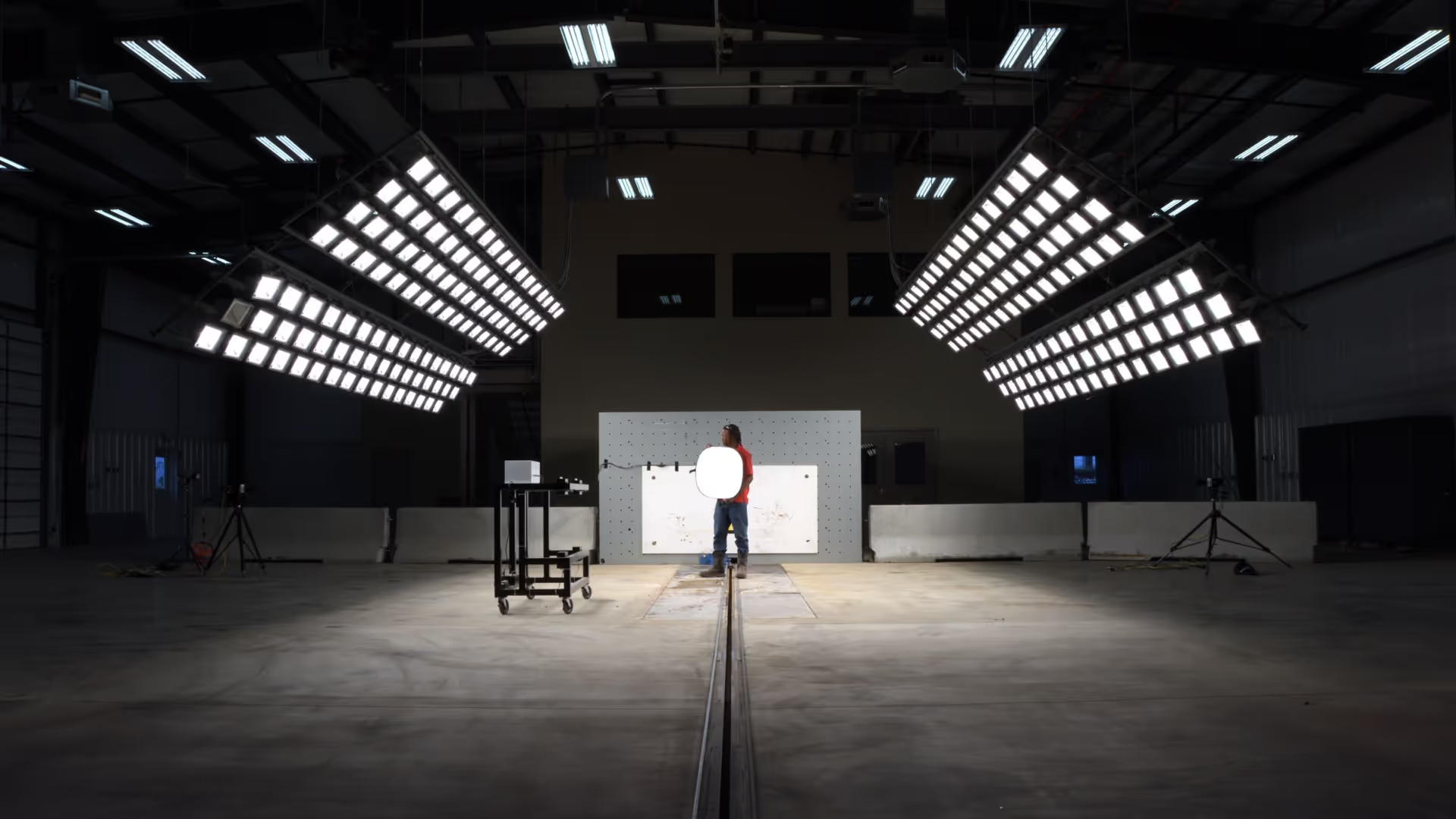
News & Insights
Stay informed with the latest updates, industry insights, and innovations from MGA Research Corporation.
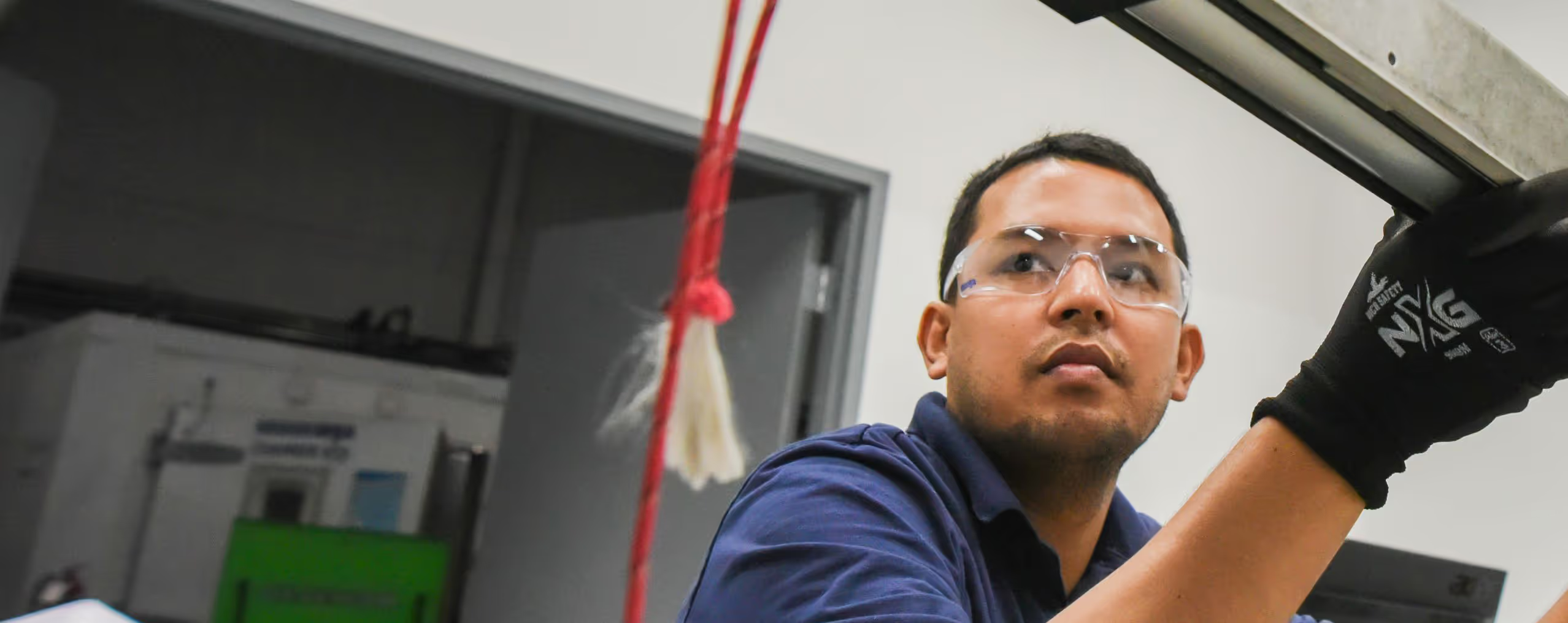
Ready to Get Started?
Let's discuss your testing needs and how MGA can help. Our team is ready to provide the expertise and solutions you're looking for.