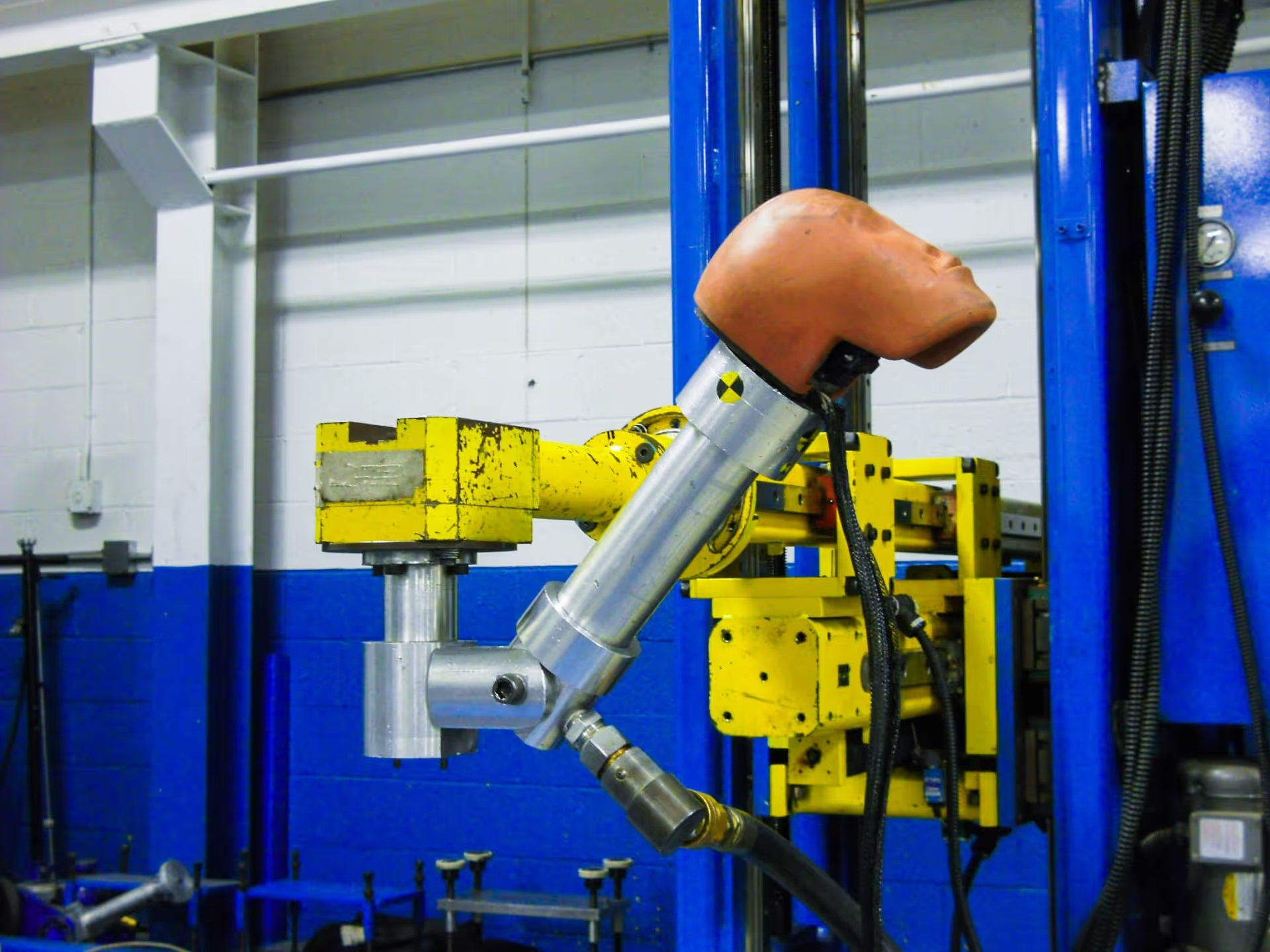
Vehicle Safety and FMVSS 200 Series
Over 30 years of industry-leading expertise in FMVSS and ECE Type Approval testing providing state-of-the-art quality services and ensuring reliable and accurate results.
Quick Overview
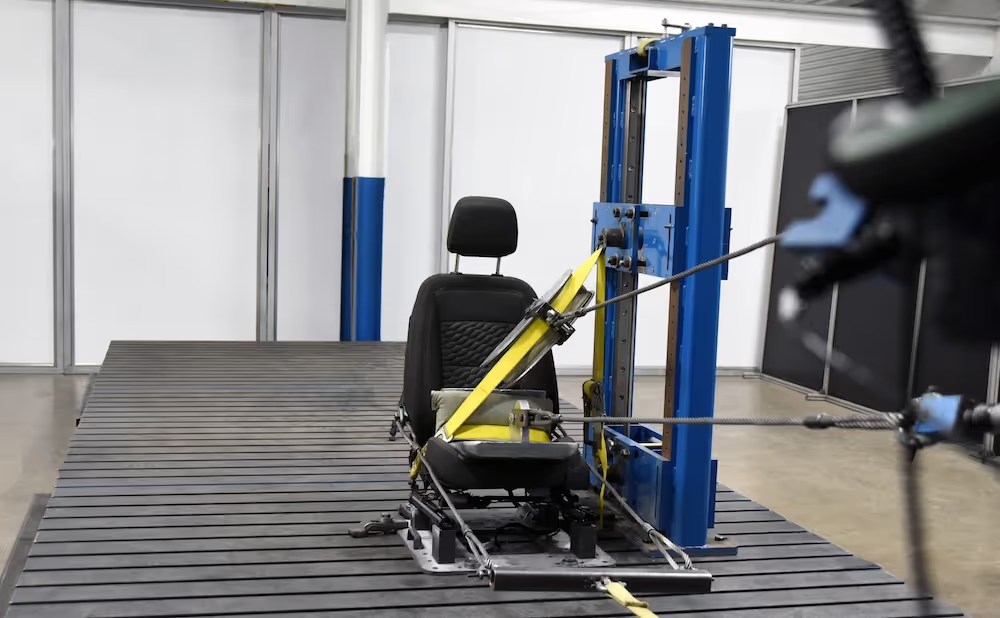
Comprehensive Safety Testing
We offer a complete range of vehicle safety tests, including FMVSS 200 Series, ECE Type Approval, and custom evaluations for various vehicle components.
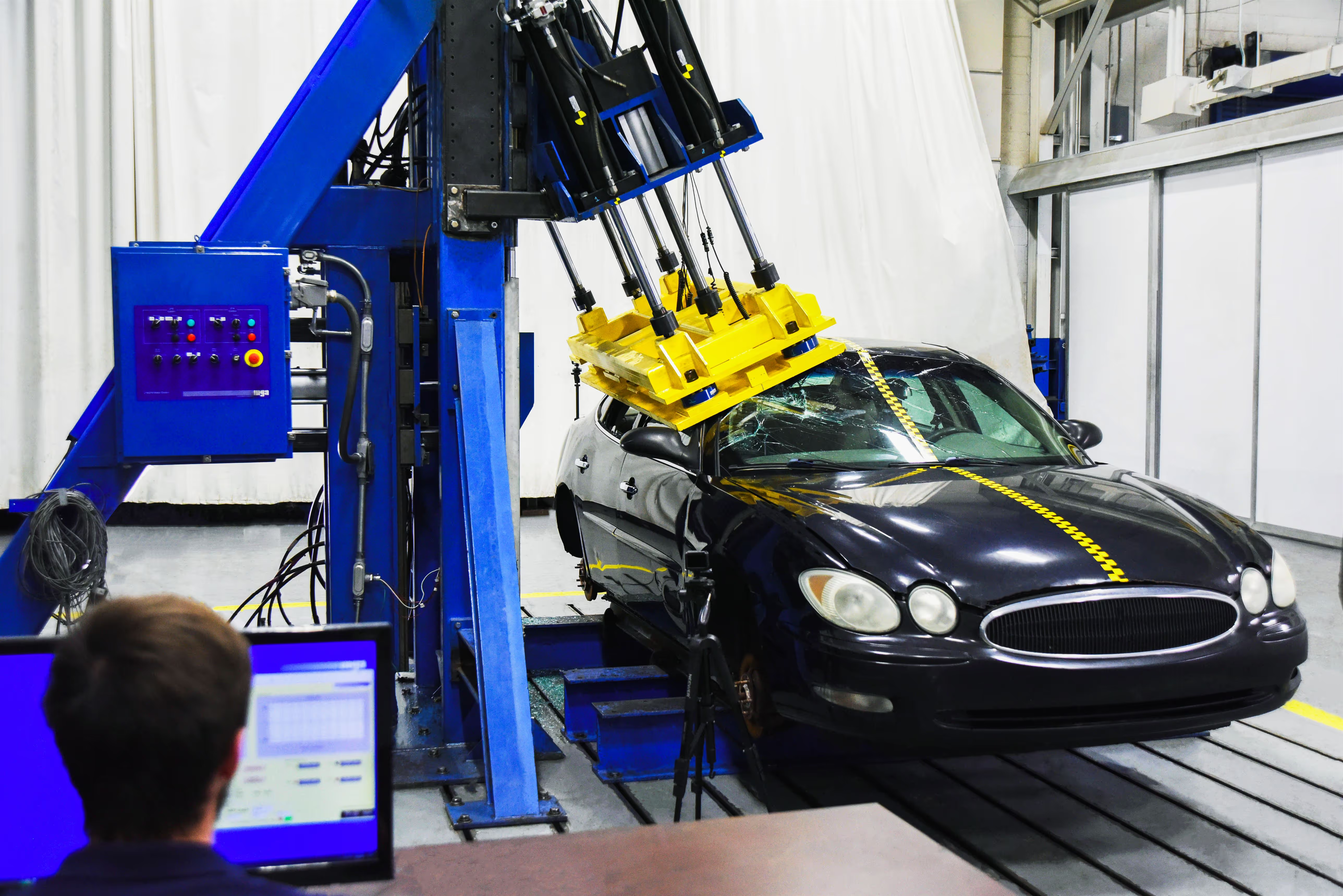
Industry-Leading Expertise
With over 30 years of experience, we provide regulatory insight and reliable and accurate results for all aspects of vehicle passive safety testing.
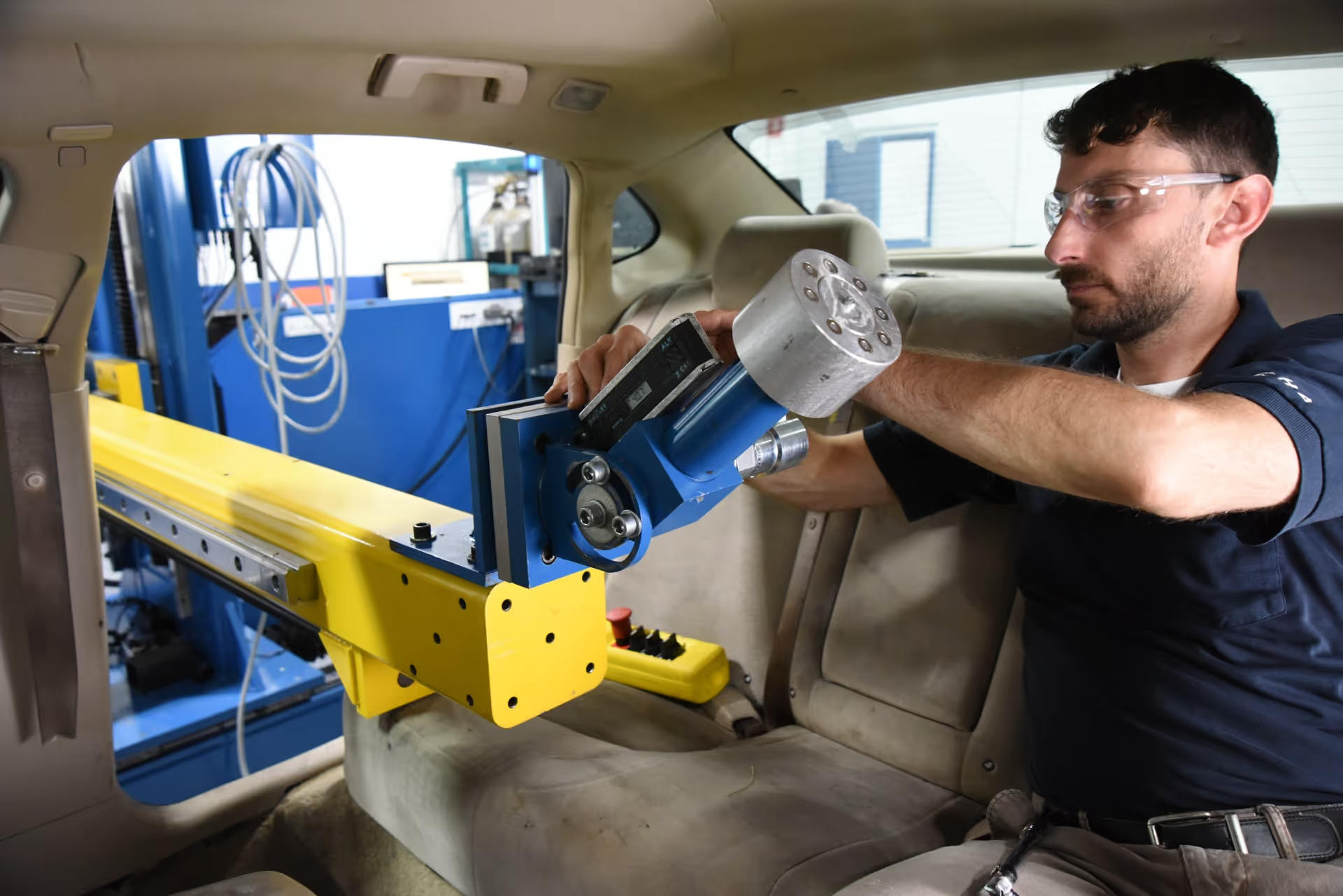
Advanced Testing Equipment
We utilize industry-leading test equipment, much of which is developed in-house, ensuring precise and consistent results across all safety evaluations.
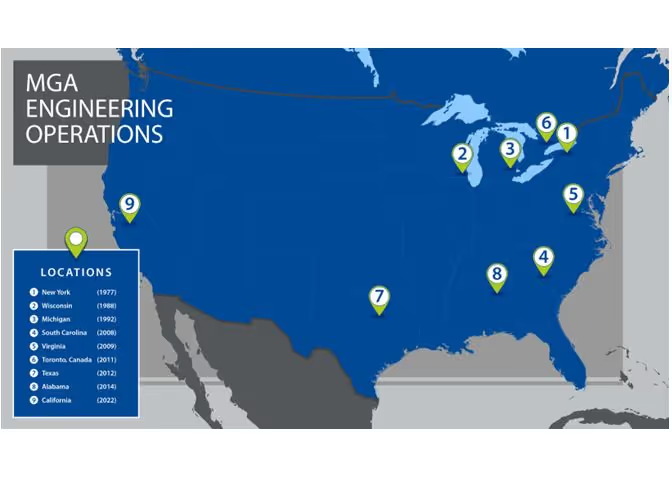
Flexible Testing Network
Our network of test labs and large inventory of equipment allow for rapid deployment of capabilities to any of our locations, maintaining aggressive testing schedules.
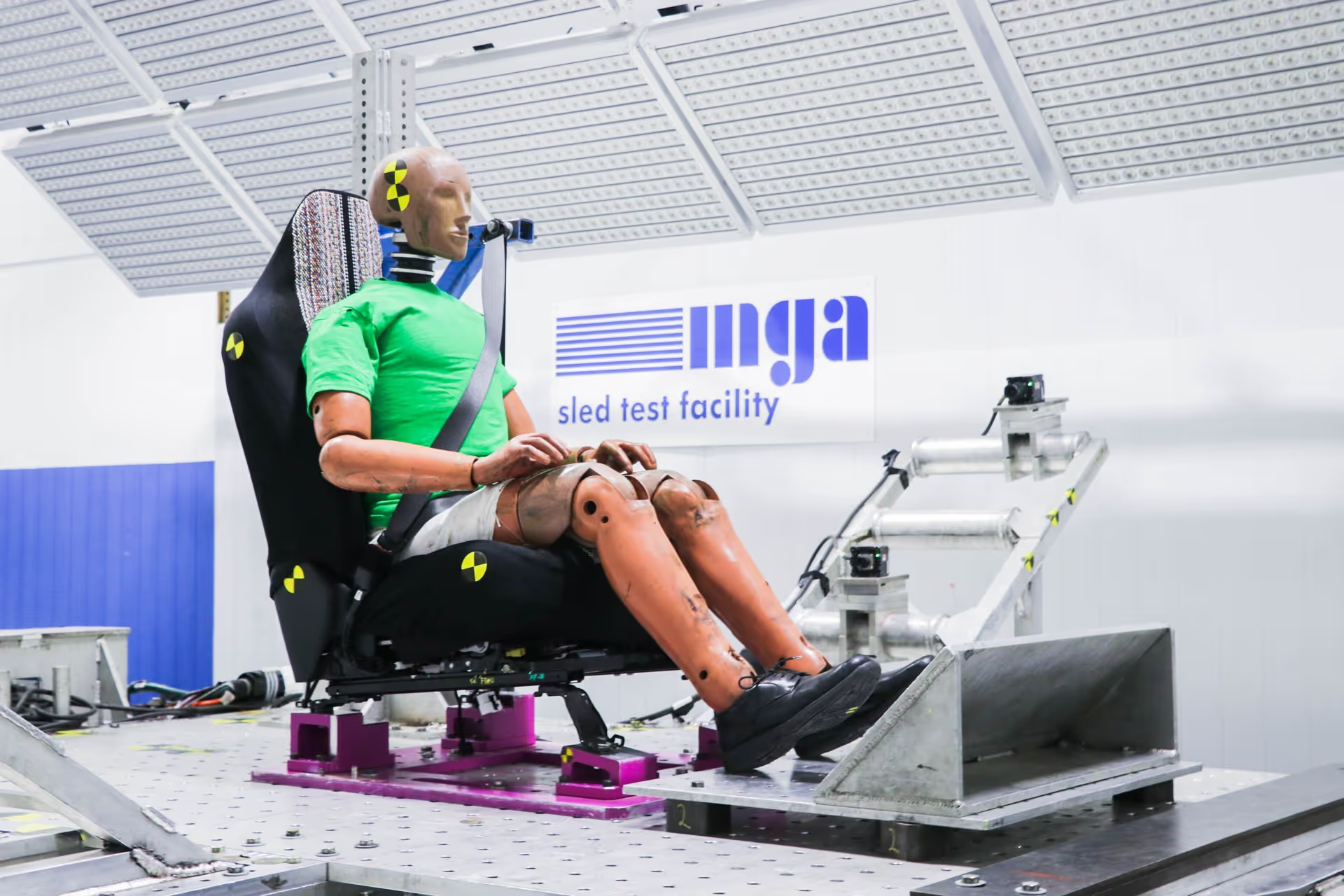
Diverse Test Methodologies
We conduct a wide array of tests, including quasi-static structural strength, dynamic impact, and dynamic sled tests, to evaluate vehicle and component safety comprehensively.
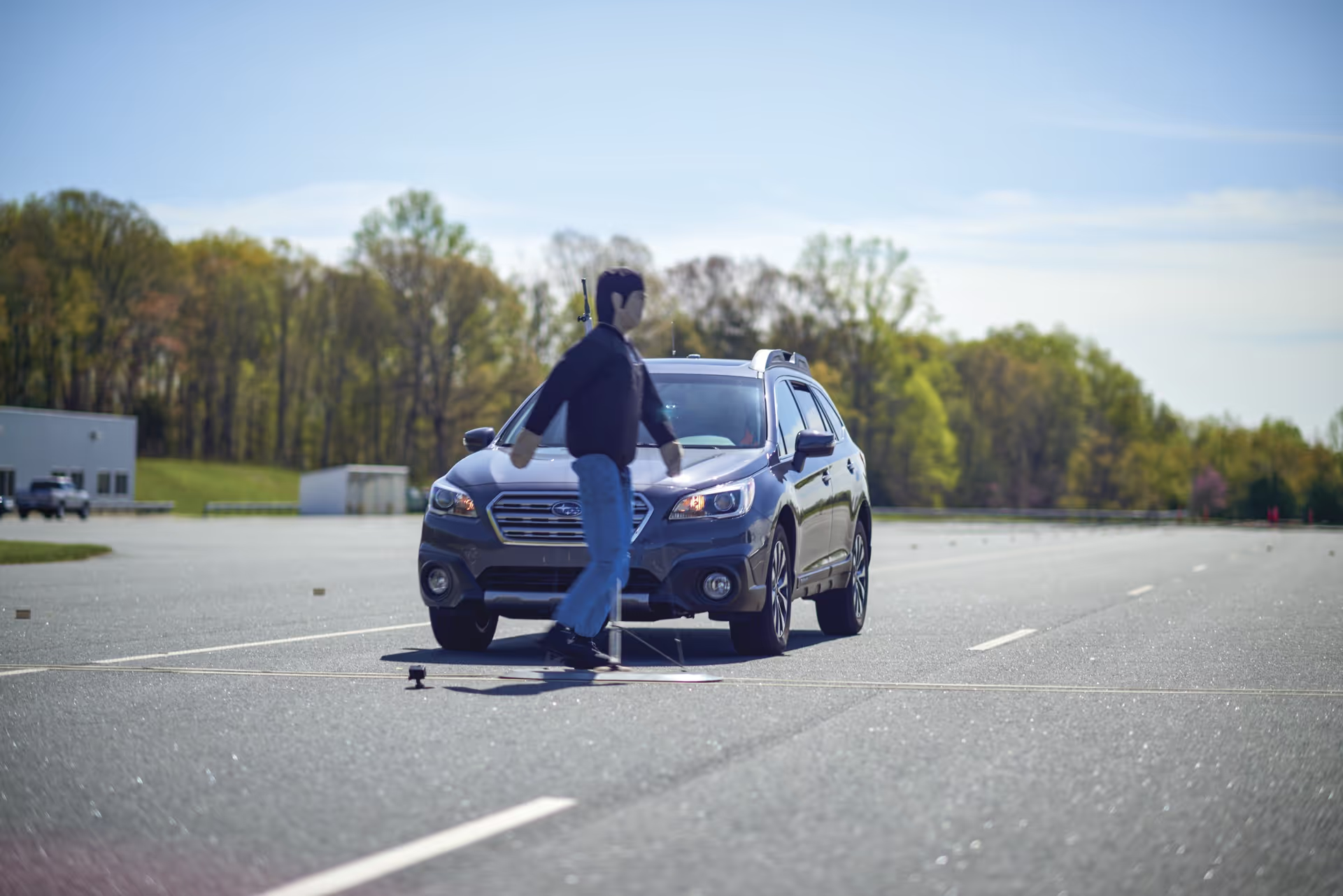
Regulatory Compliance Support
We assist manufacturers in meeting and exceeding federal and international safety standards, supporting efforts to achieve top ratings in NCAP and IIHS evaluations.
Passive safety testing is the cornerstone of MGA. It defines the ability of a vehicle to protect occupants during crash events. How a vehicle or component performs during safety testing is critical to the manufacturer. The Federal Motor Vehicle Safety Standards (FMVSS) outline requirements for vehicles to be sold in the United States, which are enforced by the National Highway Traffic Safety Association (NHTSA). These regulations are aimed at preventing vehicle crashes or reducing the severity of the crash thus enhancing safety for drivers, passengers, and pedestrians alike. They outline specific requirements for the design, performance, and durability of motor vehicles.
Outside of crash testing, the federal regulations applicable to vehicle passive safety components are generally referred to by the phrase “200 Series”. This grouping of safety regulations is focused on occupant injury prevention, in other words, crashworthiness. Further, this series of tests can be categorized into test types, namely, Quasi-Static Structural Strength, Dynamic Impact, and Dynamic Sled. MGA has been actively supporting the advancement of vehicle safety with test services for over 30 years.
MGA Advantage:
- Over 30 years of industry leading expertise in the full suite of FMVSS tests, and equivalent ECE Type Approvals
- Industry leading test equipment, developed by MGA
- Continual collaboration among network of test labs to ensure consistent procedural practices and to maintain aggressive testing schedules
- Large inventory of test equipment in use and in inventory, allowing rapid deployment of capability to any of our locations
Defining the Requirement
The most used phrases in vehicle commercials and print ads are "Top Safety Pick" and "Five-Star" crash test rating. The goal is to provide the highest level of safety possible for the product. Industry-defined standards such as FMVSS, ECE and SAE, are used to evaluate many different types of safety scenarios. The set of tests required for your product depends on the product itself. The most common safety products include:
- Full Vehicles
- Airbags and Seatbelts
- Sensor Systems including Active Safety Devices and “Emergency Call – E-Call”
- Seats including head restraints and airbag suppression systems
- Instrument panel and cockpit assemblies
- Bumpers
- Doors
- Roof structures
Types of Tests
Almost everyone can relate the words crash test with something they have seen on TV. Popular news shows regularly do segments on the latest government crash test results. Long before the government tests the vehicle however, hundreds or perhaps even thousands of tests have been conducted on the vehicle and its safety components. These include:
- Full-vehicle crash testing including frontal, side, rollover or car-to-car impacts.
- Sled testing to evaluate unbelted/belted occupant use.
- Crash simulation evaluating moving objects or projectiles (e.g. luggage).
- Head impact testing to determine injury values.
- Static and synchronized airbag deployment.
- Seat anchorage strength and belt pull testing.
- Bumper evaluation including underride on large trucks.
Quasi-Static Structural Strength
Testing in this category applies a certain force, moment, or displacement rate to various vehicle subsystems and the vehicle itself. Various sensors, actuators, static load forms, data acquisition, and real-time video cameras capture all aspects of the test and are used to evaluate the subsystem or vehicle against the standard’s requirements.
FMVSS 202aS Seating Systems
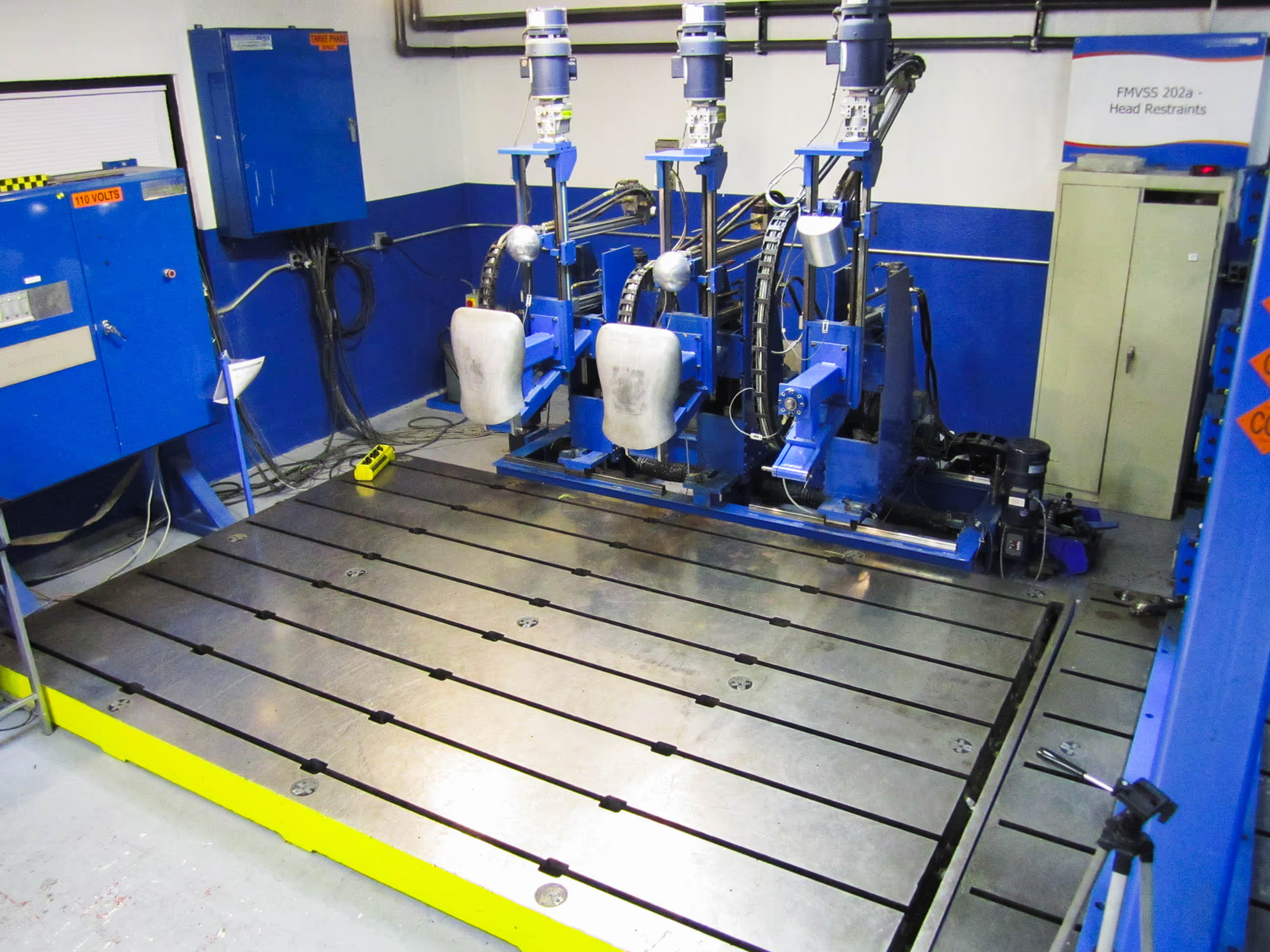
Testing to this regulation determines a seating system’s ability to protect a seated occupant from injury in a whiplash condition, i.e., low-speed rear end collision. Each outboard occupant seating position in all vehicle rows is required to comply with FMVSS 202a. Quasi-statically, a simulated headform and back form is used to apply loads using specified load protocols to evaluate the dimension suitability and strength of the seat, seat back and head restraint.
FMVSS 206 Door Latches and Hinges
This safety standard has several compliance tests related to door systems and door latch and hinge components. Each test is used to evaluate the door system or component’s ability to withstand specific forces and not open. Tests are conducted in various latched conditions (primary and secondary) to ensure the door stays closed during any possible latch position.
FMVSS 207 Seating Systems
This safety standard requires seats to be evaluated in various loading conditions to ensure that the seat back stays in its proper place in the event of a crash. Keeping the occupant in their most advantageous position is key to complying with this test. It is intended to simulate high loads to the seat back, seat cushion and adjusters to test their strength and reliability to stay locked.
FMVSS 210 Seat Belt Anchorage Systems
This regulation involves a combined loading strength test to evaluate the strength of seating systems and their seat belt anchorage. It uses fixtures representative of a human torso and lap to apply loads simulating a frontal crash. Since this test is for a high-speed crash and is looking at seat belt anchor points in particular, the loads are higher than FMVSS 207 loads.
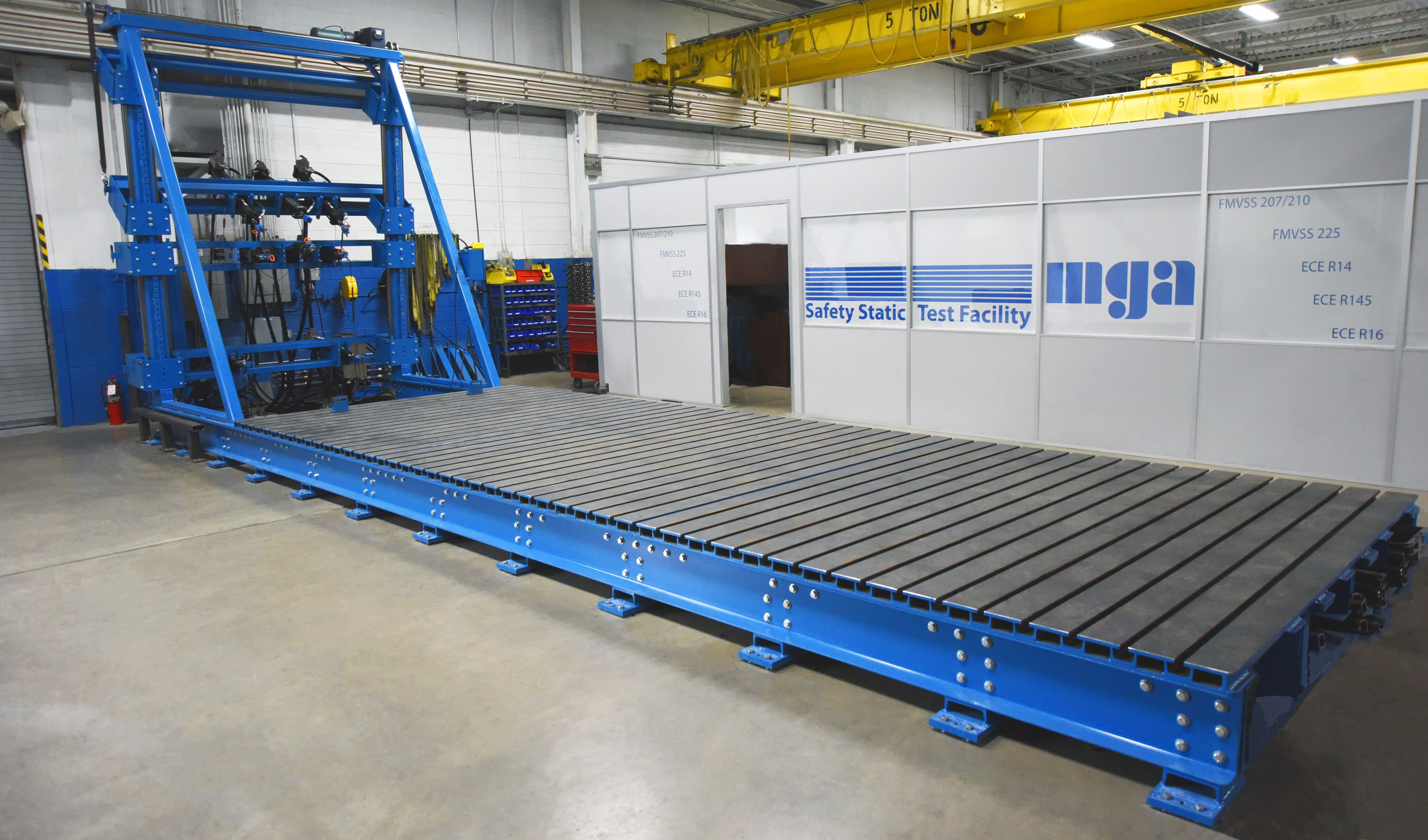
FMVSS 214S Side Door Intrusion
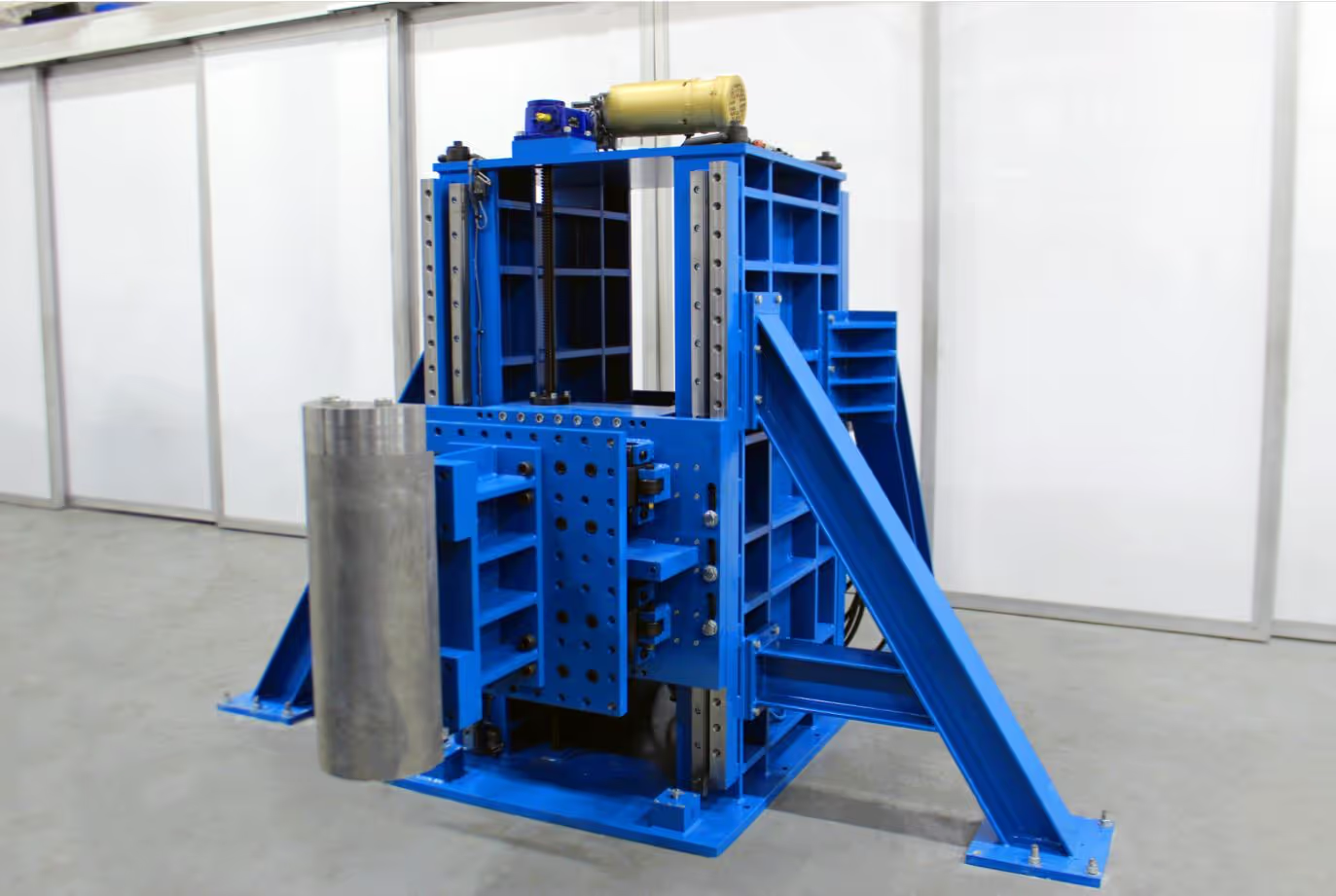
For two specific regulations, 214 and 216s, the federal regulation has two test requirements: a quasi-static test and a dynamic crash test. Manufacturers are required to comply with both test options. The 214S Side Impact test procedure uses a 10” pole fixture and pushes into the door structure until a specific load, energy, and displacement are achieved. This is considered a destructive test and its aim is to prevent door openings so that occupant ejection is thwarted.
FMVSS 216a Roof Crush
Roof Crush Resistance is the second 200 series regulation with a static and dynamic option. In the quasi-static test, a large, rigid test platen is lowered onto the front corner of the vehicle at a specified pitch and yaw. The platen is pushed into the roof structure of the vehicle until a specified load is achieved, which is generally 3.5 times the vehicle curb weight. Simulating a rollover crash event, this test aims to prevent the deformed roof structure from contact with the interior occupants thus avoiding an occupant being trapped in a vehicle following a rollover.
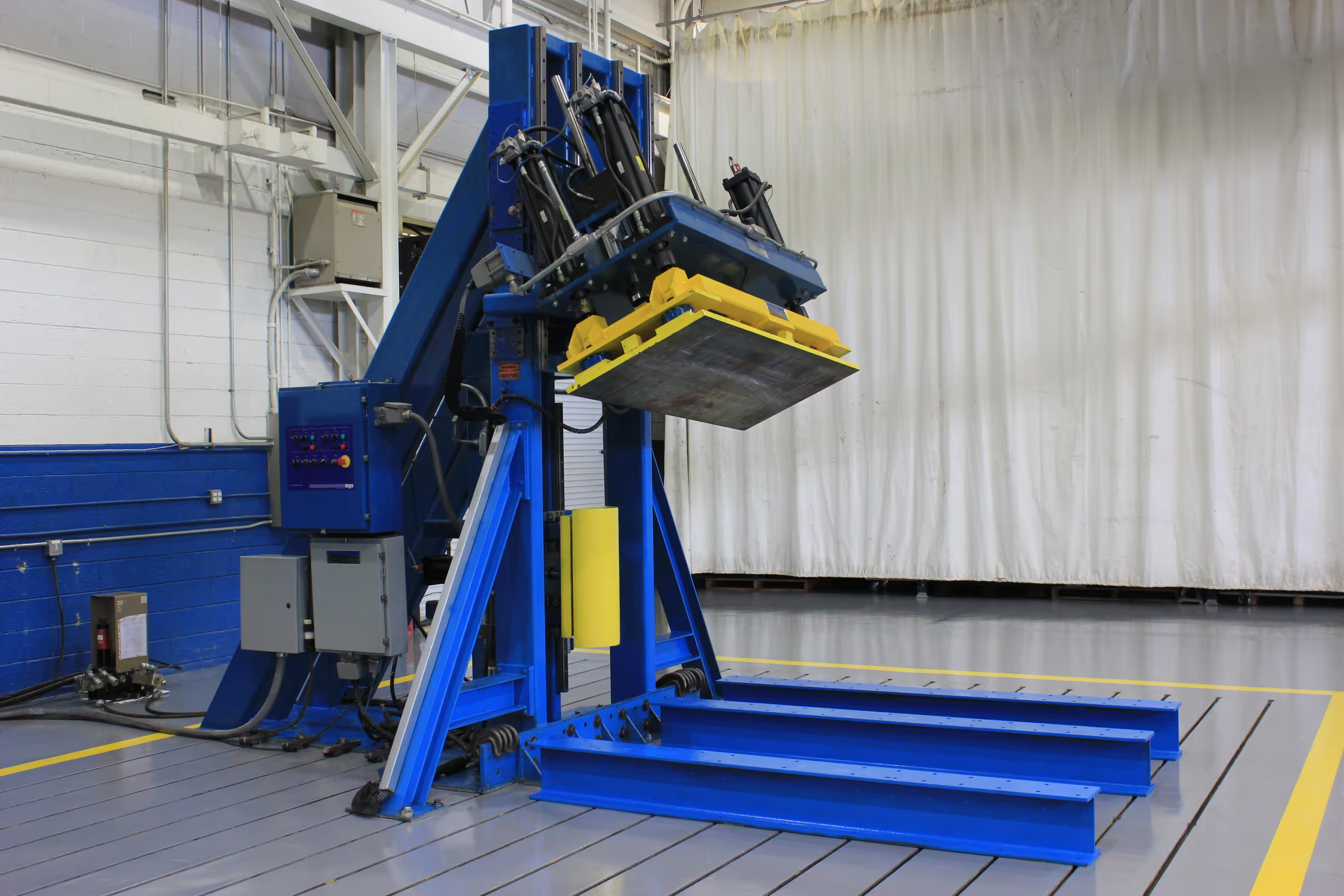
FMVSS 225 Child Seat Anchorage Systems
Evaluating a seating system’s ability to provide sufficient protection with an add-on child restraint system attached to the seat is the goal of this safety standard. Simulating crash events from the front and side, child seat fixtures are used to apply loads to the CRS LATCH system for each occupant seating position.
Dynamic Impact
This grouping includes any regulation aimed at preventing serious injury due to the occupant making direct contact with an interior component in the vehicle during a crash. This includes subsystems such as instrument panels, seating systems, head restraints, sun visors, door panels, and the entire upper interior including pillars, side rails, seat belt anchorages, and headliners. Various unique impactors and impact forms, precise 2000g accelerometers and dynamic-rated load cells and displacement transducers, data acquisition with a sampling rate of at least 10 kHz, and high-speed video cameras up to 2,000 frames per second is most of the equipment needed to conduct successful dynamic tests.
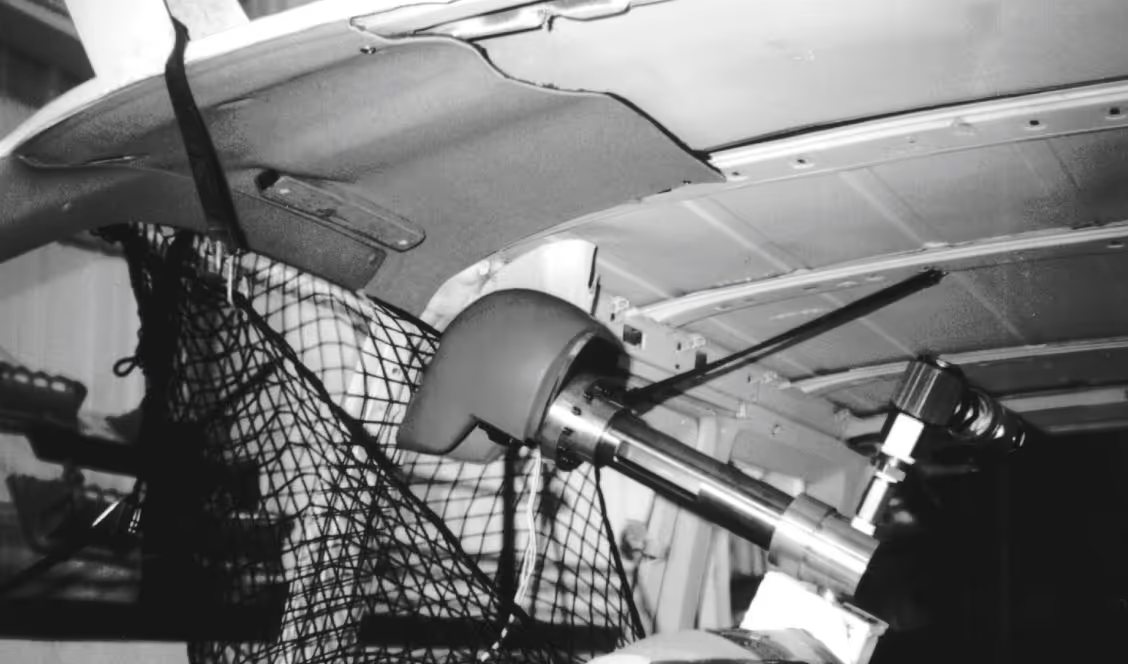
FMVSS 201L Occupant Protection in Interior Impact
In a frontal crash, the occupant typically pivots forward at their hip during the event and may hit their head on a subsystem or component in front of them, specifically the instrument panel, center console, airbag, or seat. This standard uses a dynamic impactor with a simulated headform to impact various components to measure the head injury level. This equipment, the linear impactor and the inverted pendulum impactor, is used globally for any head impact regulation.
FMVSS 201U Upper Interior Occupant Protection
MGA’s Free-Motion Headform (FMH) test system is considered an industry standard in laboratories across the world. The test system is used for conducting occupant head impact simulations on the vehicle’s upper interior. The FMH consists of a skull covered with dummy skin and tri-axial accelerometers mounted at the center of gravity (CG). When impacted against the required upper interior surfaces such as pillars, seat belt anchorages, side rails, headers, and headliner, the Head Injury Criteria (HIC) is evaluated for compliance.
FMVSS 202aS Head Restraints
Testing to this regulation determines a seating system’s ability to protect a seated occupant from injury in a whiplash condition, i.e., low-speed rear end collision. Each outboard occupant seating position in all vehicle rows is required to comply with FMVSS 202a. The dynamic impact for 202a involves a linear impactor for a simulated headform being guided into a head restraint at a high speed to evaluate 3 msec Clip, which is an indicator of head injury level.
FMVSS 203 Protection Against Steering Wheel Impact
This safety standard is exempt in today’s modern vehicles equipped with a Driver Air Bag (DAB). For countries that do not require frontal airbags, FMVSS 203 is used to evaluate potential driver chest injuries in a frontal crash simulation. An impactor called a BLAK Tuffy Dummy, essentially an upper torso with head, is propelled into the steering wheel at a high rate of speed. The force measured during impact on the dummy is used to calculate the peak force, which is compared to the acceptable limit for compliance.
FMVSS 226 Ejection Mitigation
The test standard is used to evaluate countermeasure designs for side curtain air bags, glass, and other subsystems, that are intended to reduce occupant ejection in rollover or side impact events. Like FMH, a dummy skull and skin are placed at the end of the ejection mitigation impactor and launched into the deployed air bag or other countermeasure. If the headform reaches a specific limit passed the window (outside of the vehicle), then the countermeasure does not comply with this standard.
Dynamic Sled
MGA’s Accelerator Sleds have supported a variety of industries throughout the world for over 30 years. With systems installed in facilities ranging from automotive OEMs to child restraint manufacturers, our facilities have produced repeatable results that aid in product development. Not only do we design these systems but 12 of our sled systems are being used at MGA facilities every day. This gives us the ability to layout optimized lab space to maximize efficiency. Our experience with these systems, along with our expertise in design, results in our customers having the best installation, training, and system dependability for this certified test facility.
For FMVSS-related testing, there are four safety standards that have an inertial component, essentially imparting a specific crash pulse to the specific subsystem to see if it unlatches, moves out of position, opens, etc. In case of 202a, compliance can be achieved using a dynamic sled option (instead of conducting the static portion). Another optional test method for most inertial evaluations is the calculation method that allows for computer-generated data to be used in place of conducting sled tests (only applies to 201L S5.3 and 206 S4.1.1.4 and S4.2.1.3).
FMVSS 201L Occupant Protection in Interior Impact
Glove boxes, center console storage compartment, and any other storage area is evaluated for latch retention during crash pulses from all six orthogonal directions. If the latch opens, then the component does not comply with the inertial requirements of this standard.
FMVSS 202aD Head Restraints
Manufacturers have two options for 202a compliance, static or dynamic. The dynamic option uses a Hybrid III 50th percentile ATD seated in any outboard occupant position in the vehicle. A low-speed rear crash pulse is applied to the seat and the head-to-torso rotation is calculated using gyros in the head and chest area of the ATD.
FMVSS 206 Door Latches and Hinges
Door systems including latches, hinges, and hardware are required to meet inertial pulses in the same way as glove boxes and storage compartments in 201L. In this test, the crash pulses are applied to the full vehicle with the doors latched in their primary position. Following each pulse (3 to 6 directional pulses required), the door is attempted to be pulled open using a peak force. Compliance with this standard requires the door to stay closed and not pop open.
FMVSS 207 Seating Systems
This safety standard requires that all seating systems with adjustable seat backs (i.e., recliners) meet an inertial pulse simulating a frontal crash. The crash pulse is applied to the seat in an unoccupied state (no ATD used). For compliance, using high-speed video review, the adjustment positions of the seat are evaluated to ensure each remained in its pre-set position.
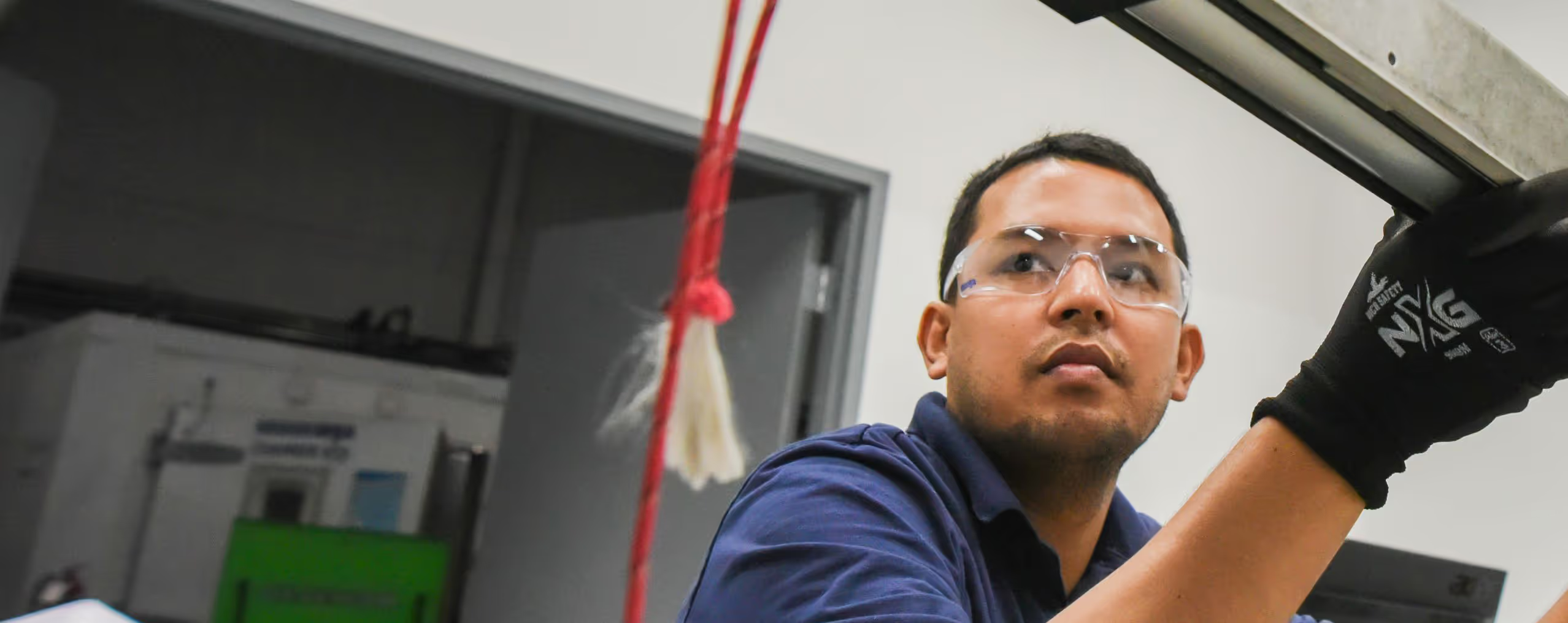
Ready to Get Started?
Let's discuss your testing needs and how MGA can help. Our team is ready to provide the expertise and solutions you're looking for.