MGA’s Expert Fixture Fabrication & Validation for Precision Testing
Mar 13, 2025
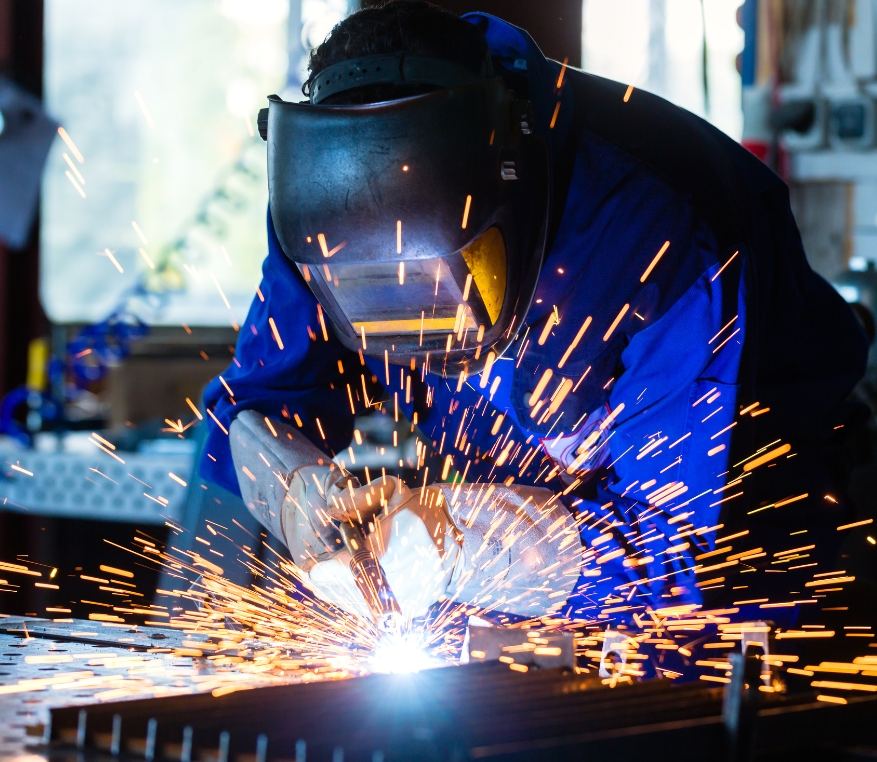
Fixtures play an invaluable role in the test laboratory and production plant. In the lab, the quality of a test greatly depends on the characteristics and workmanship exhibited by the fixture. In a plant setting, the dimensional accuracy and function of the produced part is evaluated utilizing a fixture. In general, a fixture is used to hold a test article in its intended real world use position. For most development programs, it is not feasible to use the actual full system, whether it is a vehicle body, aircraft fuselage, or a military application. This is where a fixture is utilized. A fixture will be used to hold the test article in the manner that it is intended to be used, with correct dimensions, and the fixture/component will be attached to the test machine. This approach has been used universally by suppliers in developing their products in various industries.
MGA engineers, designers, and fabricators work together to solve challenges our customers are facing and offer suitable equipment for the issue. The combined expertise of our test engineers and fabrication specialists results in industry-leading solutions.
The MGA Advantage: Our Process
Our highly skilled team manages every step, ensuring accuracy, durability, and compliance with your exact specifications.
Services currently supported are:
- Design: Collaborating closely with clients to create fixtures that perfectly meet testing and production requirements
- CNC Machining: Using state-of-the-art 3-axis and 5-axis CNC machines for maximum precision
- Fabrication and Assembly: Expert welding, milling, and fabrication, bringing your fixture to life
- CMM Checkout & Validation: We conduct a thorough inspection using Coordinate Measuring Machines (CMM) to ensure every fixture meets the highest quality standards
Our extensive testing and fabrication experience ensures simple, sturdy, user-friendly fixtures. All fixtures undergo rigorous testing and validation to meet customer specifications. Throughout the entire process, our customers are kept up to date so that if any new changes or needs arise, we can fit them in.
Categories of Fixtures Supported:
Seating Fixtures
With a large inventory of stock materials and base plates, our teams are available to support all your seating fixture needs in design, analysis, manufacturing, testing, and dimensional validation. The table below outlines fixtures currently supported by our team.
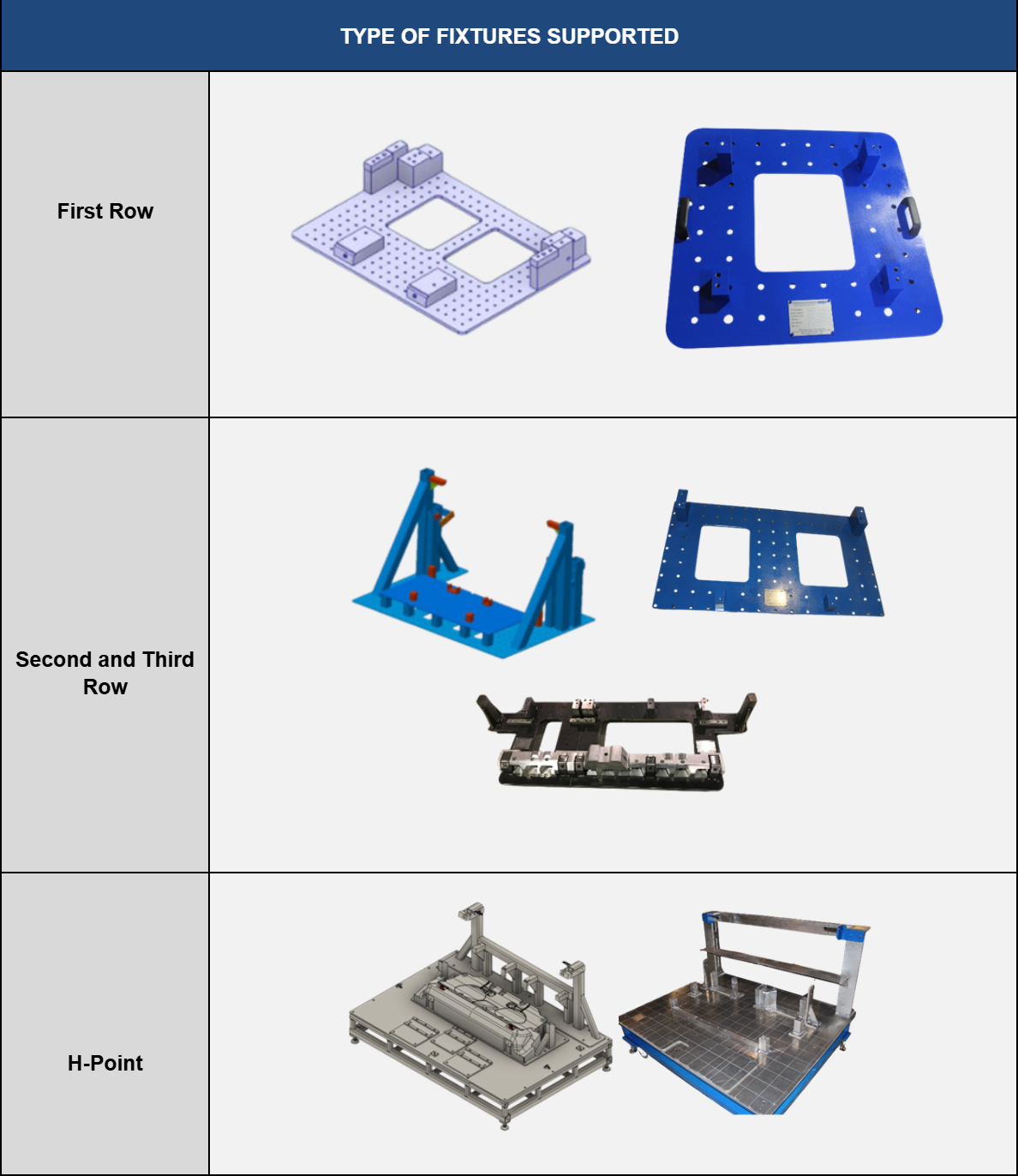
We also offer all types of peripheral fixtures to support custom angles on heel plates & luggage tables, as well as program specific D-ring fixtures.
Interior & Exterior fixtures
MGA fabricates fixtures for interior and exterior components, including instrument panels, headliners, and front-end modules, with options ranging from high-precision machined fixtures to cost-effective aluminum and 3D-printed solutions.
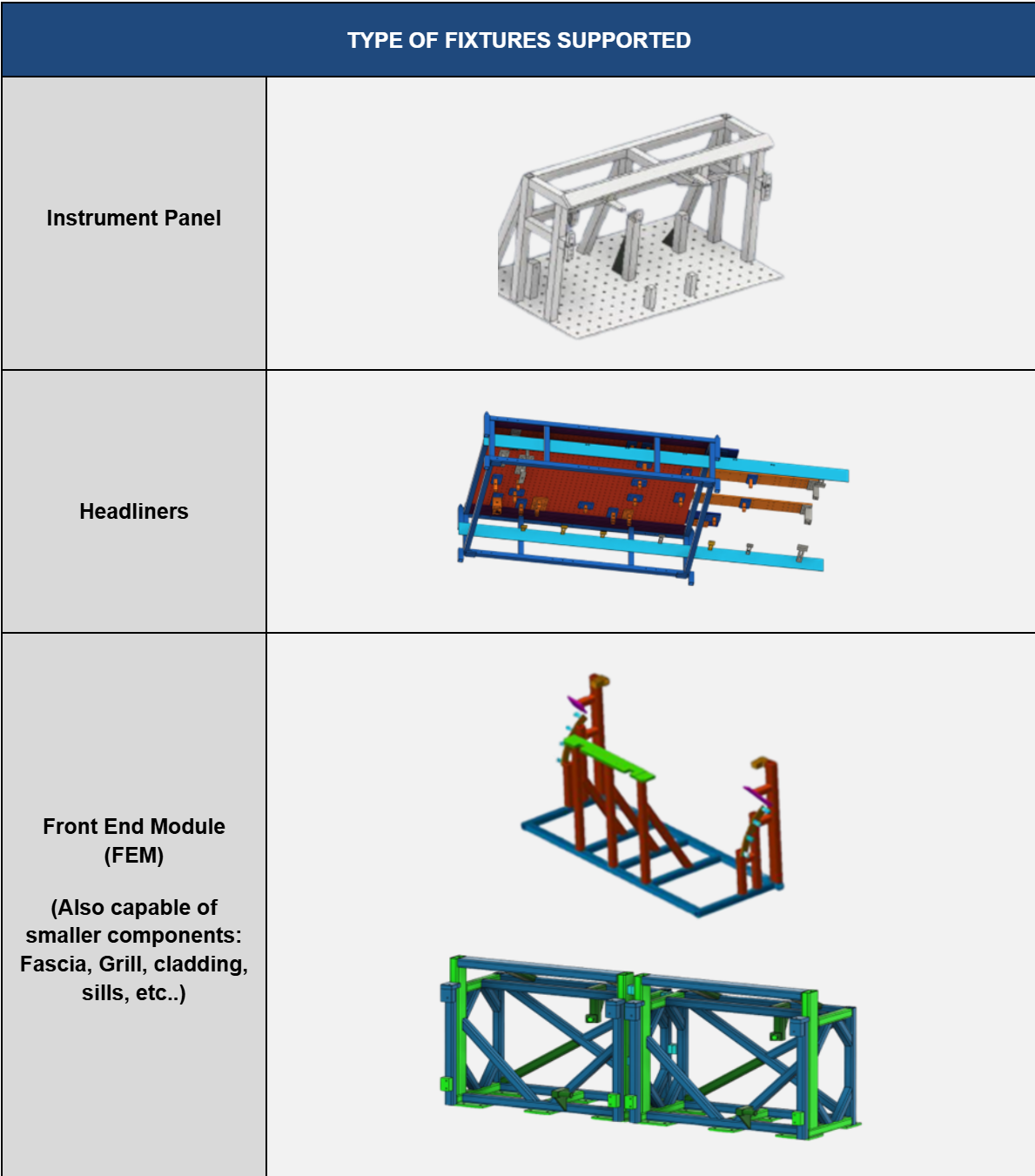
Aircraft & Aerospace fixtures
As part of our support to the aircraft/aerospace industry, we’ve developed a good understanding of testing requirements and fixture needs. MGA is capable of design and manufacturing fixtures and adaptor plates/blocks to ensure the units under test are secured properly throughout their testing campaigns. We also have universal fixturing solutions (i.e. pitch and roll fixtures) that have been designed, proven out, and used internally for years now.
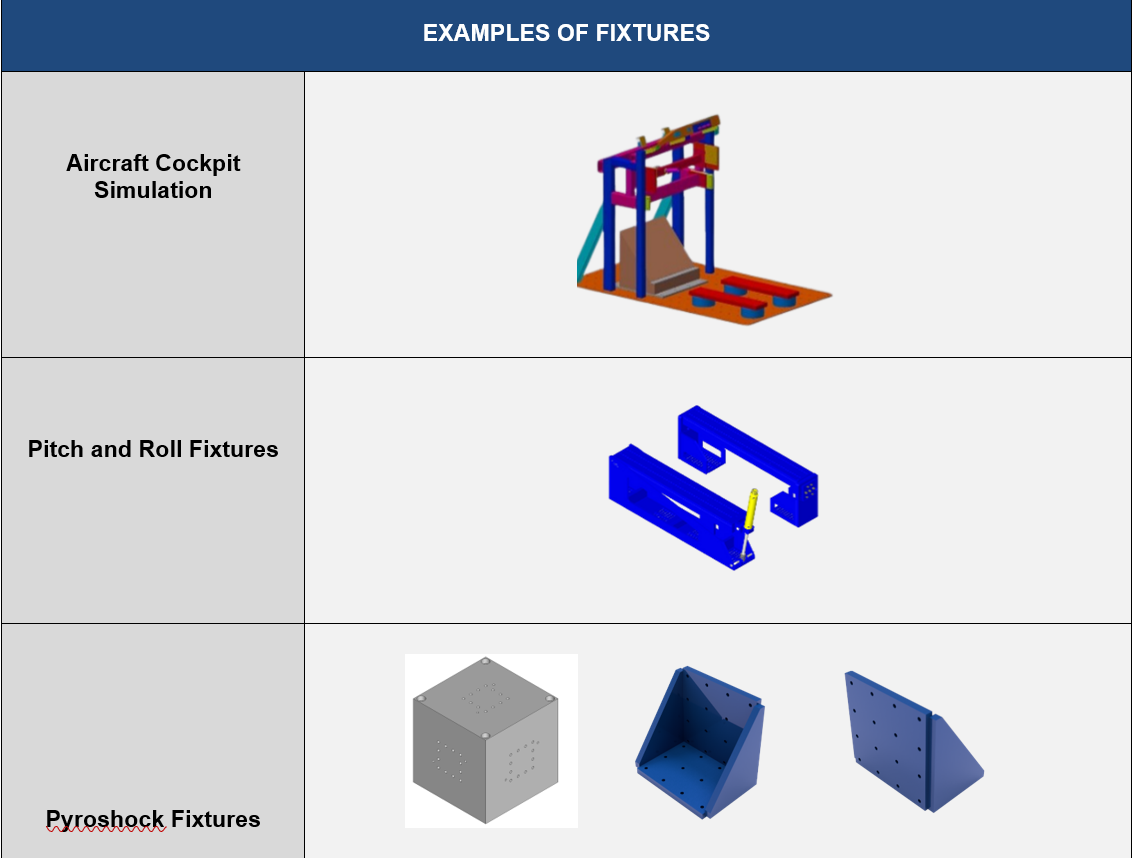
Custom fixtures
Being in the R&D service industry, we understand that some requirements can be unique. With decades of experience in custom testing, MGA provides tailored fixture solutions for static, dynamic, durability, and environmental requirements (see below table for a couple of examples).
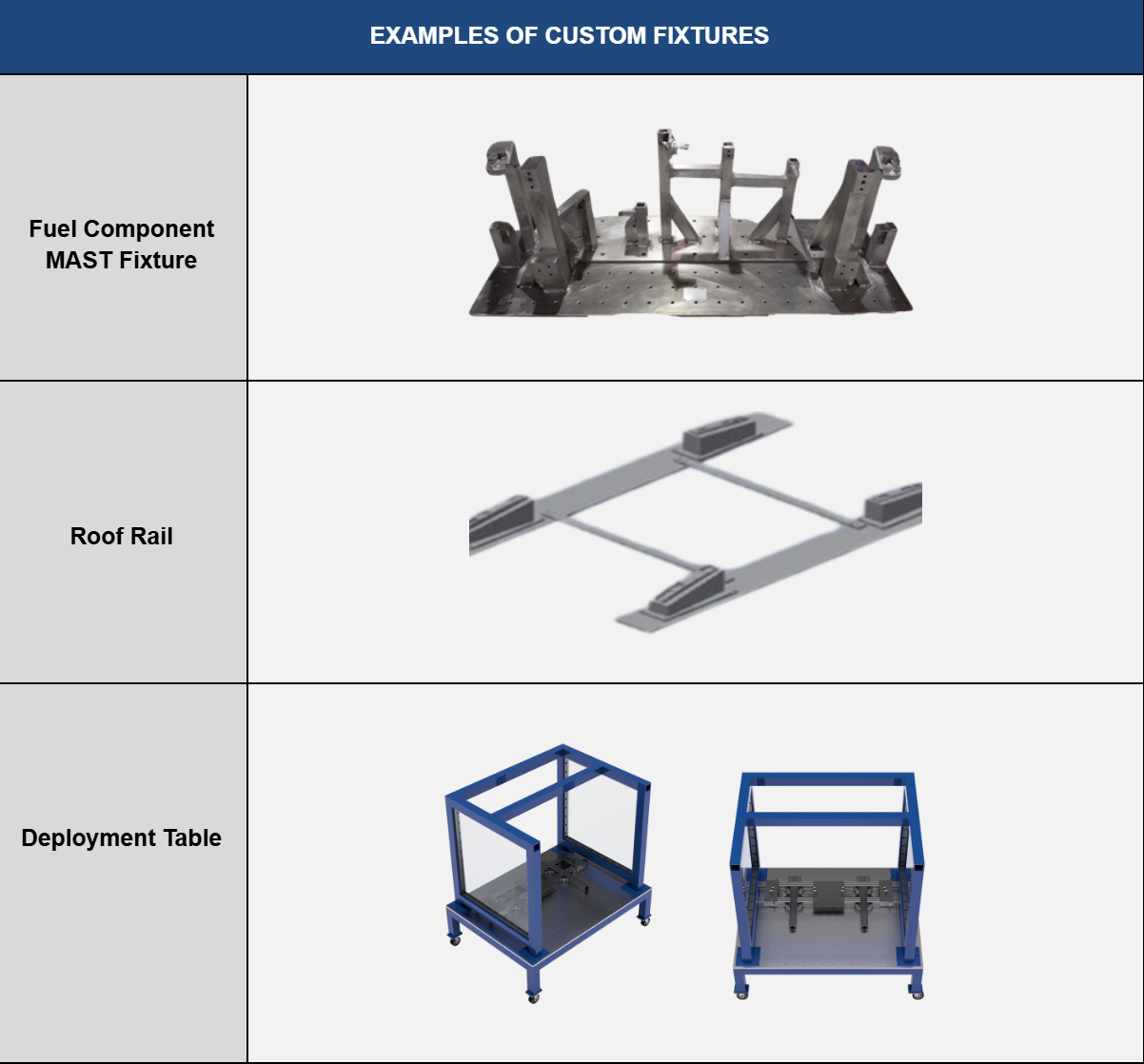
3D printing
With standard fixtures being made of metal, they are often designed and manufactured to withstand higher loads and frequencies. For lower-load applications like environmental or dimensional testing, MGA offers cost-effective 3D-printed fixtures nationwide (see table below examples).
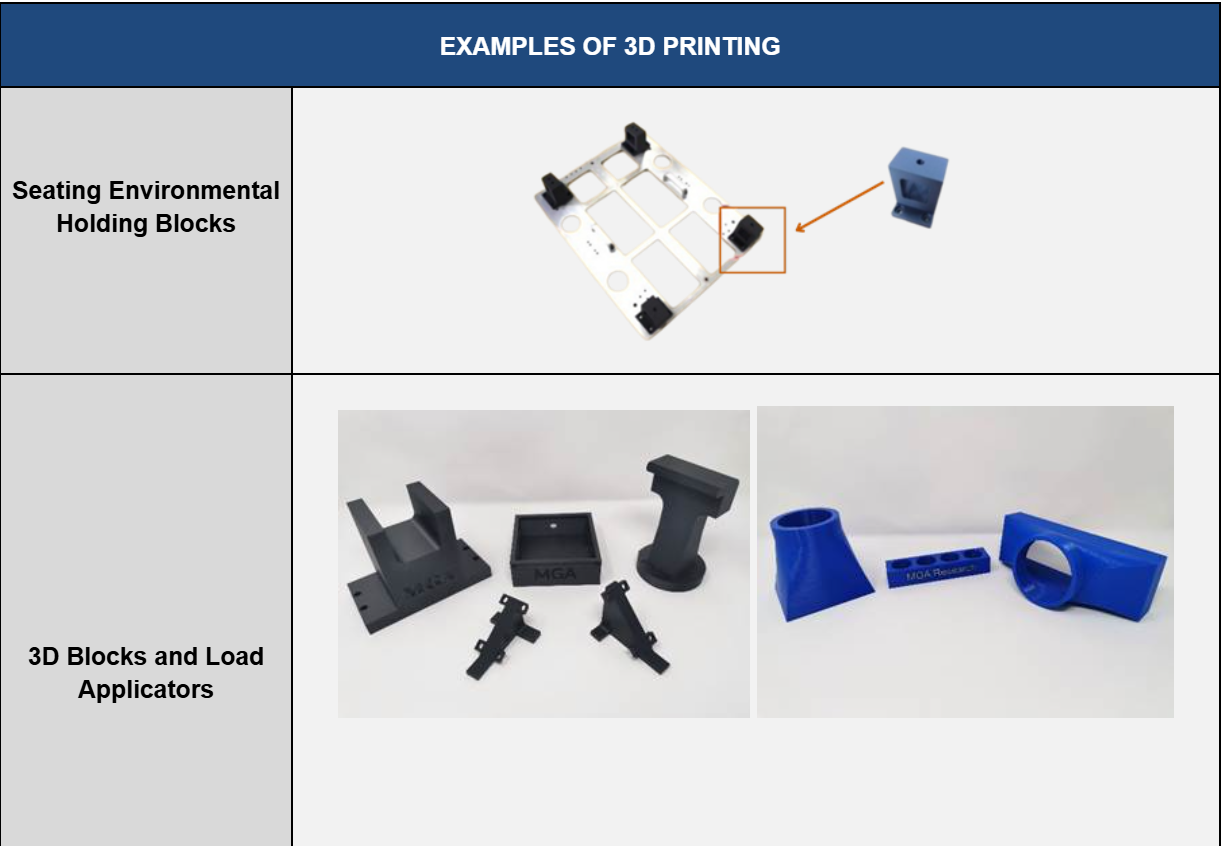
Fixture Validation using CMM & 3D Scanning
Using CMM and 3D scanning, MGA verifies that all critical fixation points are within ±1mm of nominal coordinates.
Validation Process
- Fixture Fabrication & Assembly – Fixtures are built to request specifications.
- CMM/3D Scan Inspection – High-precision metrology tools measure fixation points.
- Tolerance Verification – Measured data is compared against nominal design coordinates.
- Validation Report – A detailed report documents all measurements and compliance.
- Customer Sign Off – Customer reviews and approves the validation report.
- Fixture Delivery – The validated fixture is shipped to the customer or MGA test lab.
This data-driven quality assurance approach guarantees that our fixtures deliver repeatability, accuracy, and reliability.
On-Site Fixture Validation
MGA also offers on-site fixture validation services for non-MGA fixtures. Whether you need revalidation or verification of existing tooling we can deploy our metrology-grade equipment & personnel to your location.
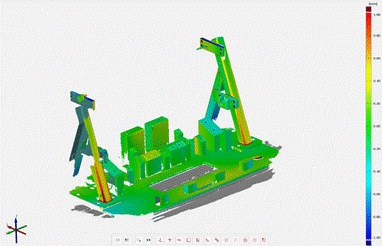
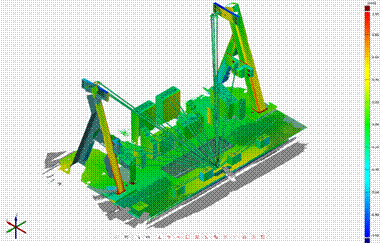
For questions and inquiries, please reach out to us through our online form to learn more!
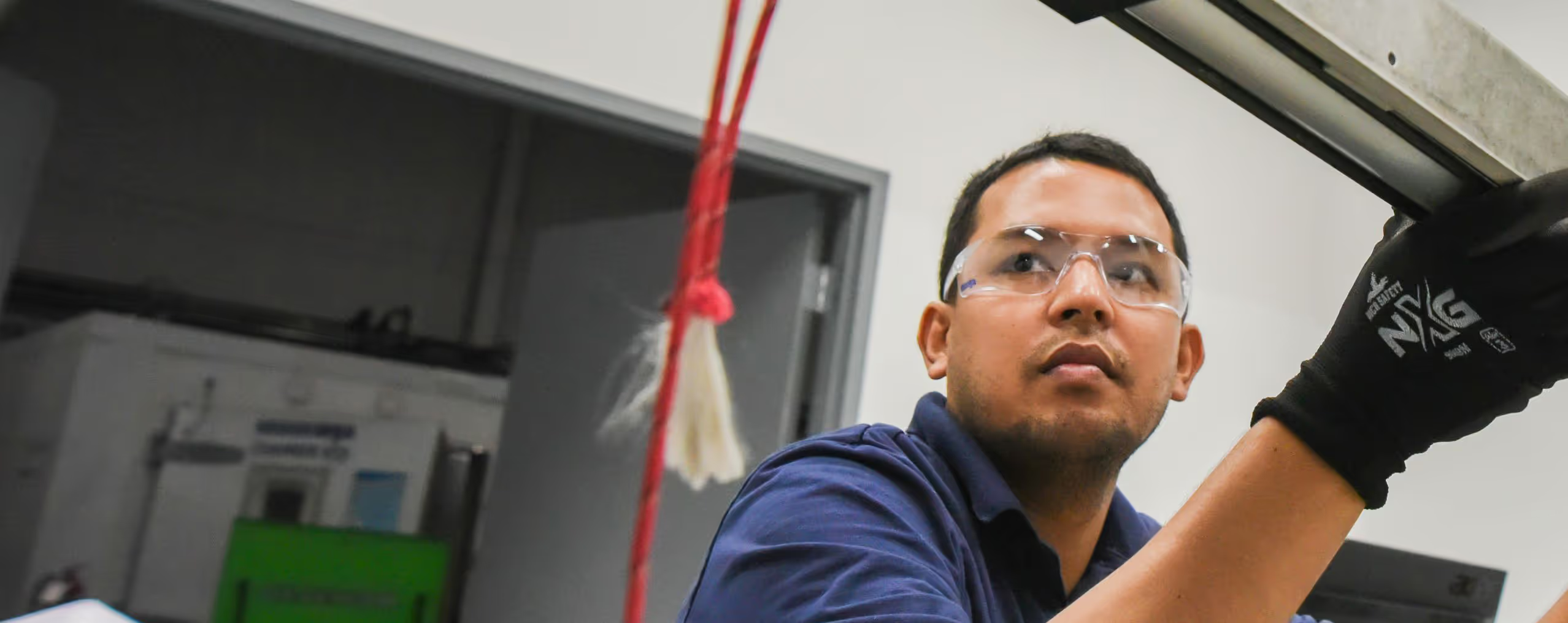
Ready to Get Started?
Let's discuss your testing needs and how MGA can help. Our team is ready to provide the expertise and solutions you're looking for.