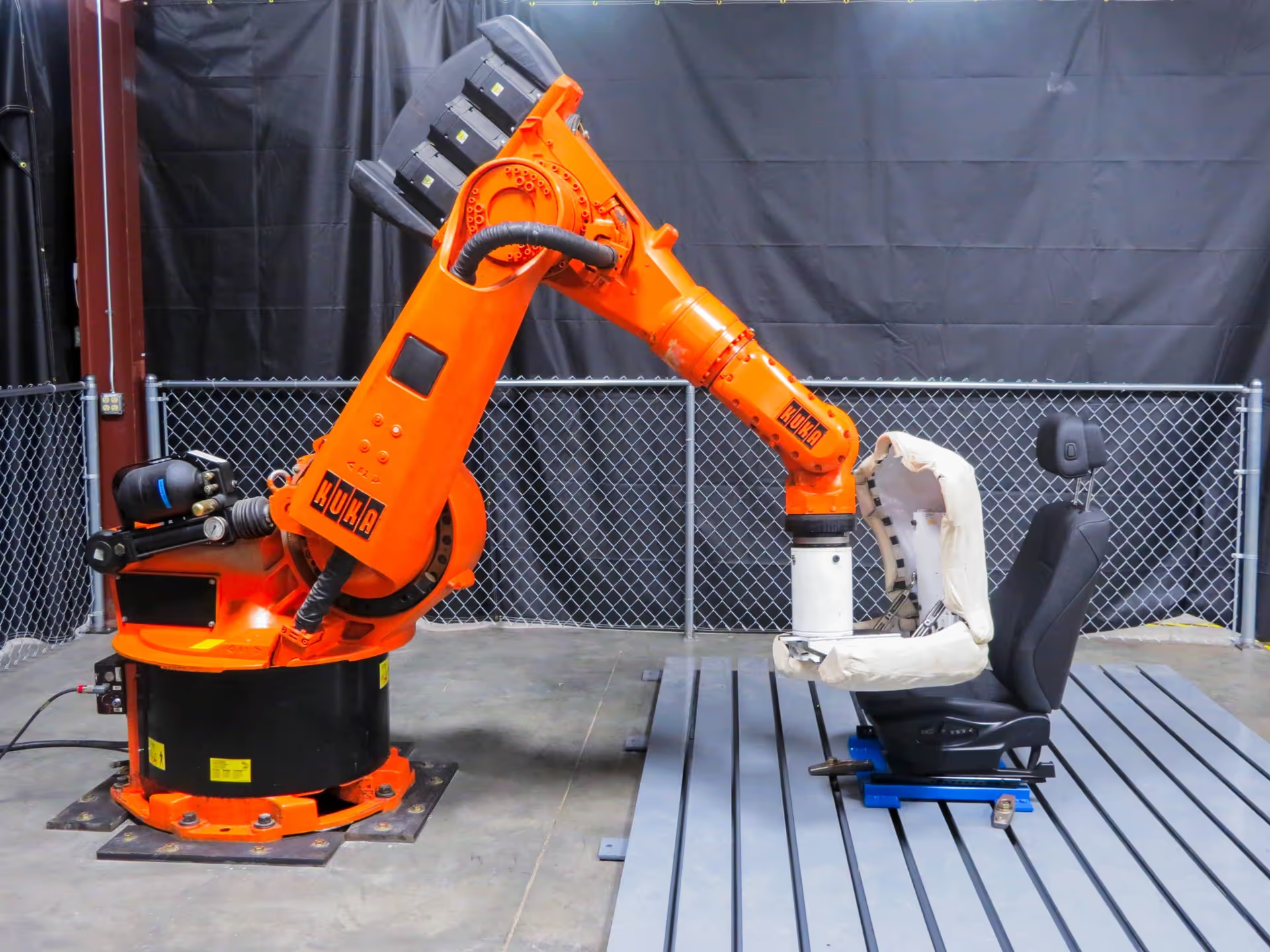
Real-World Fatigue Testing
We conduct realistic fatigue testing using advanced robotics and specialized equipment to simulate human interaction and long term structural and aesthetic durability.
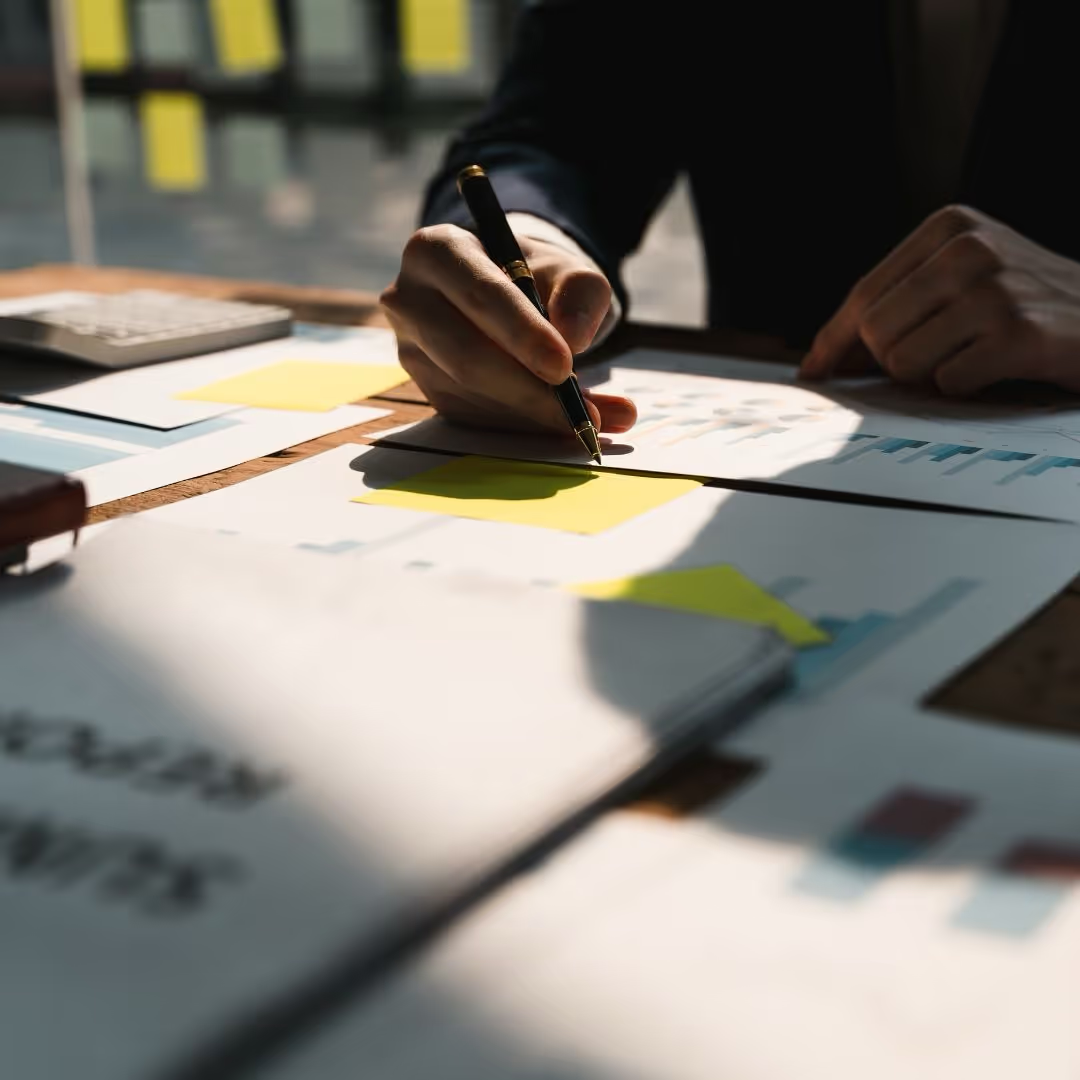
Full DVP&R Project Management
Let our project management team help streamline your validation efforts.
MGA Research is an industry leader in automotive seating test methodologies. With decades of experience, the engineers at MGA have at their disposal an arsenal of the most up to date technology and equipment to guarantee efficient, accurate, and consistent results for all specifications and regulations. Our capabilities span from the smallest mechanical components of a seat to the recent integration of sophisticated computer technology and CAN bus control, as well as any of the modern innovations in safety/comfort features.
MGA Advantage:
- Complete seat development testing experience at all stages including mechanisms, motors, structures, and seat complete (Tier 1)
- Unmatched equipment capacity across our network of test labs
- Full DVP&R Capability!
- Extensive experience with most OEM technical specifications including GM, Stellantis, VW, Mercedes-Benz, Hyundai/Kia, and more.
Durability
Life Cycle Durability & Environmental
Durability testing in the automotive seating sector assesses the lifetime resilience and longevity of all components/features. This testing is designed to simulate the years of use that will be seen in real-world examples. Mechanical/power cycling, exposure to various environmental temperatures/humidity's, or simulation of a person ingress/egressing into a seat a just a few examples of durability test types.
MGA has the capabilities to perform cyclical custom durability testing with a variety of our MGA developed controllers. Whether it be pneumatic, power, servo electric, or robotic, MGA has a solution to perform. A brief summary of these capabilities includes the following:
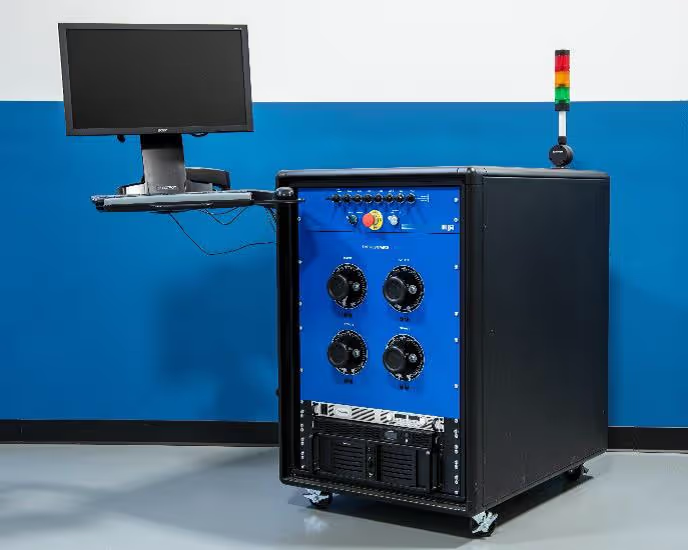
- Force/Current Feedback
- Digital and analog limit switches for risk mitigation and cycle integrity.
- Data recording available at any intervals.
- Cycling capabilities at ambient or extreme temperatures.
- Custom load/fatigue profile capabilities with load/displacement control with servo electric cylinders.
- Monitoring and control for complex systems (i.e., pneumatic comfort systems).
One of the core components of durability testing is the environmental chambers. At MGA Research these include a range in size from reach-in chambers for small components all the way to large drive-in chambers that can fit full vehicles. These chambers have the ability to simulate the widespread conditions that a seat may experience in any part of the world. These chambers are capable of the following:
- Temperature range of -40°C to 105°C with humidity control.
- Adjustable/programmable lamp setups to achieve simulated sun load surface temperatures.
- Fully customizable/programmable profiles with ramp times/rates and soaks.
- Temperature/humidity logging capabilities.
- Corrosion chamber with temperature control and fogging atomizer.
Real-world fatigue testing is also a tenant in the seating durability test log. The simulation of real human beings sitting in seats is integral for ensuring material/structural integrity. Test types include the below:
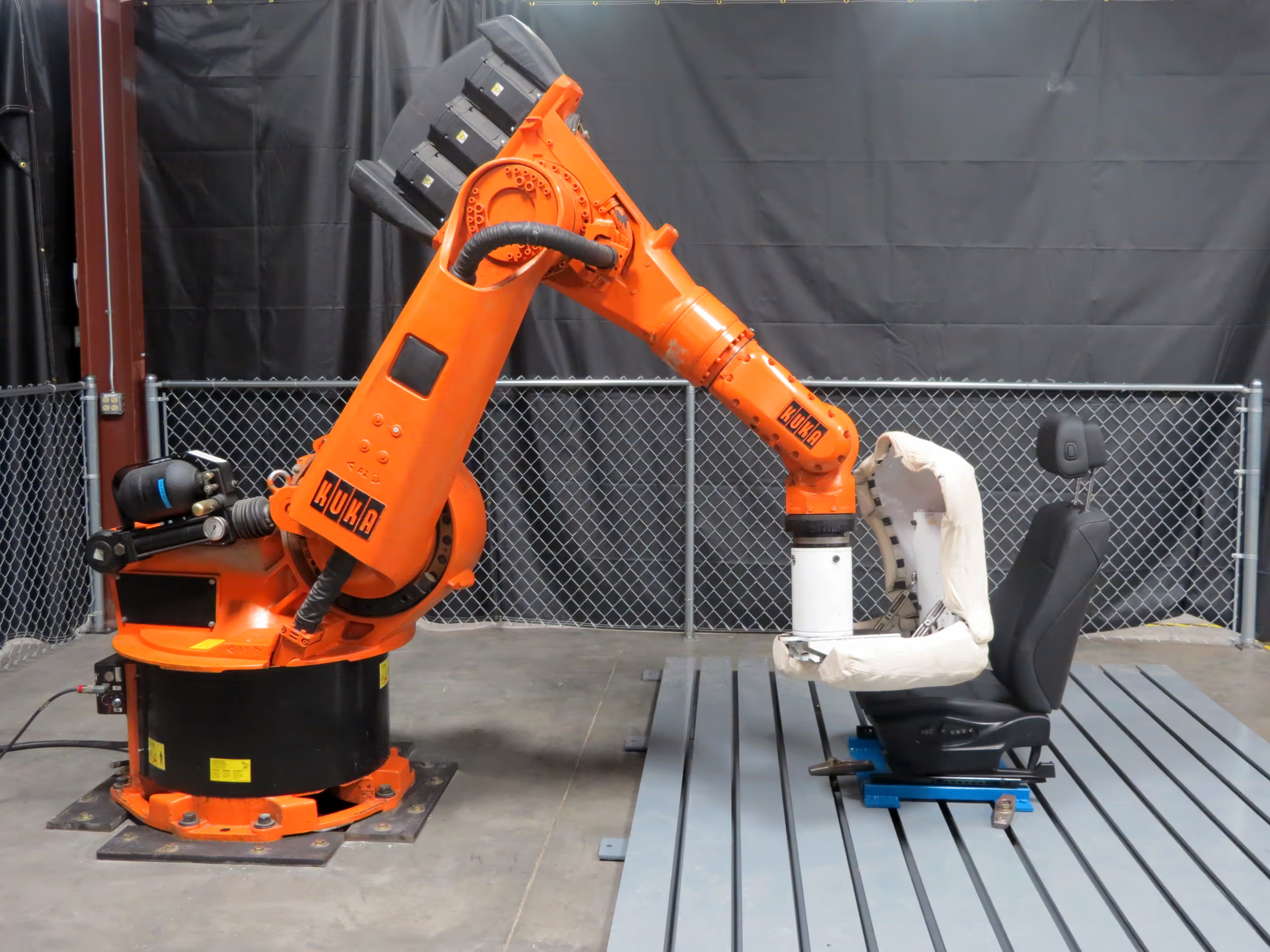
Ingress/Egress Testing
- Seat foam and trim durability.
- Load controlled KUKA KRC2 Robot for seat foam and trim durability testing.
- Simulated real-world motion and loading capabilities.
- Custom forms and end-effectors available.
Jounce & Squirm Testing
- Trim and structural durability testing.
- Variable table stroke and frequency, squirm angle, frequency, and load capacity.
- SAE Back and Butt load forms to test both seat backs and cushions.
Hydraulic Fatigue Testing
- Structural fatigue testing.
- Load controlled & Displacement controlled capabilities.
- Hydraulic actuators of various stroke and load ratings available.
- Various load applicators and attachment methods available.
Safety
Safety testing is required by law to ensure that the seats in a vehicle provide protection during real-world collisions. Testing includes evaluations for seatbelts, seat anchor points, airbag deployments, and capability to withstand the forces seen in vehicle crashes. MGA has the equipment to simulate these tests with high accuracy and repeatability. You can learn about our full safety test capability here, and a summary below:
.avif)
Accelerator Sled Testing
- High-speed video with frame rates of 1,000+ fps.
- Able to produce highly repeatable results.
- Over 100 dummies in MGA including Thor and World SID.
Static Airbag Deployment Testing
- High-speed video with frame rates of 2,000+ fps.
- Ambient or temperature-controlled deployments with in-chamber deployment capabilities.
- Fixtures for seats simulate component position in the vehicle including reaction surface.
Impact Testing
- MGA’s versatile impact testing system is able to satisfy testing needs such as: FMVSS 201 and 202a, as well as ECE 21 and 17 with linear and pendulum impactors.
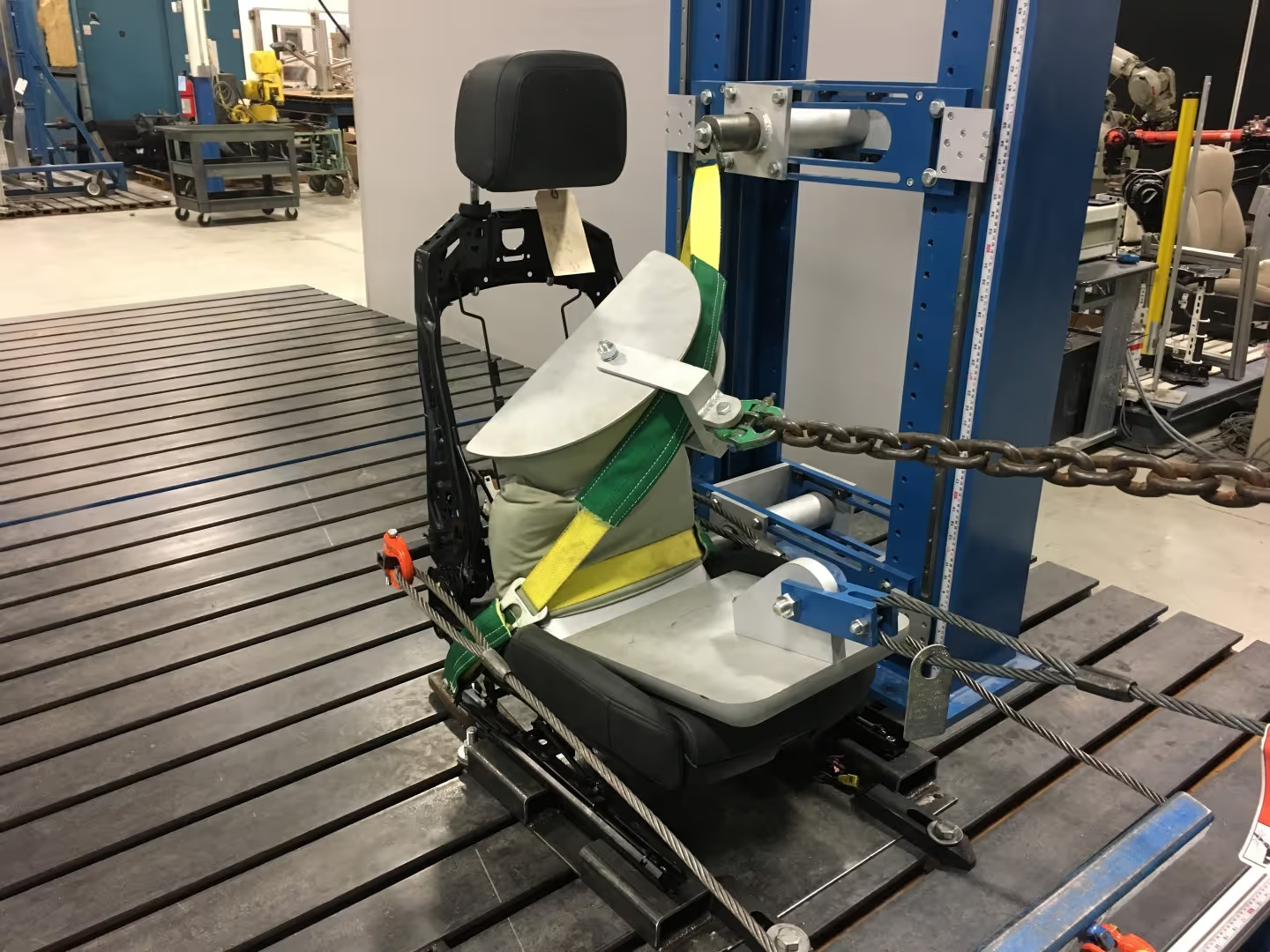
Static Anchorage Testing
- 9 cylinders able to apply loads in excess of 5,000 pounds each.
- Capable of running FMVSS 207/210 and FMVSS 225.
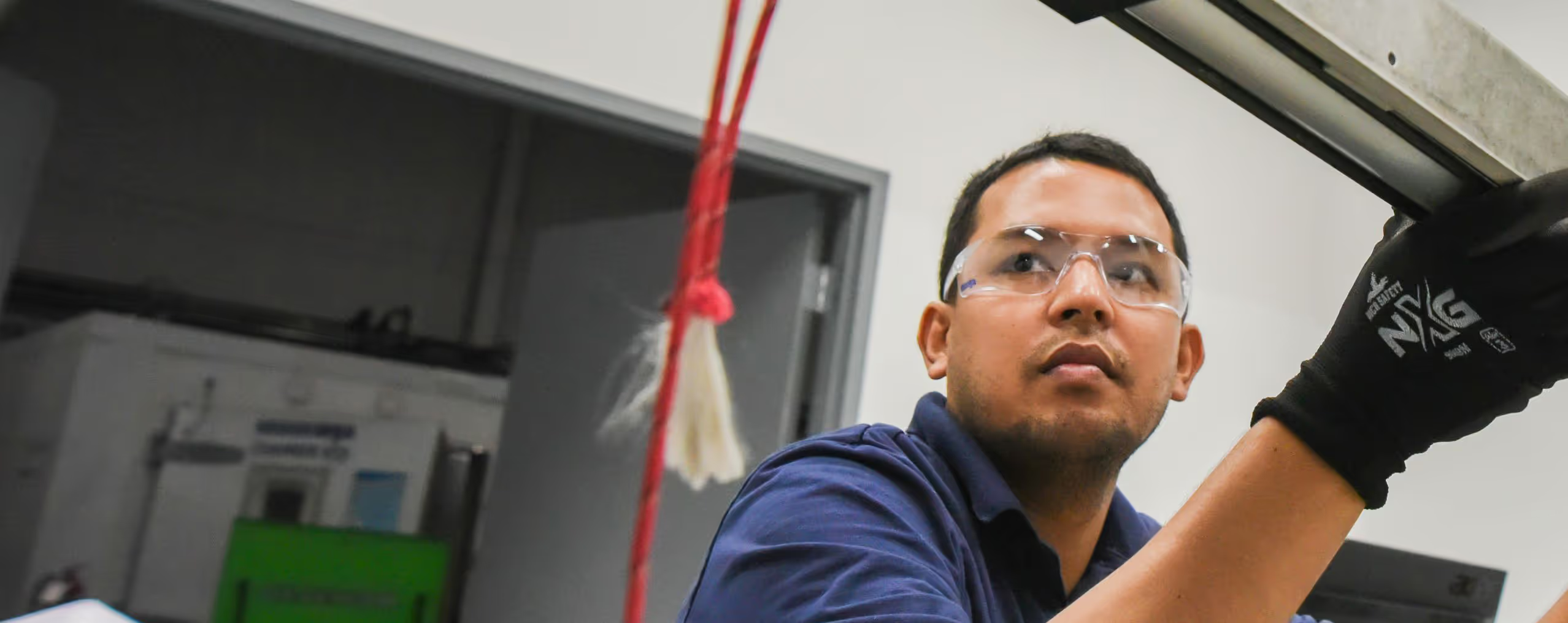
Ready to Get Started?
Let's discuss your testing needs and how MGA can help. Our team is ready to provide the expertise and solutions you're looking for.