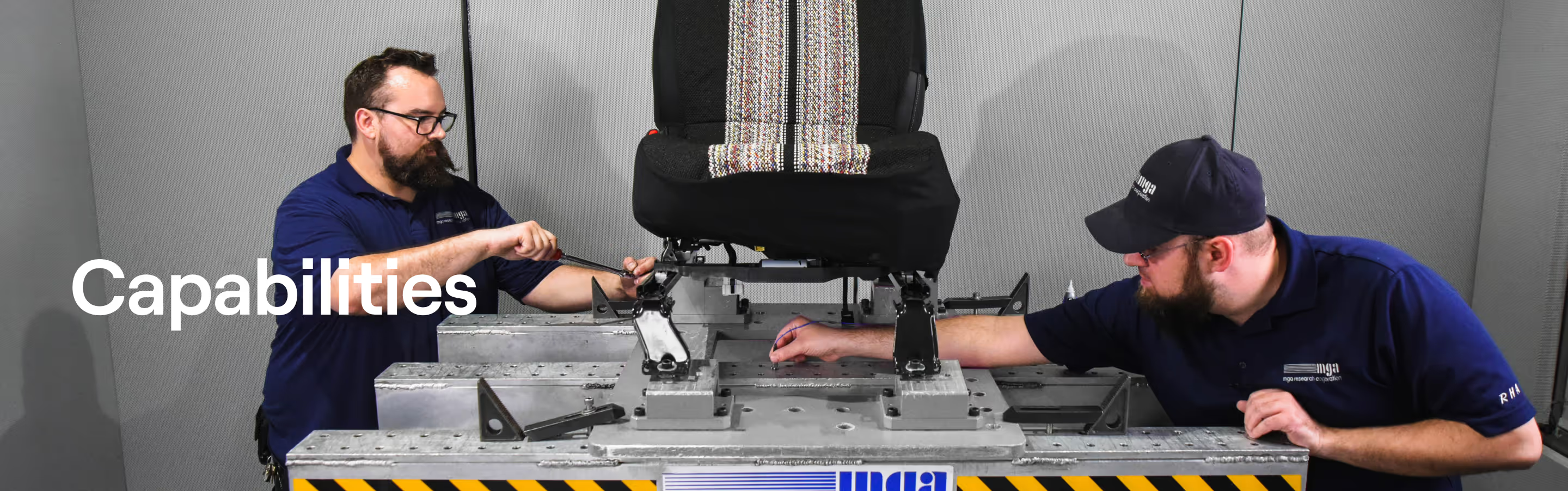
Testing Services
MGA delivers comprehensive testing services and equipment solutions to ensure the safety, durability, and performance of vehicles and automotive components.
Vehicle Safety Testing
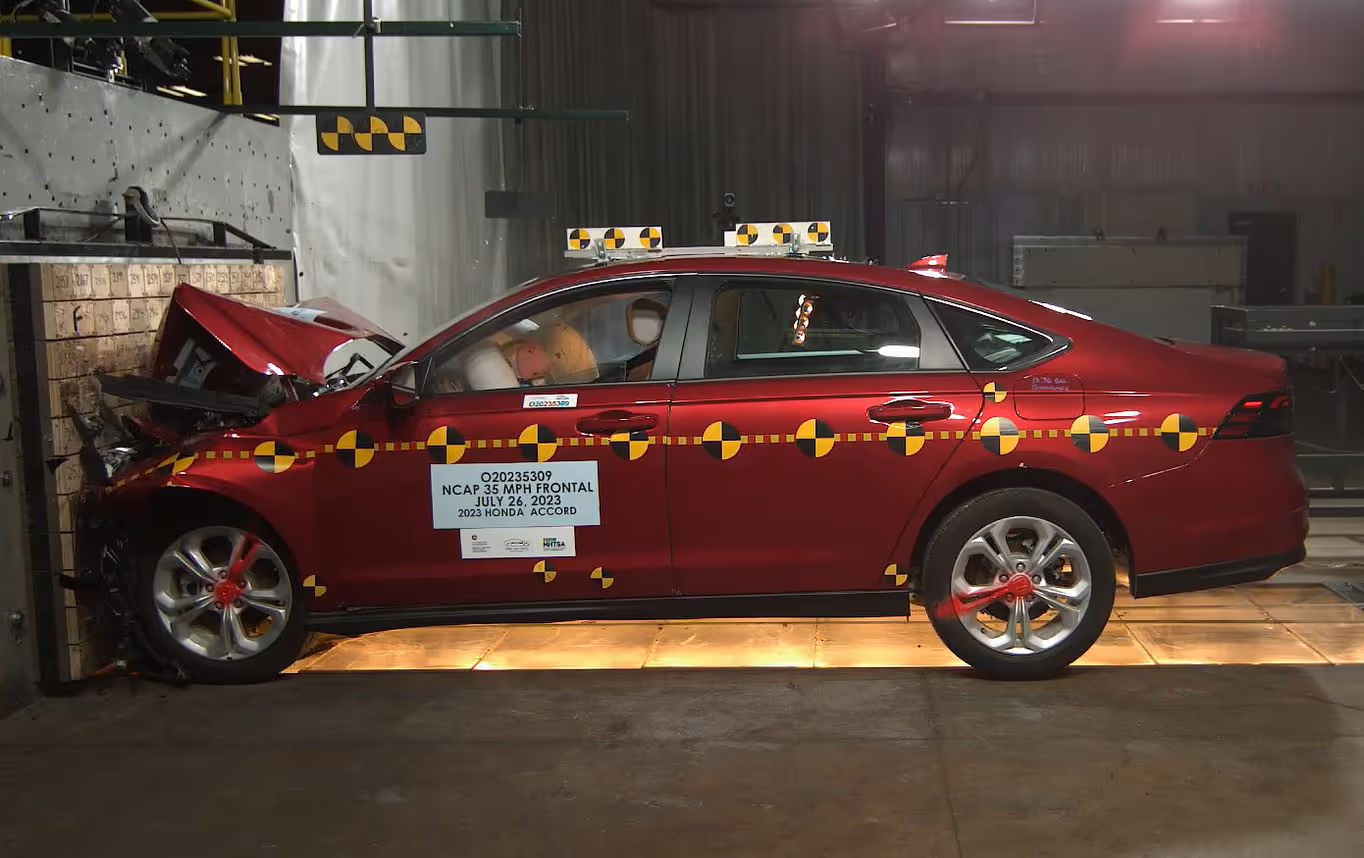
Crash Testing
Comprehensive crash testing services support automotive safety development from early prototypes through final regulatory compliance and consumer ratings.
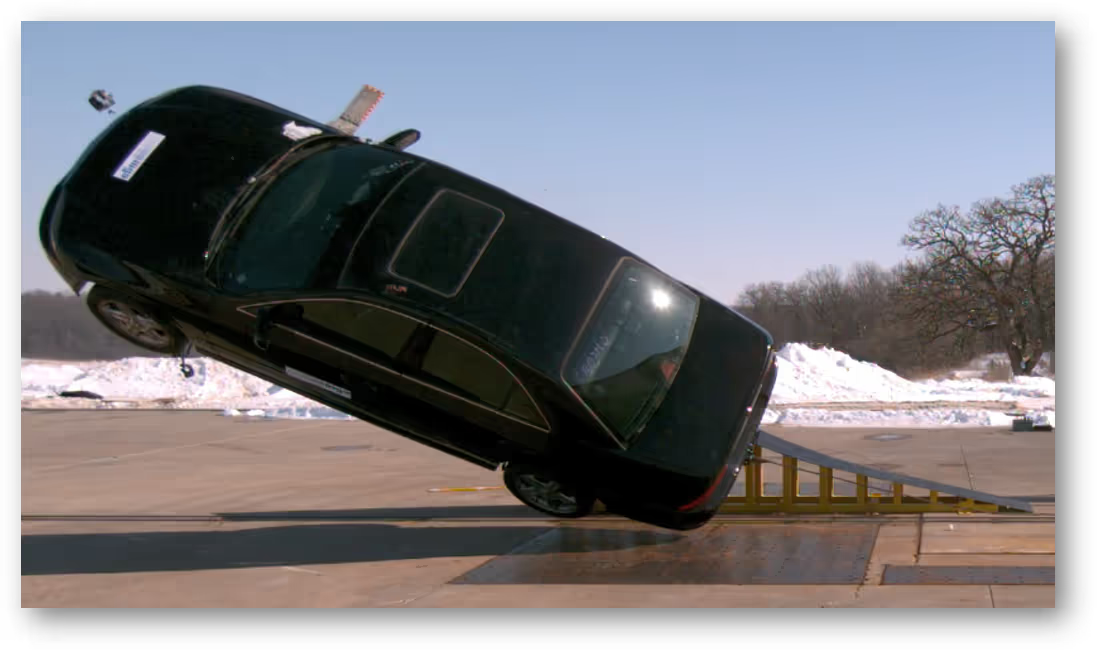
Rollover and Sensor Development
Extensive static and dynamic testing evaluates airbag sensor performance across a spectrum of real-world scenarios, from minor impacts to extreme events.
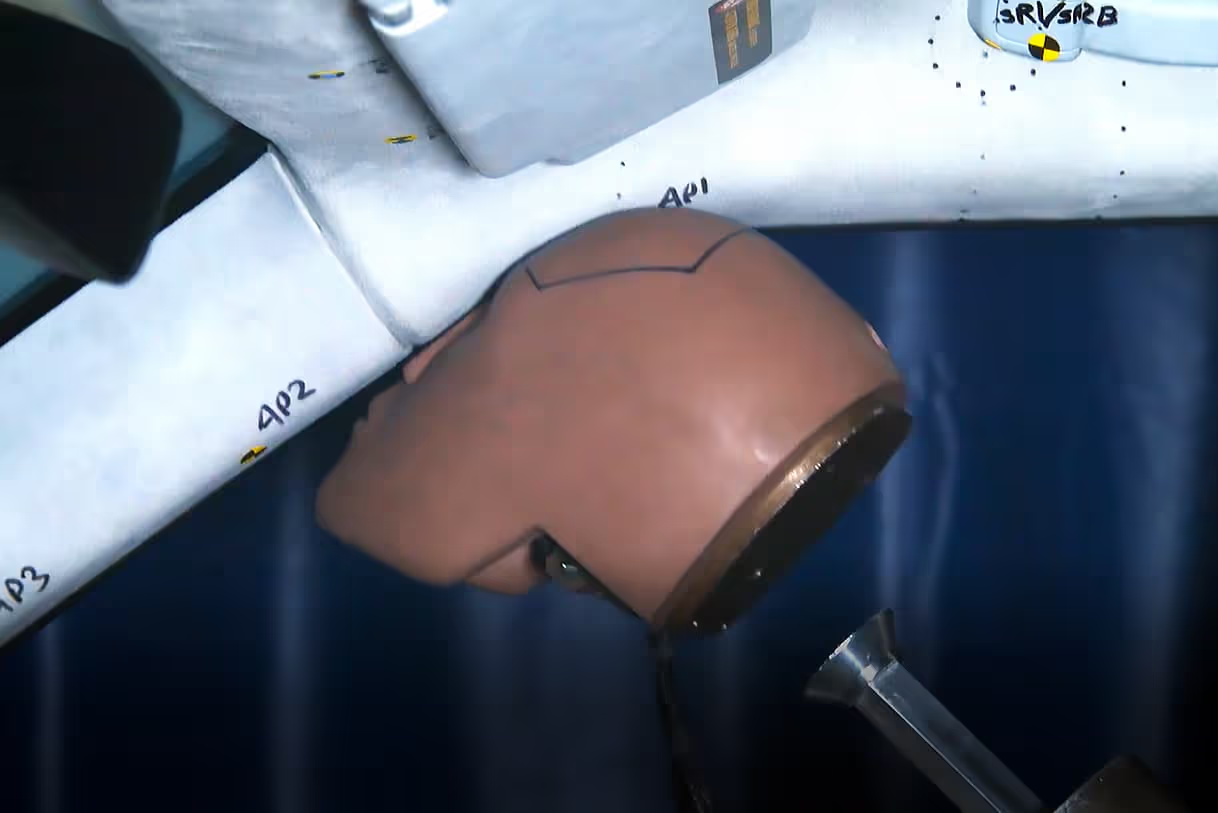
Vehicle Safety and FMVSS 200 Series
Rigorous testing evaluates vehicle and component safety performance across a range of scenarios, from quasi-static structural tests to dynamic sled impacts.
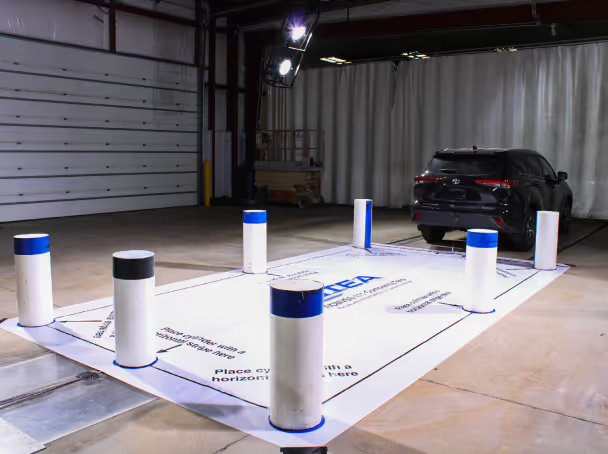
FMVSS 100 Series Testing
Specialized testing evaluates vehicle crash avoidance features, including controls, visibility systems, and safety mechanisms, to ensure compliance with federal standards.
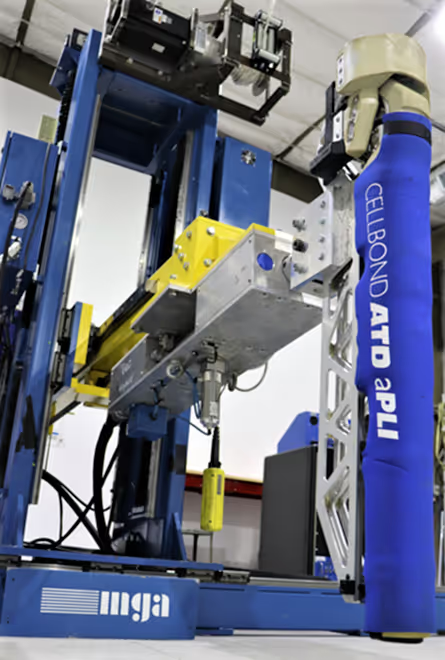
Passive Pedestrian Protection
Advanced testing evaluates vehicle designs to mitigate pedestrian injuries in collisions, focusing on head, upper leg, and lower leg impacts using specialized equipment and global standards.
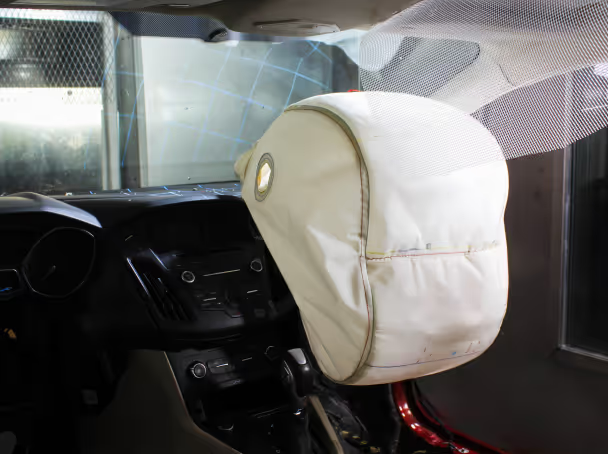
Airbag Deployment
Comprehensive airbag testing services ensure reliability and performance across various types and deployment scenarios, supporting manufacturers throughout development and production phases.
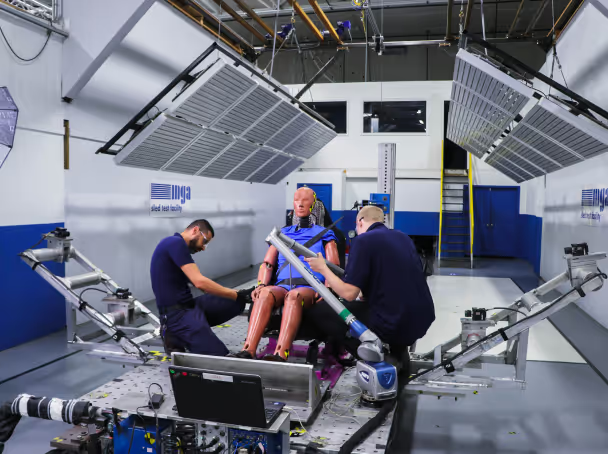
Sled Testing
Comprehensive sled testing services utilizing proprietary acceleration technology and expertise to simulate crash conditions for safety evaluation across automotive, aerospace, and related industries.
Component Development Testing
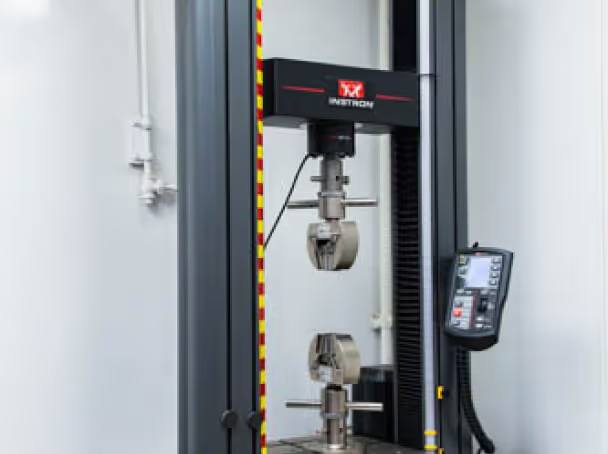
Materials
Comprehensive automotive material testing services evaluating physical and aesthetic properties, utilizing advanced facilities and expertise to ensure quality, durability, and compliance with industry standards.
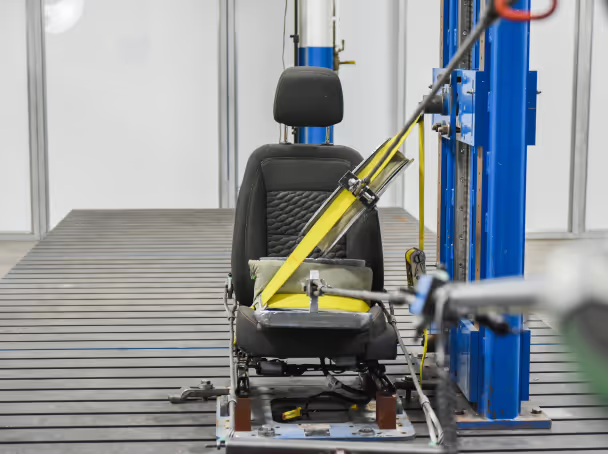
Seating
Comprehensive automotive seating testing services covering durability, safety, and comfort, utilizing advanced technology and expertise to ensure quality and compliance with industry standards.
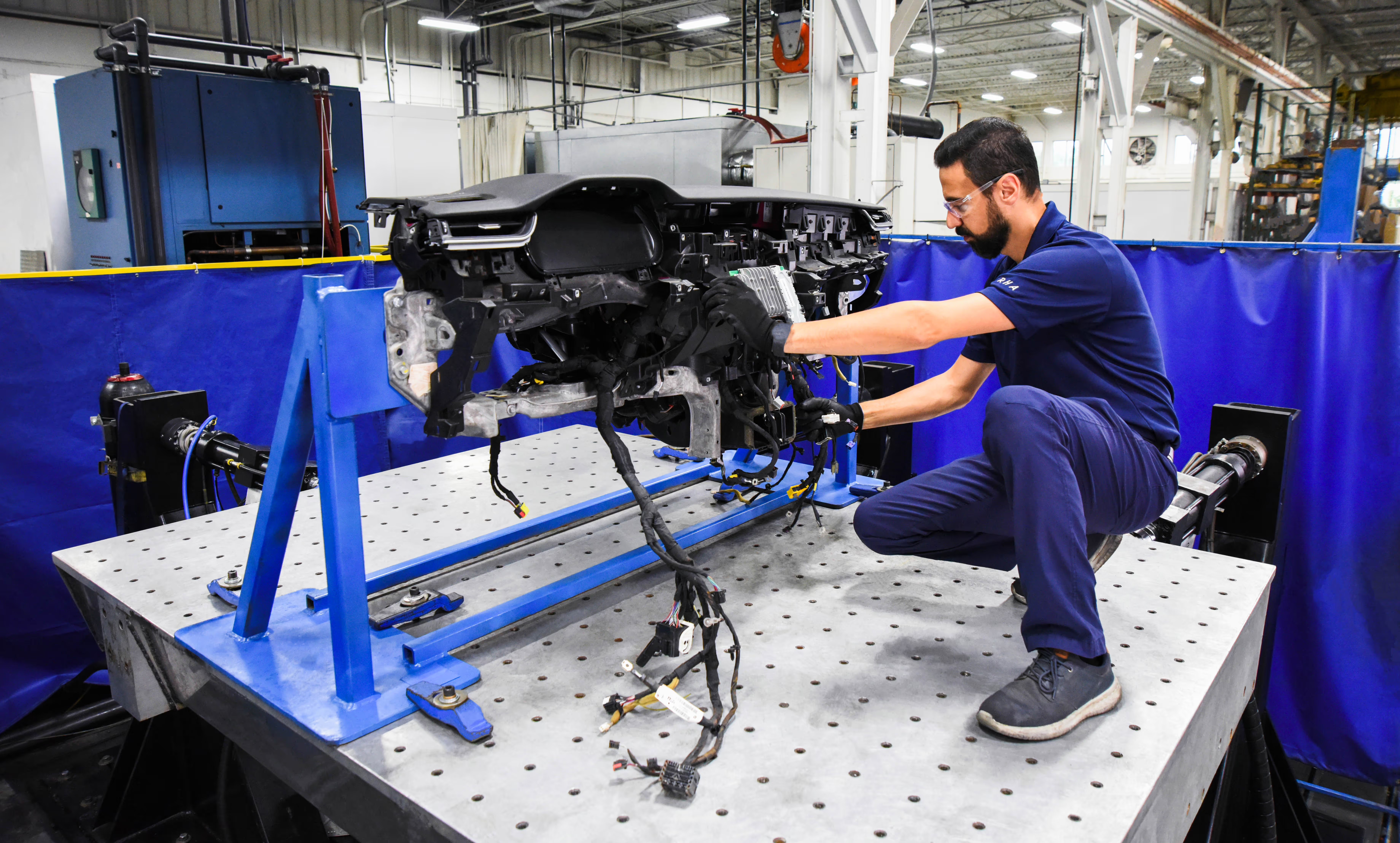
Interiors
Comprehensive automotive interior testing services covering comfort, safety, durability, and functionality, utilizing an extensive network of laboratories and advanced technologies to ensure quality and compliance with industry standards.
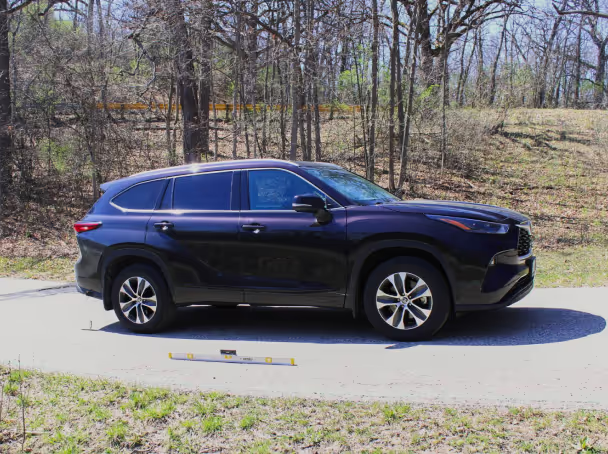
Exteriors & Closures
Comprehensive automotive exterior testing services covering environmental durability, functionality, and aesthetics, utilizing an extensive network of laboratories and advanced technologies to ensure quality and compliance with industry standards.
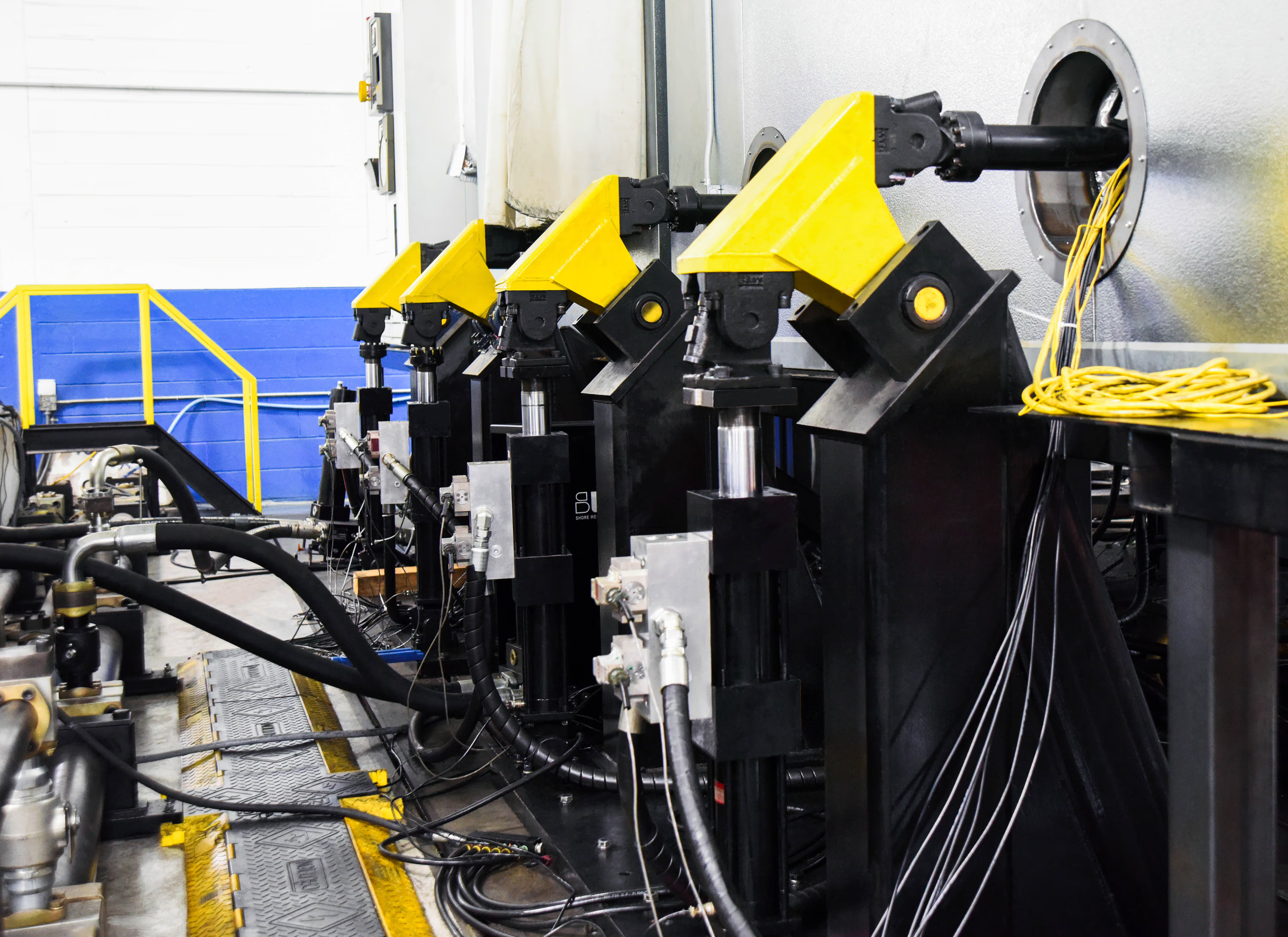
Hydraulic Durability & Chassis Testing
MGA leverages over 20 years of experience, state-of-the-art facilities, and expert engineers to provide industry-leading hydraulic durability testing services for automotive, aerospace, and other industries.
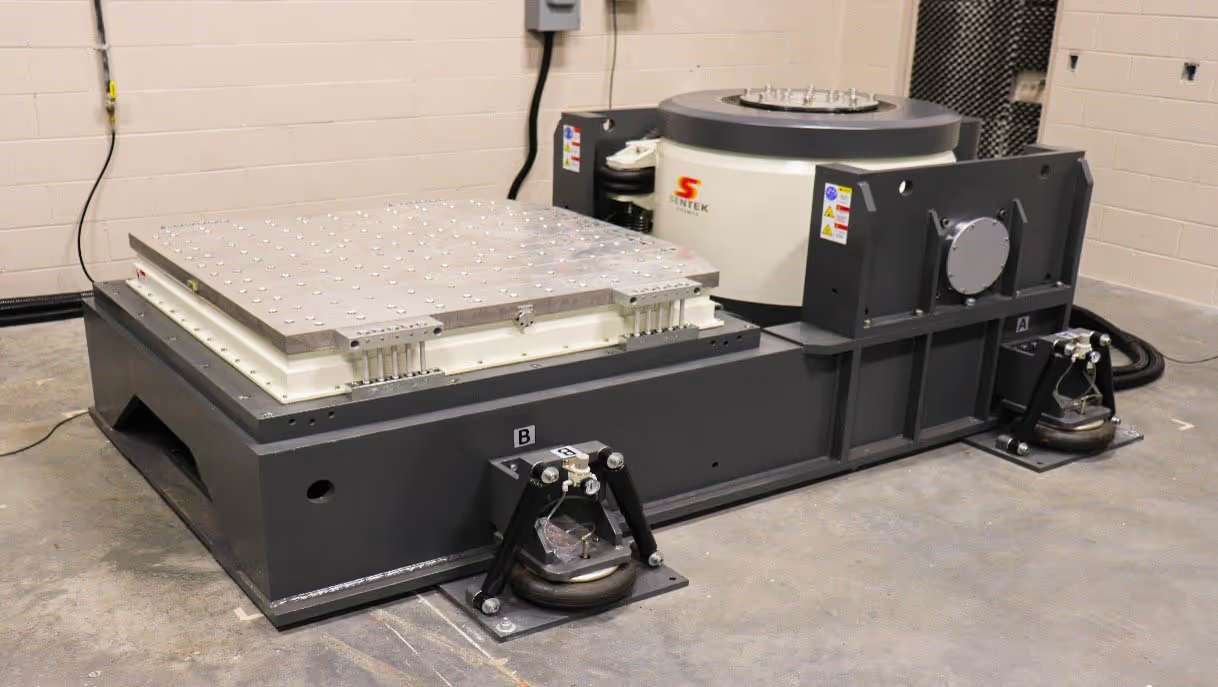
Vibration Testing
MGA offers comprehensive vibration testing services across seven laboratories, utilizing state-of-the-art equipment to simulate real-world conditions and ensure product reliability for automotive, aerospace, electronics, and defense industries.
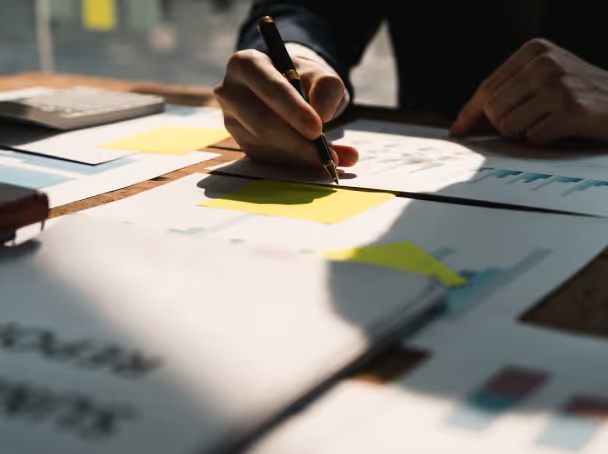
Full DVPR & Project Management
MGA offers comprehensive DVP&R management services, leveraging our cross-disciplinary expertise and lab network to streamline test planning, execution, and reporting, enabling efficient product development and confident market launches for our automotive and aerospace clients.
Battery Testing
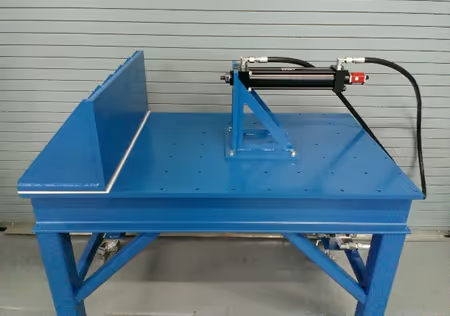
Cell
MGA Research offers comprehensive battery cell testing services across three dedicated facilities, leveraging decades of experience and advanced equipment to ensure the safety, performance, and regulatory compliance of battery cells for automotive, aerospace, and commercial energy storage applications.
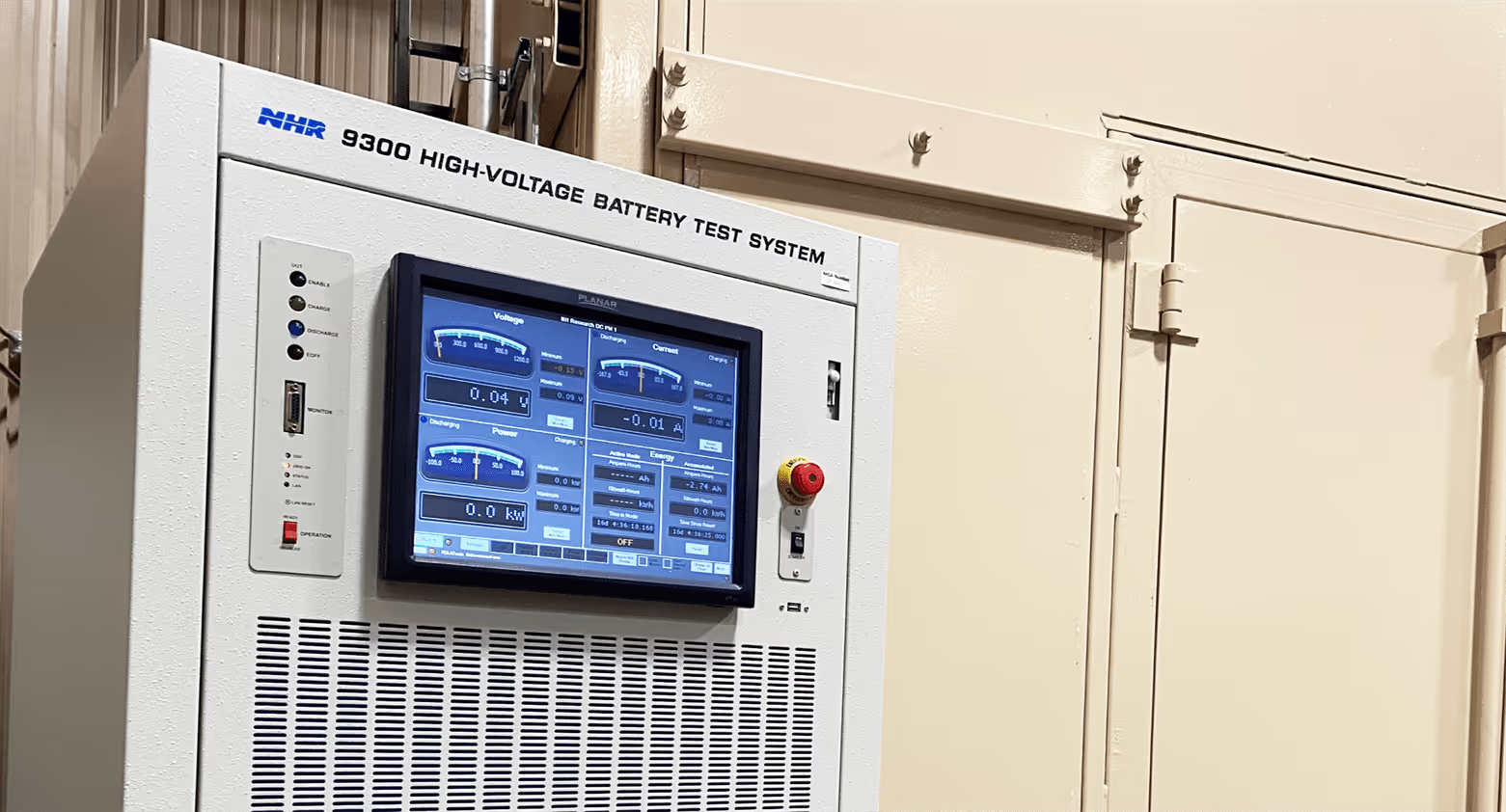
Module, Pack, and Full Vehicle
MGA Research offers comprehensive battery testing services for modules, packs, and full vehicles across three specialized facilities, leveraging over 20 years of experience and advanced equipment to ensure safety, performance, and regulatory compliance for automotive, aerospace, and energy storage applications.
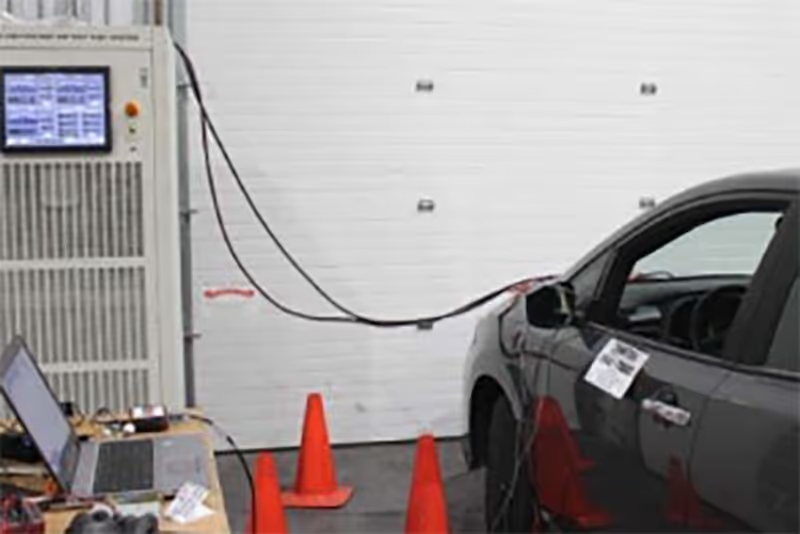
UN38.3
MGA Research provides comprehensive UN38.3 battery testing services across three ISO 17025 accredited facilities, ensuring the safe transportation of lithium batteries through rigorous safety evaluations that meet United Nations requirements for cells, modules, and full battery packs.
Aerospace & Defense
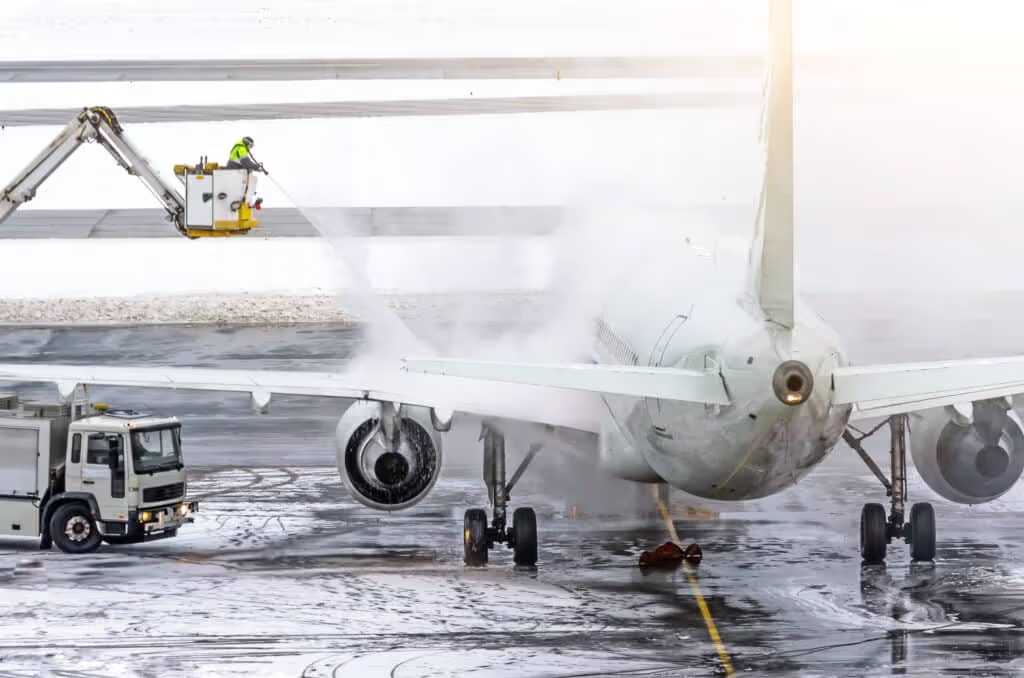
Aircraft
MGA Research provides cutting-edge testing services for the aerospace industry, leveraging decades of experience, state-of-the-art facilities, and expert staff to support safety, durability, and performance evaluations for aircraft components and systems across nine specialized laboratories.
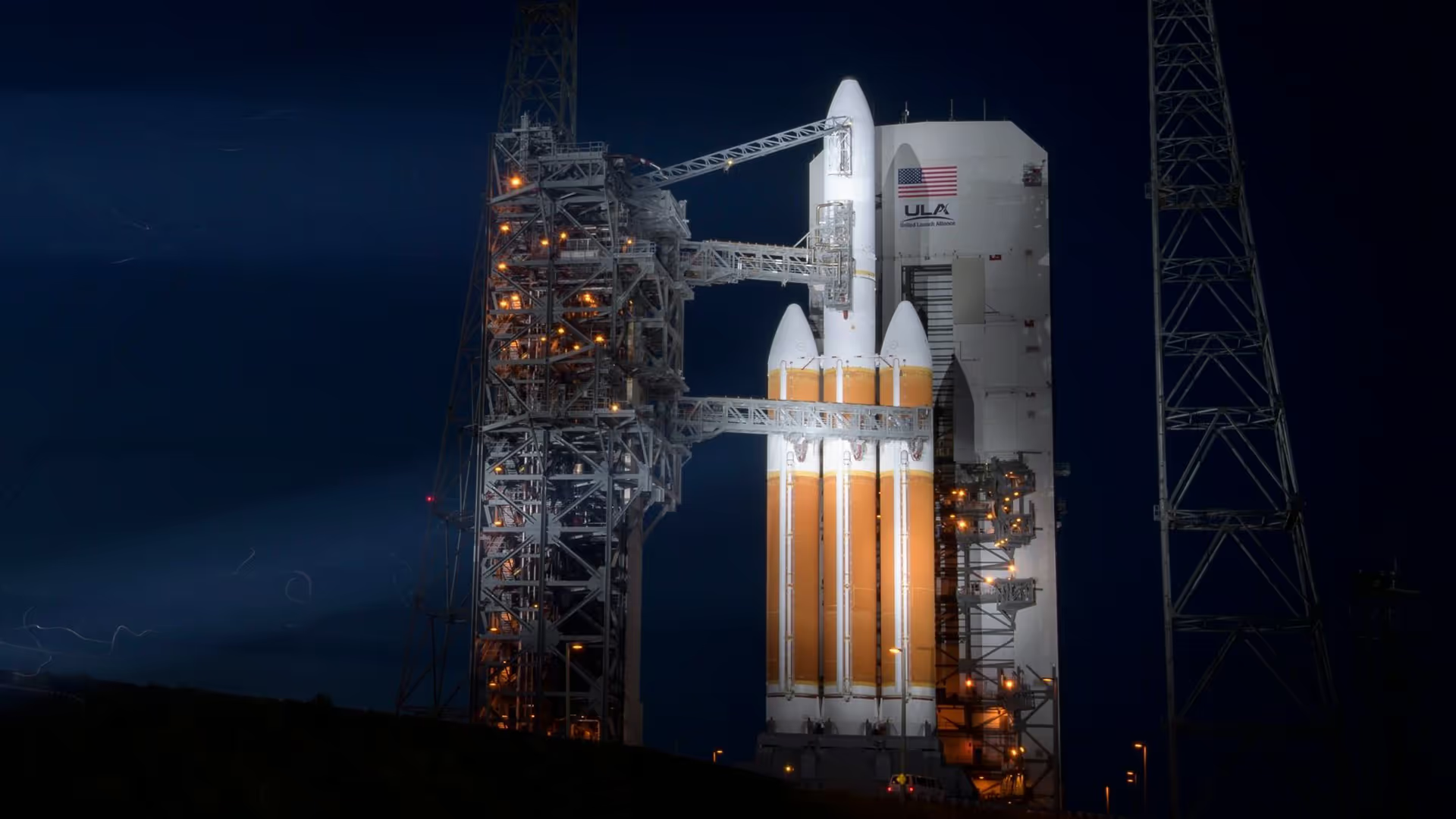
Space & Defense
MGA Research offers comprehensive testing services for the space and defense industries, leveraging proprietary equipment and extensive expertise to simulate extreme conditions like pyroshock, vibration, thermal stress, and mine blasts, ensuring component reliability and occupant safety across various applications.
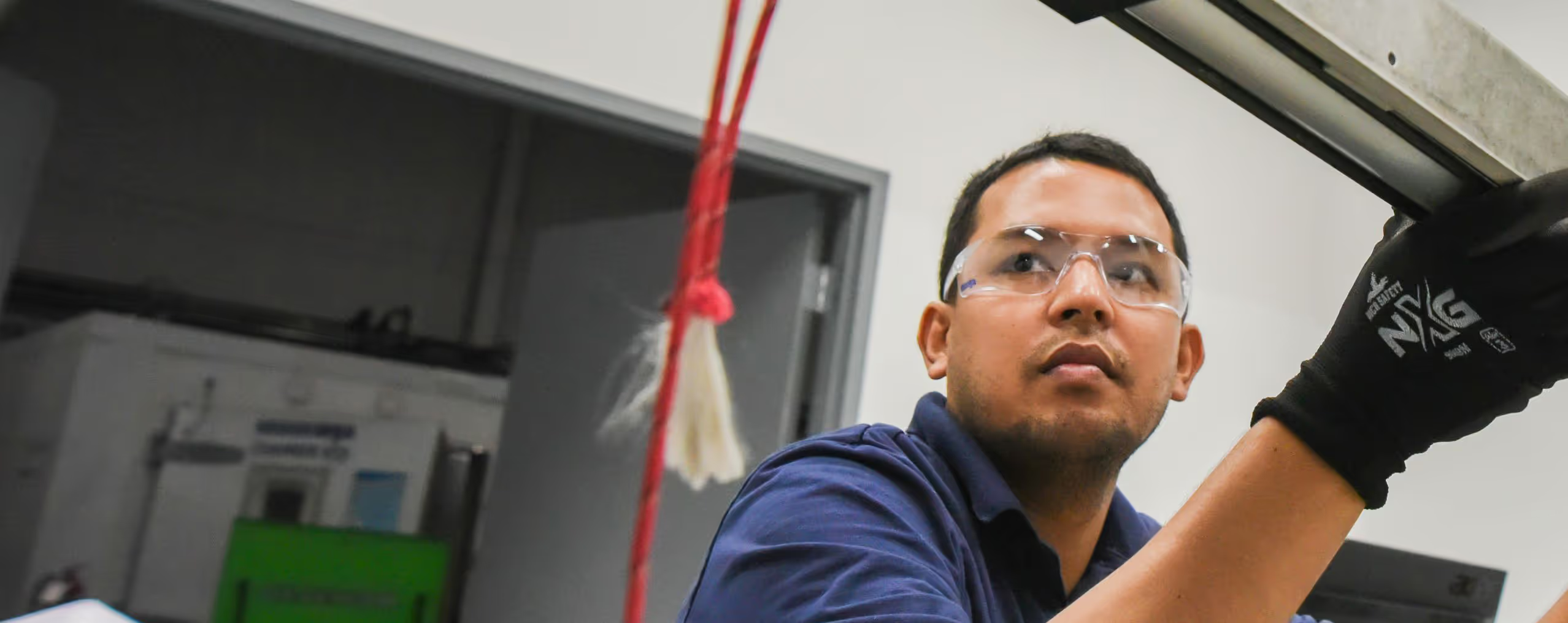
Ready to Get Started?
Let's discuss your testing needs and how MGA can help. Our team is ready to provide the expertise and solutions you're looking for.